Hotline
+86-136 8495 9862
Email:cennia@szmizhi.com
Add::104,Building 27,Third Industrial Zone, Longxi Community,Longgang District,Shenzhen,China.
Coil Forming & Handling Equipment
Surface Treatment Equipment
Solutions
Application
About Us
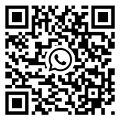
Welcome to MIZHI
For consultation/feedback, please call the service hotline: +86-136 8495 9862 Email:cennia@szmizhi.com
Introduction
An automatic shot blaster is a highly efficient and technologically advanced piece of equipment that has become an indispensable tool in various industries. It is designed to clean, prepare, or finish surfaces by propelling abrasive particles at high velocities onto the workpiece. This automated process offers numerous advantages over traditional manual methods, making it a preferred choice for many surface treatment applications.
Working Principle
The operation of an automatic shot blaster typically involves several key steps :
Loading and Positioning: The workpieces are first loaded onto a conveyor system or placed inside a blasting chamber. The machine ensures proper alignment and secure fixation of the items to be blasted, enabling efficient and uniform cleaning.
Abrasive Propulsion: Once the workpieces are in position, the automatic shot blaster activates a high-speed impeller or other mechanisms to accelerate abrasive projectiles, such as steel balls or grit, towards the surface. The abrasive particles strike the surface with controlled force, effectively removing contaminants, rust, coatings, and other imperfections.
Dust Collection: During the blasting process, a significant amount of dust and debris is generated. To maintain a clean working environment and protect the operators' health, automatic shot blasters are equipped with robust dust extraction systems. These systems capture and remove the dust particles, preventing them from spreading in the workplace.
Abrasive Recuperation: Many automatic shot blasters also incorporate an abrasive recovery system. This system collects the used abrasive particles, separates them from the debris, and allows for their reuse. By recycling the abrasive, the machine not only reduces waste but also contributes to cost savings and environmental sustainability.
Surface Inspection: After the blasting procedure is complete, the surface is carefully inspected. Any remaining contaminants or flaws can be identified and addressed, ensuring that the final surface meets the required quality standards.
Types of Automatic Shot Blasters
Wheel Blast Machines: Wheel blast machines are widely used in the industry due to their high efficiency and ability to handle large volumes of workpieces. They operate by using a high-speed rotating wheel to accelerate the abrasive media against the surface. There are several subtypes of wheel blast machines, each designed for specific applications :
Tumble Blast Machines: Ideal for small, bulk parts, tumble blast machines work like a tumbler, where the parts are tumbled inside a chamber while being blasted with abrasive media. This ensures that all surfaces of the parts are evenly cleaned.
Table Blast Machines: Suited for larger, flat parts, table blast machines have a flat table where the workpieces are placed. The abrasive is then directed at the surface from above or from the sides, providing precise and uniform cleaning.
Spinner Hanger Blast Machines: These are designed for hanging parts, such as those with irregular shapes or complex geometries. The parts are suspended from a hanger and rotated while being blasted, allowing for complete coverage and effective cleaning of all surfaces.
Continuous Blast Machines: Best for high-volume production lines, continuous blast machines operate continuously, with workpieces being fed into the blasting chamber at a constant rate. This ensures a seamless and efficient blasting process, maximizing productivity.
Air Blast Machines: Air blast machines offer greater flexibility and precision, making them suitable for a wide range of applications, especially those requiring delicate handling or detailed work. They use compressed air to shoot abrasive media at the surface. Some common types of air blast machines include:
Suction Blast Machines: In suction blast machines, the abrasive is drawn into the airstream by suction, creating a vacuum effect. This allows for precise control of the abrasive flow and is often used for light cleaning or deburring tasks.
Pressure Blast Machines: Pressure blast machines operate by forcing the abrasive media out of a nozzle at high pressure, similar to a firehose. They provide more powerful blasting capabilities and are suitable for heavier cleaning or surface preparation jobs.
Wet Blast Machines: Wet blast machines combine water with abrasive media to create a slurry, which is then propelled at the surface. This method offers a cleaner finish, reduces dust generation, and is often used for applications where a smooth and polished surface is required.
Applications
Automatic shot blasters find extensive use in numerous industries, thanks to their versatility and effectiveness in surface treatment :
Construction Industry: In construction, automatic shot blasters are used to prepare concrete surfaces before applying coatings, such as epoxy or paint. They can remove old paint, dirt, and laitance from concrete floors, walls, and other structures, improving the adhesion of the new coating and enhancing its durability. Shot blasters are also employed to clean and prepare steel structures, such as bridges, beams, and columns, by removing rust and mill scale, thereby preventing corrosion and extending the lifespan of the structures.
Automotive Industry: The automotive sector relies on automatic shot blasters for various applications, including cleaning engine components, preparing car bodies for painting, and removing paint and corrosion from chassis and other metal parts. By providing a clean and roughened surface, shot blasting improves the adhesion of paint and coatings, resulting in a better finish and increased resistance to wear and tear. Additionally, shot blasting can be used for peening processes to strengthen metal components, enhancing their durability and performance under stress.
Aerospace Industry: In the aerospace industry, where precision and quality are of utmost importance, automatic shot blasters play a crucial role in surface preparation. They are used to clean and deburr aircraft components, such as turbine blades, landing gear, and fuselage parts. Shot blasting helps to remove any surface imperfections, improve fatigue life, and enhance the adhesion of protective coatings, ensuring the safety and reliability of aerospace structures.
Foundry Industry: Foundries use automatic shot blasters to clean castings, removing sand, scale, and other residues from the surface of metal castings. This process not only improves the appearance of the castings but also prepares them for further processing, such as machining or coating. Shot blasting can also be used to enhance the surface finish of castings, reducing the need for additional finishing operations and saving time and cost.
Shipbuilding Industry: Shipbuilders employ automatic shot blasters to clean and prepare the surfaces of ship hulls, decks, and other components. By removing rust, paint, and other contaminants, shot blasting provides a clean and suitable surface for the application of anti-corrosion coatings and paints. This helps to protect the ship from the harsh marine environment and extends its service life.
Manufacturing and Metalworking Industries: In general manufacturing and metalworking, automatic shot blasters are used for a variety of tasks, such as cleaning and preparing metal sheets, plates, and fabricated parts before welding, painting, or assembly. They can also be used for surface texturing, creating a desired roughness or finish on the workpiece for aesthetic or functional purposes.
Benefits
The use of automatic shot blasters offers several significant benefits compared to traditional surface treatment methods :
Enhanced Productivity and Efficiency: Automatic shot blasters are capable of processing a large number of workpieces in a relatively short period. Their automated operation reduces the need for manual labor, minimizes human error, and significantly increases productivity. This allows businesses to complete projects faster, meet tight deadlines, and improve overall operational efficiency.
Uniform and Consistent Cleaning: These machines ensure consistent and uniform surface cleaning, leaving no untreated areas or uneven surfaces. The controlled propulsion of abrasive particles guarantees a uniformly textured and smooth profile, which is essential for achieving high-quality surface finishes and proper adhesion of coatings.
Improved Surface Preparation for Coating: By effectively removing contaminants, rust, and other surface imperfections, automatic shot blasters create an ideal surface for coating application. This enhances the adhesion of coatings, such as paint, epoxy, or powder coating, resulting in a more durable and long-lasting finish. The improved coating adhesion also reduces the likelihood of peeling, flaking, or premature failure, thereby reducing maintenance costs and increasing the lifespan of the coated surfaces.
Versatility: Automatic shot blasters can handle a wide variety of materials, including metals, concrete, stone, and composites. They can be adjusted to accommodate different workpiece sizes, shapes, and surface requirements, making them suitable for diverse applications across multiple industries. This versatility allows businesses to use the same equipment for different projects, maximizing its utility and return on investment.
Cost-effectiveness: Although the initial investment in an automatic shot blaster may be higher than that of manual tools, the long-term cost savings are significant. The increased productivity, reduced labor requirements, and efficient use of abrasive media result in lower operating costs over time. Additionally, the abrasive recovery system helps to minimize material waste, further reducing costs associated with abrasive consumption.
Enhanced Safety: Automatic shot blasters are equipped with various safety features, such as safety interlocks, emergency stop buttons, and dust collection systems, to protect the operators from potential hazards. The automated operation also reduces the operators' exposure to abrasive particles and other risks associated with manual blasting, improving workplace safety and reducing the likelihood of accidents and injuries.