Hotline
+86-136 8495 9862
Email:cennia@szmizhi.com
Add::104,Building 27,Third Industrial Zone, Longxi Community,Longgang District,Shenzhen,China.
Coil Forming & Handling Equipment
Surface Treatment Equipment
Solutions
Application
About Us
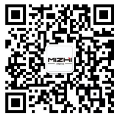
Welcome to MIZHI
For consultation/feedback, please call the service hotline: +86-136 8495 9862 Email:cennia@szmizhi.com
Introduction
A conveyor blasting machine is an important piece of equipment in the field of surface treatment, which combines the functions of material conveyance and blasting to achieve efficient and uniform surface processing of workpieces. It is widely used in various industries such as metal processing, machinery manufacturing, and construction to improve the quality and performance of workpiece surfaces.
Working Principle
The working principle of a conveyor blasting machine mainly involves the use of mechanical or pneumatic power to propel abrasive particles onto the surface of workpieces that are continuously moving on a conveyor belt or roller conveyor. In pneumatic conveyor blasting machines, compressed air is used to accelerate the abrasive media and direct them towards the workpiece surface. The high-speed abrasive particles strike the surface, removing contaminants, rust, scale, or old coatings, and simultaneously roughening or texturing the surface to enhance adhesion for subsequent treatments such as painting or coating. In mechanical conveyor blasting machines, such as wheel blasting machines, a rotating wheel imparts centrifugal force to the abrasives, throwing them onto the workpiece with high velocity.
Types of Conveyor Blasting Machines
Roller Conveyor Shot Blasting Machines: These are designed for processing long and flat workpieces such as plates, sheets, profiles, beams, and pipes. The workpieces are placed on motor-driven roller conveyors and pass through a blasting chamber where shot blast wheels are positioned to direct the abrasive media onto the surface. Different versions of roller conveyor shot blasting machines are available, such as the standard (S) and heavy-duty (H) versions for general plate and section processing, and the construction (C) version for post-fabrication treatment of structural components in industries like shipbuilding, automotive, and construction.
Overhead Conveyor Shot Blasting Machines: Ideal for handling workpieces with complex shapes or those that require all-round blasting. The workpieces are suspended from an overhead conveyor and move through the blasting area, where they are blasted from multiple angles by strategically placed blast guns or wheels. This type of machine is commonly used for treating components like cylinders, large castings, or fabricated structures.
Troughed Belt Conveyor Blasting Machines: Suitable for continuous blasting of bulk materials or small to medium-sized workpieces. The troughed belt conveyor provides a stable and continuous flow of workpieces through the blasting zone, ensuring even coverage and efficient processing. These machines are often used in industries where high-volume production and consistent surface treatment are required.
Suspended Load Shot Blasting Machines: Used for blasting and shot peening of castings, forgings, stamped, and welded assemblies. The workpieces are hung on hooks or fixtures and are rotated or oscillated during the blasting process to ensure complete coverage of the surface. This type of machine is beneficial for achieving uniform surface treatment and strengthening of critical components.
Components of a Conveyor Blasting Machine
Conveyor System: This is the core component responsible for transporting the workpieces through the blasting machine. It can be a roller conveyor, troughed belt conveyor, or overhead conveyor, depending on the type of machine and the nature of the workpieces. The conveyor speed is adjustable to control the residence time of the workpieces in the blasting zone and thus the intensity of the blasting process.
Blasting Unit: Consists of blast wheels, nozzles, or guns that are used to propel the abrasive media onto the workpiece surface. The blast wheels are typically made of wear-resistant materials and are powered by electric motors. The nozzles or guns are designed to control the direction and spread of the abrasive stream, ensuring accurate and efficient surface treatment.
Abrasive Storage and Feeding System: Stores the abrasive material and feeds it continuously to the blasting unit. It includes an abrasive hopper or tank, along with a metering device to control the flow rate of the abrasives. Some machines also have an abrasive recycling system to recover and reuse the spent abrasives, reducing operating costs and environmental impact.
Dust Collection and Filtration System: As the blasting process generates a significant amount of dust, a proper dust collection and filtration system is essential to maintain a clean and healthy working environment. It typically consists of dust collectors, filters, and exhaust fans that capture and remove the dust particles from the air, preventing them from being released into the workplace or the atmosphere.
Control Panel: Allows the operator to control and monitor various parameters of the conveyor blasting machine, such as conveyor speed, blasting pressure, abrasive feed rate, and machine operation time. The control panel may also include safety interlocks and alarms to ensure safe and reliable operation.
Applications of Conveyor Blasting Machines
Surface Preparation for Coating: Conveyor blasting machines are widely used to prepare metal surfaces for painting, powder coating, or other protective coatings. By removing rust, scale, dirt, and other contaminants, and creating a rough surface profile, they improve the adhesion and durability of the coatings, resulting in better corrosion resistance and longer service life of the coated components.
Rust and Scale Removal: In industries such as metal fabrication, construction, and automotive, conveyor blasting is an effective method for removing rust and scale from steel structures, pipes, and components. It restores the original surface condition of the metal, allowing for further processing or use without the negative effects of corrosion.
Shot Peening for Surface Strengthening: Some conveyor blasting machines can be used for shot peening, a process that imparts compressive stresses on the surface of metal components. This helps to increase the fatigue strength, resistance to stress corrosion cracking, and wear resistance of the parts, improving their overall performance and reliability in demanding applications such as aerospace, automotive, and machinery industries.
Deburring and Edge Rounding: Conveyor blasting can also be used to remove burrs and round the edges of machined or fabricated parts, improving their surface finish and reducing the risk of injury during handling or assembly. It provides a consistent and efficient way to achieve the desired edge quality for a large number of workpieces.
Advantages of Using Conveyor Blasting Machines
High Efficiency and Productivity: The continuous operation of the conveyor system allows for a large number of workpieces to be blasted in a relatively short time, significantly increasing production efficiency compared to manual or batch blasting methods. This is especially beneficial for high-volume production lines where quick turnaround and consistent quality are required.
Uniform Surface Treatment: The controlled movement of the workpieces on the conveyor ensures that each part receives a uniform and consistent blast treatment, resulting in a more even surface finish and better quality control. This is crucial for applications where precise surface preparation is necessary, such as in the aerospace and automotive industries.
Versatility: Conveyor blasting machines can handle a wide variety of workpiece shapes, sizes, and materials, making them suitable for diverse manufacturing and processing requirements. They can be easily customized or configured with different conveyor types, blasting units, and abrasive media to meet specific application needs.
Cost-Effective: Although the initial investment in a conveyor blasting machine may be relatively high, the long-term cost savings are significant. The increased productivity, reduced labor requirements, and efficient use of abrasives result in lower overall operating costs per workpiece. Additionally, the improved quality of the surface treatment can reduce the need for rework or premature replacement of components, further saving costs.
Safety Precautions
Personal Protective Equipment: Operators must wear appropriate personal protective equipment, including safety glasses, ear protection, helmets, protective clothing, and gloves, to protect themselves from flying abrasives, dust, and noise generated during the blasting process.
Proper Training: Only trained and authorized personnel should operate the conveyor blasting machine. They should be familiar with the machine's operation, maintenance procedures, safety regulations, and emergency shutdown procedures to ensure safe and correct use.
Dust Control and Ventilation: The dust collection and filtration system should be regularly inspected and maintained to ensure its proper functioning. Adequate ventilation should be provided in the workplace to remove dust and fumes and maintain good air quality. In some cases, additional respiratory protection may be required depending on the dust levels and the nature of the abrasives used.
Machine Guarding: The conveyor blasting machine should be equipped with appropriate safety guards to prevent accidental contact with moving parts, such as the conveyor belt, rollers, and blast wheels. These guards should be in place and properly maintained to ensure the safety of the operators.
Regular Maintenance: Routine maintenance of the conveyor blasting machine is essential to keep it in good working condition and prevent potential safety hazards. This includes checking for wear and tear of components, replacing worn-out parts, cleaning the abrasive system, and ensuring the proper alignment and functioning of the conveyor and blasting units.
Conclusion
Conveyor blasting machines play a vital role in modern manufacturing and surface treatment processes, offering efficient, uniform, and cost-effective solutions for improving the quality and performance of workpiece surfaces. With their various types, components, and applications, they provide manufacturers with the flexibility to meet different production requirements and achieve high-quality surface finishes. By following proper safety precautions and maintenance procedures, these machines can operate reliably and contribute to increased productivity and profitability in a wide range of industries. As technology continues to advance, conveyor blasting machines are likely to become even more efficient, precise, and environmentally friendly, further enhancing their value and importance in the field of surface treatment.