Hotline
+86-136 8495 9862
Email:cennia@szmizhi.com
Add::104,Building 27,Third Industrial Zone, Longxi Community,Longgang District,Shenzhen,China.
Coil Forming & Handling Equipment
Surface Treatment Equipment
Solutions
Application
About Us
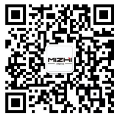
Welcome to MIZHI
For consultation/feedback, please call the service hotline: +86-136 8495 9862 Email:cennia@szmizhi.com
1.Name:Door Frame Profile Roll Forming Machine
2.Application: Making Door Frame Profile
3.It can custom-design
Introduction
A Door Frame Profile Roll Forming Machine is a specialized piece of equipment designed to produce door frames from metal coils. This machine is widely used in the manufacturing of steel and aluminum door frames for residential, commercial, and industrial applications. It offers high precision, efficiency, and versatility in producing various door frame profiles.
Key Components
1.Decoiler: Unwinds the metal coil and feeds the material into the machine.
2.Leveling Device: Ensures the metal strip is flat before entering the forming process.
3.Roll Forming Stands: A series of rollers that incrementally bend the metal strip into the desired door frame profile.
4.Punching System: Adds necessary holes or slots for hinges, locks, and other hardware.
5.Cutting Device: Cuts the formed profile to the specified length. Options include flying cutting, tracking cutting, or stop-to-cut systems.
6.Output System: Collects the finished profiles. Options include manual support or automatic stacking.
7.PLC Control System: Manages the entire production process, ensuring precision and automation.
Working Process
1.Material Feed: The metal coil is loaded onto the decoiler and fed into the machine.
2.Leveling: The metal strip is flattened to ensure uniformity.
3.Forming: The strip passes through a series of roll forming stands, where it is gradually shaped into the desired profile.
4.Punching: Holes or slots are punched into the profile as required.
5.Cutting: The formed profile is cut to the specified length using the cutting device.
6.Output: The finished door frames are collected on an output table or automatic stacker.
Features and Advantages
1.High Precision: Ensures uniform dimensions and tight tolerances, reducing the need for adjustments.
2.Durability: Consistent material thickness and superior surface finishes enhance the longevity of the frames.
3.Efficiency: Automated production reduces manual labor, material waste, and lead times.
4.Versatility: Can accommodate complex designs and varied material thicknesses, allowing for custom frame profiles.
5.Cost-Effectiveness: Minimizes material waste and labor costs, resulting in lower overall production costs.
Types of Door Frame Roll Forming Machines
1.Automatic Cut-to-Length Machines: These machines produce door frames of fixed lengths and offer a high degree of automation.
2.Variable Length Machines: These machines produce continuous lengths of door frames, offering more flexibility in production planning.
Applications
1.Residential Buildings: Produces door frames for homes.
2.Commercial Spaces: Manufactures door frames for offices and retail stores.
3.Industrial Structures: Creates robust door frames for warehouses and factories.
Technical Parameters
Parameter | Specification |
Material Thickness | 0.8 mm to 2.0 mm (cold-rolled steel, galvanized steel, aluminum) |
Material Width | As required by the profile |
Production Speed | Up to 30 m/min |
Cutting Accuracy | ±1.0 mm |
Main Motor Power | 7.5 kW to 18.5 kW |
Roller Material | GCr15 with heat treatment (HRC58-62°) |