Hotline
+86-136 8495 9862
Email:cennia@szmizhi.com
Add::104,Building 27,Third Industrial Zone, Longxi Community,Longgang District,Shenzhen,China.
Coil Forming & Handling Equipment
Surface Treatment Equipment
Solutions
Application
About Us
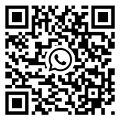
Welcome to MIZHI
For consultation/feedback, please call the service hotline: +86-136 8495 9862 Email:cennia@szmizhi.com
1. Automotive Industry: In the automotive industry, Wheelabrator shot blast machines are used to prepare body panels, engine parts, and other components for painting and coating. They can remove rust, scale, and old coatings, ensuring a clean and smooth surface for adhesion.
2. Aerospace Industry: The aerospace industry requires high-quality surface preparation for aircraft components and structures. Wheelabrator shot blast machines are used to remove contaminants, improve surface finish, and enhance the adhesion of protective coatings.
3. Construction and Infrastructure: In the construction and infrastructure sectors, Wheelabrator shot blast machines are used to prepare concrete surfaces for coatings, overlays, and decorative finishes. They can also be used to clean and prepare steel structures for painting and corrosion protection.
4. Manufacturing Industry: Across various manufacturing industries, Wheelabrator shot blast machines are used to prepare parts and components for painting, coating, welding, and other finishing processes. They can handle a wide range of materials and sizes, making them suitable for diverse manufacturing applications.
5. Foundry Industry: In foundries, Wheelabrator shot blast machines are used to clean castings and remove sand, oxides, and other contaminants. They can improve the surface quality of castings and prepare them for further processing.
VI. How to Choose the Right Wheelabrator Shot Blast Machine
When choosing a Wheelabrator shot blast machine, there are several factors to consider to ensure that you select the right machine for your specific needs. These include:
1. Surface Preparation Requirements: Determine the type of surface preparation required for your application. Consider factors such as the material being processed, the desired surface finish, and the level of cleanliness required. This will help you choose the appropriate blast wheel technology, abrasive media, and control system.
2. Production Volume and Capacity: Consider your production volume and capacity requirements. Determine the size and configuration of the shot blast machine that can handle your production needs without sacrificing efficiency or quality.
3. Budget: Set a budget for your surface preparation equipment purchase. Consider the initial cost of the machine, as well as ongoing operating and maintenance costs. Look for a machine that offers a good balance of performance and cost-effectiveness.
4. Service and Support: Consider the availability of service and support from the manufacturer or supplier. Ensure that you can get timely assistance with installation, training, maintenance, and repairs. Look for a company with a reputation for excellent customer service.
5. Customization Options: Depending on your specific application requirements, you may need a customized shot blast machine. Consider whether the manufacturer offers customization options, such as special sizes, configurations, or features.
VII. Maintenance and Care of Wheelabrator Shot Blast Machines
Proper maintenance and care are essential to ensure the long-term performance and reliability of your Wheelabrator shot blast machine. Here are some tips for maintaining your machine:
1. Regular Inspections: Perform regular inspections of your shot blast machine to check for signs of wear and tear, damage, or malfunction. Inspect the blast wheels, abrasive media, dust collection system, and other components for proper functioning.
2. Cleanliness: Keep your shot blast machine clean by regularly removing dust, debris, and spent abrasive media. This will help to prevent clogging and ensure efficient operation.
3. Lubrication: Lubricate moving parts as recommended by the manufacturer to reduce friction and wear. Use the appropriate lubricants and follow the recommended lubrication schedule.
4. Media Replacement: Replace abrasive media as needed to maintain optimal performance. Monitor the condition of the media and replace it when it becomes worn or contaminated.
5. Training and Safety: Provide proper training to operators on the safe and efficient operation of the shot blast machine. Follow all safety guidelines and procedures to prevent accidents and injuries.
VIII. Shot Blast Booth: Ensuring a Controlled Environment for Surface Preparation
A shot blast booth is an essential accessory for a Wheelabrator shot blast machine. It provides a controlled environment for surface preparation, ensuring safety, efficiency, and quality. In this section, we will take a closer look at shot blast booths, their features, benefits, and how they can enhance your surface preparation processes.
IX. Features and Components of a Shot Blast Booth
1. Enclosure: The enclosure of a shot blast booth is designed to contain the blast media and dust generated during the surface preparation process. It is typically made from steel or other durable materials and is equipped with viewing windows and access doors for operator convenience.
2. Lighting: Adequate lighting is essential for safe and efficient surface preparation. Shot blast booths are equipped with high-intensity lighting to ensure good visibility inside the booth.
3. Dust Collection System: A shot blast booth is integrated with a dust collection system to capture and filter the dust generated during the blasting process. This helps to maintain a clean and safe working environment.
4. Material Handling System: Depending on the size and configuration of the booth, it may be equipped with a material handling system to move parts or materials through the booth. This can include conveyor systems, hoists, or robotic manipulators.
5. Safety Features: Shot blast booths are equipped with various safety features, such as emergency stop buttons, safety interlocks, and explosion-proof lighting, to ensure the safety of operators.
X. Benefits of Using a Shot Blast Booth
1. Controlled Environment: A shot blast booth provides a controlled environment for surface preparation, minimizing the risk of dust and debris escaping into the surrounding area. This helps to maintain a clean and safe working environment and reduces the risk of contamination of other areas.
2. Improved Efficiency: By containing the blast media and dust, a shot blast booth can improve the efficiency of the surface preparation process. It allows for better control over the blasting parameters and reduces the need for frequent clean-up.
3. Enhanced Quality: A controlled environment in a shot blast booth can result in a more consistent and high-quality surface finish. It reduces the risk of contamination and ensures that the surface is prepared uniformly.
4. Safety: Shot blast booths are equipped with safety features to protect operators from the hazards of the blasting process. This includes protection from flying debris, dust inhalation, and noise.
5. Versatility: Shot blast booths can be customized to meet the specific needs of different applications. They can be designed to handle different sizes and shapes of parts, and can be equipped with various material handling systems.
XI. How to Choose the Right Shot Blast Booth
When choosing a shot blast booth, there are several factors to consider to ensure that you select the right booth for your specific needs. These include:
1. Size and Capacity: Determine the size and capacity of the booth required for your application. Consider the size of the parts or materials to be processed, as well as the production volume.
2. Blast Media Compatibility: Ensure that the shot blast booth is compatible with the abrasive media used in your Wheelabrator shot blast machine. Consider factors such as the type of media, its size, and its hardness.
3. Dust Collection System: The dust collection system of the shot blast booth should be efficient and capable of handling the volume of dust generated during the blasting process. Consider the filtration efficiency, capacity, and maintenance requirements of the system.
4. Material Handling System: Depending on your application requirements, you may need a specific material handling system in the shot blast booth. Consider options such as conveyor systems, hoists, or robotic manipulators.
5. Safety Features: Ensure that the shot blast booth is equipped with the necessary safety features to protect operators. Look for features such as emergency stop buttons, safety interlocks, and explosion-proof lighting.
XII. Maintenance and Care of a Shot Blast Booth
Proper maintenance and care are essential to ensure the long-term performance and reliability of your shot blast booth. Here are some tips for maintaining your booth:
1. Regular Cleaning: Keep the shot blast booth clean by regularly removing dust, debris, and spent abrasive media. This will help to prevent clogging and ensure efficient operation of the dust collection system.
2. Inspections: Perform regular inspections of the booth to check for signs of wear and tear, damage, or malfunction. Inspect the enclosure, lighting, dust collection system, and material handling system for proper functioning.
3. Filter Maintenance: The dust collection filters in the shot blast booth should be regularly cleaned or replaced to maintain their efficiency. Follow the manufacturer's recommendations for filter maintenance.
4. Safety Checks: Conduct regular safety checks to ensure that all safety features are functioning properly. Test emergency stop buttons, safety interlocks, and explosion-proof lighting regularly.
5. Training and Safety: Provide proper training to operators on the safe and efficient use of the shot blast booth. Follow all safety guidelines and procedures to prevent accidents and injuries.
XIII. Future Trends in Wheelabrator Shot Blast Machines and Shot Blast Booths
The field of surface preparation is constantly evolving, and Wheelabrator is at the forefront of innovation. Here are some future trends to look out for in Wheelabrator shot blast machines and shot blast booths:
1. Automation and Robotics: As the demand for increased productivity and efficiency grows, we can expect to see more automation and robotics in surface preparation. Wheelabrator is likely to continue developing automated shot blast machines and booths that can perform complex tasks with precision and consistency.
2. Intelligent Control Systems: Advanced control systems that can optimize the blasting process based on real-time data and feedback are likely to become more common. These systems will enable operators to achieve better results while reducing waste and energy consumption.
3. Environmentally Friendly Solutions: With growing concerns about environmental sustainability, there will be a greater focus on developing environmentally friendly surface preparation solutions. Wheelabrator is likely to continue investing in research and development to create shot blast machines and booths that are more energy-efficient and produce less waste.
4. Customization and Flexibility: As industries become more diverse and specialized, the demand for customized surface preparation solutions will increase. Wheelabrator is likely to offer more customization options and flexible configurations to meet the unique needs of different customers.
5. Integration with Digital Technologies: The integration of digital technologies such as the Internet of Things (IoT) and artificial intelligence (AI) is likely to transform the surface preparation industry. Wheelabrator may develop shot blast machines and booths that can be connected to digital networks for remote monitoring, diagnostics, and optimization.
XIV. Conclusion
The Wheelabrator shot blast machine and shot blast booth are powerful tools for surface preparation. With their advanced technology, superior performance, and wide range of applications, they can help you achieve high-quality surface finishes and improve the efficiency and productivity of your operations. By understanding the features, benefits, and applications of these products, and by choosing the right machine and booth for your specific needs, you can take your surface preparation processes to the next level. Whether you are in the automotive, aerospace, construction, manufacturing, or foundry industry, Wheelabrator has a solution that can meet your surface preparation requirements.