Hotline
+86-136 8495 9862
Email:cennia@szmizhi.com
Add::104,Building 27,Third Industrial Zone, Longxi Community,Longgang District,Shenzhen,China.
Coil Forming & Handling Equipment
Surface Treatment Equipment
Solutions
Application
About Us
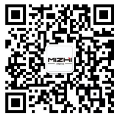
Welcome to MIZHI
For consultation/feedback, please call the service hotline: +86-136 8495 9862 Email:cennia@szmizhi.com
In the world of metal processing and fabrication, a heavy gauge cut to length line plays a crucial role in transforming large coils of metal into precisely cut sheets of specific lengths. This advanced machinery is designed to handle thick and heavy metal sheets with high precision and efficiency, meeting the demanding requirements of various industries.
I. Introduction
The heavy gauge cut to length line is a specialized piece of equipment that is essential for businesses involved in metal processing, manufacturing, and construction. These lines are capable of cutting metal sheets with thicknesses ranging from several millimeters to several inches, depending on the specific model and capabilities. With the ability to handle heavy gauges, these machines offer a reliable and efficient solution for producing large-format metal sheets for a wide range of applications.
II. Components of a Heavy Gauge Cut to Length Line
1. Uncoiler
The uncoiler is the first component of a heavy gauge cut to length line. It is responsible for unwinding the large coil of metal and feeding it into the line. Uncoilers can be either hydraulic or mechanical and are designed to handle heavy loads.
Some uncoilers come with features such as coil car loading systems, which make it easier to load and unload the coils. Additionally, automatic coil centering systems ensure that the coil is properly aligned for smooth feeding into the line.
2. Straightener
After the metal coil is unwound, it passes through the straightener. The straightener is designed to remove any curvature or distortion in the metal sheet, ensuring that it is flat and ready for cutting.
Heavy gauge cut to length lines typically use multiple roll straighteners, which can handle the thick and heavy metal sheets. These straighteners are adjustable to accommodate different gauges and types of metals.
3. Shear or Guillotine Cutter
The shear or guillotine cutter is the heart of the heavy gauge cut to length line. It is responsible for cutting the metal sheet into the desired lengths with high precision.
Shear cutters are typically used for thinner gauges, while guillotine cutters are better suited for thicker gauges. Both types of cutters can be hydraulically or mechanically operated and are designed to provide clean and accurate cuts.
4. Stacker or Conveyor System
Once the metal sheet is cut, it needs to be stacked or conveyed for further processing or storage. Stackers are used to stack the cut sheets in an organized manner, while conveyor systems can transport the sheets to different locations within the facility.
Some heavy gauge cut to length lines come with automated stackers or conveyors, which can increase productivity and reduce labor costs.
III. Working Principle of a Heavy Gauge Cut to Length Line
The working principle of a heavy gauge cut to length line is relatively straightforward. The metal coil is first unwound by the uncoiler and fed into the straightener. The straightener removes any curvature or distortion in the metal sheet, making it flat and ready for cutting. The straightened sheet then passes through the shear or guillotine cutter, which cuts it into the desired lengths. Finally, the cut sheets are stacked or conveyed for further processing or storage.
During the cutting process, the length and width of the metal sheet can be precisely controlled by adjusting the settings on the cutter. Some heavy gauge cut to length lines also come with automated measurement and control systems, which ensure accurate cutting and minimize waste.
IV. Applications of Heavy Gauge Cut to Length Lines
1. Construction Industry
In the construction industry, heavy gauge cut to length lines are used to produce metal sheets for roofing, siding, and structural components. These sheets are often made of steel or aluminum and are cut to specific lengths and widths to meet the requirements of different construction projects.
The ability to handle heavy gauges makes these lines ideal for producing large-format metal sheets that can withstand the rigors of construction sites.
2. Automotive Industry
The automotive industry also uses heavy gauge cut to length lines to produce metal parts for vehicles. These parts can include body panels, chassis components, and engine parts.
The precision cutting capabilities of these lines ensure that the metal parts are accurately sized and shaped, which is essential for proper fit and function in vehicles.
3. Manufacturing Industry
In the manufacturing industry, heavy gauge cut to length lines are used to produce metal sheets for a wide range of applications, including machinery parts, electrical enclosures, and storage tanks.
The ability to handle different gauges and types of metals makes these lines versatile and suitable for a variety of manufacturing processes.
4. Other Industries
Heavy gauge cut to length lines are also used in other industries such as shipbuilding, aerospace, and energy. These industries require large-format metal sheets for various applications, and the precision cutting capabilities of these lines make them an ideal choice.
V. Advantages of Heavy Gauge Cut to Length Lines
1. High Precision Cutting
Heavy gauge cut to length lines are designed to provide high precision cutting, ensuring that the metal sheets are cut to the exact lengths and widths required. This precision is essential for applications where accurate sizing and fit are critical.
Some lines come with automated measurement and control systems, which further enhance the cutting accuracy and minimize waste.
2. High Production Capacity
These lines are capable of handling large coils of metal and cutting them into sheets at a high speed. This high production capacity makes them ideal for large-scale manufacturing and processing operations.
The ability to handle heavy gauges also means that these lines can produce large-format metal sheets in a single pass, reducing production time and increasing efficiency.
3. Versatility
Heavy gauge cut to length lines can handle a wide range of gauges and types of metals, making them versatile and suitable for a variety of applications. This versatility allows businesses to process different types of metals and meet the diverse needs of their customers.
4. Cost-Effective
Compared to other metal processing methods, heavy gauge cut to length lines are often more cost-effective. They can reduce material waste, labor costs, and production time, resulting in lower overall costs.
Additionally, the ability to handle heavy gauges means that businesses can use thicker metal sheets, which can provide greater strength and durability, reducing the need for additional reinforcement or support.
VI. Considerations When Choosing a Heavy Gauge Cut to Length Line
1. Capacity and Gauge Range
Consider the capacity and gauge range of the heavy gauge cut to length line to ensure that it can handle the thicknesses and sizes of metal sheets required for your applications.
Some lines are designed to handle specific gauges or types of metals, so it is important to choose a line that is suitable for your specific needs.
2. Cutting Accuracy
Look for a heavy gauge cut to length line that offers high cutting accuracy to ensure that the metal sheets are cut to the exact lengths and widths required. This is especially important for applications where precision is critical.
Consider factors such as the type of cutter used, the accuracy of the measurement and control systems, and the repeatability of the cutting process.
3. Production Capacity
Determine your production requirements and choose a heavy gauge cut to length line that can meet your production needs. Consider factors such as the speed of the line, the size of the coils it can handle, and the number of cuts per minute.
4. Reliability and Durability
Look for a heavy gauge cut to length line that is reliable and durable, with a proven track record of performance. Consider factors such as the quality of the components, the construction of the line, and the availability of spare parts and service.
5. Automation and Control Features
Consider the automation and control features of the heavy gauge cut to length line. Automated measurement and control systems can improve cutting accuracy and productivity, while features such as programmable cut lengths and widths can increase flexibility.
VII. Maintenance and Operation of Heavy Gauge Cut to Length Lines
1. Regular Maintenance
To ensure the reliable operation of a heavy gauge cut to length line, it is important to perform regular maintenance. This includes lubricating the moving parts, checking the alignment of the components, and inspecting the cutter for wear and damage.
Follow the manufacturer's recommended maintenance schedule and keep detailed records of all maintenance activities.
2. Operator Training
Operators should be trained on the proper operation and safety procedures of the heavy gauge cut to length line. This includes understanding the controls, knowing how to load and unload coils, and being able to troubleshoot common issues.
Provide ongoing training and refresher courses to ensure that operators are up to date on the latest operating procedures and safety guidelines.
3. Safety Precautions
Heavy gauge cut to length lines can be dangerous if not operated properly. Follow all safety guidelines and procedures, including wearing appropriate personal protective equipment, keeping hands and feet away from the cutter, and ensuring that the line is properly guarded.
Install safety devices such as emergency stop buttons and safety interlocks to prevent accidents.
VIII. Future Trends in Heavy Gauge Cut to Length Lines
1. Automation and Digitalization
The future of heavy gauge cut to length lines is likely to be more automated and digitalized. Look for features such as automated coil loading and unloading, intelligent cutting systems, and real-time monitoring and control.
Digitalization can also improve productivity and quality control by providing data on production processes and equipment performance.
2. Energy Efficiency
As energy costs continue to rise, there is an increasing demand for energy-efficient heavy gauge cut to length lines. Look for features such as energy-saving motors, variable frequency drives, and optimized cutting processes to reduce energy consumption.
3. Customization and Flexibility
Manufacturers are increasingly offering heavy gauge cut to length lines that can be customized to meet specific customer requirements. This may include options for different cutter types, gauges, and lengths, as well as the ability to integrate with other production processes.
Flexibility in design can also allow for easy adaptation to changing market demands and production requirements.
IX. Conclusion
Heavy gauge cut to length lines are essential pieces of equipment for businesses involved in metal processing and fabrication. These lines offer high precision cutting, high production capacity, versatility, and cost-effectiveness, making them ideal for a wide range of applications. When choosing a heavy gauge cut to length line, consider factors such as capacity, cutting accuracy, production capacity, reliability, and automation features. Additionally, proper maintenance and operation are crucial for ensuring the reliable performance and longevity of the line. With the right heavy gauge cut to length line, businesses can improve their production processes, reduce costs, and meet the demanding requirements of their customers.