Hotline
+86-136 8495 9862
Email:cennia@szmizhi.com
Add::104,Building 27,Third Industrial Zone, Longxi Community,Longgang District,Shenzhen,China.
Coil Forming & Handling Equipment
Surface Treatment Equipment
Solutions
Application
About Us
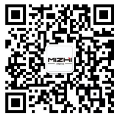
Welcome to MIZHI
For consultation/feedback, please call the service hotline: +86-136 8495 9862 Email:cennia@szmizhi.com
Roof panel machines are essential tools in the construction industry for manufacturing various types of roof panels. These machines offer efficient and cost-effective solutions for producing high-quality roof panels that meet the specific requirements of different construction projects. In this article, we will provide a comprehensive introduction to roof panel machines for sale, including their types, features, applications, and benefits.
I. Introduction to Roof Panel Machines
Roof panel machines are designed to fabricate roof panels from different materials such as metal, plastic, or composite materials. These machines use advanced technology and automation to ensure precise and consistent production of roof panels with different shapes, sizes, and profiles. The roof panel machines can be customized to meet the specific needs of different customers, depending on the type of material, panel design, and production volume.
II. Types of Roof Panel Machines
1. Roll Forming Machines
Roll forming machines are the most common type of roof panel machines. These machines use a series of rollers to gradually shape a flat sheet of material into a specific roof panel profile. Roll forming machines can produce a wide range of roof panel profiles, including corrugated, trapezoidal, and standing seam panels. They are suitable for producing large quantities of roof panels with consistent quality and dimensions.
2. Press Brake Machines
Press brake machines are used to bend and form metal sheets into roof panels. These machines use hydraulic or mechanical pressure to bend the metal sheets at specific angles and shapes. Press brake machines are suitable for producing custom-shaped roof panels or for small-scale production runs.
3. Injection Molding Machines
Injection molding machines are used to produce plastic roof panels. These machines inject molten plastic into a mold cavity to create the desired roof panel shape. Injection molding machines are suitable for producing large quantities of plastic roof panels with complex designs and high precision.
4. Composite Panel Machines
Composite panel machines are used to produce roof panels made of composite materials, such as fiberglass-reinforced plastic (FRP) or insulated metal panels (IMP). These machines combine different materials and processes to create roof panels with excellent insulation, durability, and aesthetic appeal.
III. Features of Roof Panel Machines
1. High Production Efficiency
Roof panel machines are designed for high-speed production, enabling manufacturers to produce large quantities of roof panels in a short period. The advanced automation and control systems of these machines ensure consistent quality and dimensional accuracy, reducing the need for manual labor and increasing production efficiency.
2. Customizable Panel Designs
Roof panel machines can be customized to produce different panel designs and profiles, depending on the specific requirements of the construction project. Manufacturers can choose from a wide range of panel shapes, sizes, colors, and finishes to create unique and aesthetically pleasing roof panels.
3. Durable and Reliable Construction
Roof panel machines are built with high-quality materials and components to ensure durability and reliability. The machines are designed to withstand heavy use and harsh working conditions, providing long-term service and minimal maintenance requirements.
4. Advanced Automation and Control Systems
Roof panel machines are equipped with advanced automation and control systems that enable precise control of the production process. These systems can adjust the speed, pressure, and temperature of the machine to ensure optimal production conditions and consistent panel quality.
5. Safety Features
Roof panel machines are designed with safety features to protect operators and prevent accidents. These features may include safety guards, emergency stop buttons, and interlocks to ensure safe operation of the machine.
IV. Applications of Roof Panel Machines
1. Residential Construction
Roof panel machines are widely used in residential construction for producing roof panels for houses, townhouses, and apartments. The different types of roof panels produced by these machines offer various benefits, such as durability, insulation, and aesthetic appeal, making them ideal for residential roofing applications.
2. Commercial Construction
In commercial construction, roof panel machines are used to produce roof panels for buildings such as offices, warehouses, and shopping centers. The high-quality and customizable roof panels produced by these machines can meet the specific requirements of different commercial projects, providing long-term durability and energy efficiency.
3. Industrial Construction
Roof panel machines are also used in industrial construction for producing roof panels for factories, plants, and storage facilities. The durable and corrosion-resistant roof panels produced by these machines can withstand harsh industrial environments and provide reliable protection for industrial buildings.
4. Agricultural Construction
In agricultural construction, roof panel machines are used to produce roof panels for barns, sheds, and greenhouses. The lightweight and cost-effective roof panels produced by these machines can provide good insulation and ventilation for agricultural buildings, protecting crops and livestock.
V. Benefits of Roof Panel Machines
1. Cost-Effective Production
Roof panel machines offer cost-effective solutions for producing roof panels. The high production efficiency and automation of these machines reduce labor costs and increase productivity, resulting in lower production costs per panel. Additionally, the customizable panel designs and materials allow manufacturers to optimize the cost and performance of the roof panels.
2. High-Quality Panels
Roof panel machines produce high-quality roof panels with consistent dimensions, shapes, and finishes. The advanced technology and control systems of these machines ensure precise production, resulting in panels with excellent durability, insulation, and aesthetic appeal.
3. Versatility and Customization
Roof panel machines can be customized to produce different panel designs and profiles, allowing manufacturers to meet the specific requirements of different construction projects. The versatility of these machines enables manufacturers to offer a wide range of roof panel options to their customers.
4. Time-Saving
The high production speed of roof panel machines saves time in the construction process. Manufacturers can produce large quantities of roof panels in a short period, reducing the overall construction time and enabling projects to be completed faster.
5. Environmental Benefits
Some roof panel machines produce panels made of sustainable materials or with energy-efficient features, providing environmental benefits. For example, insulated metal panels can reduce energy consumption by improving the thermal insulation of buildings, while composite panels made of recycled materials can help reduce waste.
VI. Considerations When Buying a Roof Panel Machine
1. Panel Requirements
Determine the specific requirements for the roof panels, such as panel type, size, shape, and material. Consider the intended application of the panels and the environmental conditions they will be exposed to. This will help you choose a roof panel machine that can produce the desired panels.
2. Production Capacity
Consider the production volume required for your project or business. Choose a roof panel machine with a production capacity that meets your needs. If you have a large-scale project or plan to produce panels on a regular basis, a high-capacity machine may be more suitable.
3. Quality and Durability
Look for a roof panel machine that is known for its quality and durability. Check the reputation of the manufacturer and read reviews from other customers. Consider the materials and components used in the machine and ensure they are of high quality to ensure long-term performance.
4. Customization Options
If you require custom panel designs or features, make sure the roof panel machine you choose offers customization options. Some machines can be programmed to produce specific panel profiles or can be equipped with additional features such as embossing or perforating.
5. Price and Cost of Ownership
Consider the price of the roof panel machine and the overall cost of ownership. Factor in the initial purchase price, installation costs, maintenance requirements, and energy consumption. Compare prices from different manufacturers and suppliers to ensure you get the best value for your money.
6. Technical Support and Service
Choose a manufacturer or supplier that offers good technical support and service. This includes installation assistance, training for operators, and ongoing maintenance and repair services. Ensure that the manufacturer has a responsive customer service team that can address any issues or concerns promptly.
VII. Maintenance and Operation of Roof Panel Machines
1. Regular Maintenance
Perform regular maintenance on the roof panel machine to ensure its optimal performance and longevity. This may include cleaning the machine, lubricating moving parts, checking for wear and tear, and replacing damaged components. Follow the manufacturer's maintenance guidelines and schedule to keep the machine in good condition.
2. Operator Training
Provide proper training to the operators of the roof panel machine. Ensure that they are familiar with the machine's operation, safety features, and maintenance requirements. Operators should be trained on how to adjust the machine settings, troubleshoot common issues, and perform basic maintenance tasks.
3. Safety Precautions
Follow all safety precautions when operating the roof panel machine. This may include wearing appropriate personal protective equipment, such as safety glasses, gloves, and ear protection. Ensure that the machine is properly guarded and that operators are trained on emergency stop procedures.
4. Quality Control
Implement a quality control system to ensure the production of high-quality roof panels. This may include regular inspections of the panels for dimensional accuracy, surface finish, and strength. Use quality control tools such as gauges and testing equipment to verify the quality of the panels.
VIII. Conclusion
Roof panel machines for sale offer a wide range of benefits for the construction industry. These machines provide efficient and cost-effective solutions for producing high-quality roof panels with customizable designs and materials. Whether you are a contractor, manufacturer, or builder, investing in a roof panel machine can help you improve productivity, reduce costs, and enhance the quality of your construction projects. When choosing a roof panel machine, consider your specific panel requirements, production capacity, quality and durability, customization options, price, and technical support. With proper maintenance and operation, a roof panel machine can provide years of reliable service and help you meet the growing demand for high-quality roof panels.