Hotline
+86-136 8495 9862
Email:cennia@szmizhi.com
Add::104,Building 27,Third Industrial Zone, Longxi Community,Longgang District,Shenzhen,China.
Coil Forming & Handling Equipment
Surface Treatment Equipment
Solutions
Application
About Us
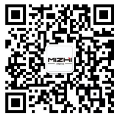
Welcome to MIZHI
For consultation/feedback, please call the service hotline: +86-136 8495 9862 Email:cennia@szmizhi.com
1.Name:Roll Forming Machine
2.Application: All Kinds of Cold Forming Products
3.It Can Custom-Design
Comprehensive Overview
A Roll Forming Machine is a versatile piece of industrial equipment used to produce metal profiles by continuously bending a metal strip through a series of rollers. This process, known as roll forming, is highly efficient and precise, making it ideal for manufacturing a wide range of products, from construction materials to automotive components.
Key Components
1.Decoiler and Feeding System:
Decoiler: Unwinds the metal coil and feeds it into the machine. It can handle various coil sizes and materials.
Feeding System: Ensures the metal strip is fed smoothly and accurately into the roll forming section. It often includes a leveling unit to straighten the metal strip.
2.Roll Forming Section:
Roller Stations: The core of the machine, where the metal strip is gradually shaped into the desired profile through a series of rollers. Each set of rollers bends the metal slightly, building up the final shape incrementally.
Number of Stations: Typically ranges from 10 to 20, depending on the complexity of the profile.
3.Punching and Cutting Device:
Punching Device: Punches holes or shapes into the metal strip as it passes through the machine. This is crucial for creating attachment points or specific features in the final product.
Cutting Device: Cuts the formed profile to the specified length. This can be hydraulic, pneumatic, or servo-driven, depending on the machine's design.
4.Control System:
Modern roll forming machines are equipped with advanced control systems, often using PLC (Programmable Logic Controller) and HMI (Human-Machine Interface) touchscreens. These systems allow for precise control over the forming process, including speed, feed rate, and roller adjustments.
Applications
Roll forming machines are used across various industries to produce a wide range of products, including:
Construction: Formwork profiles, purlins, studs, and other structural components.
Automotive: Body panels, frames, and structural components.
Agriculture: Fencing, animal housing, and other metal structures.
Electrical: Cable trays, conduit, and other electrical components.
HVAC: Ductwork, ventilation components, and other HVAC parts.
Technical Specifications
1.Material Compatibility: Suitable for a wide range of materials, including cold-rolled steel, galvanized steel, stainless steel, and aluminum.
2.Material Thickness: Typically ranges from 0.5mm to 6mm, depending on the application.
3.Forming Speed: Varies from 5 to 30 meters per minute, depending on the machine's design and the complexity of the profile.
4.Power Requirements: Main motor power ranges from 5kW to 30kW, depending on the size and speed of the machine.
5.Machine Weight: Typically between 5 to 20 tons, depending on the model and configuration.
6.Dimensions: Vary based on the model, but common dimensions include 6m to 12m in length, 1m to 2m in width, and 1.5m to 3m in height.
Advantages
1.High Precision: CNC machining of rollers ensures precise shaping and consistent quality.
2.Customization: Machines can be configured to produce a wide range of profiles and sizes.
3.Efficiency: Continuous production and high-speed operation increase productivity.
4.Versatility: Suitable for various materials and applications.
5.Durability: High-quality materials and components ensure long-term reliability.
Industry Standards
Roll forming machines must comply with various industry standards to ensure safety, quality, and environmental sustainability:
1.ISO 9001: Quality management system.
2.CE Certification: Required for machines sold in the European Union.
3.ASTM Standards: Such as ASTM A653 for steel sheet specifications.
4.EN Standards: European standards for specific applications, such as EN 10346 for cold-formed steel.
Conclusion
The Roll Forming Machine is a highly efficient and versatile solution for producing metal profiles. Its precision, customization capabilities, and durability make it a valuable asset in various industries. By adhering to industry standards and regulatory requirements, these machines ensure the production of safe, reliable, and high-quality components.