Hotline
+86-136 8495 9862
Email:cennia@szmizhi.com
Add::104,Building 27,Third Industrial Zone, Longxi Community,Longgang District,Shenzhen,China.
Coil Forming & Handling Equipment
Surface Treatment Equipment
Solutions
Application
About Us
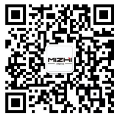
Welcome to MIZHI
For consultation/feedback, please call the service hotline: +86-136 8495 9862 Email:cennia@szmizhi.com
"The Future of Shot Blasting: Predictive Maintenance and IoT Integration"
"The Future of Shot Blasting: Predictive Maintenance and IoT Integration" highlights how modern shot blasting machines are leveraging advanced technologies to transform the industry. Here’s a detailed explanation based on recent industry trends and advancements:
Predictive Maintenance
Predictive maintenance is a game-changer for shot blasting operations. Traditional maintenance schedules often result in unnecessary repairs or, worse, unexpected failures that halt production. Modern shot blasting machines equipped with real-time sensors and AI-powered diagnostics can detect abnormal wear, energy spikes, and system inefficiencies before they escalate. This enables condition-based maintenance, reducing downtime and preventing costly emergency repairs.
Benefits of Predictive Maintenance
Reduced Downtime: Early warnings prevent unexpected failures.
Lower Maintenance Costs: Avoid unnecessary repairs and optimize servicing schedules.
Extended Equipment Life: Prevent excessive wear and premature component failure.
Stable Production: Maintain a consistent workflow without disruptions.
IoT Integration
IoT integration is another key driver of the future of shot blasting. By connecting machines to the internet, manufacturers can achieve remote monitoring, automatic parameter adjustments, and data-driven optimization. Smart shot blasting machines can communicate with other equipment and systems, enabling seamless integration into Industry 4.0 ecosystems. This connectivity allows for real-time scheduling, process optimization, and improved overall efficiency.
Key Technologies Driving Digital Transformation
IoT Sensors: Enable remote monitoring and real-time tracking.
Data Analytics: Predict failures, optimize production, and boost efficiency.
Automated Controls: Ensure precision with minimal human intervention.
Smart Connectivity: Integrates with ERP/MES systems for real-time scheduling.
Future Trends
As industries push for leaner, greener, and more adaptive manufacturing, shot blasting machines are evolving to meet these demands. Future systems will focus on:
AI-Driven Optimization: Using artificial intelligence to further enhance process efficiency and decision-making.
Sustainability Initiatives: Reducing energy consumption and eliminating hazardous waste.
3D Printing Integration: Enhancing surface quality and mechanical properties of 3D-printed components.
Miniaturized Systems: Enabling on-site cleaning and maintenance for remote or hard-to-access locations.
Conclusion
The future of shot blasting is bright, thanks to predictive maintenance and IoT integration. These technologies not only reduce downtime and maintenance costs but also enhance overall productivity and sustainability. By adopting these innovations, manufacturers can stay ahead in a rapidly evolving industrial landscape, achieving higher efficiency, greater precision, and long-term cost savings.