Hotline
+86-136 8495 9862
Email:cennia@szmizhi.com
Add::104,Building 27,Third Industrial Zone, Longxi Community,Longgang District,Shenzhen,China.
Coil Forming & Handling Equipment
Surface Treatment Equipment
Solutions
Application
About Us
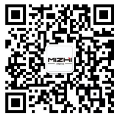
Welcome to MIZHI
For consultation/feedback, please call the service hotline: +86-136 8495 9862 Email:cennia@szmizhi.com
Automatic blasting machines are advanced pieces of equipment that have revolutionized the surface preparation and finishing processes in various industries. These machines offer efficient, consistent, and high-quality results, making them an essential tool for many manufacturing and restoration operations. In this article, we will explore the features, applications, benefits, and working principles of automatic blasting machines.
I. Introduction to Automatic Blasting Machines
Automatic blasting machines are designed to clean, roughen, or texture surfaces by propelling abrasive materials at high velocities. The abrasive particles impact the surface, removing contaminants, rust, old coatings, and creating a profile that enhances the adhesion of new coatings or finishes. These machines are available in various configurations and sizes to meet the specific needs of different applications.
II. Types of Automatic Blasting Machines
1. Pressure Blasting Machines
Pressure blasting machines use compressed air to propel the abrasive particles. They are suitable for heavy-duty applications and can handle large volumes of abrasive. These machines are often used in industries such as shipbuilding, construction, and metal fabrication.
2. Suction Blasting Machines
Suction blasting machines operate by creating a vacuum that draws the abrasive particles into a mixing chamber and then propels them onto the surface. They are ideal for smaller-scale operations and are commonly used in automotive restoration, woodworking, and other applications where a more controlled blasting environment is required.
3. Centrifugal Blasting Machines
Centrifugal blasting machines use a spinning wheel to accelerate the abrasive particles. These machines are known for their high productivity and are often used in mass production settings. They are suitable for applications such as metal casting, forging, and heat treatment.
III. Components of an Automatic Blasting Machine
1. Abrasive Storage and Feeding System
The abrasive storage and feeding system stores the abrasive material and supplies it to the blasting gun or nozzle. This system may include a hopper, conveyor, or screw feeder, depending on the type of machine.
2. Blasting Gun or Nozzle
The blasting gun or nozzle is the part of the machine that directs the abrasive particles onto the surface. It is designed to control the flow and velocity of the abrasive, ensuring a uniform and effective blasting pattern.
3. Compressed Air System
The compressed air system provides the force needed to propel the abrasive particles. It typically consists of an air compressor, air filter, and pressure regulator.
4. Control System
The control system allows the operator to adjust the blasting parameters such as abrasive flow rate, air pressure, and blasting time. It may include a programmable logic controller (PLC) or a microprocessor-based controller.
5. Dust Collection System
The dust collection system captures the dust and debris generated during the blasting process. This helps to maintain a clean and safe working environment and reduces the risk of respiratory problems for the operator.
IV. Applications of Automatic Blasting Machines
1. Metal Surface Preparation
Automatic blasting machines are widely used in the metalworking industry for surface preparation before painting, coating, or welding. They can remove rust, scale, and old coatings from steel, aluminum, and other metals, creating a clean and rough surface that promotes adhesion.
2. Foundry and Casting
In the foundry and casting industry, automatic blasting machines are used to clean castings of sand, oxides, and other contaminants. They can also be used to texture the surface of castings for improved appearance and functionality.
3. Automotive Restoration
Automatic blasting machines are popular in the automotive restoration industry for removing rust and old paint from car bodies, frames, and engine parts. They can also be used to texture surfaces for a custom finish.
4. Woodworking
In woodworking, automatic blasting machines can be used to texture wood surfaces for a unique look. They can also be used to remove paint and stains from wooden furniture and fixtures.
5. Stone and Concrete Processing
Automatic blasting machines can be used to clean and texture stone and concrete surfaces. They are often used in the construction industry for preparing surfaces for coatings or adhesives.
V. Benefits of Automatic Blasting Machines
1. Efficiency
Automatic blasting machines are highly efficient and can complete surface preparation tasks much faster than manual methods. They can handle large volumes of work and reduce labor costs.
2. Consistency
These machines provide consistent results, ensuring that each surface is treated uniformly. This is important for applications where a specific surface profile or finish is required.
3. Quality
Automatic blasting machines can achieve a high level of surface cleanliness and roughness, which improves the quality of coatings and finishes. They can also remove contaminants that could otherwise lead to premature failure of the coating.
4. Safety
Automatic blasting machines are designed with safety features such as enclosures, dust collection systems, and emergency stop buttons. This reduces the risk of operator injury and exposure to hazardous materials.
5. Versatility
Automatic blasting machines can be used on a wide variety of materials and surfaces, making them a versatile tool for many industries. They can handle different abrasive materials and adjust the blasting parameters to meet specific application requirements.
VI. Working Principle of Automatic Blasting Machines
The working principle of an automatic blasting machine is based on the principle of abrasive blasting. The abrasive material is accelerated by a force (such as compressed air or centrifugal force) and directed onto the surface to be treated. The impact of the abrasive particles removes contaminants and creates a roughened surface.
In a pressure blasting machine, compressed air is used to propel the abrasive particles through a blasting gun or nozzle. The air pressure and abrasive flow rate can be adjusted to control the intensity of the blasting. In a suction blasting machine, a vacuum is created to draw the abrasive particles into a mixing chamber, where they are mixed with compressed air and then propelled onto the surface. In a centrifugal blasting machine, a spinning wheel accelerates the abrasive particles and throws them onto the surface.
VII. Factors to Consider When Choosing an Automatic Blasting Machine
1. Application Requirements
Consider the type of surface to be treated, the required surface finish, and the volume of work. This will help determine the appropriate type and size of automatic blasting machine.
2. Abrasive Material
Choose an abrasive material that is suitable for the surface being treated and the desired result. Different abrasives have different hardnesses, sizes, and shapes, which can affect the blasting efficiency and surface finish.
3. Machine Capacity
Consider the capacity of the machine in terms of abrasive storage, air pressure, and blasting rate. This will ensure that the machine can handle the volume of work required.
4. Safety Features
Look for automatic blasting machines with safety features such as enclosures, dust collection systems, and emergency stop buttons. These features will protect the operator and ensure a safe working environment.
5. Maintenance and Service
Consider the ease of maintenance and availability of service and spare parts. A machine that is easy to maintain and has good after-sales support will ensure long-term reliability and productivity.
VIII. Maintenance and Operation of Automatic Blasting Machines
1. Regular Maintenance
Perform regular maintenance on the automatic blasting machine to ensure its proper functioning and longevity. This may include cleaning the abrasive storage and feeding system, inspecting the blasting gun or nozzle, and checking the compressed air system and dust collection system.
2. Operator Training
Provide proper training to the operators on the safe and efficient operation of the automatic blasting machine. This includes understanding the controls, safety procedures, and maintenance requirements.
3. Safety Precautions
Follow all safety precautions when operating the automatic blasting machine. Wear appropriate personal protective equipment such as safety glasses, ear protection, and a dust mask. Ensure that the machine is properly grounded and that all safety guards are in place.
4. Troubleshooting
In case of any problems or malfunctions, refer to the machine's manual or contact the manufacturer for troubleshooting advice. Common issues may include blocked nozzles, low air pressure, or abrasive flow problems.
In conclusion, automatic blasting machines are powerful and versatile tools that offer many benefits for surface preparation and finishing. By understanding their features, applications, working principles, and factors to consider when choosing and operating them, you can make an informed decision and use these machines effectively to improve the quality and productivity of your operations.