Hotline
+86-136 8495 9862
Email:cennia@szmizhi.com
Add::104,Building 27,Third Industrial Zone, Longxi Community,Longgang District,Shenzhen,China.
Coil Forming & Handling Equipment
Surface Treatment Equipment
Solutions
Application
About Us
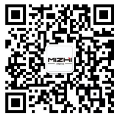
Welcome to MIZHI
For consultation/feedback, please call the service hotline: +86-136 8495 9862 Email:cennia@szmizhi.com
Concrete sandblasting machines are powerful tools used for surface preparation and cleaning of concrete surfaces. These machines utilize abrasive materials, such as sand, to remove contaminants, smooth rough surfaces, and create a textured finish. In this article, we will explore the various aspects of concrete sandblasting machines, including their types, working principles, applications, benefits, and considerations for use.
I. Introduction to Concrete Sandblasting Machines
Concrete sandblasting is a process that involves propelling abrasive particles at high velocities onto a concrete surface. The impact of the abrasive particles removes dirt, stains, paint, and other contaminants, while also creating a roughened surface that can improve adhesion for coatings or overlays. Concrete sandblasting machines are designed to perform this process efficiently and effectively, providing a clean and prepared surface for various applications.
II. Types of Concrete Sandblasting Machines
1. Pressure Sandblasting Machines
Pressure sandblasting machines use compressed air to propel the abrasive particles. These machines are typically more powerful and can handle larger volumes of abrasive material. They are suitable for heavy-duty applications and can quickly remove thick coatings and contaminants from concrete surfaces.
2. Suction Sandblasting Machines
Suction sandblasting machines operate by creating a vacuum that draws the abrasive particles into a mixing chamber and then propels them onto the concrete surface. These machines are generally smaller and more portable than pressure sandblasting machines. They are suitable for lighter-duty applications and are often used for smaller projects or in areas where access is limited.
3. Wet Sandblasting Machines
Wet sandblasting machines use a mixture of water and abrasive particles to perform the sandblasting process. The addition of water helps to reduce dust emissions and can provide a cleaner working environment. Wet sandblasting is also less aggressive than dry sandblasting and can be used on delicate surfaces or in areas where dust control is a concern.
III. Working Principle of Concrete Sandblasting Machines
The working principle of a concrete sandblasting machine is relatively simple. The machine consists of a hopper or container that holds the abrasive material, a compressed air source or vacuum system, a blasting gun or nozzle, and a dust collection system.
In a pressure sandblasting machine, compressed air is forced through the blasting gun or nozzle, creating a high-velocity stream of air. The abrasive material is then added to this stream of air, and the combined force propels the abrasive particles onto the concrete surface. The impact of the abrasive particles removes the contaminants and creates a roughened surface.
In a suction sandblasting machine, a vacuum is created by a fan or blower. The abrasive material is drawn into a mixing chamber by the vacuum, where it is mixed with air. The mixture is then propelled through the blasting gun or nozzle onto the concrete surface.
In a wet sandblasting machine, water is added to the abrasive material in the hopper or container. The mixture is then pumped through a hose and nozzle, where it is sprayed onto the concrete surface. The water helps to reduce dust emissions and also provides lubrication for the abrasive particles, reducing wear on the blasting equipment.
IV. Applications of Concrete Sandblasting Machines
1. Surface Preparation for Coatings and Overlays
Concrete sandblasting is often used as a surface preparation method before applying coatings or overlays. The roughened surface created by sandblasting provides better adhesion for the new coating or overlay, ensuring a long-lasting and durable finish.
2. Removal of Contaminants and Stains
Concrete sandblasting can effectively remove dirt, grease, oil, rust, and other contaminants from concrete surfaces. It can also be used to remove stains caused by spilled chemicals or dyes.
3. Texture Creation
Sandblasting can be used to create a textured finish on concrete surfaces. This can improve slip resistance and give the surface a more aesthetically pleasing appearance. Textured surfaces are often used in outdoor areas, such as sidewalks, driveways, and pool decks.
4. Restoration of Historic Structures
Concrete sandblasting is a popular method for restoring historic concrete structures. It can remove years of dirt, grime, and paint, revealing the original texture and beauty of the concrete. Sandblasting can also be used to repair damaged concrete surfaces by removing loose or deteriorated material and creating a clean surface for patching or repair.
V. Benefits of Concrete Sandblasting Machines
1. Efficient Surface Preparation
Concrete sandblasting machines can quickly and efficiently prepare concrete surfaces for various applications. They can remove contaminants and create a roughened surface in a fraction of the time it would take to perform manual surface preparation methods.
2. Versatility
These machines can be used on a wide range of concrete surfaces, including floors, walls, ceilings, and outdoor structures. They can also handle different types of contaminants and surface conditions, making them a versatile tool for many applications.
3. Cost-Effective
Concrete sandblasting can be a cost-effective surface preparation method compared to other methods, such as chemical stripping or mechanical grinding. It requires less labor and can often be completed in a shorter amount of time, reducing overall project costs.
4. Environmentally Friendly
Some concrete sandblasting machines are designed to be environmentally friendly by reducing dust emissions and using recycled abrasive materials. Wet sandblasting machines, in particular, can significantly reduce dust levels, making them a more sustainable option.
VI. Considerations for Using Concrete Sandblasting Machines
1. Safety
Concrete sandblasting can be a hazardous operation, and proper safety precautions must be taken. Operators should wear appropriate personal protective equipment, such as safety glasses, ear protection, a dust mask, and protective clothing. The work area should also be properly ventilated to reduce dust exposure.
2. Abrasive Material Selection
The choice of abrasive material can have a significant impact on the effectiveness of the sandblasting process. Different abrasive materials have different hardnesses, sizes, and shapes, which can affect the surface finish and removal rate. It is important to select an abrasive material that is suitable for the specific application and surface condition.
3. Surface Damage
Care must be taken to avoid excessive sandblasting, which can cause damage to the concrete surface. Over-sandblasting can lead to pitting, cracking, or weakening of the concrete. It is important to follow the manufacturer's guidelines and use proper blasting techniques to ensure a safe and effective surface preparation.
4. Dust Control
Dust generated during concrete sandblasting can be a significant environmental and health hazard. Adequate dust collection systems should be used to capture and filter the dust, reducing emissions and protecting the operator and surrounding environment.
VII. Maintenance and Care of Concrete Sandblasting Machines
1. Regular Inspection
Regularly inspect the concrete sandblasting machine for signs of wear and damage. Check the hoses, nozzles, and fittings for leaks or cracks. Inspect the abrasive hopper and feeder for blockages or damage.
2. Cleaning
After each use, clean the machine thoroughly to remove any remaining abrasive material and dust. Use compressed air or a vacuum cleaner to clean the hoses, nozzles, and other components. Clean the abrasive hopper and feeder to prevent clogging.
3. Lubrication
Lubricate the moving parts of the machine, such as the compressor or blower, according to the manufacturer's instructions. This will help to reduce wear and prolong the life of the machine.
4. Storage
When not in use, store the concrete sandblasting machine in a dry, clean location. Cover the machine to protect it from dust and moisture. Store the abrasive material in a sealed container to prevent moisture absorption and contamination.
VIII. Conclusion
Concrete sandblasting machines are powerful tools for surface preparation and cleaning of concrete surfaces. They offer efficient, versatile, and cost-effective solutions for a wide range of applications. However, it is important to consider safety, abrasive material selection, surface damage, and dust control when using these machines. By following proper safety procedures and maintenance guidelines, operators can ensure the safe and effective operation of concrete sandblasting machines, providing a clean and prepared surface for coatings, overlays, or other applications.