Hotline
+86-136 8495 9862
Email:cennia@szmizhi.com
Add::104,Building 27,Third Industrial Zone, Longxi Community,Longgang District,Shenzhen,China.
Coil Forming & Handling Equipment
Surface Treatment Equipment
Solutions
Application
About Us
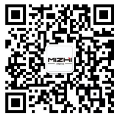
Welcome to MIZHI
For consultation/feedback, please call the service hotline: +86-136 8495 9862 Email:cennia@szmizhi.com
1.Name:Sandwich Panel Rolling Forming Machine
2.Application: Making Sandwich Board
3.It Can Custom-Design
A Sandwich Panel Rolling Forming Machine is a specialized piece of equipment used to produce sandwich panels, which are composite materials consisting of a core material (such as polyurethane foam, mineral wool, or EPS) sandwiched between two metal sheets (typically steel or aluminum). These machines are designed for continuous production, offering high efficiency and flexibility in manufacturing sandwich panels for various applications, including construction, cold storage, and industrial buildings.
Key Components and Workflow
1. Uncoiling System: Metal coils (usually steel or aluminum) are fed into the machine through an uncoiling unit, which ensures smooth and controlled uncoiling of the material.
2. Roll Forming Section: The metal sheets are progressively shaped into the desired profiles through a series of rolling stands. Each stand performs a specific bending operation to form the sheet into the required shape.
3. Core Material Injection: For polyurethane sandwich panels, liquid polyurethane foam is mixed, reacted, and injected between the formed metal sheets. The foam expands and cures, bonding the metal sheets together.
4. Curing and Cooling: The sandwich panel passes through a curing oven where the foam expands and bonds with the metal sheets. The panel is then cooled to ensure proper curing.
5. Cutting and Stacking: The finished sandwich panels are cut to the desired length by an automatic cutting machine and stacked for further processing or packaging.
Technical Specifications
1. Production Speed: Typically ranges from 20 to 40 meters per minute.
2. Effective Width: Can handle widths from 1000mm to 1500mm or more.
3. Thickness: The thickness of the sandwich panel can vary from 50mm to 300mm.
4. Power Consumption: Depending on the model, power requirements can range from 15 to 100 kW.
5. Control System: Modern machines often feature advanced control systems, including PLCs and touchscreens, for precise control over the production process.
Types of Machines
1. PU Sandwich Panel Roll Forming Line: A complete automated line for forming and filling polyurethane foam between metal sheets.
2. Double Layer Roll Forming Machine: Forms the two metal facer sheets separately before bonding.
3. Laminating Machine: Used for bonding the metal sheets after the core material has been injected.
Advantages
1. High Output and Consistency: Automated production ensures high output rates and consistent product quality.
2. Customization: Machines can be customized to produce panels of various sizes and profiles, meeting specific application requirements.
3. Energy Efficiency: Some machines feature energy-saving designs, such as semi-dry roll forming and optimized heating systems.
Applications
Sandwich panels produced by these machines are widely used in:
1. Construction: For roofing, walls, and insulation in buildings.
2. Cold Storage: Due to their excellent thermal insulation properties.
3. Industrial Buildings: For their durability and resistance to wear and tear.