Hotline
+86-136 8495 9862
Email:cennia@szmizhi.com
Add::104,Building 27,Third Industrial Zone, Longxi Community,Longgang District,Shenzhen,China.
Coil Forming & Handling Equipment
Surface Treatment Equipment
Solutions
Application
About Us
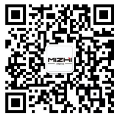
Welcome to MIZHI
For consultation/feedback, please call the service hotline: +86-136 8495 9862 Email:cennia@szmizhi.com
Sandblasting Room is ideal for the large-scale structures, widely used in blasting of hulls, stoves,boilers and wind power parts, etc.Large structures can move inside the Blast Room on work cars sliding on rails. Mainly composed with the main body of Blasting Room, Workpiece Transportation System,Sandblasting System, Abrasive recovery system, ,Dust Collecting System, Central Control System and lighting system.
Sandblasting room has its other names as shot blasting room & sand hitting room. It is usually suitable for huge work piece in surface cleaning, de-rusting and enhancing the adhesive of painting layer. Sand blasting room has two types of shots recycling: automatic recycling system & semi-automatic recycling system. Operator does the blasting work in the blasting room, with protection suit and helmet to protect himself and fresh air from the ventilation device through the helmet.
Sand blasting room consists of light steel structure blasting room with protective rubber inside, sand blasting system, mechanical or manual shots recycling system, dedusting system and lighting system, and it is mainly designed for huge castings and steel structural work pieces’ surface cleaning.
Sand blasting room main compositions
Sand blasting chamber
Abrasive Storage Hopper
Sandblaster
Bucket elevator
Screw conveyor
Elevator
Separator
Abrasive recycling system
Lighting system
Dust Collector
Steel grating
Trolley system
Electric control system
High-efficiency sand recycling system
Automatic recycling system is recommended for high-efficiency abrasives usage and short time of shots recovery. Shots are gathered to the screw conveyor below the blasting room and pushed to the elevator automatically for recycle usage to save cost and time of shots transporting.
Compatible semi-automatic recycling system
When digging a deep pit below the blasting room is not allowed, the semi-automatic recycling system is recommended for the compatibility of recycling shots. Shots are collected manually and transported to the bottom of the elevator for recycling or a short screw conveyor can be equipped before the elevator and shots are manually loaded into the screw conveyor for transporting to the elevator for recycling.
High quality & durability
The blasting room is built with color-coated steel sandwich boards in a steady and sturdy light-steel structure. Hard-wearing rubber protective boards are attached onto the inside wall of the room in the purpose of protecting the room walls from being damaged by the sand blasting.
Customizable room configurations
Both blasting gun number and room size are customizable according to specific work piece parameters and production capacity.
More option of high automation
Mechanical arm is available to be equipped into the blasting system to realize automatic sand blasting and greatly reduce time of manual operation.
Easy to operate and maintain
Windows are set on the sandblasting chamber for convenient maintenance and examination.
Environmental Protection
we have adopted advanced methods to reduce noise to 85DB and dust emission concentration to less than 50mg/m3 (stricter requirements needs higher standard configuration)
Sandblasting room
a.The blasting room is built with color-coated steel sandwich boards in a steady and sturdy light-steel structure. Hard-wearing rubber protective boards are attached onto the inside wall of the room in the purpose of protecting the room walls from being damaged by the sand blasting.
b.SandBlast Room are designed and fabricated according to the size requested by the customer.
c.They may have one or two main doors for material access. The structure of the room may consist either of steel walls or color sandwich panels with polyurethane insulation.
d.The internal walls are lined with wear-proof rubber. The floor is made of steel grating which cover the automatic recovery system for abrasives. The material handling can be done by trolleys or by overhead crane.
Portable Pressure Pot Sandblaster
a.Portable Pressure Pot Sandblaster is powered with compressed air, the abrasive media is accelerated to 50-60m / s impact to the workpieces’ surface, it is a non-contact, less non-polluting method of surface treatment.
b.Portable Pressure Pot Sandblaster
c.The system is installed with 1-2 pcs peach-style pressure tank and designed to increase steel grit fluidity.
d.The upper part is connected with a pneumatic butterfly-style valve and a storage bin. The pneumatic valve is closed during the blasting operation and opened to input shots at the end of the blasting.
e.The pipeline is equipped with a manual air on-off valve, oil-water separator, pressure regulator, pneumatic diaphragm valve, gas storage tank, riot device, exhaust muffler and sand valve etc.
f.2 or more tungsten carbide blasting guns, with a 10-meter-long sandblasting hose connected to each gun.
Abrasive Recovery System
The abrasive recovery system for blasting room consist of floor recovery, bucket elevator and separator.
1.Floor recovery system
Sandblast room recovery system use floor recovery system to reclaim the used blasting media and contaminants into the bucket elevator and then into the dust collector system, and then the cleaned abrasive get into the storage hopper to recycle, the residual will get our of the recycle system from the separator.
2.Bucket elevator system
a.The dismountable elevator is driven by 1 gear motor at the top of the elevator and built with steel plates by accurate soldering technique and It includes 2pcs high-quality wheel hubs, 1 elevator body, 1 high-performance and durable belt and several alloy buckets.
b.The maximum transfer amount of the elevator is 120Ton/H. It collects and lifts the shots recycled by the screw conveyor onto the separator and storage cabinet.
c.A window is designed on the elevator for easy maintenance and examination.
3.Separator system
a.The air-flow separator is used to separate good shots and broken shots and dust. It is built and soldered with steel plates and different chambers inside to lead the air flow and multi-level steel plates to adjust and balance the sliding shots flow amount.
b.Shots & dust mixture is transported from the screw conveyor and go downward on a sliding steel board and get into the way of the air flow. Good shots are heavy and not driven to move by the air flow but broken shots are much lighter to be lead to the other slide board that connected with a broken shot collector/bucket. Dust directly flows in the air flow direction and is taken to the air outlet to be dealt with by the dust collector.
Sweep/Shovel Chute Type
Sweep/ shovel chute type is the most economical abrasive reclaim system, which is only appropriate for low production operations.This is the simplest reclaim system, but need to collect the abrasive and push the abrasive into the recycle system manually after blasting work.This blasting room recovery system just need a small pit for elevator, no need other foundation pit, no damage to the ground.
Single Screw or Scraper Partial Reclaim System
The most economical floor design is available. The system contains one or more screw conveyor or craper conveyor, heavy-duty screw belt and bucket elevator, air-wash separator, and oversized abrasive storage hopper with a caged man ladder and handrail. This can be expanded to an "H", "U", or full floor reclaim system, which is best suited for low to medium production levels.
"L"- Shaped Partial Reclaim System
One longitudinal conveyor installed at the one sidewall of the blast room is allowing the abrasive delivered from the spray guns, which is either blown or rebounded off the workpiece, to strike the side walls and fall into the conveyors, automatically reclaiming approximately 40-70 percent of the blast media. The reclaiming abrasive on the blast booth floor is pushed into the screw or scraper conveyors assemblies at the end of the work shift. The "L" shaped floor design is typically used in a “flow-through” room configuration where heavy workpieces and/or material handling devices can drive into the room. This is best suited for low to medium production.
"H" - Shaped Partial Reclaim System
Two sets of longitudinal conveyors installed at each sidewall of the sandblast room allowing the abrasive delivered from the spray guns, which is either blown or rebounded off the workpiece, to strike the side walls and fall into the conveyors, automatically reclaiming approximately 60-90 percent of the blast media. The reclaiming abrasive on the floor is pushed into the screw or scraper conveyors assemblies at the end of the work shift. The “H” shaped floor design is typically used in a “flow-through” room configuration where heavy workpieces and/or material handling devices can drive into the room. This is best suited for medium to high production.
"U"- Shape Partial Reclaim System
Two longitudinal screw or scraper conveyors assemblies along each wall of the blast room and positions the cross screw or scraper conveyors along the back wall of the blast room. This allows the abrasive delivered from spray guns, which is either blown or rebounded off the workpiece, to strike the sidewalls and back wall of the blast room and fall into the reclaim system, A “U”- shaped floor design will automatically reclaim 60-90 percent of the blast media. The remaining abrasive on the floor is pushed into the metered shed plate screw assemblies at the end of the work shift, The “U”-shaped floor design is typically used in an “in-out” room configuration where heavy workpieces and/or material handling devices can drive into the room. This is best suited for medium to high production.
Full Floor Partial Reclaim System
The full-floor reclaim system utilizes multiple screw assemblies or scraper assemblies to create a fully automatic, high volume abrasive reclaim system where 100% of the abrasive blast media is returned to the separator system during the blasting operation. This allows for a faster reclaim as well as full recycling of the abrasive media, saving your blasting operation both time and cost.
The Full Floor Reclaim System allows for the maximum efficiency of your abrasive blast system. This abrasive blast reclaim system is well suited for pass-thru and/or high production requirements.
Dust Collector System
1.It includes cyclone separator and the cartridge filter. the cyclone separator separates most of heavy dust and the cartridge filter blocks and filters the escaped air & dust mixture.
2.Electromagnetic pulse technology is applied in the cartridge filter to shock and separate the dust from the filter. Dust goes down to the collect storage cabinet due to its gravity. Silencer and secondary filter ensure that noise emission is lower than 85DB and dust emission is lower than 50mg/m³
3.Wet dust collector, a high performance dedusting system with Venturi theory, especially for flammable and explosive media, automatically recycle dust.
Sandblasting Room | |||||||
Machine Name | Semi-Auto Sandblasting Room | Automatic Sandblasting Room | |||||
Model | MSH804030-300L1-1 | MSH805040-300L1-2 | MSA905750-300L1-2 | MSA805060-300L1-2 | MSA704540-300L1-2 | MSA120505-900L2-4 | MSA120605-900L1-2 |
Max. length of Blast Room (mm) | 8000 | 8000 | 9000 | 8000 | 7000 | 12000 | 12000 |
Max. length of Width Room (mm) | 4000 | 5000 | 5700 | 5000 | 4500 | 5000 | 6000 |
Max. length of Height Room (mm) | 3000 | 4000 | 5000 | 6000 | 4000 | 5000 | 5000 |
Max. Volume of Pressure Tank(L) | 300 | 300 | 300 | 300 | 300 | 2*900L | 900L |
Number of gun (Piece) | 1 | 2 | 2 | 2 | 2 | 4 | 2 |
Working pressure (Mpa) | 0.6~0.8 | ||||||
Air consumption(m3/min) | 6-10m3/min | 12-15m3/min | 24-28m³/min | 12-15m3/min | |||
Pressure adjustment range (Bar) | 4-7bar | ||||||
Abrasive Recovery Mothod | Manual abrasive Collecting + Automatic abrasive lifting | Automatic Screw conveyor recovery | |||||
Work Pieces Loading Type | Manual /Trolley | ||||||
Dust Colloctor | DC-12 | DC-36 | DC-48 | ||||
Equipment Dimension(L*W*H mm) | 8500*5750*4390 | 8800*7877*5576 | 9800*8453*9234 | 8000*5000*6000 | 7670*4910*4130 | 14797*12531*8120 | 11000*6000*5000 |
Total Power(Exclude dust collector) | 20KW | 3.44KW | 7.24KW | 7.27KW | 7.8KW | 9.6KW | 9.6KW |
Total Weight(Exclude dust collector) | 8T | 10T | 16T | 18.5T | 18.3T+ | 31.5T | 28.2T |