Hotline
+86-136 8495 9862
Email:cennia@szmizhi.com
Add::104,Building 27,Third Industrial Zone, Longxi Community,Longgang District,Shenzhen,China.
Coil Forming & Handling Equipment
Surface Treatment Equipment
Solutions
Application
About Us
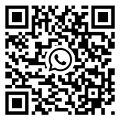
Welcome to MIZHI
For consultation/feedback, please call the service hotline: +86-136 8495 9862 Email:cennia@szmizhi.com
Roll forming machines are vital pieces of equipment in the manufacturing industry, used to transform flat metal sheets into various profiled products. For businesses looking to invest in these machines, the cost is a significant consideration. Discounts and promotions can offer substantial savings, making high - quality machines more accessible. This article will explore the availability of discounts and promotions for roll forming machines, with a particular focus on purlin roll forming machines.
General Availability of Discounts and Promotions
Seasonal Promotions
Many roll forming machine manufacturers and suppliers offer seasonal discounts. For example, during the end - of - financial - year periods, companies may want to clear their inventory to make room for new models or to meet sales targets. This often leads to significant price cuts on roll forming machines. In regions where the construction industry has peak and off - peak seasons, suppliers might offer promotions during the off - peak times to stimulate demand. For instance, in areas with harsh winters where construction activity slows down, roll forming machine suppliers may offer discounts from November to February. This is an opportune time for potential buyers, such as small - to - medium - sized metal fabricators or construction companies planning for the next season, to purchase machines at a reduced price.
Special Events and Trade Shows
Trade shows related to the manufacturing, construction, or metalworking industries are hotspots for discounts and promotions. Exhibitors at these shows, including roll forming machine manufacturers, often offer special deals to attract customers. They might provide on - the - spot discounts, free accessories, or extended warranties. For example, at a major international construction equipment trade show, a roll forming machine manufacturer could offer a 10% discount on all their machines to visitors who place an order during the show. Additionally, some companies use these events to launch new models and may offer discounted prices on older, but still reliable, models to clear stock. This benefits buyers who are looking for a good - quality machine at a more affordable price.
Factors Influencing Discount Eligibility
Quantity Purchases
Buyers who order multiple roll forming machines at once are more likely to be eligible for discounts. Manufacturers and suppliers are often willing to offer price breaks for bulk orders as it helps them increase their sales volume. For a construction company that needs to set up multiple production lines or a large - scale metal - working factory expanding its operations, ordering, say, five or more purlin roll forming machines could result in a discount of 15 - 20% off the regular price per unit. This not only reduces the overall cost of the machines but also ensures a consistent supply of equipment for the business's production needs.
Long - Term Business Relationships
Establishing a long - term relationship with a roll forming machine supplier can also lead to discounts and promotions. Suppliers value loyal customers and may offer preferential treatment in the form of price cuts, early access to new product promotions, or exclusive deals. A metal fabricator that has been purchasing machines from the same supplier for years may be offered a special discount when they decide to upgrade their equipment. The supplier may also provide additional services such as free maintenance consultations or priority technical support as part of the loyalty benefits.
Discounts and Promotions for Purlin Roll Forming Machines
Manufacturer - Specific Deals
Some manufacturers specialize in purlin roll forming machines and offer their own unique discounts. For example, a company that has developed a new and improved version of their purlin roll forming machine may offer a discount on the older model. A manufacturer might reduce the price of a semi - automatic purlin roll forming machine by 25% when they launch a fully - automatic, more advanced model. This allows them to sell off the existing inventory while still promoting their new technology. Additionally, manufacturers may offer package deals for purlin roll forming machines. They could bundle the machine with essential accessories like a coil reel, a cutting system upgrade, or a set of spare rollers at a discounted overall price.
Supplier - Initiated Promotions
Suppliers, especially those with a large inventory of purlin roll forming machines, may run promotions to move stock quickly. If a supplier has an overstock of a particular type of purlin roll forming machine, perhaps one that is designed for a specific market segment that has seen a temporary slowdown in demand, they may offer significant discounts. A supplier might offer a 30% discount on a purlin roll forming machine that is optimized for producing very large - sized purlins if there has been a lull in the large - scale construction projects that require such components. Suppliers may also collaborate with financial institutions to offer financing promotions for purlin roll forming machines. This could include low - interest loans or extended payment terms, effectively reducing the overall cost burden on the buyer.
How to Find Discounts and Promotions
Online Research
The internet is a powerful tool for finding discounts and promotions on roll forming machines. Potential buyers can start by visiting the websites of well - known roll forming machine manufacturers and suppliers. These sites often have a dedicated section for promotions, special offers, or clearance sales. Additionally, online marketplaces that deal with industrial equipment may list roll forming machines at discounted prices. Platforms like Alibaba or Made - in - China.com frequently feature deals on a variety of roll forming machines, including purlin roll forming machines. Buyers can use search filters to narrow down their options based on price, machine type, and discount percentage. Social media platforms can also be useful. Following roll forming machine manufacturers and industry - related groups on platforms like LinkedIn, Facebook, or Twitter may provide early access to discount announcements or exclusive offers.
Contacting Suppliers Directly
Reaching out to roll forming machine suppliers directly can yield valuable information about potential discounts and promotions. A simple phone call or email to the sales department of a supplier can initiate a conversation about any ongoing or upcoming deals. Suppliers may be more willing to offer personalized discounts based on the specific needs and circumstances of the buyer. For example, if a buyer can demonstrate that they have a long - term project that will require additional machines in the future, the supplier may be more inclined to offer a discount on the initial purchase as an incentive for future business.
Case Studies of Discount - Based Purchases
Case 1: Small - Scale Metal Fabricator
A small - scale metal fabricator was looking to expand its product line to include purlin production. The fabricator noticed that a roll forming machine manufacturer was running a promotion for the end - of - year. The manufacturer was offering a 15% discount on all their purlin roll forming machines. The fabricator, which had a limited budget, was able to take advantage of this discount. As a result, they were able to purchase a high - quality purlin roll forming machine that they otherwise could not afford at the regular price. This purchase not only allowed them to expand their business but also increased their competitiveness in the local market by offering a new product line.
Case 2: Construction Company
A construction company needed to purchase multiple purlin roll forming machines for a large - scale housing project. They contacted several suppliers and negotiated based on the quantity they were planning to buy. One supplier offered them a 20% discount per machine for ordering five purlin roll forming machines. In addition, the supplier provided free installation and a one - year extended warranty as part of the deal. The construction company was able to save a significant amount of money on the purchase, and the additional services provided by the supplier ensured a smooth start to their production for the housing project.
Conclusion
Discounts and promotions for roll forming machines, including purlin roll forming machines, are available through various channels and under different circumstances. Seasonal promotions, trade show offers, quantity - based discounts, and long - term relationship benefits are some of the ways buyers can save money on these essential pieces of equipment. By conducting thorough online research, reaching out to suppliers directly, and being aware of industry events, businesses can take advantage of these opportunities to acquire high - quality roll forming machines at more affordable prices. This not only helps in reducing the initial investment but also contributes to the overall competitiveness and growth of the business in the manufacturing and construction sectors.
Roof Roll Forming Machine: Revolutionizing the Roofing Industry
1. Introduction
The roof roll forming machine has emerged as a game - changing technology in the roofing sector. In the construction of residential, commercial, and industrial buildings, the roof is one of the most critical components, not only for providing shelter but also for enhancing the overall structural integrity and aesthetic appeal of the building. Roof roll forming machines play a pivotal role in manufacturing roofing materials with precision, efficiency, and versatility. These machines have transformed the way roofing sheets are produced, replacing traditional and often labor - intensive methods. This comprehensive exploration will cover various aspects of roof roll forming machines, including their working mechanisms, types, applications, advantages, and future prospects.
2. Working Mechanism
2.1 Material Feeding
The process begins with the supply of raw material, typically metal coils. These coils can be made of different metals such as galvanized steel, aluminum, or colored steel. The metal coil is loaded onto a decoiler, which is an integral part of the roof roll forming machine setup. The decoiler is designed to unwind the metal strip at a controlled rate. Advanced decoilers are equipped with tension control systems to ensure that the metal strip is fed into the forming section evenly without any slack or excessive tension. This precise control of the material feeding is crucial as it directly impacts the quality of the final roofing product.
2.2 Forming Process
Once the metal strip is fed from the decoiler, it enters the roll forming section. This is where the magic happens. The roll forming section consists of a series of rollers, each with a specific profile. As the metal strip passes through these rollers in a sequential manner, it gradually takes on the desired roofing profile. The rollers are carefully engineered to bend and shape the metal at specific angles and radii. For example, if the goal is to produce corrugated roofing sheets, the rollers will create a series of alternating ridges and troughs. The number of roller sets in a roof roll forming machine can vary depending on the complexity of the roofing profile. More intricate profiles may require a larger number of roller sets to achieve the correct shape.
2.3 Cutting and Finishing
After the metal strip has been formed into the roofing profile, the next step is cutting it to the desired length. Most roof roll forming machines are equipped with an automated cutting system. This can be either a flying shear or a fixed - position shear. A flying shear cuts the roofing sheet while it is still in motion, allowing for continuous production without the need to stop the machine. This significantly increases the production speed. On the other hand, a fixed - position shear requires the machine to stop briefly for each cut. Some advanced machines also offer additional finishing options. For instance, they can add a protective coating to the roofing sheet during the production process. This coating can enhance the durability and corrosion resistance of the roof, especially in harsh environmental conditions.
3. Types of Roof Roll Forming Machines
3.1 Single - Layer Roof Roll Forming Machines
Single - layer roof roll forming machines are the most basic type. They are designed to produce a single layer of roofing material. These machines are relatively simple in construction and are often used for applications where a basic roofing solution is required, such as in some agricultural buildings or low - cost housing projects. They are cost - effective to purchase and operate, making them accessible to small - scale contractors or those on a tight budget. However, they offer limited functionality compared to more advanced models.
3.2 Double - Layer Roof Roll Forming Machines
Double - layer roof roll forming machines have the capability to produce two - layer roofing systems. These machines are more complex as they need to handle the formation and assembly of two different layers simultaneously. The two - layer design can provide enhanced insulation and structural strength. For example, in some commercial buildings, a double - layer roof may consist of an outer layer for weather protection and an inner layer for thermal insulation. Double - layer roof roll forming machines are popular in regions where energy efficiency and durability are highly valued.
3.3 Multi - Profile Roof Roll Forming Machines
Multi - profile roof roll forming machines are highly versatile. They are equipped with interchangeable roller sets, allowing them to produce different roofing profiles. This is extremely beneficial for contractors or manufacturers who need to cater to a diverse range of projects. For instance, in a single production facility, they can switch between producing corrugated roofing sheets for industrial buildings and trapezoidal profiles for residential homes. The ability to produce multiple profiles reduces the need for multiple specialized machines, saving both space and cost.
3.4 Automatic Roof Roll Forming Machines
Automatic roof roll forming machines are at the forefront of technology in this field. They are equipped with advanced control systems, often based on computer - numerical - control (CNC) technology. Operators can input the desired specifications, such as the length of the roofing sheet, the type of profile, and the quantity required, into the control panel. The machine then automatically adjusts the decoiler speed, the roll forming process, and the cutting operation. These machines offer high precision and can produce roofing sheets at a much faster rate compared to manual or semi - automatic models. They are ideal for large - scale production facilities that need to meet high - volume demands.
4. Applications
4.1 Residential Roofing
In residential construction, roof roll forming machines have found widespread use. Homeowners and contractors can choose from a variety of profiles produced by these machines to match the architectural style of the house. For example, the classic corrugated profile provides a rustic look, while trapezoidal profiles offer a more modern and sleek appearance. The ability to produce roofing sheets on - site using a roll forming machine can also save costs, as it eliminates the need to transport pre - made sheets over long distances. Additionally, the customization options available with these machines allow for the creation of roofing solutions that fit the unique dimensions of each residential property.
4.2 Commercial Roofing
Commercial buildings, such as offices, shopping malls, and warehouses, require durable and efficient roofing systems. Roof roll forming machines can produce large - scale roofing sheets that are suitable for covering the extensive rooftops of these structures. The high - speed production capabilities of these machines make them ideal for meeting the tight deadlines often associated with commercial construction projects. Moreover, the ability to produce double - layer or multi - layer roofing systems using specialized machines provides enhanced insulation and weather resistance, which is crucial for maintaining a comfortable indoor environment in commercial buildings.
4.3 Industrial Roofing
Industrial buildings have unique roofing requirements. They often need roofing materials that can withstand heavy loads, extreme weather conditions, and exposure to industrial pollutants. Roof roll forming machines can produce thick - gauge roofing sheets with customized profiles to meet these demands. For example, in a factory where there may be a risk of falling debris, a stronger and more robust roofing profile can be produced. Additionally, the ability to add protective coatings during the roll forming process can enhance the corrosion resistance of the roof in industrial settings where chemical exposure may be a concern.
4.4 Agricultural Buildings
Agricultural buildings, such as barns and sheds, also benefit from the use of roof roll forming machines. These machines can produce cost - effective roofing solutions that are suitable for the agricultural environment. The corrugated profiles produced by these machines are popular in agricultural buildings as they provide good water runoff, preventing water from pooling on the roof. Moreover, the ability to produce roofing sheets on - site allows farmers to quickly repair or replace damaged roofing materials, minimizing downtime for their agricultural operations.
5. Advantages
5.1 High - Quality Output
One of the primary advantages of roof roll forming machines is the high - quality output they produce. The precise and sequential roll forming process ensures that each roofing sheet has consistent dimensions and a uniform shape. This is crucial for proper installation and long - term performance. In contrast, manually fabricated roofing sheets may have variations in size and shape, which can lead to leaks, improper drainage, and reduced structural integrity. The use of advanced control systems in modern roll forming machines further enhances the quality by allowing for real - time adjustments during the production process.
5.2 Cost - Efficiency
In the long run, roof roll forming machines offer significant cost savings. Although the initial investment in purchasing a machine can be substantial, especially for more advanced models, the ability to produce roofing sheets in - house reduces the cost of purchasing pre - made sheets from external suppliers. Additionally, the high - speed production capabilities of these machines lead to economies of scale. As the volume of production increases, the cost per unit of roofing sheet decreases. Moreover, the reduced need for transportation and the ability to minimize material waste contribute to overall cost - efficiency.
5.3 Customization
Roof roll forming machines provide a high degree of customization. With the use of interchangeable roller sets, different roofing profiles can be produced. This allows for the creation of roofing solutions that are tailored to the specific needs of each project. Whether it's a unique architectural design in a residential project or a specialized requirement in an industrial building, the customization options offered by these machines ensure that the roofing material not only functions properly but also enhances the overall look and performance of the building.
5.4 Productivity
The automation features of modern roof roll forming machines, especially in automatic models, significantly increase productivity. These machines can operate continuously, producing roofing sheets at a much faster rate than manual methods. The use of flying shears and advanced control systems allows for seamless production without significant interruptions. This increased productivity is beneficial for construction companies and manufacturers that need to complete projects in a timely manner, meeting the demands of clients and staying competitive in the market.
6. Future Prospects
6.1 Technological Advancements
The future of roof roll forming machines is likely to be characterized by continued technological advancements. There will be a greater integration of artificial intelligence (AI) and machine learning (ML) in these machines. AI - powered systems can analyze the production data in real - time, predict potential machine failures, and optimize the production process for maximum efficiency. Additionally, the development of more advanced materials, such as high - strength and lightweight alloys, will require the adaptation of roof roll forming machines to handle these materials effectively. New roller designs and machine settings will need to be developed to ensure the proper forming of these innovative materials.
6.2 Sustainability
Sustainability will be a key focus in the future of roof roll forming machines. There will be a growing demand for machines that can produce roofing materials from recycled or sustainable sources. Manufacturers will need to develop machines that are energy - efficient, reducing the carbon footprint associated with the production process. Additionally, the use of water - based or environmentally friendly coatings during the roll forming process will become more prevalent, further enhancing the sustainability of the roofing products.
6.3 Industry Integration
Roof roll forming machines are likely to be more closely integrated with other aspects of the construction industry. For example, they may be integrated with building information modeling (BIM) software. This integration would allow for seamless communication between the design phase of a building project and the production of roofing materials. The machine could directly receive the roofing specifications from the BIM model, ensuring that the produced roofing sheets are an exact match to the overall building design. This integration will lead to more efficient project management and reduced errors in the construction process.
In conclusion, roof roll forming machines have had a profound impact on the roofing industry and will continue to do so in the future. Their ability to produce high - quality, customized, and cost - effective roofing materials makes them an essential tool for construction companies, manufacturers, and contractors. As technology evolves and industry demands change, these machines will adapt and continue to revolutionize the way roofs are designed and constructed.