Hotline
+86-136 8495 9862
Email:cennia@szmizhi.com
Add::104,Building 27,Third Industrial Zone, Longxi Community,Longgang District,Shenzhen,China.
Coil Forming & Handling Equipment
Surface Treatment Equipment
Solutions
Application
About Us
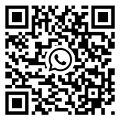
Welcome to MIZHI
For consultation/feedback, please call the service hotline: +86-136 8495 9862 Email:cennia@szmizhi.com
1. Introduction
In the highly competitive landscape of industrial manufacturing, the ability to process raw materials with utmost precision and efficiency is of paramount importance. Athader, a leading name in the field of coil processing lines, has established itself as a provider of top - notch slitting lines that cater to a diverse range of industries. These slitting lines are engineered to transform large coils of materials such as carbon steel, stainless steel, and aluminum into narrower coils with exceptional precision and cut quality. This not only enables manufacturers to meet the exacting demands of their customers but also enhances overall production efficiency and profitability.
2. Design Philosophy and Flexibility
2.1. Catering to Diverse Material Thicknesses
Athader's slitting lines are designed with an impressive range of thickness capabilities. They can handle materials as thin as 0.1 mm, which is crucial for industries like electronics where precision - cut thin strips are used for components such as circuit boards. On the other end of the spectrum, these lines can process materials up to a substantial 19 mm thick. This makes them suitable for heavy - duty applications in sectors like construction and large - scale manufacturing, where thick steel or aluminum strips are required for structural components. The flexibility in thickness handling is achieved through a combination of advanced mechanical engineering and intelligent control systems. For example, the slitting heads are designed to adjust the cutting force and blade penetration depth according to the thickness of the material being processed. This ensures that whether it's a delicate thin film or a thick metal slab, the cut is clean, accurate, and free from defects.
2.2. Adapting to Different Coil Sizes
In addition to thickness, Athader slitting lines are highly adaptable to various coil sizes. The uncoiling and recoiling mechanisms are engineered to handle coils of different diameters and weights. This is essential as different industries and production processes may require coils of specific dimensions. For instance, in the automotive industry, where large - scale production of parts from metal coils is common, the slitting lines need to be able to handle large - diameter and high - weight coils efficiently. Athader's slitting lines can accommodate coils with diameters and weights that are well - within the requirements of such high - volume manufacturing operations. The ability to work with different coil sizes also allows for greater flexibility in inventory management. Manufacturers can stock a variety of coil sizes and use the slitting line to process them into the desired narrow coils as per their production needs, without having to invest in multiple specialized machines for different coil sizes.
2.3. Customization Options
Athader understands that each customer has unique requirements. To meet these, the company offers a wide range of customization options for its slitting lines. Customers can choose from different types of slitting heads, tension control systems, and recoiling mechanisms based on their specific application. For example, if a customer is dealing with materials that are prone to stretching or wrinkling during the slitting process, they can opt for a more advanced tension control system that provides precise and consistent tension throughout the operation. Similarly, for applications where high - speed cutting is required, Athader can supply slitting lines with high - performance slitting heads that can operate at speeds of up to 500 mts/min for light - gauge materials. This level of customization ensures that the slitting line is tailored to the exact needs of the customer, maximizing productivity and product quality.
3. Key Components and Their Functions
3.1. Uncoiler
The uncoiler is the starting point of the slitting line process. Athader's uncoilers are designed to hold the large coils securely and unwind them at a controlled speed. They are available in both fixed - type and movable - type configurations. Fixed uncoilers are ideal for operations where the coil size and weight are relatively consistent. They are cost - effective and easy to maintain. Movable uncoilers, on the other hand, offer greater flexibility. They can be adjusted to accommodate coils of different diameters and weights, making them suitable for a wider range of applications. Advanced uncoilers from Athader are equipped with automatic tension control systems. These systems play a crucial role in ensuring that the material is unwound at a constant speed and with the right amount of tension. If the tension is too high, the material may stretch or break; if it is too low, the material may sag, leading to inaccuracies in the slitting process. The tension control system uses sensors to monitor the tension in real - time and adjusts the speed of the uncoiler accordingly.
3.2. Straightening and Leveling Units
Before the material reaches the slitting section, it often needs to be straightened and leveled. This is especially important for materials like metal coils, which may have some curvature or unevenness due to the coiling process or transportation. Athader's straightening and leveling units are highly effective in removing these imperfections. They consist of multiple rollers arranged in a specific pattern. As the material passes through these rollers, the rollers apply pressure to straighten and flatten the material. The number of rollers and their diameter can vary depending on the thickness and type of material. For example, thicker materials may require fewer but larger - diameter rollers, while thinner materials may need more rollers with smaller diameters to achieve the desired flatness. Some of Athader's advanced straightening and leveling units also use sensors to detect any remaining imperfections in the material and make real - time adjustments to the roller pressure. This ensures that the material is in the optimal condition for slitting, resulting in higher - quality cut strips.
3.3. Slitter Head
The slitter head is the heart of the slitting line machine, and Athader has invested heavily in research and development to make theirs stand out. These slitter heads are designed with ultra - precision components that guarantee maximum width precision and minimum strip burr. They feature slitter arbors mounted on double eccentrics for precise penetration. The eccentrics are driven by motorized AC drives, and the gap penetration is displayed on the operator screen, providing real - time feedback. The frames of the slitter heads are robust and highly rigid, ensuring stability during the cutting process. Ultra - precision and preloaded bearings are used to reduce friction and wear, while hydraulic and high - pressure locks keep the blades in place. The shear shafts are precision - machined from high - strength steel. Thanks to this precision and robustness, Athader can offer different sizes of shears to cut thicknesses ranging from 0.15 mm to 19 mm. The slitter heads also offer advantages such as increased blade life, automatic gap adjustment, automatic tooling block and change, and “zero” axial clearances. Some models even come with scrap choppers and a slitting head tooling assembly robot, further enhancing efficiency and reducing downtime.
3.4. Recoiler
After the material has been slit into the desired strips, the recoiler winds each strip into a smaller coil. Athader's recoilers are designed to wind the strips neatly and tightly. They have a variable - speed motor that can adjust the winding speed according to the speed of the slitting process. This ensures that the tension in the strips is maintained during the winding process. The recoiler also has a mechanism to control the diameter of the wound coils. This is important because different applications may require coils of specific diameters. Some of Athader's recoilers are equipped with an automatic coil - transfer system. Once a coil is fully wound, the system automatically transfers the coil to a pallet or another storage area, allowing the recoiler to start winding the next coil without interruption. This significantly increases the productivity of the slitting line. In addition, the recoilers are designed to be compatible with the overall control system of the slitting line, ensuring seamless operation.
3.5. Scrap Winder
During the slitting process, some material on the edges of the coil, known as trim or scrap, is removed. Athader's scrap winders are responsible for collecting and compressing this scrap material for recycling or disposal. The scrap winder typically consists of a rotating drum or spool. As the scrap material is produced, it is guided onto the drum and wound around it. The drum is often powered by a motor, which can be adjusted to control the speed of the scrap winding. In some cases, the scrap winder may also be equipped with a cutting mechanism. This mechanism cuts the scrap material into smaller pieces, making it easier to handle and transport. For example, in a metal slitting line, the scrap winder may cut the metal scrap into small, manageable pieces that can be easily recycled. The scrap winder is an important component of the slitting line as it helps to keep the work area clean and organized, and also ensures that the scrap material is properly processed.
3.6. Control System
Modern Athader slitting lines are equipped with sophisticated control systems. These control systems are typically based on programmable logic controllers (PLCs) or industrial computers. The control system allows operators to set various parameters, such as the width of the slit strips, the cutting speed, the tension of the material, and the winding speed of the recoiler. For example, an operator can input the desired strip width on a touch - screen interface, and the control system will automatically adjust the position of the blades in the slitter head. The control system also monitors the operation of the machine in real - time. It uses sensors to detect any abnormalities, such as changes in tension, speed, or temperature. If an issue is detected, the control system can automatically stop the machine or make adjustments to prevent damage to the machine or the material. Some advanced control systems from Athader also have remote - monitoring capabilities. This allows plant managers or maintenance personnel to monitor the performance of the slitting line machine from a remote location, such as an office or a control room. This not only improves the efficiency of machine operation but also enables timely maintenance and troubleshooting.
4. Technological Advancements
4.1. Ultra - Precision Cutting Technology
Athader's slitting lines are renowned for their ultra - precision cutting capabilities. The double - eccentric slitting heads, with their automatic locking and gap - setting systems, ensure that the cut widths are extremely accurate. The precision of the cutting is so high that it can meet the tightest tolerances required by industries such as aerospace and medical device manufacturing. In the aerospace industry, for example, metal strips used in the construction of aircraft components need to be cut with extremely high precision to ensure the structural integrity and safety of the aircraft. Athader's slitting lines can achieve this level of precision, making them a preferred choice for aerospace suppliers. The use of high - quality materials in the blades and other cutting components also contributes to the long - term accuracy of the cutting process. The blades are made of hardened steel or carbide, which not only ensures sharpness but also resists wear and tear, maintaining the cutting precision over an extended period.
4.2. Advanced Tension Control Systems
Tension control is a critical aspect of the slitting process, and Athader has developed advanced systems to address this. The automatic tension control systems in Athader's slitting lines can adjust the tension in real - time based on the material being processed. Different types of automatic tension systems are available, depending on the material characteristics. For example, for materials that are more prone to stretching, such as some types of aluminum alloys, a more sensitive tension control system may be used. These systems can also compensate for any “camber” in the material. Camber is a common issue in coils, where the strip has a slight curvature along its length. The tension control system can detect the camber and adjust the tension on either side of the strip to ensure that it is fed through the slitting line evenly, resulting in straight and accurate cuts. This advanced tension control technology is essential for producing high - quality slit coils.
4.3. Automatic Tooling and Changeover Systems
To minimize downtime and increase productivity, Athader's slitting lines are equipped with automatic tooling and changeover systems. These systems allow for quick and easy replacement of the cutting tools, such as the blades in the slitter head. In a high - volume production environment, every minute of downtime can result in significant losses. The automatic tooling change systems can change the tools in a matter of minutes, compared to the hours it may take for manual tool changes. Some of Athader's slitting lines also feature a tool assembly robot. This robot can accurately assemble the cutting tools, ensuring that they are properly aligned and installed. This not only reduces the time required for tool changes but also improves the quality of the tool installation, leading to more consistent and accurate cutting performance.
4.4. Integration of Smart Technologies
Athader is at the forefront of integrating smart technologies into its slitting lines. Internet of Things (IoT) sensors are installed throughout the machine to monitor the performance of each component in real - time. These sensors can collect data on factors such as temperature, vibration, and wear of the components. The data is then analyzed using advanced algorithms to predict maintenance needs. For example, if a sensor detects that a particular bearing is showing signs of increased wear, the system can alert the maintenance team in advance, allowing them to schedule maintenance before a breakdown occurs. This predictive maintenance approach helps to reduce unplanned downtime and extend the lifespan of the machine. The slitting lines can also be integrated with the customer's Manufacturing Execution System (MES) or Enterprise Resource Planning (ERP) system. This integration enables seamless communication between the slitting line and the overall production process, allowing for better production planning and control.
5. Applications Across Industries
5.1. Automotive Industry
In the automotive industry, Athader slitting lines are used for a variety of applications. Metal strips are cut to precise widths for the production of car body panels, such as doors, hoods, and fenders. The high - precision cutting capabilities of the slitting lines ensure that the panels fit together perfectly during the assembly process. This not only improves the structural integrity of the vehicle but also enhances its aesthetic appearance. In addition, Athader slitting lines are used to produce metal strips for automotive interior components, such as seat frames and dashboard supports. The ability to produce consistent and accurate strip widths is crucial in the automotive industry, as any deviation can lead to problems in the assembly process and affect the quality of the final product. The slitting lines can also handle different types of automotive - grade metals, including high - strength steel and aluminum alloys, which are increasingly being used in modern vehicles to reduce weight and improve fuel efficiency.
5.2. Construction Industry
The construction industry also benefits greatly from Athader slitting lines. Metal strips are cut for roofing, wall cladding, and structural components. For roofing applications, the slitting lines can produce long, continuous strips that are easy to install and provide a seamless finish. In the case of wall cladding, the precise cutting ensures that the panels fit together tightly, providing a weather - resistant and aesthetically pleasing exterior. For structural components, such as steel beams and columns, the slitting lines can produce the required metal strips with the right dimensions and quality. The ability to process thick and heavy materials makes Athader slitting lines suitable for large - scale construction projects. In addition, the slitting lines can be used to cut metal strips for decorative elements in construction, such as railing components and architectural accents, adding a touch of elegance and functionality to buildings.
5.3. Electronics Industry
In the electronics industry, Athader slitting lines are used to cut materials such as copper foils, insulating films, and printed circuit board (PCB) materials. Copper foils are slit into narrow strips for use in the production of electrical conductors in electronic devices. The precision of the cutting is crucial, as even the slightest deviation in the width of the copper strips can affect the electrical performance of the device. Insulating films are also slit to the appropriate widths for use in protecting and insulating electronic components. In the production of PCBs, the slitting lines can cut the large sheets of PCB materials into smaller, more manageable sizes. The high - speed and high - precision cutting capabilities of Athader slitting lines enable electronics manufacturers to meet the high - volume production requirements of the industry while maintaining strict quality control.
5.4. Packaging Industry
The packaging industry relies on Athader slitting lines to produce narrow strips of materials such as paper, plastic films, and aluminum foils. These strips are used for various packaging applications, such as making bags, labels, and wrapping materials. The ability to produce consistent and accurate strip widths is essential in the packaging industry, as it ensures the proper fit and functionality of the packaging products. For example, in the production of food packaging, the slitting lines can cut plastic films to the exact width required for wrapping food products, ensuring a tight seal and proper protection of the contents. The slitting lines can also handle different types of packaging materials, including biodegradable and recyclable materials, which are becoming increasingly popular in the packaging industry due to environmental concerns.
6. Installation, Maintenance, and Customer Support
6.1. Installation and Commissioning
Athader provides comprehensive installation and commissioning services for its slitting lines. A team of experienced technicians is dispatched to the customer's site to install the machine. The installation process is carefully planned and executed to ensure that all components are properly assembled and integrated. Once the installation is complete, the technicians conduct a series of tests to ensure that the slitting line is operating correctly. This includes testing the cutting accuracy, tension control, and overall performance of the machine. During the commissioning process, the technicians also train the customer's operators on how to use the slitting line safely and efficiently. They provide hands - on training on all aspects of the machine, including setting up the parameters, changing the tools, and troubleshooting common issues. This ensures that the customer can start using the slitting line as soon as possible and get the most out of its capabilities.
6.2. Regular Maintenance
Regular maintenance is essential to keep an Athader slitting line operating at peak performance. The company provides detailed maintenance schedules and guidelines to its customers. Maintenance tasks include routine inspection of all components, such as the uncoiler, straightening and leveling units, slitter head, recoiler, and scrap winder. The blades in the slitter head should be inspected regularly for sharpness and wear. Dull blades can cause poor - quality cuts, increased burrs, and higher energy consumption. When the blades are worn, they should be sharpened or replaced. The rollers in the straightening and leveling units and the recoiler should also be inspected for wear and misalignment. Worn rollers can cause the material to be unevenly straightened or wound. Lubrication of moving parts, such as bearings, gears, and shafts, is crucial. Proper lubrication reduces friction, extends the lifespan of the components, and improves the overall efficiency of the machine. The control system of the slitting line should also be maintained. This includes checking for software updates, ensuring that the sensors are working properly, and testing the emergency stop systems.