Hotline
+86-136 8495 9862
Email:cennia@szmizhi.com
Add::104,Building 27,Third Industrial Zone, Longxi Community,Longgang District,Shenzhen,China.
Coil Forming & Handling Equipment
Surface Treatment Equipment
Solutions
Application
About Us
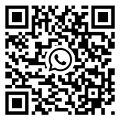
Welcome to MIZHI
For consultation/feedback, please call the service hotline: +86-136 8495 9862 Email:cennia@szmizhi.com
I. Introduction
An automatic cut - to - length machine represents a significant technological advancement in the field of material processing. It is designed to precisely cut a continuous length of material, such as metal, plastic, or paper, into specific lengths without the need for extensive manual intervention. This type of machine has found wide - ranging applications across various industries, including manufacturing, construction, and packaging, due to its ability to enhance productivity, improve accuracy, and reduce labor costs.
II. Working Principles of Automatic Cut - to - length Machines
1. Material Feeding Mechanism
- The first step in the operation of an automatic cut - to - length machine is the material feeding process. These machines are equipped with a feeding mechanism that ensures a consistent and controlled supply of the material to be cut. For example, in the case of a metal strip, a set of rollers may be used to draw the strip from a coil or a stack. The rollers are often driven by a motor, and their speed can be adjusted to match the desired cutting rate. The feeding mechanism also includes features to maintain proper tension on the material. If the tension is too high, the material may stretch or break, while too low tension can lead to wrinkling or inaccurate feeding. Tension control devices, such as load cells or spring - loaded mechanisms, are employed to keep the tension within an optimal range.
2. Measuring and Sensing Systems
- To achieve accurate cut - to - length operations, automatic cut - to - length machines rely on precise measuring and sensing systems. One common method is the use of encoder wheels. These wheels are attached to the feeding rollers and are designed to measure the linear displacement of the material. As the material moves, the encoder wheel rotates, and the number of rotations is translated into the length of the material that has passed through. Another important sensing device is the photoelectric sensor. It is used to detect the leading and trailing edges of the material. This information is crucial for triggering the cutting operation at the correct moment. Additionally, some machines may use laser - based measurement systems for even higher accuracy, especially when dealing with very thin or high - value materials.
3. Cutting Mechanisms
- There are several types of cutting mechanisms employed in automatic cut - to - length machines. One popular option is the shear - cutting mechanism. In shear cutting, two blades move relative to each other to cut through the material. This method is suitable for thicker materials, such as metal sheets. The blades are typically made of high - quality steel and are sharpened regularly to ensure clean and accurate cuts. Another type is the rotary - cutting mechanism. Rotary cutters consist of a circular blade that rotates at a high speed. They are often used for cutting softer materials like plastic films or paper. The rotary blade can be adjusted in terms of its rotational speed and the depth of cut to accommodate different materials and thicknesses. In some advanced machines, laser - cutting technology is also utilized. Laser cutting offers extremely high precision and can be used for a wide range of materials, from metals to non - metals. It works by melting or vaporizing the material along the desired cut line.
III. Types of Automatic Cut - to - length Machines
1. Guillotine - style Machines
- Guillotine - style automatic cut - to - length machines are characterized by a large, flat blade that moves vertically to cut the material. These machines are often used for cutting large - format materials, such as large sheets of plywood or metal plates. They offer high - cutting force and are capable of handling thick materials with ease. The guillotine blade is usually hydraulically or pneumatically actuated, which allows for a quick and powerful cutting action. The material is placed on a flat bed, and the blade descends to make the cut. These machines are known for their simplicity and reliability in cutting straight lines.
2. Flying - shear Machines
- Flying - shear automatic cut - to - length machines are designed to cut the material while it is in motion. This is a key advantage for high - speed production lines. The flying shear consists of a set of blades that move synchronously with the moving material. As the material passes through the machine at a constant speed, the flying shear cuts it at the desired length without the need to stop the material flow. This type of machine requires precise control systems to ensure accurate cutting, as any deviation in the speed or position of the shear blades can result in inaccurate cut lengths. Flying - shear machines are commonly used in industries where continuous production and high throughput are essential, such as the steel and aluminum processing industries.
3. Circular - saw - based Machines
- Circular - saw - based automatic cut - to - length machines use a circular saw blade to cut the material. These machines are suitable for cutting materials with a certain thickness, such as wooden boards or plastic profiles. The circular saw blade rotates at a high speed, and the material is fed towards the blade. The advantage of circular - saw - based machines is their versatility in cutting different shapes and angles. They can be adjusted to make bevel cuts or miter cuts, depending on the requirements of the end - product. However, they require proper safety measures due to the exposed saw blade, and regular maintenance to keep the blade sharp and properly aligned.
IV. Control Systems in Automatic Cut - to - length Machines
1. Programmable Logic Controllers (PLCs)
- Programmable Logic Controllers (PLCs) play a central role in the control of automatic cut - to - length machines. PLCs are programmed to manage various aspects of the machine's operation, such as the feeding speed of the material, the activation of the cutting mechanism, and the overall production sequence. For example, a PLC can be programmed to adjust the feeding speed based on the length of the material remaining in the coil or stack. It can also control the cutting mechanism to ensure that each cut is made at the exact specified length. PLCs are highly reliable and can operate in harsh industrial environments. They are capable of handling multiple input and output signals, which allows them to interface with various sensors and actuators on the machine.
2. Human - Machine Interfaces (HMIs)
- Human - Machine Interfaces (HMIs) provide an interface between the operators and the automatic cut - to - length machine. Through the HMI, operators can set parameters such as the desired cut length, the number of cuts to be made, and the production speed. The HMI also displays real - time information about the status of the machine, such as the current length of the material that has been processed, the status of the cutting mechanism (e.g., if the blade needs sharpening), and any error messages. Modern HMIs are often touch - screen based, making it easy for operators to interact with the machine and monitor its performance.
3. Sensor - based Feedback Control
- Sensor - based feedback control is essential for the accurate operation of automatic cut - to - length machines. As mentioned earlier, sensors such as encoder wheels, photoelectric sensors, and load cells are used to measure various parameters of the material and the machine's operation. The data collected by these sensors is fed back to the control system (usually the PLC). Based on this feedback, the control system can make real - time adjustments to optimize the machine's performance. For example, if a photoelectric sensor detects that the material is not properly aligned, the control system can adjust the feeding rollers to correct the alignment. If the encoder wheel indicates that the material is being fed too fast or too slow, the PLC can adjust the motor speed accordingly.
V. Applications of Automatic Cut - to - length Machines in Different Industries
1. Manufacturing Industry
- In the manufacturing industry, automatic cut - to - length machines are used for a wide variety of materials. For example, in the automotive manufacturing process, these machines are used to cut metal sheets for car body parts, such as doors, hoods, and fenders. The accuracy of the cut - to - length operation is crucial as it ensures that the parts fit together properly during assembly. In the electronics manufacturing industry, automatic cut - to - length machines are used to cut printed circuit boards (PCBs) and flexible substrates. These materials need to be cut to precise lengths to meet the design requirements of electronic devices. Additionally, in the furniture manufacturing industry, these machines are used to cut wooden boards and veneers to the required lengths for constructing tables, chairs, and cabinets.
2. Construction Industry
- The construction industry heavily relies on automatic cut - to - length machines. For building materials such as metal roofing sheets, siding panels, and structural steel members, these machines are used to cut the materials to the exact lengths required on the construction site. This not only saves time but also reduces waste. In the case of concrete formwork, automatic cut - to - length machines can be used to cut plywood or plastic sheets to the appropriate sizes. Moreover, for the installation of electrical wiring and plumbing pipes, these machines can be used to cut wires and pipes to the correct lengths, ensuring efficient installation and minimizing the need for on - site adjustments.
3. Packaging Industry
- In the packaging industry, automatic cut - to - length machines are essential for processing packaging materials. For example, in the production of cardboard boxes, these machines are used to cut large rolls of corrugated cardboard into the appropriate lengths for box - making. For plastic films used for wrapping products, automatic cut - to - length machines are used to cut the films to the required sizes. This is particularly important for products that require a specific amount of packaging material, such as food items or consumer goods. The ability to accurately cut the packaging materials to length helps to reduce material waste and improve the overall appearance of the packaged product.
VI. Advantages of Automatic Cut - to - length Machines
1. High Precision
- One of the main advantages of automatic cut - to - length machines is their high precision. These machines are capable of cutting materials to extremely accurate lengths, often within a tolerance of a few millimeters or even less. This level of precision is crucial in industries where the fit and function of the end - product depend on the accuracy of the cut lengths. For example, in the aerospace industry, where components need to fit together precisely, automatic cut - to - length machines are used to cut materials such as titanium sheets and composite materials with high accuracy.
2. Increased Productivity
- Automatic cut - to - length machines can significantly increase productivity compared to manual cutting methods. They can operate at high speeds, continuously cutting materials without the need for frequent breaks. Moreover, the automated nature of these machines means that they can be integrated into production lines, allowing for a seamless flow of materials from one process to another. This reduces production time and increases the overall output of the manufacturing process. For instance, in a steel processing plant, a flying - shear automatic cut - to - length machine can cut steel coils into desired lengths much faster than manual cutting, enabling the plant to meet higher production demands.
3. Cost - effectiveness
- Although the initial investment in an automatic cut - to - length machine may be relatively high, in the long run, these machines are cost - effective. They reduce labor costs as they require minimal human intervention once set up. Additionally, the high precision of these machines reduces material waste. Since the cuts are accurate, there is less scrap material generated. For example, in the packaging industry, accurate cutting of packaging materials reduces the amount of material that is wasted due to incorrect lengths, thereby saving on material costs.
VII. Challenges and Solutions in Automatic Cut - to - length Machine Operation
1. Material Variability
- One of the challenges in automatic cut - to - length machine operation is dealing with material variability. Different materials have different properties, such as thickness, hardness, and elasticity, which can affect the cutting process. For example, cutting a thick and hard metal sheet requires a different cutting force and blade type compared to cutting a thin and soft plastic film. To address this, automatic cut - to - length machines are often equipped with adjustable cutting mechanisms. The cutting force, blade speed, and depth of cut can be adjusted according to the material being processed. Additionally, some machines use intelligent control systems that can automatically detect the type of material and adjust the cutting parameters accordingly.
2. Maintenance Requirements
- Automatic cut - to - length machines have relatively complex mechanical and electrical components, which require regular maintenance. The cutting blades, for example, need to be sharpened or replaced regularly to ensure accurate cuts. The feeding rollers may wear out over time and need to be replaced. The sensors and control systems also need to be checked and calibrated periodically. To simplify maintenance, some machines are designed with modular components that can be easily removed and replaced. Additionally, manufacturers often provide maintenance schedules and guidelines to help operators keep the machines in optimal condition.
3. Integration with Existing Production Lines
- Integrating an automatic cut - to - length machine into an existing production line can be a challenge. Compatibility issues may arise in terms of the speed of material flow, the communication between different machines, and the overall layout of the production line. To overcome these challenges, manufacturers often offer customization options for their machines. They can adjust the machine's design and control system to match the requirements of the existing production line. Additionally, the use of standard communication protocols and interfaces can facilitate the integration process, allowing the automatic cut - to - length machine to communicate effectively with other machines on the production line.
VIII. Future Trends in Automatic Cut - to - length Machines
1. Integration with Industry 4.0
- Automatic cut - to - length machines will increasingly be integrated with Industry 4.0 concepts. This means that they will be connected to the factory's overall network, allowing for real - time data sharing. Operators will be able to remotely monitor and control the machines, and predictive maintenance will become more common. Sensors on the machines will be able to detect potential problems before they cause a breakdown, and the necessary maintenance can be scheduled in advance. Additionally, the machines will be able to exchange data with other machines on the production line, enabling more efficient production planning and resource allocation.
2. Advanced Cutting Technologies
- There will be a continued development of advanced cutting technologies in automatic cut - to - length machines. For example, laser - cutting technology may become more prevalent and more affordable, allowing for even higher precision cutting of a wider range of materials. Plasma - cutting technology may also be explored for certain applications, especially for cutting thick metals. Additionally, new types of cutting blades and mechanisms may be developed to improve the cutting efficiency and quality for different materials.
3. Customization and Flexibility
- As the demand for more customized products increases, automatic cut - to - length machines will need to become more flexible. They will be designed to handle a wider range of materials and cut - to - length requirements. Machines may be equipped with programmable cutting patterns and adjustable cutting parameters to meet the specific needs of different customers. This will enable manufacturers to produce a greater variety of products without the need for extensive re - tooling or investment in multiple specialized machines.
In conclusion, automatic cut - to - length machines are a vital part of modern manufacturing and processing industries. Their ability to accurately cut materials to length, along with their advantages in terms of productivity, cost - effectiveness, and precision, make them an indispensable tool. As technology continues to evolve, these machines will continue to improve and adapt to meet the ever - changing needs of different industries.