Hotline
+86-136 8495 9862
Email:cennia@szmizhi.com
Add::104,Building 27,Third Industrial Zone, Longxi Community,Longgang District,Shenzhen,China.
Coil Forming & Handling Equipment
Surface Treatment Equipment
Solutions
Application
About Us
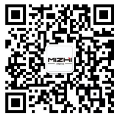
Welcome to MIZHI
For consultation/feedback, please call the service hotline: +86-136 8495 9862 Email:cennia@szmizhi.com
Introduction
A concrete blasting machine is a specialized piece of equipment designed to remove or clean concrete surfaces through the use of high-velocity abrasive materials. It is widely used in various construction and renovation projects to achieve different surface preparation requirements, such as roughening for better adhesion of coatings or removal of deteriorated concrete layers.
Working Principles
Compressed Air Propulsion: Most concrete blasting machines operate based on the principle of using compressed air to accelerate abrasive particles. The compressed air is supplied by an air compressor and is forced through a nozzle or a series of nozzles. As the high-pressure air passes through the nozzle, it creates a Venturi effect, which sucks in the abrasive material from a hopper or a storage tank. The mixture of air and abrasive is then ejected at high speed towards the concrete surface.
Centrifugal Force: Some concrete blasting machines, such as wheel blasting machines, utilize centrifugal force to propel the abrasive media. In these machines, a rotating wheel is used to accelerate the abrasives. The wheel spins at a high speed, and as the abrasives are fed onto the wheel, they are thrown outwards due to centrifugal acceleration and strike the concrete surface with great force, effectively removing the unwanted material.
Types of Concrete Blasting Machines
Dry Blasting Machines: These are the most common type of concrete blasting machines. They use dry abrasive materials such as sand, grit, or steel shot. The dry abrasives are propelled by compressed air and can provide a high level of cleaning and surface roughening. However, they generate a significant amount of dust during operation, which requires proper dust collection and containment systems to comply with environmental regulations and ensure the safety of the operators.
Wet Blasting Machines: Wet blasting machines, also known as slurry blasting machines, use a mixture of water and abrasive particles. The water serves multiple purposes, including reducing dust emissions, cooling the surface being blasted, and improving the overall efficiency of the blasting process. The abrasive slurry is pumped to the nozzle and then sprayed onto the concrete surface under high pressure. Wet blasting is often preferred in situations where dust control is of utmost importance, such as in enclosed or populated areas.
Vacuum Blasting Machines: Vacuum blasting machines combine the blasting process with an integrated vacuum system. As the abrasives are propelled onto the concrete surface to remove the unwanted material, the vacuum system immediately sucks up the spent abrasives, dust, and debris, preventing them from scattering in the surrounding environment. This type of machine is highly effective in minimizing dust pollution and is commonly used in indoor or sensitive locations where cleanliness and environmental protection are critical.
Components of a Concrete Blasting Machine
Abrasive Hopper or Storage Tank: This is where the abrasive materials are stored before being fed into the blasting system. The hopper or tank is usually designed to hold a sufficient quantity of abrasives to ensure continuous operation without frequent refilling.
Compressor: The compressor is a crucial component that provides the compressed air necessary for propelling the abrasive particles. It must be capable of delivering air at the required pressure and volume to achieve effective blasting results. Different blasting applications may require different compressor capacities and pressures.
Nozzles: Nozzles play a vital role in determining the pattern, intensity, and coverage of the blasting. They come in various shapes, sizes, and designs to suit different blasting requirements. The nozzle diameter, angle, and length can be adjusted to control the flow rate and direction of the abrasive jet, allowing for precise surface treatment.
Control Panel: The control panel enables the operator to adjust and monitor various parameters of the blasting process, such as air pressure, abrasive feed rate, and blasting duration. It may also include safety features and indicators to ensure the proper functioning of the machine and the safety of the operator.
Dust Collection System: In dry blasting machines, a dust collection system is essential to capture and filter out the dust generated during the blasting process. This system typically consists of filters, cyclones, and dust collectors that work together to remove the dust particles from the air, improving air quality and reducing environmental pollution.
Applications of Concrete Blasting Machines
Surface Preparation for Coatings: Before applying paints, sealants, or other protective coatings to concrete surfaces, it is necessary to clean and roughen the surface to enhance the adhesion of the coating. Concrete blasting machines can effectively remove dirt, grease, loose concrete, and other contaminants, creating a clean and textured surface that promotes better coating performance and durability.
Concrete Repair and Restoration: In cases where concrete structures have deteriorated due to factors such as weathering, corrosion, or physical damage, blasting can be used to remove the damaged or weakened concrete layers. This prepares the surface for subsequent repair work, such as patching, resurfacing, or reinforcement, ensuring a strong bond between the new and existing concrete.
Removal of Unwanted Concrete: Concrete blasting machines are often used to remove unwanted concrete in situations such as demolition, renovation, or modification of structures. They can quickly and efficiently break down and remove concrete slabs, walls, or other concrete elements, making way for new construction or changes to the existing layout.
Texturing and Profiling: Concrete surfaces can be textured or profiled using blasting machines to achieve specific aesthetic or functional requirements. For example, in the case of decorative concrete, blasting can create unique patterns or finishes, enhancing the visual appeal of the surface. In industrial settings, texturing can improve slip resistance or provide a better grip for machinery or vehicles.
Advantages of Using Concrete Blasting Machines
High Efficiency: Concrete blasting machines can cover large surface areas in a relatively short period, significantly reducing the time and labor required for surface preparation compared to manual methods. This increased productivity is especially beneficial for large-scale construction projects or when tight schedules need to be met.
Precise Surface Treatment: The ability to control the blasting parameters, such as air pressure, abrasive type, and nozzle settings, allows for precise surface treatment. This ensures that the concrete surface is cleaned, roughened, or removed to the exact specifications required for the intended application, resulting in a consistent and high-quality finish.
Versatility: These machines can be used on a variety of concrete surfaces, including floors, walls, ceilings, and structural elements, making them suitable for a wide range of construction and renovation projects. Additionally, different abrasive materials can be selected depending on the hardness of the concrete and the desired blasting effect, further enhancing their versatility.
Cost-Effective: Although the initial investment in a concrete blasting machine may be significant, the long-term cost savings can be substantial. By reducing labor requirements, improving productivity, and minimizing the need for additional surface preparation materials, these machines can offer a cost-effective solution for concrete surface treatment over time.
Safety Precautions
Personal Protective Equipment: Operators must wear appropriate personal protective equipment, including safety glasses, ear protection, gloves, and protective clothing, to prevent injuries from flying abrasives, dust, and noise generated during the blasting process.
Proper Training: Only trained and authorized personnel should operate the concrete blasting machine. They should be familiar with the machine's operation, safety procedures, and emergency shutdown protocols to ensure safe and efficient use.
Dust Control: As mentioned earlier, dust generated during dry blasting can pose a significant health hazard. Adequate dust collection and ventilation systems should be in place to maintain a clean and healthy working environment. Regular maintenance and cleaning of the dust collection equipment are also necessary to ensure its proper functioning.
Equipment Inspection and Maintenance: Regular inspection and maintenance of the concrete blasting machine are essential to identify and address any potential safety hazards or mechanical issues. This includes checking for leaks in the air compressor, wear and tear of nozzles and hoses, and proper functioning of the control panel and safety devices.
Conclusion
Concrete blasting machines are indispensable tools in the construction and renovation industries, offering efficient, precise, and cost-effective solutions for concrete surface treatment. By understanding their working principles, types, components, applications, and safety precautions, construction professionals can make informed decisions when selecting and using these machines to achieve the desired surface preparation results while ensuring the safety of the operators and compliance with environmental regulations. With continued advancements in technology, concrete blasting machines are likely to become even more efficient, environmentally friendly, and user-friendly in the future, further enhancing their value in the construction field.