Hotline
+86-136 8495 9862
Email:cennia@szmizhi.com
Add::104,Building 27,Third Industrial Zone, Longxi Community,Longgang District,Shenzhen,China.
Coil Forming & Handling Equipment
Surface Treatment Equipment
Solutions
Application
About Us
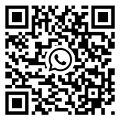
Welcome to MIZHI
For consultation/feedback, please call the service hotline: +86-136 8495 9862 Email:cennia@szmizhi.com
1. Introduction
In modern manufacturing, the diversity of workpiece sizes and shapes poses a significant challenge in surface treatment processes. A one - size - fits - all approach is no longer sufficient, especially when it comes to shot blasting, a crucial method for cleaning, strengthening, and preparing the surfaces of various components. The adjustable hanger hook shot blasting machine has been developed as a revolutionary solution to this problem. This specialized equipment allows manufacturers to efficiently treat workpieces of different sizes, from small - scale components to large - sized structures, by providing a flexible and adaptable hanger hook system.
2. Working Principle
2.1 Adjustable Hanger Hook System
The core of the adjustable hanger hook shot blasting machine is its innovative hanger hook system. This system is designed with a high degree of flexibility to accommodate workpieces of various dimensions. The hanger hooks are typically attached to a rail or a conveyor mechanism, which can be adjusted both horizontally and vertically.
Horizontally, the hooks can be spaced apart or brought closer together to fit the width of the workpiece. This is achieved through a motor - driven or manually - operated adjustment mechanism. For example, in a manufacturing facility that processes both small metal brackets and large - sized automotive body panels, the horizontal adjustment of the hanger hooks allows for easy and secure suspension of these different - sized workpieces.
Vertically, the hanger hooks can be raised or lowered. This is particularly useful for workpieces with varying heights. A sophisticated lifting mechanism, often controlled by a programmable logic controller (PLC) or a manual winch system, enables precise vertical positioning of the hooks. This ensures that the workpiece is placed at the optimal height within the shot blasting chamber for effective surface treatment.
2.2 Shot Blasting Unit
The shot blasting unit of the machine is responsible for delivering the abrasive media onto the surface of the suspended workpiece. It typically consists of one or more centrifugal wheels or high - pressure nozzles.
Centrifugal wheels are a common component in the shot blasting process. These wheels are equipped with vanes that accelerate abrasive media, such as metal or ceramic shots, to high velocities. The shots are fed into the center of the wheel and are then flung outwards at speeds that can reach up to 100 meters per second or more. Multiple centrifugal wheels are strategically positioned around the area where the workpiece is suspended. The orientation and angle of these wheels can be adjusted to ensure comprehensive coverage of the workpiece's surface, regardless of its size or shape.
High - pressure nozzles may also be used, either in combination with centrifugal wheels or as a standalone option. These nozzles can deliver a highly focused stream of abrasive media at pressures ranging from several bar to hundreds of bar. They are particularly effective for treating workpieces with complex geometries or for targeting specific areas that require more intensive surface treatment.
2.3 Abrasive Media Recycling and Separation
Efficient use of abrasive media is essential for cost - effective shot blasting operations. The adjustable hanger hook shot blasting machine is equipped with an advanced abrasive media recycling and separation system.
After the abrasive media impacts the surface of the workpiece and falls to the bottom of the shot blasting chamber, it is collected through a series of chutes and conveyor belts. The used media is then passed through a separation process. This process typically involves a combination of mechanical sieving to remove large debris and magnetic separation (if the abrasive media is ferromagnetic) to extract any metal particles that may have been worn off the workpiece or the machine components during the blasting process.
The clean and reusable abrasive media is then recycled back into the shot blasting unit, ready for the next cycle of treatment. This closed - loop system not only reduces the cost of constantly purchasing new abrasive media but also minimizes environmental waste, making it an environmentally friendly and sustainable solution.
3. Advantages of the Adjustable Hanger Hook Shot Blasting Machine
3.1 Versatility in Workpiece Sizes
1. Accommodation of Diverse Workpieces: The ability to adjust the hanger hooks both horizontally and vertically allows the machine to handle an extremely wide range of workpiece sizes. Whether it's a tiny electronic component that measures only a few centimeters in size or a massive industrial machinery part that spans several meters, the machine can be easily configured to suspend and treat the workpiece. This versatility is a significant advantage for manufacturers that produce a diverse range of products or for job - shops that need to handle different customer orders with varying workpiece dimensions.
2. Reduced Need for Multiple Machines: In the past, manufacturers often had to invest in multiple shot blasting machines, each designed to handle a specific range of workpiece sizes. With the adjustable hanger hook shot blasting machine, a single piece of equipment can replace several specialized machines. This not only saves on the initial capital investment but also reduces the space required for equipment installation and storage, making it a more cost - effective and space - efficient solution.
3.2 Optimal Surface Treatment for All Workpieces
1. Uniform Coverage: The strategic positioning of the shot - blasting units around the suspended workpiece, combined with the ability to adjust the position of the workpiece within the chamber, ensures uniform coverage of the entire surface area. Regardless of the size or shape of the workpiece, all parts are exposed to the abrasive media in a consistent manner. This results in a uniform surface finish, which is crucial for applications such as painting, coating, or where consistent surface properties are required.
2. Customizable Treatment Intensity: The machine offers a high degree of control over the treatment intensity. Operators can adjust parameters such as the speed of the centrifugal wheels (which determines the velocity of the abrasive shots), the pressure of the high - pressure nozzles (if used), and the distance between the shot - blasting units and the workpiece. This allows for customization of the surface treatment based on the specific requirements of the workpiece material, the existing surface condition, and the desired final surface finish. For example, a delicate small - sized workpiece may require a gentler treatment, while a large - sized, more robust workpiece can withstand a more aggressive shot blasting process.
3.3 Cost - Efficiency
1. Reduced Labor Costs: The automated and adjustable nature of the machine significantly reduces the need for manual labor. In traditional shot blasting setups, workers may need to spend a significant amount of time and effort in manually loading and positioning workpieces of different sizes. With the adjustable hanger hook system, the process is streamlined, and the only human intervention required is setting up the machine for different workpiece sizes and monitoring its operation. This not only cuts down on labor costs but also reduces the variability in the quality of surface treatment that may be associated with manual handling.
2. Efficient Abrasive Usage: The abrasive media recycling and separation system ensures that the abrasive media is used efficiently. Since the machine can handle a wide range of workpiece sizes, the cost of abrasive media per unit of production is minimized. By recycling and reusing the shots, manufacturers can save a substantial amount of money over time, especially in high - volume production environments.
4. Applications in Different Industries
4.1 Automotive Industry
1. Diverse Component Treatment: The automotive industry produces a vast array of components, from small engine parts like valves and pistons to large body panels and chassis components. The adjustable hanger hook shot blasting machine can handle all these components. For small engine parts, the hanger hooks can be adjusted to a close - spaced and low - hanging position, while for large body panels, they can be widened and raised. The machine can clean the surfaces of these components, removing rust, casting residues, and improving the adhesion of coatings, which is essential for corrosion protection and aesthetic appeal.
2. Flexible Production Lines: In modern automotive manufacturing, production lines are designed to be flexible to accommodate different models and variants. The adjustable hanger hook shot blasting machine fits perfectly into this flexible production environment. It can quickly adapt to changes in the size and type of components being produced, ensuring that surface treatment processes can keep up with the dynamic production requirements.
4.2 Construction and Infrastructure Industry
1. Steel Structure Components: The construction industry uses a variety of steel structure components, such as beams, columns, and trusses, which come in different sizes. The machine can handle these large - sized components, effectively removing rust, mill scale, and preparing the surface for painting or galvanizing. For smaller steel components like bolts and brackets, the adjustable hanger hooks can be reconfigured to securely hold and treat these parts. This ensures that all steel components in a construction project receive the necessary surface treatment for long - term durability.
2. Custom - Made Fabrications: Construction often involves custom - made fabrications that may have unique sizes and shapes. The adjustable hanger hook shot blasting machine is well - suited for treating these custom components. It can be adjusted to fit the specific dimensions of each fabricated part, providing a cost - effective solution for surface treatment in construction projects where standard - sized components are not always used.
4.3 Electronics Industry
1. Miniature Component Cleaning: In the electronics industry, there are many small - sized components, such as connectors, circuit board housings, and small metal enclosures. The adjustable hanger hook shot blasting machine can be adjusted to handle these miniature components with precision. It can clean the surfaces of these components, removing any contaminants that could affect their electrical performance or the adhesion of protective coatings.
2. Large - Scale Electronic Equipment Parts: On the other hand, large - scale electronic equipment also has components that are relatively large, such as server racks and large - sized heat sinks. The machine's ability to adjust to different sizes allows it to treat these larger parts as well, ensuring that all components in the electronics manufacturing process receive the appropriate surface treatment.
5. Operation and Maintenance
5.1 Operation
1. Initial Setup: Before starting the treatment process, the operator needs to carefully set up the machine according to the size of the workpiece. This involves adjusting the horizontal and vertical position of the hanger hooks using the appropriate controls. The type and size of abrasive media need to be selected based on the workpiece material and the desired surface treatment. The intensity of the shot blasting, such as the speed of the centrifugal wheels or the pressure of the nozzles, also needs to be adjusted. Safety checks must be carried out to ensure that all protective guards are in place and the machine is in proper working condition.
2. Loading and Unloading: Workpieces are carefully loaded onto the adjusted hanger hooks at the loading station. The operator needs to ensure that the workpiece is securely attached to the hooks and is properly positioned for the shot blasting process. At the unloading station, the treated workpieces are carefully removed from the hooks. After unloading, the workpieces are inspected for quality. If any issues are detected, such as uneven surface treatment or damage, the machine settings may need to be adjusted for the next batch.
3. Monitoring: During the operation, the operator should continuously monitor the machine. This includes checking the performance of the shot - blasting units, ensuring that the hanger hook adjustment mechanism is working smoothly, and observing the quality of the treated workpieces. If any issues are detected, such as abnormal noise from the machine, inconsistent shot flow, or problems with the abrasive media recycling system, the machine should be stopped immediately for troubleshooting.
5.2 Maintenance
1. Regular Inspection: Regular inspection of the machine is essential to ensure its long - term reliable operation. Components such as the hanger hook adjustment mechanism, centrifugal wheels, nozzles (if applicable), and abrasive media recycling system should be inspected for wear and tear. The hanger hooks and the rails or conveyor mechanism may need to be checked for any signs of fatigue or damage, especially when handling heavy or frequently - adjusted workpieces. The vanes on the centrifugal wheels, which are subject to high - velocity impacts from the abrasive media, should be checked for erosion and replaced when necessary. The abrasive media recycling system should be inspected to ensure that there are no blockages in the chutes or conveyors.
2. Lubrication: Proper lubrication of moving parts is crucial for the smooth operation of the machine. The bearings on the hanger hook adjustment mechanism, the conveyor system, and the motors driving the shot - blasting units need to be lubricated regularly to reduce friction and prevent premature failure. This helps to maintain the accuracy and efficiency of the machine and reduces the risk of breakdowns during production.
3. Abrasive Media Management: The quality of the abrasive media also needs to be carefully managed. Over time, the abrasive shots may become worn or contaminated. The operator should periodically check the quality of the recycled abrasive and add new abrasive as needed to maintain the effectiveness of the shot blasting process. The type and size of the abrasive media may also need to be adjusted depending on the changing requirements of the workpiece production.
6. Conclusion
The adjustable hanger hook shot blasting machine has emerged as a game - changing solution in the field of surface treatment, offering unparalleled versatility in handling workpieces of different sizes. Its ability to provide optimal surface treatment, cost - efficiency, and adaptability to various industries make it an invaluable asset in modern manufacturing. By understanding its working principle, operation, and maintenance requirements, manufacturers can fully leverage the capabilities of this machine to enhance the quality and productivity of their production processes. As technology continues to evolve, it is expected that further improvements will be made to the adjustable hanger hook shot blasting machine, further expanding its applications and improving its performance in the treatment of diverse workpieces.