Hotline
+86-136 8495 9862
Email:cennia@szmizhi.com
Add::104,Building 27,Third Industrial Zone, Longxi Community,Longgang District,Shenzhen,China.
Coil Forming & Handling Equipment
Surface Treatment Equipment
Solutions
Application
About Us
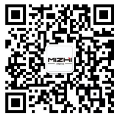
Welcome to MIZHI
For consultation/feedback, please call the service hotline: +86-136 8495 9862 Email:cennia@szmizhi.com
Introduction
A roof sheet making machine is a crucial piece of equipment in the construction and building materials industry. It is designed to produce various types of roof sheets with different shapes, sizes, and materials to meet the diverse requirements of roofing systems.
Types of Roof Sheet Making Machines
Roll Forming Machines: These are widely used for manufacturing metal roof sheets. They work by passing a continuous strip of metal through a series of rollers that gradually shape the material into the desired profile. Roll forming machines can produce a variety of profiles such as corrugated sheets, trapezoidal sheets, and standing seam sheets. They are known for their high production speed and accuracy, making them suitable for large-scale production.
Press Brake Machines: Press brake machines are used to bend and shape metal sheets into specific angles and curves. They are often used to create custom-shaped roof sheets or to form the edges and corners of larger panels. Press brakes offer precise control over the bending process, allowing for the production of complex shapes with tight tolerances.
Extrusion Machines: Extrusion machines are mainly used for producing plastic or composite roof sheets. The process involves forcing a molten material through a die to create a continuous profile with a uniform cross-section. Extruded roof sheets are lightweight, durable, and often have good insulation properties. They are commonly used in applications where corrosion resistance and low maintenance are required.
Casting Machines: In some cases, roof sheets may be made using casting processes, especially for concrete or other non-metallic materials. Casting machines pour the liquid material into a mold and allow it to solidify, resulting in a solid roof sheet. This method is suitable for creating large, custom-shaped panels with unique designs or for applications where high strength and durability are essential.
Components of a Roof Sheet Making Machine
Feeding System: The feeding system is responsible for supplying the raw material, such as metal coils or plastic granules, to the machine at a consistent rate. It typically includes components like decoilers, feed rollers, and conveyors to ensure a smooth and continuous flow of material into the processing area.
Forming or Shaping Unit: This is the core component of the machine where the actual shaping of the roof sheet takes place. In roll forming machines, it consists of a series of rollers mounted on shafts that gradually deform the metal strip into the desired profile. In press brake machines, it includes the hydraulic or mechanical press mechanism and the bending dies. For extrusion machines, the shaping unit is the extrusion die through which the molten material is forced.
Cutting Device: Once the roof sheet has been formed to the required length, a cutting device is used to separate it from the continuous material stream. Cutting can be achieved through various methods such as mechanical shears, laser cutting, or plasma cutting, depending on the material and the precision required.
Control System: The control system of a roof sheet making machine is responsible for regulating and monitoring all the machine's operations. It includes a control panel with programmable logic controllers (PLCs) or computer numerical control (CNC) systems that allow operators to set parameters such as sheet dimensions, forming speeds, and cutting lengths. The control system also ensures the synchronization of different components to achieve accurate and efficient production.
Tooling and Dies: Tooling and dies are essential components that determine the final shape and dimensions of the roof sheets. In roll forming, different sets of rollers are used to produce various profiles. For press brakes, custom-designed bending dies are required for each specific shape. The quality and precision of the tooling directly affect the quality of the finished roof sheets.
Materials Used in Roof Sheet Production
Metal Sheets: Galvanized steel, aluminum, and stainless steel are commonly used metals for roof sheets. Galvanized steel offers good strength, durability, and corrosion resistance at an affordable cost. Aluminum is lightweight, has excellent corrosion resistance, and is suitable for applications where weight is a concern, such as in roofing systems for large-span structures. Stainless steel provides high strength and superior corrosion resistance, making it ideal for harsh environments or applications where aesthetics are important.
Plastics and Composites: Polycarbonate, polyvinyl chloride (PVC), and fiberglass-reinforced plastics (FRP) are popular materials for plastic roof sheets. These materials offer advantages such as lightweight, transparency, and good chemical resistance. They are often used in applications where natural light transmission or resistance to chemicals is required, such as in industrial roofing or greenhouse construction.
Concrete and Cementitious Materials: Concrete roof sheets are used in some cases, especially for flat or low-slope roofs. They provide high strength, fire resistance, and good sound insulation properties. However, concrete roof sheets are relatively heavy and require proper structural support.
Applications of Roof Sheet Making Machines
Residential Roofing: Roof sheet making machines produce a wide range of roof sheets used in residential buildings, including traditional corrugated sheets, standing seam roofs, and tile-shaped sheets. These sheets not only provide protection from the elements but also contribute to the aesthetic appeal of the house.
Commercial and Industrial Roofing: In commercial and industrial buildings, large quantities of roof sheets are required to cover large roof areas. Roof sheet making machines can produce high-strength, durable sheets that can withstand heavy loads, harsh weather conditions, and chemical exposure. Standing seam metal roofs and trapezoidal sheets are commonly used in these applications due to their strength and ease of installation.
Agricultural Buildings: Roof sheets for agricultural buildings such as barns, sheds, and warehouses need to be durable, weather-resistant, and provide good ventilation. Machines can produce sheets with specific profiles and features to meet these requirements, such as corrugated sheets with vents or translucent plastic sheets for natural light transmission.
Specialty Applications: Roof sheet making machines can also be used to produce custom roof sheets for specialty applications such as stadiums, airports, and architectural landmarks. These projects often require unique shapes, sizes, and materials to achieve the desired design and functionality.
Advantages of Using Roof Sheet Making Machines
Increased Productivity: Roof sheet making machines enable high-speed production of roof sheets, significantly increasing productivity compared to manual or semi-automatic production methods. This allows manufacturers to meet large orders and tight deadlines more efficiently.
Precision and Consistency: The use of advanced forming and cutting technologies in these machines ensures high precision and consistency in the dimensions and quality of the roof sheets. This results in better fit and finish during installation, reducing the need for on-site adjustments and improving the overall quality of the roofing system.
Cost Savings: By automating the production process, roof sheet making machines reduce labor costs and material waste. The precise control over material usage and the ability to produce sheets with minimal scrap contribute to significant cost savings in the long run.
Customization: Many roof sheet making machines offer the flexibility to produce custom-shaped and sized roof sheets according to specific project requirements. This allows architects and builders to create unique roofing designs and meet the aesthetic and functional needs of different buildings.
Considerations for Choosing a Roof Sheet Making Machine
Production Capacity: The required production capacity should be determined based on the expected volume of roof sheets needed. Machines with higher production speeds and larger material handling capabilities are suitable for large-scale production, while smaller machines may be sufficient for lower volume requirements.
Sheet Profiles and Materials: The type of roof sheet profiles and materials to be produced should be considered. Different machines are optimized for specific profiles and materials, so it is important to choose a machine that can handle the desired range of products.
Quality and Precision: The quality and precision of the finished roof sheets are crucial for the performance and durability of the roofing system. Look for machines with advanced control systems, high-quality tooling, and a reputation for producing accurate and consistent results.
Ease of Operation and Maintenance: The machine should be easy to operate and maintain to minimize downtime and ensure smooth production. Consider factors such as user-friendly controls, accessibility for maintenance, and the availability of spare parts and technical support.
Cost and Return on Investment: The initial cost of the machine, as well as the long-term operating costs, should be evaluated. Compare different models and manufacturers to find a machine that offers a good balance between cost and performance, with a reasonable return on investment over time.
Conclusion
Roof sheet making machines play a vital role in the construction industry by enabling the efficient and precise production of roof sheets for various applications. With the continuous development of technology, these machines are becoming more advanced, offering increased productivity, customization, and quality control. By carefully considering the specific requirements of your roofing projects and choosing the right roof sheet making machine, you can ensure the production of high-quality roof sheets that meet the demands of modern construction while maximizing efficiency and cost savings.