Hotline
+86-136 8495 9862
Email:cennia@szmizhi.com
Add::104,Building 27,Third Industrial Zone, Longxi Community,Longgang District,Shenzhen,China.
Coil Forming & Handling Equipment
Surface Treatment Equipment
Solutions
Application
About Us
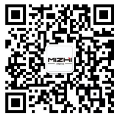
Welcome to MIZHI
For consultation/feedback, please call the service hotline: +86-136 8495 9862 Email:cennia@szmizhi.com
Roll forming machines are highly efficient and versatile pieces of equipment that play a crucial role in the manufacturing industry. They are used to shape flat metal sheets or strips into a variety of profiles with consistent cross sectional shapes. If you're in the market for a roll forming machine, here's a comprehensive guide to help you understand what's available and what to consider.
I. What is a Roll Forming Machine?
A roll forming machine is a mechanical device that continuously bends a long strip of metal through a series of rollers. Each roller in the machine progressively shapes the metal until it reaches the desired profile. The process is highly automated and can produce complex shapes with high precision.
The basic components of a roll forming machine include an uncoiler, a roll forming section, a cutting device, and a run out table. The uncoiler holds the coil of raw material (usually metal sheet or strip) and feeds it into the roll forming section. The roll forming section consists of multiple sets of rollers, each set performing a specific bending operation. The cutting device is used to cut the formed profile to the desired length, and the run out table provides a surface for the finished products to be collected.
II. Types of Roll Forming Machines
1. Single Stand Roll Forming Machines
These are relatively simple machines that have a single set of roll stands. They are suitable for forming simple profiles with fewer bends. Single stand machines are often used for small scale production or for prototyping purposes. They are cost effective and easy to operate, making them a popular choice for small businesses or hobbyists.
2. Multi Stand Roll Forming Machines
Multi stand roll forming machines have multiple sets of roll stands, allowing for more complex profile shapes. These machines can handle a wide range of materials and thicknesses. They are designed for high volume production and can produce profiles with a high degree of precision. The number of roll stands can vary depending on the complexity of the profile, with some advanced machines having dozens of stands.
3. Custom Built Roll Forming Machines
For specific and unique manufacturing requirements, custom built roll forming machines are available. These machines are designed and engineered according to the customer's exact specifications. They can incorporate special features such as additional forming stations, advanced cutting systems, or integration with other manufacturing processes. Custom built machines are often used in industries where standard machines cannot meet the required production standards or product geometries.
III. Applications of Roll Forming Machines
1. Construction Industry
In the construction industry, roll forming machines are used to produce a wide range of products such as roofing panels, wall panels, and purlins. Roofing panels can be formed into various shapes and profiles to provide both aesthetic and functional benefits. Wall panels can be customized to fit different building designs and insulation requirements. Purlins are structural components that provide support for roofing and siding materials.
2. Automotive Industry
Roll forming machines are used to manufacture automotive parts such as window frames, door frames, and bumper reinforcements. The ability to produce parts with precise shapes and consistent quality is crucial in the automotive sector, where safety and performance are of utmost importance.
3. Furniture Industry
In the furniture industry, roll forming machines are used to produce metal frames for chairs, tables, and other furniture items. The machines can form decorative and functional profiles that enhance the aesthetic appeal and structural integrity of the furniture.
4. HVAC (Heating, Ventilation, and Air Conditioning) Industry
HVAC ducts and fittings are often produced using roll forming machines. The machines can form ducts with different shapes and sizes to ensure efficient air distribution. Fittings such as elbows, tees, and reducers can also be formed to connect different sections of the ductwork.
IV. Factors to Consider When Buying a Roll Forming Machine for Sale
1. Material Compatibility
The machine should be capable of handling the type of material you plan to use. Different metals such as steel, aluminum, and copper have different mechanical properties, and the machine's rollers and drive system need to be adjusted accordingly. For example, if you're working with high strength steel, the machine may need more powerful motors and sturdier rollers to handle the material's hardness and thickness.
2. Profile Complexity
Consider the complexity of the profiles you need to produce. Simple profiles may require a less elaborate machine, while complex shapes with multiple bends and contours will need a more advanced multi stand roll forming machine. Look at the number of roll stands, the adjustability of the rollers, and the machine's ability to handle different forming sequences.
3. Production Volume
Your production requirements play a significant role in choosing the right machine. If you're a small scale producer with intermittent orders, a single stand or a less powerful multi stand machine may suffice. However, for high volume production, you'll need a machine with a high speed feeding system, efficient cutting mechanism, and reliable continuous operation capabilities.
4. Accuracy and Precision
The precision of the roll forming machine is essential, especially if you're manufacturing parts with tight tolerances. Look for machines with high quality roller bearings, accurate drive systems, and advanced control mechanisms. Some machines come with computer controlled systems that can adjust the roller positions in real time to ensure consistent profile formation.
5. Safety Features
Roll forming machines can be dangerous due to the moving parts and the high pressure operations involved. Ensure that the machine you're considering has adequate safety features such as emergency stop buttons, safety guards around the rollers and cutting area, and interlocks to prevent accidental operation.
6. After Sales Service and Support
When buying a roll forming machine, it's important to consider the after sales service provided by the manufacturer or seller. Look for a company that offers installation support, training for your operators, and reliable technical support in case of breakdowns or maintenance issues. A good warranty policy is also a plus.
V. Pricing of Roll Forming Machines
The price of roll forming machines can vary widely depending on several factors. Single stand machines for simple applications can start from a few thousand dollars, while multi stand high volume production machines can cost hundreds of thousands of dollars. Custom built machines are usually more expensive due to the additional engineering and customization involved.
The cost also depends on the machine's capacity, the quality of its components (such as rollers, motors, and control systems), and any additional features like automation or integration with other systems. It's essential to get quotes from different manufacturers and compare the features and prices to find the best value for your money.
VI. Maintenance and Operation of Roll Forming Machines
1. Regular Maintenance
Proper maintenance is crucial to keep the roll forming machine in good working condition. This includes routine inspections of the rollers, bearings, drive systems, and cutting devices. Lubrication of the moving parts should be done regularly according to the manufacturer's instructions. The rollers may need to be adjusted or replaced over time to maintain the accuracy of the profile formation.
2. Operator Training
Operators should be well trained in the operation of the roll forming machine. They need to understand the machine's controls, safety procedures, and how to adjust the settings for different profiles and materials. Training programs provided by the manufacturer or through third party institutions can help ensure that the operators can use the machine efficiently and safely.
3. Troubleshooting
Despite regular maintenance, problems may still arise. Common issues include misalignment of the rollers, material jams, or problems with the cutting mechanism. Having a good understanding of the machine's operation and access to troubleshooting guides or technical support can help quickly resolve these issues and minimize downtime.
In conclusion, when looking for a roll forming machine for sale, it's essential to thoroughly understand your manufacturing needs, the capabilities of different machines, and the factors that affect their performance and price. By carefully considering these aspects, you can make an informed decision and invest in a roll forming machine that will meet your production requirements and provide a good return on investment.