Hotline
+86-136 8495 9862
Email:cennia@szmizhi.com
Add::104,Building 27,Third Industrial Zone, Longxi Community,Longgang District,Shenzhen,China.
Coil Forming & Handling Equipment
Surface Treatment Equipment
Solutions
Application
About Us
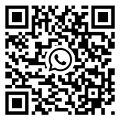
Welcome to MIZHI
For consultation/feedback, please call the service hotline: +86-136 8495 9862 Email:cennia@szmizhi.com
1. Introduction
In the realm of industrial surface preparation, the airless blasting machine has emerged as a game - changing technology. Surface preparation is a fundamental step in numerous industries, including manufacturing, construction, shipbuilding, and automotive. It involves removing contaminants, old coatings, and rust from surfaces to create a clean and suitable substrate for subsequent processes such as painting, coating, or bonding. The airless blasting machine offers a highly efficient, precise, and environmentally - friendly alternative to traditional surface - preparation methods.
2. Working Principle of Airless Blasting Machines
2.1. Media Acceleration
At the core of an airless blasting machine's operation is the acceleration of abrasive media. Instead of relying on compressed air to propel the media, as in traditional sandblasting, airless blasting machines use a mechanical means. A high - speed impeller, driven by an electric or hydraulic motor, is the key component responsible for this acceleration. The impeller has carefully designed vanes that catch the abrasive media, which can be materials like steel shot, grit, or even glass beads. As the impeller rotates at high speeds, typically ranging from 10,000 to 30,000 revolutions per minute, the media is flung outwards due to centrifugal force. This force accelerates the media to high velocities, often reaching speeds of 100 - 200 meters per second.
2.2. Media Delivery System
The media delivery system in an airless blasting machine is designed to ensure a continuous and controlled flow of abrasive media to the impeller. It starts with a storage hopper, which holds a large quantity of the abrasive media. The hopper is equipped with a feed mechanism, such as a vibrating tray or a screw conveyor. This mechanism regulates the amount of media that is fed into the impeller. The rate of media delivery can be adjusted according to the specific requirements of the surface - preparation task. For example, when dealing with a heavily rusted or coated surface, a higher media - feed rate may be required to increase the cleaning power. In contrast, for a more delicate surface that requires a gentler treatment, the media - feed rate can be reduced.
2.3. Target Surface Interaction
Once the abrasive media is accelerated by the impeller, it is directed towards the target surface. The high - velocity media impacts the surface with great force, causing a mechanical erosion effect. This impact removes contaminants, old paint, rust, and other unwanted materials from the surface. The size and shape of the abrasive media particles play a crucial role in the effectiveness of the surface - cleaning process. Larger and more angular particles are more aggressive and are suitable for removing thick layers of coatings or heavy rust. Smaller and rounder particles, on the other hand, are gentler and can be used for surface - finishing applications where a smooth surface texture is desired.
3. Components of an Airless Blasting Machine
3.1. Impeller Assembly
The impeller assembly is the heart of the airless blasting machine. It consists of the impeller itself, which is usually made of high - strength alloy steel to withstand the high - speed rotation and the impact of the abrasive media. The impeller vanes are designed with specific angles and shapes to optimize the acceleration of the media. The impeller is mounted on a shaft, which is connected to the motor. The shaft is supported by high - quality bearings to ensure smooth and stable rotation. The motor, whether electric or hydraulic, provides the necessary power to drive the impeller at the required speeds. Electric motors are commonly used in smaller - scale airless blasting machines, as they are relatively easy to install and maintain. Hydraulic motors, on the other hand, are preferred for larger and more powerful machines, as they can deliver high torque and are more suitable for continuous, heavy - duty operation.
3.2. Media Storage and Feeding System
The media storage and feeding system is another crucial component. The storage hopper, as mentioned earlier, stores the abrasive media. It is typically made of a durable material, such as steel or high - density polyethylene, to prevent wear and tear from the abrasive media. The hopper is designed with a sloping bottom to facilitate the flow of media towards the feed mechanism. The feed mechanism, whether it is a vibrating tray or a screw conveyor, is controlled by a variable - speed drive. This allows for precise adjustment of the media - feed rate. In some advanced airless blasting machines, the media - feeding system is also equipped with sensors to monitor the level of media in the hopper. When the media level gets low, an alarm can be triggered, and the machine can be stopped to prevent damage to the impeller due to insufficient media supply.
3.3. Dust Collection System
An efficient dust collection system is an essential part of an airless blasting machine. During the blasting process, a significant amount of dust is generated, which consists of the removed contaminants, old paint particles, and abrasive media fines. This dust can be a health hazard if not properly contained and can also cause environmental pollution. The dust collection system typically includes a dust collector unit, which can be of the cyclonic or bag - filter type. In a cyclonic dust collector, the dust - laden air is forced to spin in a circular motion. The centrifugal force causes the heavier dust particles to be thrown towards the walls of the cyclone and then fall into a collection bin. The cleaner air is then discharged from the top of the cyclone. Bag - filter dust collectors, on the other hand, use fabric bags to trap the dust particles. The dust - laden air passes through the bags, and the dust is collected on the surface of the bags. Periodically, the bags are cleaned, either by shaking or by using a reverse - air pulse, to remove the accumulated dust.
3.4. Control Panel
The control panel of an airless blasting machine is the interface between the operator and the machine. It allows the operator to control various parameters of the machine, such as the speed of the impeller, the media - feed rate, and the operation of the dust collection system. The control panel is usually equipped with digital displays to show the current values of these parameters. It also has switches, buttons, and knobs for adjusting the settings. In modern airless blasting machines, the control panel may be a touch - screen interface, which provides a more user - friendly and intuitive way to operate the machine. Some advanced control panels are also connected to a computer or a programmable logic controller (PLC), which can be used to automate certain functions of the machine and to record operating data for maintenance and quality - control purposes.
4. Types of Abrasive Media Used in Airless Blasting Machines
4.1. Steel Shot and Grit
Steel shot and grit are among the most commonly used abrasive media in airless blasting machines. Steel shot is small, spherical pellets made of steel. They are known for their high density and durability. Steel shot is suitable for applications where a relatively smooth surface finish is desired, such as in the preparation of metal surfaces for painting or in the peening of metal parts to improve their fatigue resistance. Steel grit, on the other hand, is made of crushed steel particles. It has a more angular shape compared to steel shot, which makes it more aggressive. Steel grit is used for removing thick layers of rust, old paint, and scale from surfaces. It is also commonly used in the surface preparation of concrete and stone.
4.2. Glass Beads
Glass beads are another popular abrasive media option. They are small, spherical beads made of glass. Glass beads are relatively soft compared to steel shot and grit, which makes them suitable for delicate surface - preparation tasks. They are often used in the aerospace industry, where the surfaces of aircraft components need to be cleaned without causing any damage to the underlying material. Glass beads are also used in the electronics industry to clean the surfaces of printed circuit boards and other sensitive components. In addition, glass beads can be used for surface - finishing applications, such as creating a smooth and reflective surface on metal parts.
4.3. Aluminum Oxide
Aluminum oxide is a very hard abrasive media. It is made from bauxite ore, which is processed to produce a fine - grained powder. This powder is then formed into abrasive particles. Aluminum oxide is highly effective in removing tough contaminants, such as hard - baked coatings and heavy rust. It is commonly used in the automotive industry for stripping old paint from car bodies and in the manufacturing of industrial equipment for cleaning and preparing metal surfaces. Aluminum oxide can be used in various particle sizes, with coarser sizes being more aggressive and finer sizes being suitable for more delicate surface - finishing work.
4.4. Garnet
Garnet is a natural abrasive media that is mined from deposits around the world. It is a hard, crystalline mineral that comes in various colors, such as red, orange, and brown. Garnet is a popular choice for environmentally - conscious applications, as it is a non - toxic and biodegradable abrasive. It is used in a wide range of industries, including shipbuilding, where it is used to clean the hulls of ships. Garnet is also suitable for surface - preparation work on concrete, wood, and stone. It can provide a good balance between cleaning power and surface - finish quality, making it a versatile abrasive media option.
5. Applications of Airless Blasting Machines
5.1. Manufacturing Industry
In the manufacturing industry, airless blasting machines are widely used for surface preparation of metal parts. Before parts are painted, coated, or assembled, they need to have a clean and rough - textured surface to ensure good adhesion of the coatings or to improve the fit between components. Airless blasting machines can quickly and efficiently remove rust, scale, and old coatings from metal parts. For example, in the production of automotive parts, airless blasting is used to clean the surfaces of engine blocks, transmission cases, and body panels. In the manufacturing of industrial machinery, airless blasting is used to prepare the surfaces of gears, shafts, and other components. The high - speed and precise nature of airless blasting machines allow for consistent and high - quality surface preparation, which is crucial for ensuring the performance and longevity of the final products.
5.2. Construction Industry
The construction industry also benefits greatly from airless blasting machines. In the restoration of old buildings, airless blasting can be used to remove layers of paint, dirt, and grime from brick, stone, and concrete surfaces. This helps to restore the original appearance of the building and also prepares the surface for repainting or other finishing treatments. In the construction of new buildings, airless blasting is used to clean and roughen the surfaces of concrete floors and walls before applying coatings or adhesives. It can also be used to remove formwork residue from concrete surfaces. In addition, airless blasting is used in the preparation of steel structures for painting and protection against corrosion. The ability to handle large - scale surface - preparation tasks makes airless blasting machines an essential tool in the construction industry.
5.3. Shipbuilding Industry
Shipbuilding is another industry where airless blasting machines play a crucial role. The hulls of ships are constantly exposed to harsh marine environments, which can cause rust and corrosion. Airless blasting machines are used to remove the rust and old paint from the hulls of ships during maintenance and repair work. They can also be used to prepare the surface of the hull for the application of anti - fouling coatings, which help to prevent the growth of marine organisms on the hull. In addition, airless blasting is used to clean the internal surfaces of ship tanks and pipelines. The high - power and efficient nature of airless blasting machines make them well - suited for the large - scale surface - preparation requirements of the shipbuilding industry.
5.4. Automotive Industry
In the automotive industry, airless blasting machines are used in several ways. As mentioned earlier, they are used for surface preparation of automotive parts before painting or coating. In addition, airless blasting can be used for the removal of dents and scratches from car bodies. By carefully controlling the blasting parameters, the high - velocity abrasive media can be used to gently reshape the metal surface, reducing the need for more invasive repair methods. Airless blasting is also used in the restoration of classic cars, where it can be used to remove layers of old paint and to prepare the surface for a new, high - quality paint job. The ability to achieve a consistent and smooth surface finish makes airless blasting machines a valuable tool in the automotive industry.
6. Advantages of Airless Blasting Machines over Traditional Methods
6.1. Higher Efficiency
Airless blasting machines are significantly more efficient than traditional surface - preparation methods, such as hand - scraping or using chemical strippers. The high - speed impeller in an airless blasting machine can accelerate the abrasive media to much higher velocities compared to the force that can be applied by hand - held tools. This results in a much faster removal of contaminants and coatings from the surface. For example, in a large - scale industrial painting project, an airless blasting machine can prepare a surface area several times larger in the same amount of time as a team of workers using hand - scraping methods. The continuous and automated media - feeding system in airless blasting machines also contributes to their high efficiency, as it allows for uninterrupted operation.
6.2. Precision and Consistency
Airless blasting machines offer a high level of precision and consistency in surface preparation. The controlled acceleration of the abrasive media and the ability to adjust the media - feed rate and impeller speed allow for precise control over the surface - cleaning process. This means that the same surface finish can be achieved across a large area, which is crucial for applications where uniformity is important, such as in the painting of automotive parts or the preparation of surfaces for bonding. In contrast, traditional methods, such as hand - scraping, are more prone to human error and can result in uneven surface preparation.
6.3. Environmentally - Friendly
Compared to some traditional surface - preparation methods, airless blasting machines are more environmentally friendly. Chemical strippers, for example, often contain harmful chemicals that can be released into the environment. Airless blasting, on the other hand, uses abrasive media, which is a non - chemical alternative. The dust collection system in airless blasting machines also helps to minimize the release of dust and contaminants into the air, reducing the environmental impact of the surface - preparation process. In addition, many of the abrasive media used in airless blasting, such as garnet, are biodegradable, further enhancing the environmental friendliness of the technology.
6.4. Cost - Effectiveness
In the long run, airless blasting machines can be more cost - effective than traditional surface - preparation methods. Although the initial investment in an airless blasting machine may be higher than that of some hand - held tools or small - scale chemical - stripping equipment, the high efficiency and lower labor requirements of airless blasting machines can result in significant cost savings over time. The ability to complete surface - preparation tasks more quickly means that less labor is required, and the overall project timeline can be reduced. In addition, the consistent and high - quality surface preparation achieved by airless blasting machines can lead to better adhesion of coatings and longer - lasting finishes, reducing the need for rework and maintenance costs.
7. Maintenance and Safety Considerations for Airless Blasting Machines
7.1. Maintenance
Regular maintenance is essential to keep an airless blasting machine in good working condition. The impeller and its associated components, such as the shaft and bearings, need to be inspected regularly for signs of wear and damage. The impeller vanes can be eroded by the abrasive media over time, and if not replaced, this can affect the performance of the machine. The media - feeding system, including the hopper, feed mechanism, and associated sensors, should also be checked regularly to ensure proper operation. The dust collection system requires regular maintenance, such as cleaning the dust collector unit, replacing the filter bags (if applicable), and checking for leaks in the system. The control panel and its associated electrical or hydraulic components should be inspected for any signs of malfunction. Regular lubrication of moving parts, such as the bearings and the motor, is also crucial to ensure smooth operation and to extend the lifespan of the machine.
7.2. Safety
Safety is a top priority when operating an airless blasting machine. The high - velocity abrasive media can be dangerous if not properly contained. Operators should always wear appropriate personal protective equipment, including safety goggles, protective clothing, and respiratory protection. The machine should be installed in a well - ventilated area to prevent the build - up of dust and fumes. The dust collection system should be properly maintained to ensure that it is effectively capturing the dust generated during the blasting process. The electrical and hydraulic components of the machine should be properly grounded and protected to prevent electrical accidents. In addition, the machine should be operated in accordance with the manufacturer's instructions, and any malfunctions or safety concerns should be addressed immediately. Training for operators on the proper use and maintenance of the airless blasting machine is also essential to ensure safe and efficient operation.
8. Future Trends in Airless Blasting Technology
8.1. Automation and Robotics
The future of airless blasting technology is likely to see an increased integration of automation and robotics. Automated airless blasting systems can be programmed to perform specific surface - preparation tasks with a high degree of precision and consistency. Robotics can be used to move the airless blasting machine around the work area, allowing for the treatment of complex - shaped surfaces. This can significantly improve the efficiency of surface - preparation processes, especially in large - scale industrial applications. In addition, automated systems can be equipped with sensors to monitor the surface condition in real - time and to adjust the blasting parameters accordingly, further enhancing the quality of the surface - preparation work.
8.2. Development of New Abrasive Media
There is a continuous research and development effort to develop new types of abrasive media for airless blasting machines. These new media are expected to offer improved performance, such as higher cleaning power, better surface - finishing capabilities, and enhanced environmental friendliness. For example, there may be the development of biodegradable and recyclable abrasive media that can reduce the environmental impact of the blasting process even further. New composite materials may also be developed to create abrasive media with unique properties, such as increased hardness and wear - resistance.
8.3. Energy - Efficiency Improvements
As energy costs continue to rise and environmental concerns become more prominent, there will be a greater focus on improving the energy efficiency of airless blasting machines. This may involve the development of more efficient motors, better - designed impellers to reduce energy losses, and the optimization of the overall machine design to minimize power consumption. Energy - recovery systems may also be integrated into airless blasting machines to capture and reuse the energy generated during the blasting process, further reducing the machine's energy footprint.
8.4. Integration with Other Manufacturing Processes
Airless blasting technology is likely to be more closely integrated with other manufacturing processes in the future. For example, it may be combined with automated painting or coating systems to create a seamless surface - preparation and finishing process. This integration can reduce the overall production time and cost, as well as improve the quality of the final product. In addition, airless blasting machines may be integrated with quality - control systems