Hotline
+86-136 8495 9862
Email:cennia@szmizhi.com
Add::104,Building 27,Third Industrial Zone, Longxi Community,Longgang District,Shenzhen,China.
Coil Forming & Handling Equipment
Surface Treatment Equipment
Solutions
Application
About Us
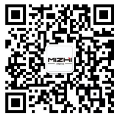
Welcome to MIZHI
For consultation/feedback, please call the service hotline: +86-136 8495 9862 Email:cennia@szmizhi.com
I. Definition and Purpose
A cut to length production line is a sophisticated industrial setup designed to transform raw metal coils into precisely cut sheets or strips of specific lengths. It is a fundamental component in various manufacturing sectors, including automotive, construction, appliance, and metal fabrication industries. The primary objective of this production line is to meet the exacting dimensional requirements of end products, ensuring consistency and quality in the manufacturing process.
II. Key Components and Their Functions
1. Uncoiling Unit
The process begins with the uncoiling unit, which houses the large metal coil. This unit is equipped with a mandrel or expansion shaft that holds the coil securely in place. As the production progresses, the coil rotates, allowing the metal strip to unwind smoothly. Variable speed drives are often incorporated to control the rate of uncoiling, matching it with the downstream processing speeds. For example, in a high volume automotive stamping plant, precise control of uncoiling speed is crucial to prevent any sudden jerks or stoppages that could damage the metal or disrupt the production flow.
Additionally, tension control devices are present. These maintain a constant tension on the unwinding metal strip, preventing it from wrinkling, sagging, or getting tangled. This is achieved through load cells and feedback control systems that continuously adjust the braking or driving force on the uncoiler.
2. Leveling Unit
After uncoiling, the metal strip typically enters a leveling unit. Metal coils, especially those stored for extended periods or transported, can develop internal stresses that cause warping or curling. The leveling unit uses a series of adjustable rollers, arranged in a specific pattern. These rollers apply pressure and bending forces in opposite directions to flatten the metal, removing any residual stresses and ensuring a flat, planar surface. In the production of high precision sheet metal components for electronics, a perfectly leveled surface is essential as even minor deformities can affect the functionality and assembly of the final product.
3. Cutting Unit
The cutting unit is the heart of the cut to length production line. There are several cutting technologies employed, depending on the material thickness, type, and production requirements. Shearing machines are commonly used for thicker metal sheets. They work on the principle of applying a large force perpendicular to the metal strip to make a clean, straight cut. For thinner materials, rotary cutters or laser cutting systems may be utilized.
Rotary cutters use a circular blade that rotates at high speed to slice through the metal. Laser cutting, on the other hand, offers extremely high precision and can create intricate shapes and patterns. In the aerospace industry, where complex geometries and tight tolerances are required, laser cutting is often the preferred method. The cutting unit is usually synchronized with the upstream and downstream processes through advanced control systems, ensuring accurate cut lengths and minimal waste.
4. Stacking and Packaging Unit
Once the metal sheets are cut to the desired lengths, they enter the stacking and packaging unit. Automated stacking systems arrange the sheets in neat piles, either horizontally or vertically, depending on the handling and storage requirements. These stacks can then be bundled together using straps or shrink wrap for protection during transportation and storage. In a construction materials manufacturing facility, the stacking and packaging process is designed to optimize space utilization in warehouses and on delivery trucks, while also safeguarding the integrity of the metal sheets.
III. Operation and Workflow
1. Initial Setup
Before starting production, operators must load the appropriate metal coil onto the uncoiling unit. This involves carefully aligning the coil and ensuring proper engagement with the mandrel. The leveling and cutting parameters are then set based on the job requirements. For instance, if producing sheets for a specific appliance model, the thickness, width, and length settings are inputted into the control system. The cutting unit's blade or laser power and speed may also need adjustment to achieve the best cutting quality.
2. Continuous Production
Once the setup is complete, the production line springs into action. The metal coil unwinds at a controlled pace, passes through the leveling unit to be flattened, and then reaches the cutting unit. Here, it is cut into precise lengths as per the programmed specifications. The cut sheets are immediately transferred to the stacking and packaging unit, where they are organized and prepared for shipment or further processing. Throughout this process, sensors and feedback loops continuously monitor the quality of the metal strip, the cutting accuracy, and the stack height, making real time adjustments to maintain optimal performance.
3. Quality Control and Monitoring
Quality control is an integral part of the cut to length production line operation. Visual inspection systems are often installed to detect any surface defects, such as scratches, dents, or discoloration. Dimensional measurement tools, like laser gauges or calipers, check the cut lengths, widths, and thicknesses against the preset tolerances. In case of any deviations, the production line can be paused automatically, and an alarm raised to alert the operators. This ensures that only high quality, accurately cut metal sheets are released for downstream use.
IV. Types of Cut to Length Production Lines
1. Heavy Duty Production Lines
These are designed for processing thick and wide metal coils, typically used in industries like shipbuilding, heavy machinery manufacturing, and large scale construction. They are equipped with powerful motors, robust rollers, and high capacity cutting systems to handle materials with thicknesses ranging from several millimeters to even centimeters. The uncoiling units can support extremely heavy coils, and the leveling and cutting processes are optimized for maximum efficiency and precision in dealing with such massive loads.
2. High Precision Production Lines
In sectors such as electronics, medical devices, and precision engineering, high precision cut to length production lines are essential. These lines feature ultra fine leveling mechanisms, advanced laser cutting or micro shearing technologies, and highly sensitive quality control systems. The tolerances for cut lengths and sheet dimensions can be as tight as a few microns. For example, in the production of microelectronic substrates, any deviation from the exact size could render the product unusable.
3. Flexible Production Lines
To meet the demands of small batch and custom manufacturing, flexible cut to length production lines have emerged. These lines are easily programmable and can quickly switch between different material types, thicknesses, and cut length requirements. They often incorporate modular components that can be reconfigured, allowing manufacturers to adapt to changing market needs without significant downtime or costly equipment overhauls.
V. Advantages of Cut to Length Production Lines
1. Accuracy and Consistency
By automating the cutting process and relying on advanced control systems, cut to length production lines ensure that each sheet is cut to the precise length and dimension. This level of accuracy is crucial in industries where components must fit together perfectly, like automotive assembly lines. The consistent quality also reduces the need for rework and waste, saving both time and materials.
2. High Productivity
These production lines can operate continuously, with minimal stoppages for coil changes or maintenance. The synchronized operation of the uncoiling, leveling, cutting, and stacking units allows for a rapid throughput of metal sheets. In a busy steel service center, a well maintained cut to length production line can process dozens of tons of metal per day, meeting tight production schedules.
3. Material Savings
With precise cutting and minimal waste generation, manufacturers can make the most of their raw materials. The ability to optimize cut lengths based on actual production needs means fewer offcuts and scrap, translating into cost savings. Additionally, the efficient use of materials helps reduce the environmental impact associated with metal production.
VI. Maintenance and Safety Considerations
1. Maintenance
Regular maintenance is vital to keep the cut to length production line running smoothly. The rollers in the uncoiling, leveling, and transport units need to be lubricated and inspected for wear. The cutting blades, whether shearing or rotary, must be sharpened or replaced regularly. The control systems and sensors also require calibration to ensure accurate operation. Manufacturers typically provide detailed maintenance schedules and procedures, which operators should follow strictly.
2. Safety
Given the presence of heavy machinery, moving parts, and cutting operations, safety is a top priority. Safety guards are installed around the uncoiling, leveling, and cutting units to prevent operators from coming into contact with dangerous elements. Emergency stop buttons are strategically placed throughout the production line, allowing for immediate shutdown in case of an accident or malfunction. Additionally, operators are trained in proper safety procedures, including the use of personal protective equipment such as safety glasses, gloves, and steel toe boots.
VII. Conclusion
Cut to length production lines are indispensable in modern manufacturing. Their ability to transform raw metal coils into accurately cut, high quality sheets with high productivity and minimal waste makes them a cornerstone of numerous industries. As technology continues to advance, these production lines will likely become even more efficient, precise, and adaptable, further fueling innovation and growth in the global manufacturing sector. Whether it's building the next generation of automobiles, constructing state of the art buildings, or manufacturing life saving medical devices, cut to length production lines will play a pivotal role in bringing these visions to life.