Hotline
+86-136 8495 9862
Email:cennia@szmizhi.com
Add::104,Building 27,Third Industrial Zone, Longxi Community,Longgang District,Shenzhen,China.
Coil Forming & Handling Equipment
Surface Treatment Equipment
Solutions
Application
About Us
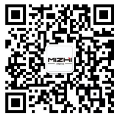
Welcome to MIZHI
For consultation/feedback, please call the service hotline: +86-136 8495 9862 Email:cennia@szmizhi.com
1.Name:Tube Roll Forming Machine Equipment Production Line
2.Application: Tube
3.It can custom-design
A Tube Roll Forming Machine Equipment Production Line is a highly automated system designed to produce steel tubes and other hollow profiles through a continuous roll forming process.
A Tube Roll Forming Machine Equipment Production Line is a highly automated system designed to produce steel tubes and other hollow profiles through a continuous roll forming process.
Below is a detailed description of its components, production process, and key features based on the latest information available:
Main Components of the Production Line
1.Uncoiling Unit:
This unit holds and feeds the steel coil into the production line. It is essential for maintaining a steady supply of material。
2.Leveling Unit:
The leveling unit flattens the steel strip to remove any deformities or waviness. This ensures that the material enters the roll forming section in a uniform condition。
3.Roll Forming Stations:
These stations are equipped with precision rollers that gradually bend the steel strip into the desired tube shape. The rollers are designed and machined to achieve high precision and dimensional accuracy。
4.Punching and Cutting Units:
These units perform any required punching or cutting operations on the formed profile. They can be integrated into the production line to achieve specific lengths or add holes as needed。
5.Hydraulic Cutting Machine:
This machine is responsible for cutting the formed tube to the desired length. It is typically equipped with high-precision cutting tools to ensure clean and accurate cuts。
6.Run Out Table:
The run out table supports the finished tubes as they exit the production line. It helps in the smooth transfer of the product for further processing or packaging。
7.Control System:
The production line is controlled by an advanced computer system, often using PLC (Programmable Logic Controller) and HMI (Human-Machine Interface) technology. This allows for precise control over the entire production process, including speed, length, and other parameters。
Production Process
The production process of a tube roll forming machine involves the following steps:
1.Uncoiling: The steel coil is loaded into the uncoiling unit.
2.Leveling: The steel strip is flattened by the leveling unit.
3.Roll Forming: The strip passes through multiple roll forming stations where it is gradually bent into the desired tube shape。
4.Punching and Cutting: Any required punching or cutting operations are performed on the formed tube。
5.Cutting to Length: The finished tube is cut to the desired length by the hydraulic cutting machine。
6.Discharge: The cut tubes are transferred to the run out table for further processing or packaging。
Technical Specifications
1.Material Thickness: Typically ranges from 1.2mm to 22.0mm。
2.Production Speed: Up to 60 meters per minute。
3.Forming Length: Standard lengths range from 4 to 12 meters。
4.Power Requirements: Depending on the size and configuration of the production line, the installed electric capacity can range from 400 kW to 2500 kW。
Key Features and Advantages
1.High Production Efficiency: The automated process allows for high production speeds, typically ranging from 0 to 60 meters per minute。
2.Precision and Consistency: The roll forming process ensures high dimensional accuracy and uniformity in the finished products。
3.Versatility: The production line can be configured to produce a wide range of tube sizes and shapes, making it suitable for various applications。
4.Low Material Waste: The continuous roll forming process minimizes material waste compared to other manufacturing methods。
5.Customization: The production line can be customized to meet specific requirements, including material thickness, tube diameter, and length。
Applications
The tubes produced by this production line are widely used in various industries, including:
1.Construction (e.g., scaffolding, structural supports)
2.Automotive (e.g., exhaust systems, frame components)
3.Furniture (e.g., chair legs, table frames)
4.Mechanical and industrial applications (e.g., pipe systems, machine parts)