Hotline
+86-136 8495 9862
Email:cennia@szmizhi.com
Add::104,Building 27,Third Industrial Zone, Longxi Community,Longgang District,Shenzhen,China.
Coil Forming & Handling Equipment
Surface Treatment Equipment
Solutions
Application
About Us
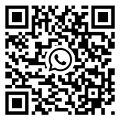
Welcome to MIZHI
For consultation/feedback, please call the service hotline: +86-136 8495 9862 Email:cennia@szmizhi.com
I. Introduction
Automatic cut to length machines have become indispensable in modern manufacturing and processing industries. These machines are designed to precisely cut various materials, such as metals, plastics, fabrics, and wires, to specific lengths with a high degree of automation. They have revolutionized the production process by reducing manual labor, increasing efficiency, and improving the accuracy of cut lengths. This has led to enhanced product quality and greater productivity in a wide range of applications.
II. Types of Automatic Cut to Length Machines
1.Shearing - based Cut to Length Machines
These machines are commonly used for cutting sheet materials, especially metals. They operate based on the principle of shearing force. The machine consists of a set of blades that are carefully aligned and actuated to cut the material. The blades are usually made of high - quality tool steel with sharp cutting edges. In some cases, the shearing action is powered by a hydraulic system, which provides the necessary force to cut through thick and tough materials. For example, in the steel processing industry, shearing - based cut to length machines can handle steel sheets of different thicknesses, from thin gauges used in automotive body panels to thick plates for construction applications.
2.Saw - based Cut to Length Machines
Saw - based machines are suitable for cutting materials that require a more aggressive cutting action. Circular saws or band saws are often employed. Circular saws are ideal for cutting materials with a relatively small cross - sectional area, such as bars or tubes. The rotating saw blade cuts through the material with high speed and precision. Band saws, on the other hand, are more versatile and can handle larger workpieces. They are often used in cutting wood, plastic, or metal profiles. The continuous band of the saw blade allows for efficient cutting of long lengths of material. In the furniture manufacturing industry, saw - based cut to length machines are used to cut wooden components to the exact lengths required for assembly.
3.Laser - based Cut to Length Machines
Laser - based cut to length machines utilize high - intensity laser beams to cut materials. This type of machine offers extremely high precision and can be used for cutting a wide variety of materials, including those that are difficult to cut with traditional methods. The laser beam is focused onto the material surface, melting or vaporizing it to create a clean cut. Laser cutting is particularly advantageous for cutting intricate shapes and patterns in materials like thin - gauge metals, plastics for electronics components, and even some fabrics in the textile industry. The non - contact nature of laser cutting minimizes the risk of material deformation during the cutting process.
4.Flying - shear Cut to Length Machines
Flying - shear machines are designed for high - speed cutting of continuous materials, such as coils of wire or metal strips. Unlike traditional stationary cutting methods, the flying - shear mechanism moves with the material during the cutting process. This enables continuous and rapid cutting without stopping the material flow. The cutting blades in a flying - shear machine are synchronized with the speed of the material to ensure accurate cut lengths. In wire production plants, flying - shear cut to length machines are used to cut long lengths of wire into specific lengths for further processing or packaging.
III. Working Principle of Automatic Cut to Length Machines
1.Material Feeding System
The first step in the operation of an automatic cut to length machine is the material feeding process. The machine has a feeding mechanism that can handle different types of materials. For sheet materials, rollers are often used to transport the material through the machine. These rollers can be driven by motors and are designed to provide a smooth and consistent feeding speed. In the case of wire or bar materials, a conveyor system or a series of guiding rollers may be employed. The feeding system is usually adjustable to accommodate materials of different widths, thicknesses, or diameters. Sensors are placed along the feeding path to monitor the position and speed of the material.
2.Length Measurement and Control
Accurate length measurement is a critical part of the automatic cut to length process. Different measurement techniques are used depending on the type of machine. In some machines, encoder wheels are attached to the feeding rollers. These encoder wheels measure the distance the material has traveled by counting the number of rotations. For more precise measurements, linear measurement sensors such as laser distance meters or optical encoders can be used. The measured length data is sent to the control system of the machine. The control system then compares the actual length with the preset length value and triggers the cutting operation when the desired length is reached.
3.Cutting Operation
As mentioned earlier, the cutting operation varies depending on the type of machine. In shearing - based machines, when the control system signals the cutting action, the hydraulic or mechanical actuators drive the blades to cut through the material. The blades are designed to close with a specific force and speed to ensure a clean cut. In saw - based machines, the saw blade rotates at high speed, and the material is fed into the cutting zone. The cutting speed and feed rate are carefully controlled to achieve the desired cut quality. In laser - based machines, the laser beam is turned on and focused onto the material at the appropriate time. The energy of the laser beam is adjusted based on the material type and thickness to ensure efficient cutting. In flying - shear machines, the cutting blades accelerate to match the speed of the moving material and then make the cut.
4.Post - cutting Processing and Quality Control
After the cutting operation, some machines may have additional post - cutting processing steps. For example, in the cutting of metal sheets, the edges may be deburred to remove any sharp edges or burrs created during the cutting process. Quality control mechanisms are also an important part of the machine's operation. Sensors can be used to check the length accuracy of the cut pieces. Any pieces that do not meet the specified length tolerance are either flagged for re - cutting or removed from the production line. In some cases, visual inspection systems may be employed to detect any surface defects or irregularities on the cut material.
IV. Key Components of Automatic Cut to Length Machines
1.Feeding Rollers or Conveyor System
The feeding rollers or conveyor system is responsible for moving the material through the machine. The rollers are usually made of materials with low friction coefficients to minimize resistance. They may have rubber or polyurethane coatings to improve grip on the material. The conveyor system, if used, can be a belt - type conveyor or a chain - driven conveyor depending on the material's weight and nature. The design of the feeding system ensures that the material is fed at a constant and controllable speed.
2.Cutting Unit
The cutting unit is the core component of the machine and depends on the type of cutting mechanism. In shearing machines, it consists of the upper and lower blades, blade holders, and the actuating mechanism. The blades are carefully aligned and have a specific clearance between them to ensure proper cutting. In saw - based machines, the cutting unit includes the saw blade, the motor that drives the saw blade, and the blade - guiding system. In laser - based machines, the cutting unit is the laser generator, the optical focusing system, and the beam - delivery system. In flying - shear machines, the cutting unit has the moving blades, the drive system to synchronize the blades with the material speed, and the associated control components.
3.Length Measurement Sensors
Length measurement sensors are crucial for accurate cutting. Encoder wheels are simple and cost - effective sensors that are widely used. They are usually mounted on the feeding rollers and have a high - resolution encoding system to measure the distance traveled by the material. Laser distance meters are more accurate and can measure the length of the material without physical contact. Optical encoders can also provide highly precise length measurements. These sensors are connected to the control system of the machine to provide real - time length data.
4.Control System
The control system is the brain of the automatic cut to length machine. It consists of a programmable logic controller (PLC) or a computer - based control unit. The control system receives input from the length measurement sensors, operator - set parameters (such as the desired cut length and cutting speed), and other sensors in the machine (such as tension sensors in some cases). Based on this information, the control system controls the operation of the feeding system, the cutting unit, and any post - cutting processing steps. It also monitors the machine's status and can generate alarms or error messages if any issues are detected.
V. Advantages of Automatic Cut to Length Machines
1.High - precision Cutting
Automatic cut to length machines are capable of achieving extremely high - precision cuts. The advanced length measurement sensors and control systems ensure that the cut lengths are within very tight tolerances. This precision is crucial in many industries where the dimensions of the cut material directly affect the quality of the final product. For example, in the electronics industry, precise cutting of wire lengths is essential for proper circuit assembly. In the automotive industry, accurate cutting of metal parts ensures proper fit and function during vehicle assembly.
2.Increased Productivity
These machines significantly increase productivity compared to manual cutting methods. The automated operation allows for continuous cutting without the need for frequent stops and starts. The high - speed cutting capabilities of some machines, especially flying - shear and laser - based machines, enable large quantities of materials to be processed in a short time. Additionally, the reduction in manual labor not only speeds up the process but also reduces the risk of human errors during cutting.
3.Versatility in Material Handling
Automatic cut to length machines can handle a wide variety of materials. They are not limited to a specific type of material or thickness. Shearing - based machines can cut different metals, from soft aluminum to hard steel. Saw - based machines can handle materials ranging from wood to plastics and metals. Laser - based machines can be used for cutting delicate materials like fabrics and thin - gauge metals as well as thicker materials with the appropriate laser power. This versatility makes them suitable for diverse manufacturing applications.
4.Improved Quality Control
The integrated quality control mechanisms in these machines ensure that the cut material meets the required quality standards. The length measurement sensors and other inspection systems detect any deviations from the specified length or any surface defects. This allows for immediate corrective action, such as re - cutting or adjusting the machine parameters. By consistently producing high - quality cut pieces, the overall quality of the final products is enhanced, reducing the number of rejects and customer complaints.
VI. Challenges and Solutions in the Operation of Automatic Cut to Length Machines
1.Material Variability and Compatibility
One of the main challenges is dealing with the variability of materials. Different materials have different physical properties, such as hardness, elasticity, and melting points. This can affect the cutting process. For example, a cutting blade that works well for cutting a soft plastic may not be suitable for cutting a hard metal. To address this, machines may have adjustable cutting parameters. The operator can select the appropriate cutting speed, force, or laser power based on the material being processed. Additionally, using specialized cutting tools or blades for different material types can improve the cutting quality.
2.Cutting Blade or Tool Wear
In shearing and saw - based machines, the cutting blades or tools are subject to wear over time. Worn - out blades can lead to poor cut quality, such as rough edges, burrs, or inaccurate cut lengths. Regular inspection of the blades is necessary. The blades should be sharpened or replaced when they show signs of wear. Using high - quality cutting tools and providing proper lubrication during the cutting process can extend the lifespan of the blades. In laser - based machines, the laser - generating components may also require maintenance and calibration over time to maintain their cutting efficiency.
3.Length Measurement Accuracy and Calibration
The accuracy of length measurement is crucial for the performance of the machine. However, factors such as sensor drift, mechanical vibrations, or changes in environmental conditions can affect the measurement accuracy. Regular calibration of the length measurement sensors is required. This can involve using standard calibration tools and procedures to ensure that the sensors are providing accurate readings. Additionally, the machine's mechanical components, such as the feeding rollers, should be inspected and maintained to prevent any issues that could affect the length measurement, such as misalignment or uneven rotation.
4.Automation and Integration with Production Lines
Integrating automatic cut to length machines with other production processes can be challenging. The machine needs to be synchronized with the upstream and downstream operations in the production line. For example, if the cut material is to be fed into a subsequent assembly process, the speed and timing of the cutting machine need to be coordinated with the assembly process. To achieve this, advanced control systems and communication protocols may be used. The machine can be equipped with interfaces that allow it to communicate with other machines in the production line, enabling seamless integration.
VII. Conclusion
Automatic cut to length machines have transformed the way materials are cut in various industries. Their diverse types, working principles, key components, advantages, and the challenges associated with their operation all contribute to the complex landscape of modern manufacturing. With continuous technological advancements and improvements in design, these machines are expected to become even more efficient, accurate, and versatile, further enhancing the productivity and quality of manufacturing processes. As industries continue to demand higher - quality cut materials in shorter production times, the role of automatic cut to length machines will only become more prominent.