Hotline
+86-136 8495 9862
Email:cennia@szmizhi.com
Add::104,Building 27,Third Industrial Zone, Longxi Community,Longgang District,Shenzhen,China.
Coil Forming & Handling Equipment
Surface Treatment Equipment
Solutions
Application
About Us
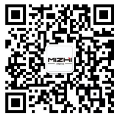
Welcome to MIZHI
For consultation/feedback, please call the service hotline: +86-136 8495 9862 Email:cennia@szmizhi.com
1.Model:MTR
2.Conveyor Way: Roller
3.Entrance Size :Custom-design
Roller conveyor shot blasting machines, specially designed for constant and continuous blasting of de-scaling, de-sanding, cleaning and pre-treatment for different type of steel, like steel plates, steel girder, shape steel, structural steel, steel pipe, steel castings etc. It is usually long and giant but compact, configurable with 4-16 sets of blast wheels and even more to meet different requirements of surface cleaning and strengthening.
The transport system is the rollers conveyor, driven steadily and stably by the chain and chain wheel and loaded with rollers of 80mm, 121mm, 180mm in diameter or even bigger, can load work pieces from 500KG to 2000KG and even heavier. Work pieces are loaded on the inlet of roller conveyor, being blasted in the blasting chamber, and come out from the outlet roller conveyor for unloading. continuous blasting process with one press of the button.
Load, roller transport, blast, unload. This is a through-type and continuous production line with high efficiency and an ideal option for surface cleaning of long and large steel materials, structural steel, steel welding part etc.
Applicable Work pieces
Transport system:Roller Conveyor
Surface condition before shot blasting: Rust, Scalings
Advised load weight per meter: 2000kgs
Number of Blast Wheels: 16 sets
Suitable Work pieces:Profiles, H beam, I Beam, C channels, Plate, Welded steel fabrications, Structural steel, transmission & television towers, Pipe and so on.
Automatic loading system can be customized
Can be equipped with painting line
Optimized design & economic solution
Ultimately compact design for easy operation and wide range of options of models to adapt to diversified production efficiencies and sizes of work pieces. Constant & continuous blasting process with high efficiency, saving abrasives with reliable performance of cleaning & dedusting and low costs.
Reliable quality & stable performance
Blasting machine body: 6-10mm thickness Manganese 13 steel plates well-welded in one piece and Manganese 13 steel protective boards, offering excellent wear resistance and protection from even the most aggressive blast media. Roller diameters, from 80mm to 180mm or even bigger and loading weight, from 500KG to 2000KG and even heavier, guarantee a long equipment life with a high uptime and low maintenance cost.
Stepless speed regulation is adopted for the roller conveying system to have stable and reliable operation and optimized blasting result on work piece.
High-end technologies applied
Optical grating detecting device is equipped in the front of the blasting chamber inlet to transmit time-lapse signal to the PLC as soon as work piece goes into the blasting chamber and gets ready for blasting process.
Compressed-air reverse-direction device, equipped in
the outlet roller segment, blows away the shots on the work piece and keeps work piece’s surface clean before it’s transported to the unloading roller segment.
Convenient control & maintenance
PLC control, all process parameters of work pieces blasting can be configured and saved in PLC control unit, in the result that repeat input, repeat pushing different buttons are completely unnecessary. This means, much shorter time of parameter configuration, much less working hours of operator and high efficiency.
Maintenance and examination windows are set on each core working parts of this machine for easy maintenance.
Special design of sealing
Blasting sealing: rubber segments are equipped at the roller conveyor inlet & outlet and the blasting chamber to make the machine sealing effect excellently and prevent accidents of shot spillage.
Care about environment
Great importance is attached by MIZHI to environment protection: noise and dust emission. We adopt high-end methods to reduce noise to 85DB and dust emission concentration to less than 50mg/m3 (these results can be even better with higher standard of configurations).
Blasting chamber system
a.6mm-10mm thickness Manganese 13 steel plates, accurately welded in one piece, and a line of 10mm Manganese 13 steel protective boards, installed at the area exposed to blasting shots stream, guarantee excellent wear resistance of the blasting chamber.
b.4-16 sets of blast wheels, equipped vertically and horizontally at both sides of the chamber, guarantees thorough cleaning of every work piece.
Multi-layer rubber sealing technique is used at the inlet chamber and outlet chamber to protect the side steel plates. Rubber segments sealing method make the machine sealing effect excellently and prevents accidents of shot spillage.
Roller conveyor system
a.Stepless speed regulation system is used for the whole transporting system for the work pieces to have stable and reliable operation and optimized blasting result on work piece.
b.The roller conveyor system is combined with three segments: inlet roller conveyor, blasting chamber roller conveyor and outlet roller conveyor.
High loading weight makes the roller conveyor system sustainable to heavy work piece and workload.
Screw conveyor system
a.2 or more screw conveyor systems, installed at the bottom of the blasting chamber and driven by the gear motor of the bucket elevator, consist of screw axle, blades and screw heads at both sides.
b.During working, the screw conveyor pushes the collected shots to the bottom of the bucket elevator and the shots are lifted by the buckets to the upper part of the elevator and pour into the shot separator.
1 screw conveyor system is installed at the top side of the bucket elevator to both push shots to the shots separator and separating partial dust and small broken shots through the rolling mesh sieve.
Bucket elevator system
a.The elevator system is built with steel plates by accurate soldering technique and driven by 1 gear motor at the top.
b.It includes, 2pcs high-quality wheel hubs, 1 elevator body, 1 high-performance and durable belt and several alloy buckets, providing the maximum transporting amount 130Ton/H. It collects and lifts those shots that are recycled by the screw conveyor, onto the separator and storage cabinet.
c.A window is designed on the elevator for easy maintenance and examination.
Separator system
a. Air-flow separator is used to separate good shots and broken shots and dust. It is built andsoldered with steel plates and different chambers are designed inside to lead the air flow.
b.Mixture of shots & dust is transported from the screw conveyor (if equipped) and goes downward on a sliding steel board and get into the way of the air flow. Good shots are heavy and not driven to move by the air flow but broken shots are much lighter to be lead to the other slide board to be connected with collector/bucket. Dust directly sucked and taken to the air outlet to the dust collector.
Multi-level steel plates are installed to adjust and balance the sliding shots flow amount. Good shots are collected by the shots storage cabinet for recycling usage.
Semi-automatic flow valve
a.Semi-automatic flow valves, fully sealed with lockable examination window, are equipped to control the flow amount of shots into the blast wheels.
On the top of each flow valve, in case steel shots flow from the storage silo, a manual stop valve can be switched off under the circumstance of examination, repairing and maintenance.
Blast wheel system
a.Thanks to German technology, MIZHI casting and fully CNC machined blast wheels are designed and manufactured with highly hard-wearing materials and steel plates for easy replacement and maintenance.
b.Designed and manufactured in combination of our own industrial advantages and features to have excellent performance of dynamic balance and perfect shots output efficiency.
c.Highly hard-wearing materials and steel plates are installed inside for easy replacement and maintenance, working with variable-frequency speed control technology to control and adjust the power of the blasting.
d.MIZHI P series power system (available), specially-designed and manufactured ABB motor, die steel CNC machined + low-pressure & vacuum heat treatment vulnerable parts inside. These special vulnerable parts have 58-62HRC surface hardness that is extremely durable and has super long lifespan.
Abrasive Romoval Unit ( For Steel Plate )
a. After the blasting process, the workpiece may still be covered in blast media, which must be cleaned off. This task is carried out by a rotating brush, which is fitted with securely attached brush segments, which are interchangeable.
b. To avoid blast media building up on long parts, the rotation brushes flick the spent abrasive from the work surface into a specially designed trough which has a screw conveyor taking the media back into circulation. To keep the position between the brushes and the screw conveyor constant when blasting different sized work pieces, both are built with the same adjustable framework. manual bursh height adjustment by press button. Finally remaining media on the surface of work pieces will be removed by the blow off station, which is mounted on the same framework and uses high pressure ventilators to blow off any media remaining.
Dedusting System: cartridge filter with secondary filter system
a.A typical dedusting system for shot blasting machine: cyclone separator and the cartridge filter. the cyclone separator separates and collects most of heavy dust and the cartridge filter blocks and filters the escaped air & dust mixture.
b.Electromagnetic pulse technology is applied in the cartridge filter to shock and separate the dust from the filter. Dust goes down to the collect storage cabinet due to its gravity.
c.The built-in filter needs regular cleaning and replacement to prevent the spillage of dust from inside because of the blocked and malfunctioned filter.
d.This dedusting system works with silencer and secondary filter to ensure that noise emission is lower than 85DB and dust emission is lower than 50mg/m³
Wet dust collector is available. High performance dedusting system, with Venturi theory, is a great dust separator especially for flammable and explosive media. Wet dust is automatically recycled and the electromagnetic water valve automatically open to provide new water when the water level in the water box is low.
Machine Model | MTR-1040Q11-4 | MTR-1240Q11-4 | MTR-1650Q15-4 | MTR-1650Q15-6 | MTR-2050Q15-6 | MTR-2560Q15-6 | MTR-3060Q15-8 | MTR-4080Q15-8 |
Max working width for plates (mm) | 1000 | 1250 | 1600 | 1600 | 2000 | 2500 | 3000 | 4000 |
Max working width for profiles (mm) | 700 | 800 | 1200 | 1200 | 1200 | 1800 | 2000 | 2000 |
Max working height for profiles (mm) | 400 | 400 | 500 | 500 | 500 | 600 | 600 | 800 |
Pass speed (m/min) | 0.4-2.0 | 0.4-2.0 | 0.5-2.5 | 0.5-2.5 | 0.5-2.5 | 0.5-2.5 | 0.6-3.0 | 0.6-3.0 |
Max load per m on roller conveyor (kg/m) | 500 | 600 | 1000 | 1000 | 1000 | 1500 | 2000 | 2000 |
Blast wheel power (kW) | 11 | 11 | 15 | 11-(15) | 11-(15) | 15-(22) | 15-(22) | 15-(30) |
Number of blast wheels | 4 | 4 | 4 | 6 | 6 | 6 | 8 | 8 |
Diameter of blast wheels (mm) | 380 | 380 | 380 | 380 | 380 | 380 | 380 | 380 |
Can be customized accroding to customer's requirements |