Hotline
+86-136 8495 9862
Email:cennia@szmizhi.com
Add::104,Building 27,Third Industrial Zone, Longxi Community,Longgang District,Shenzhen,China.
Coil Forming & Handling Equipment
Surface Treatment Equipment
Solutions
Application
About Us
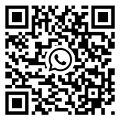
Welcome to MIZHI
For consultation/feedback, please call the service hotline: +86-136 8495 9862 Email:cennia@szmizhi.com
Introduction
In the world of metal processing and manufacturing, the cut to length coil line plays a crucial role. It is a highly specialized piece of equipment that has revolutionized the way metal coils are transformed into precisely sized metal sheets. This article delves deep into the various aspects of cut to length coil lines, including their components, working principles, applications, advantages, and the challenges associated with them.
Components of a Cut to Length Coil Line
1. Uncoiler: This is the starting point of the coil line. The uncoiler is responsible for holding the metal coil and gradually unwinding it. There are different types of uncoilers, such as the fixed - type and the expandable - mandrel type. The expandable - mandrel uncoiler can adapt to different inner diameters of the coils, providing more flexibility in handling various coil sizes. It is equipped with motors and control systems to ensure a smooth and controlled unwinding process.
2. Leveler: Once the metal strip is unwound, it often has some curvature and unevenness due to the coiling process. The leveler is designed to flatten the strip. It consists of multiple rolls that apply controlled pressure to the metal strip, gradually straightening it. The number of rolls and their arrangement can vary depending on the thickness and material of the metal strip. For example, for thicker steel strips, a more robust leveler with a larger number of rolls may be required.
3. Cutting Unit: This is the heart of the cut to length coil line. The cutting unit is responsible for shearing the straightened metal strip into the desired lengths. There are two main types of cutting methods: mechanical shearing and laser cutting. Mechanical shearing uses sharp blades to cut the metal, which is a cost - effective and high - speed method for most common metal materials. Laser cutting, on the other hand, uses a high - energy laser beam to melt and vaporize the metal, providing extremely precise cuts, especially for thinner and more delicate materials or when high - precision edges are required.
4. Stacker: After the metal strips are cut to the desired lengths, they need to be neatly stacked for further processing or storage. The stacker is designed to receive the cut sheets and stack them in an organized manner. It can be automated to adjust the stacking height and ensure that the sheets are stacked evenly, preventing damage to the cut metal sheets.
Working Principle
The operation of a cut to length coil line is a sequential and highly coordinated process. First, the metal coil is loaded onto the uncoiler. The control system of the uncoiler is then activated, and it starts to unwind the coil at a controlled speed. As the metal strip comes out of the uncoiler, it enters the leveler. The leveler's rolls work in tandem to gradually flatten the strip, eliminating any waviness or curvature.
Once the strip is leveled, it moves forward to the cutting unit. The cutting unit is programmed with the desired length of the cut sheets. When the strip reaches the cutting position, the cutting mechanism is activated. In the case of mechanical shearing, the blades close rapidly to cut the strip. For laser cutting, the laser beam is focused on the strip, melting and vaporizing the metal along the cutting line.
After cutting, the individual sheets are conveyed to the stacker. The stacker positions the sheets one by one, creating a neat stack. Throughout the entire process, sensors and control systems are used to monitor and adjust the speed, tension, and position of the metal strip to ensure accurate and efficient operation.
Applications
1. Automotive Industry: In the automotive manufacturing process, cut to length coil lines are used to produce various metal components. For example, the body panels of cars, such as the hood, doors, and fenders, are made from metal sheets that are cut to precise lengths and shapes using these coil lines. The high - precision cuts ensure a perfect fit during the assembly process, improving the overall quality and appearance of the vehicle.
2. Construction Industry: Metal sheets are widely used in the construction industry for roofing, siding, and structural components. Cut to length coil lines are used to produce the required lengths of metal sheets according to the construction plans. The ability to produce large quantities of accurately sized sheets helps in streamlining the construction process and reducing waste.
3. Appliance Manufacturing: Home appliances like refrigerators, washing machines, and ovens require metal sheets for their outer casings and internal components. Cut to length coil lines are used to manufacture these sheets with the exact dimensions needed, ensuring a seamless manufacturing process and a consistent product quality.
Advantages
1. High Precision: Cut to length coil lines can achieve extremely high precision in cutting the metal sheets. The advanced control systems and cutting technologies ensure that the length and width tolerances of the cut sheets are within very narrow limits. This precision is crucial for industries where a perfect fit of components is essential, such as the automotive and aerospace industries.
2. High Efficiency: These coil lines are designed for continuous operation. They can process metal coils at a relatively high speed, reducing the production time per unit of metal sheet. The automated nature of the process, from uncoiling to stacking, also minimizes the need for manual intervention, further increasing productivity.
3. Material Savings: By cutting the metal sheets to the exact required lengths, cut to length coil lines help in reducing material waste. This is especially important considering the high cost of metal materials, and it also contributes to a more sustainable manufacturing process.
Challenges
1. Initial Investment: The purchase and installation of a cut to length coil line can be a significant capital investment. The cost includes not only the equipment itself but also the associated infrastructure, such as a suitable workshop space, electrical systems, and ventilation for laser - cutting - equipped coil lines. Small and medium - sized enterprises may find it difficult to afford such high - cost equipment.
2. Maintenance and Calibration: To ensure the continued high - precision operation of the coil line, regular maintenance and calibration are required. The cutting blades need to be sharpened or replaced regularly in mechanical shearing units, and the laser - cutting systems need to be maintained to ensure the quality of the laser beam. Any deviation in the calibration can lead to inaccurate cuts and reduced product quality.
3. Skilled Labor Requirement: Operating and maintaining a cut to length coil line requires a certain level of technical expertise. Workers need to be trained in setting up the equipment, programming the cutting lengths, and troubleshooting any issues that may arise during operation. The shortage of skilled labor in some regions can pose a challenge to the efficient use of these coil lines.
Future Developments
1. Integration of Smart Technologies: In the future, cut to length coil lines are likely to be integrated with more smart technologies, such as the Internet of Things (IoT) and artificial intelligence (AI). IoT sensors can be used to monitor the performance of the equipment in real - time, sending data to a central control system. AI algorithms can then analyze this data to predict maintenance needs, optimize cutting parameters, and improve overall efficiency.
2. Enhanced Material Compatibility: As new types of metal alloys and composite materials are developed, cut to length coil lines will need to be adapted to handle these materials. This may involve the development of new cutting technologies and leveler designs to ensure that these advanced materials can be processed with the same level of precision and efficiency as traditional metals.
In conclusion, the cut to length coil line is an essential piece of equipment in the metal - processing industry. Its components, working principles, wide range of applications, numerous advantages, and the challenges it faces all contribute to its significance in modern manufacturing. With future developments on the horizon, it is set to play an even more crucial role in the evolving landscape of metal manufacturing.
"CR Cut - to - Length Machine: A Comprehensive Exploration"
I. Introduction
In the realm of modern manufacturing and industrial processing, the CR Cut - to - Length Machine stands as a crucial piece of equipment. It plays a pivotal role in various industries, from metalworking to the production of building materials, by precisely cutting materials to the required lengths. This machine has revolutionized the way manufacturers handle raw materials, enhancing efficiency, reducing waste, and ensuring consistent product quality.
II. Working Principle
1. Material Feeding
The process begins with the feeding of the raw material, which can be in the form of coils, sheets, or long strips. For coil - fed CR Cut - to - Length Machines, a decoiling mechanism is used. This mechanism carefully unwinds the coil, ensuring a smooth and continuous supply of the material. In the case of sheet or strip - fed machines, the materials are manually or automatically loaded onto the feeding table.
2. Measurement and Detection
Accurate measurement is the heart of the cut - to - length operation. Most CR Cut - to - Length Machines are equipped with advanced measuring systems. These can include encoders, which are mechanical or optical devices that track the movement of the material. As the material moves through the machine, the encoder records the distance traveled. Laser sensors are also commonly used for highly precise measurements. They emit a laser beam onto the material, and the reflection of the beam is detected to calculate the position and length of the material.
3. Cutting Process
Once the desired length is measured, the cutting mechanism comes into action. There are several cutting methods employed in CR Cut - to - Length Machines. Shearing is a common method, where sharp blades are used to cut through the material. The blades can be designed in different shapes and configurations depending on the type of material and the required cut quality. For example, in metal - cutting applications, hardened steel blades are used to ensure clean and precise cuts. Plasma cutting is another option, especially for cutting thick metal sheets. This method uses a high - temperature plasma arc to melt and vaporize the material, creating a cut. Laser cutting is also gaining popularity, especially for materials that require extremely high - precision cuts, such as thin - gauge metals or plastics.
III. Types of CR Cut - to - Length Machines
1. Roll - to - Roll Cut - to - Length Machines
These machines are mainly used for processing materials in coil form. They are widely used in the metal stamping industry, where coils of steel, aluminum, or other metals are cut into precise lengths before being further processed into components such as automotive parts, electrical enclosures, and household appliances. The roll - to - roll cut - to - length machines can handle a wide range of coil widths and thicknesses, making them highly versatile.
2. Sheet - Fed Cut - to - Length Machines
Sheet - fed CR Cut - to - Length Machines are designed for processing pre - cut sheets of materials. They are commonly used in the construction industry for cutting building materials such as plywood, drywall, and metal sheets. These machines can handle sheets of different sizes and thicknesses, and they are often equipped with features such as adjustable cutting fences and multiple cutting heads to increase productivity.
3. Special - Purpose Cut - to - Length Machines
There are also special - purpose CR Cut - to - Length Machines designed for specific applications. For example, in the wire and cable industry, there are machines that can cut wires and cables to precise lengths, often with additional features such as stripping the insulation at the ends. In the textile industry, cut - to - length machines are used to cut fabric rolls into specific lengths for garment production.
IV. Applications
1. Automotive Industry
In the automotive manufacturing process, the CR Cut - to - Length Machine is used for cutting various metal components. For example, it cuts the steel sheets used for car body panels, ensuring that each panel has the correct dimensions. The precise cutting provided by these machines is crucial for the proper fit and assembly of the car parts. It also cuts the metal rods and tubes used in the chassis and engine components, contributing to the overall structural integrity and performance of the vehicle.
2. Construction Industry
In construction, the CR Cut - to - Length Machine is used for processing a wide range of materials. It cuts the steel reinforcement bars (rebar) used in concrete structures, ensuring that the rebars are of the correct length for different construction applications. It also cuts the metal sheets used for roofing, siding, and structural components. In addition, it can cut non - metallic materials such as plywood and PVC pipes, which are commonly used in building interiors and plumbing systems.
3. Electronics Industry
In the electronics manufacturing, the CR Cut - to - Length Machine is used for cutting materials such as copper foils, which are used in printed circuit boards (PCBs). The precise cutting of these foils is essential for the proper functioning of the PCBs. It also cuts the plastic sheets and metal enclosures used for housing electronic components, ensuring a perfect fit and protection for the delicate electronics.
V. Advantages
1. High Precision
The CR Cut - to - Length Machine offers an extremely high level of precision. With advanced measurement and cutting technologies, it can achieve cutting tolerances of up to ±0.1mm or even less in some high - end models. This precision ensures that the cut materials fit perfectly into the subsequent manufacturing processes, reducing the need for rework and improving overall product quality.
2. Increased Efficiency
These machines can operate at high speeds, significantly increasing the production rate. For example, a modern roll - to - roll cut - to - length machine can process hundreds of meters of material per minute. The automated feeding and cutting processes also reduce the need for manual labor, further enhancing efficiency.
3. Waste Reduction
By precisely cutting materials to the required lengths, the CR Cut - to - Length Machine minimizes waste. In traditional cutting methods, there is often a significant amount of material wasted due to inaccurate cuts. With the high - precision cutting of these machines, manufacturers can optimize the use of raw materials, leading to cost savings.
4. Versatility
CR Cut - to - Length Machines can handle a wide variety of materials, including different types of metals, plastics, and composites. They can also be adjusted to cut materials of different thicknesses and widths, making them suitable for a wide range of applications.
VI. Challenges and Solutions
1. Wear and Tear of Cutting Tools
The cutting tools in a CR Cut - to - Length Machine, such as blades or plasma torches, are subject to wear and tear during operation. This can affect the cutting quality and the machine's performance. To address this issue, manufacturers often use high - quality, wear - resistant cutting tools. Regular maintenance and replacement of the cutting tools are also essential. Some advanced machines are equipped with automatic tool - monitoring systems that can detect the wear of the cutting tools and alert the operator when replacement is needed.
2. Material Variability
Different batches of raw materials may have slight variations in their properties, such as thickness, hardness, or surface finish. These variations can pose challenges to the cutting process. To overcome this, modern CR Cut - to - Length Machines are often equipped with sensors that can detect the properties of the incoming material and adjust the cutting parameters accordingly. For example, if the material is slightly thicker than normal, the machine can automatically increase the cutting force or adjust the cutting speed to ensure a clean cut.
3. Integration with Other Systems
In some manufacturing processes, the CR Cut - to - Length Machine needs to be integrated with other equipment, such as stamping machines, welding robots, or automated conveyor systems. Ensuring seamless integration can be a challenge. To solve this, manufacturers are increasingly adopting standard communication protocols and interfaces in their machines. This allows for easier integration with other systems and enables the implementation of fully automated manufacturing lines.
VII. Future Trends
1. Automation and Robotics Integration
The future of CR Cut - to - Length Machines lies in increased automation and integration with robotics. More advanced machines will be able to operate with minimal human intervention, with robots handling tasks such as material loading, unloading, and quality inspection. This will not only increase productivity but also improve workplace safety.
2. Smart Manufacturing and IoT Connectivity
CR Cut - to - Length Machines will be increasingly connected to the Internet of Things (IoT). This will allow manufacturers to monitor the machine's performance in real - time, receive alerts for maintenance needs, and analyze production data to optimize the manufacturing process. Smart sensors will be used to collect data on factors such as cutting force, temperature, and material quality, enabling predictive maintenance and process improvements.
3. Advanced Cutting Technologies
New and improved cutting technologies will continue to emerge. For example, the development of more powerful and precise laser cutting systems will allow for even higher - quality cuts on a wider range of materials. The use of water - jet cutting in combination with other cutting methods may also become more common, offering unique advantages in terms of cut quality and material compatibility.
In conclusion, the CR Cut - to - Length Machine is an indispensable piece of equipment in modern manufacturing. Its precise cutting capabilities, high efficiency, and versatility make it a key component in various industries. As technology continues to advance, these machines will play an even more significant role in the future of manufacturing, driving innovation and productivity improvements.