Hotline
+86-136 8495 9862
Email:cennia@szmizhi.com
Add::104,Building 27,Third Industrial Zone, Longxi Community,Longgang District,Shenzhen,China.
Coil Forming & Handling Equipment
Surface Treatment Equipment
Solutions
Application
About Us
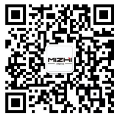
Welcome to MIZHI
For consultation/feedback, please call the service hotline: +86-136 8495 9862 Email:cennia@szmizhi.com
Introduction
A wheel blasting machine, also known as a shot peening machine in some cases, is a crucial piece of equipment in the field of surface treatment. It is widely used in various industries such as automotive, aerospace, construction, shipbuilding, and foundry to improve the surface quality and mechanical properties of metal components.
Working Principle
The working principle of a wheel blasting machine is based on the use of a high-speed rotating wheel to accelerate abrasive particles (such as steel shot, grit, or other suitable media) and project them onto the surface of the workpiece. The wheel, usually driven by an electric motor, rotates at a high speed within a specially designed housing. As the wheel spins, the abrasive particles are thrown outwards with great force due to centrifugal acceleration. When these accelerated particles strike the surface of the workpiece, they remove impurities, oxides, and other unwanted materials, while also inducing compressive stresses on the surface, which can enhance the fatigue strength and wear resistance of the component.
Types of Wheel Blasting Machines
Tumblast Wheel Machines
Tumblast wheel machines are designed for batch cleaning and are highly reliable and versatile. They are equipped with rubber work conveyors that provide a gentler tumbling action, making them suitable for handling fragile workpieces. These machines can operate continuously in an unmanned mode, offering the efficiency of batch cleaning. Typically, a tumblast wheel machine has a single wheel and is ideal for processing a wide range of parts with different shapes and sizes.
Table Machines
Table machines, including rotary table wheel machines with door-mounted swing tables or cabinet-mounted tables, are used to clean castings and large workpieces that may not be suitable for tumblast or spinner hanger systems. They are designed for rugged operation and are among the most versatile machines. Table machines usually have 1-2 wheels and allow for easy manual loading of small to medium-sized components.
Spinner Hanger Systems
Spinner hanger wheel machines are designed to blast clean workpieces on an overhead conveyor. The machine rotates the work hanger to achieve maximum exposure of the parts to the blast streams. There are various designs available, such as turnstiles, Y-tracks, and flow-through cabinets, to suit different requirements. These systems are commonly used to clean castings and large parts that cannot be tumbled easily and typically have 2-4 wheels.
Roller Conveyor Systems
Roller conveyor wheel blast systems are fully automated and are specifically developed to meet the needs of the fabrication industry. They are designed to descale and remove rust from plate and structural members prior to fabrication. These systems can effectively clean large workpieces, eliminating the environmental problems and high labor costs associated with manual air blasting. A typical roller conveyor system usually has 4 wheels and can handle heavy and bulky components with ease.
Monorail Blast Machines
Monorail blast machines are used with an overhead monorail conveyor and can be designed for higher throughput than spinner hanger systems. They are typically powered by a chain conveyor or self-powered drives, and the parts on hangers are automatically cleaned and transferred to the unload station. Monorail blast machines are suitable for processing components in a continuous flow, making them ideal for high-volume production lines.
Applications
Automotive Industry
In the automotive industry, wheel blasting machines are used to clean and prepare various components such as engine blocks, crankshafts, gears, and wheels. By removing surface impurities and creating a proper surface finish, these machines help improve the performance and durability of automotive parts. For example, shot peening of gears can increase their fatigue life, while cleaning and roughening the surface of engine blocks can enhance the adhesion of coatings and improve heat transfer properties.
Aerospace Industry
The aerospace sector demands the highest level of precision and quality in component manufacturing. Wheel blasting machines are used to treat critical aerospace parts such as turbine blades, landing gear components, and structural members. Shot peening is employed to induce compressive stresses on the surface of these components, which significantly improves their resistance to fatigue and stress corrosion cracking, ensuring the safety and reliability of aircraft structures.
Construction Industry
In construction, wheel blasting machines are used for surface preparation of steel structures, such as beams, columns, and plates. By removing rust, scale, and other contaminants, these machines provide a clean and roughened surface that is ideal for painting or coating applications, enhancing the adhesion and durability of protective coatings. Additionally, wheel blasting can also be used to clean and texture concrete surfaces, improving the bond strength of overlays or coatings.
Shipbuilding Industry
Shipbuilding involves the fabrication and assembly of large steel structures that are exposed to harsh marine environments. Wheel blasting machines are essential for removing mill scale, rust, and other surface impurities from ship plates and components before painting or welding. This surface preparation process helps prevent corrosion and improves the quality and longevity of the ship's hull and other structures.
Foundry Industry
In the foundry industry, wheel blasting machines are used to clean castings after they have been removed from the mold. The process removes sand, cores, and other residues from the casting surface, improving its appearance and dimensional accuracy. Shot peening can also be applied to castings to enhance their mechanical properties, such as tensile strength and fatigue resistance.
Advantages
High Efficiency
Wheel blasting machines can process workpieces at a relatively high speed, making them suitable for large-scale production. The continuous or batch operation modes, depending on the machine type, allow for efficient cleaning and treatment of multiple parts in a short period, increasing productivity and reducing production costs.
Superior Surface Finish
These machines can achieve a consistent and uniform surface finish, which is crucial for many applications. The precise control of abrasive particle size, velocity, and impact angle ensures that the workpiece surface is cleaned, roughened, or peened to the desired level, meeting strict quality standards and aesthetic requirements.
Environmental Friendliness
Modern wheel blasting machines are often equipped with advanced dust collection systems that capture and contain the abrasive particles and debris generated during the blasting process. This helps reduce air pollution and creates a cleaner working environment, complying with environmental regulations and improving workplace safety.
Versatility
With different types and configurations of wheel blasting machines available, they can handle a wide variety of workpieces, ranging from small and delicate components to large and heavy structures. Additionally, the adjustable blasting parameters allow for customization of the surface treatment process according to specific requirements, making wheel blasting machines suitable for diverse applications across multiple industries.
Considerations for Selection
Workpiece Characteristics
The size, shape, material, and surface condition of the workpiece are important factors to consider when selecting a wheel blasting machine. For example, small and intricate parts may require a table machine or a tumblast system with a gentle handling mechanism, while large and heavy plates or structures may necessitate a roller conveyor or monorail blast machine.
Production Volume
The required production volume determines the type and capacity of the wheel blasting machine needed. High-volume production lines may require fully automated continuous blast machines, while smaller workshops or job shops with lower production volumes may find batch-type machines more suitable and cost-effective.
Blasting Media
The choice of abrasive media depends on the workpiece material, the desired surface finish, and the specific application. Different types of media, such as steel shot, grit, or cut wire, offer varying levels of aggressiveness and cleaning or peening effects. It is essential to select the appropriate media and ensure its compatibility with the wheel blasting machine to achieve the best results.
Budget
The cost of wheel blasting machines can vary significantly depending on their type, size, automation level, and additional features. It is important to consider the initial investment, as well as the long-term operating costs, including maintenance, media consumption, and energy consumption, when determining the budget for purchasing a wheel blasting machine.
Conclusion
Wheel blasting machines play a vital role in modern manufacturing and surface treatment processes. Their ability to improve surface quality, enhance mechanical properties, and increase productivity makes them indispensable in various industries. By understanding the different types, working principles, applications, and considerations for selection of wheel blasting machines, manufacturers and surface treatment professionals can make informed decisions to choose the most suitable machine for their specific needs, ensuring high-quality production and efficient operation.