Hotline
+86-136 8495 9862
Email:cennia@szmizhi.com
Add::104,Building 27,Third Industrial Zone, Longxi Community,Longgang District,Shenzhen,China.
Coil Forming & Handling Equipment
Surface Treatment Equipment
Solutions
Application
About Us
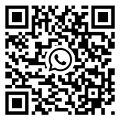
Welcome to MIZHI
For consultation/feedback, please call the service hotline: +86-136 8495 9862 Email:cennia@szmizhi.com
In the modern manufacturing landscape, the demand for wire mesh products across various industries such as construction, automotive, and filtration has been steadily increasing. To meet this high - volume demand efficiently, manufacturers are turning to advanced machinery, and one such crucial equipment is the automatic wire mesh shot blasting machine. This machine plays a pivotal role in the mass production of wire mesh products, enhancing both the quality and quantity of output.
Working Principle of Automatic Wire Mesh Shot Blasting Machine
The automatic wire mesh shot blasting machine operates on a relatively straightforward yet highly effective principle. It uses a high - velocity stream of abrasive media, typically small metal shots, to clean, strengthen, and prepare the surface of wire mesh products.
Shot Projection System
At the heart of the machine is the shot projection mechanism. This consists of one or more powerful centrifugal wheels. These wheels are designed to accelerate the abrasive shots to high speeds. The shots are fed into the center of the wheel and are then flung outwards through specially designed vanes at extremely high velocities, often reaching speeds of up to 100 meters per second or more. This high - speed projection allows the shots to impact the wire mesh surface with significant force.
Wire Mesh Conveyor System
To ensure continuous and efficient processing for mass production, the machine is equipped with an automated wire mesh conveyor system. The wire mesh products are placed on a conveyor belt that moves them through the blasting chamber at a controlled speed. The speed of the conveyor can be adjusted according to the type of wire mesh, the desired level of surface treatment, and the production volume requirements. As the wire mesh moves through the chamber, it is exposed to the intense stream of abrasive shots from multiple angles, ensuring comprehensive surface treatment.
Abrasive Recovery and Recycling System
In a mass - production setup, efficient use of abrasive media is essential to keep production costs down. The automatic wire mesh shot blasting machine incorporates an abrasive recovery and recycling system. After the shots have impacted the wire mesh and fallen to the bottom of the blasting chamber, they are collected through a series of chutes and conveyors. The used shots are then passed through a separation system. This system removes any dust, debris, and broken shots, ensuring that only clean and usable shots are recycled back into the shot projection system for further use. This closed - loop system not only saves on the cost of abrasive media but also reduces environmental waste.
Advantages of Automatic Wire Mesh Shot Blasting Machine in Mass Production
Enhanced Product Quality
Surface Cleaning: One of the primary advantages is its ability to thoroughly clean the surface of wire mesh products. In mass production, wire mesh may accumulate dirt, rust, or scale during the manufacturing process or storage. The high - velocity shots from the blasting machine effectively remove all these contaminants, leaving a clean and smooth surface. This is crucial for applications such as filtration systems, where a clean surface ensures optimal performance.
Surface Strengthening: The impact of the abrasive shots on the wire mesh surface also induces a process known as shot peening. This causes the surface layer of the wire mesh to undergo plastic deformation, creating compressive stresses. These compressive stresses significantly improve the fatigue resistance and durability of the wire mesh products. For example, in automotive applications where wire mesh is used in components such as fuel filters or exhaust systems, the enhanced strength provided by shot blasting can withstand the harsh operating conditions and vibrations, extending the lifespan of the components.
Improved Coating Adhesion: When wire mesh products are to be coated for corrosion protection or decorative purposes, a proper surface preparation is essential. The shot blasting process creates a rough and textured surface on the wire mesh, which greatly improves the adhesion of coatings. In mass production, this means that the coated wire mesh products are more likely to maintain their coating integrity over time, reducing the risk of coating peeling or flaking.
High Production Efficiency
Continuous Processing: The automated conveyor system in the shot blasting machine allows for continuous processing of wire mesh products. This is in stark contrast to manual or semi - automated surface treatment methods, which often involve batch - by - batch processing. In a mass - production environment, the ability to continuously feed wire mesh into the machine and obtain treated products at the other end significantly increases the production throughput. For instance, a large - scale construction project may require thousands of square meters of wire mesh for reinforcement. With an automatic shot blasting machine, this large quantity can be processed in a relatively short time.
Customizable Processing Parameters: The machine offers a high degree of flexibility in terms of processing parameters. The speed of the conveyor, the intensity of shot projection (which can be adjusted by changing the rotational speed of the centrifugal wheels), and the type and size of abrasive media can all be customized according to the specific requirements of the wire mesh products. This means that different types of wire mesh, such as fine - gauge mesh for sieving applications or heavy - duty mesh for industrial fencing, can be efficiently processed on the same machine, further optimizing production efficiency.
Cost - Effectiveness
Reduced Labor Costs: In mass production, labor costs can be a significant expense. The automatic nature of the wire mesh shot blasting machine reduces the need for a large number of manual laborers. Instead of relying on workers to manually clean and treat the wire mesh, the machine can perform these tasks with minimal human intervention. This not only cuts down on labor costs but also reduces the variability in the quality of surface treatment that may be associated with manual work.
Efficient Abrasive Usage: As mentioned earlier, the abrasive recovery and recycling system in the machine ensures that the abrasive media is used efficiently. This reduces the need to constantly purchase new abrasive, resulting in significant cost savings over the long term. In a mass - production facility that processes large volumes of wire mesh on a daily basis, these savings in abrasive costs can be substantial.
Operation and Maintenance of Automatic Wire Mesh Shot Blasting Machine
Operation
Initial Setup: Before starting the mass - production process, the machine needs to be properly set up. This involves adjusting the conveyor speed to match the production requirements. If different types of wire mesh are to be processed, the operator also needs to select the appropriate abrasive media and adjust the shot projection intensity. Additionally, safety checks must be carried out to ensure that all protective guards are in place and the machine is in proper working condition.
Loading and Unloading: Wire mesh products are loaded onto the conveyor at the input end of the machine. The operator needs to ensure that the mesh is properly positioned on the conveyor to ensure even treatment. At the output end, the treated wire mesh is unloaded and either sent for further processing (such as coating) or packaged for shipment.
Monitoring: During the operation, the operator should continuously monitor the machine. This includes checking the performance of the shot projection system, ensuring that the abrasive recovery system is working smoothly, and observing the quality of the treated wire mesh. If any issues are detected, such as uneven surface treatment or a decrease in shot projection power, the machine may need to be stopped for troubleshooting.
Maintenance
Regular Inspection: Regular inspection of the machine is crucial to ensure its long - term reliable operation. Components such as the centrifugal wheels, conveyor belts, and abrasive recovery system should be inspected for wear and tear. The vanes on the centrifugal wheels, which are subject to high - velocity impacts from the abrasive shots, may need to be replaced periodically. The conveyor belts should be checked for any signs of stretching or damage, and the abrasive recovery system should be inspected to ensure that there are no blockages.
Lubrication: Proper lubrication of moving parts is essential. The bearings on the conveyor rollers and the motors driving the centrifugal wheels need to be lubricated regularly to reduce friction and prevent premature failure. This helps to maintain the smooth operation of the machine and reduces the risk of breakdowns during mass production.
Abrasive Media Management: The quality of the abrasive media also needs to be managed. Over time, the abrasive shots may become worn or contaminated. The operator should periodically check the quality of the recycled abrasive and add new abrasive as needed to maintain the effectiveness of the shot blasting process.
Applications of Wire Mesh Products Treated by Automatic Shot Blasting Machine
Construction Industry
Reinforcement Mesh: In the construction of buildings and infrastructure, wire mesh is widely used as reinforcement in concrete structures. The shot - blasted wire mesh has better adhesion to concrete due to its rough surface, which enhances the structural integrity of the concrete. This is especially important in large - scale construction projects where the durability and strength of the structure are of utmost importance.
Fencing and Screening: Wire mesh fencing and screening are common in construction sites and residential areas. The shot - blasted surface of the wire mesh not only provides a clean and aesthetically pleasing appearance but also improves its resistance to corrosion, ensuring a longer lifespan for the fencing and screening products.
Automotive Industry
Filters: As mentioned earlier, wire mesh is used in various automotive filters, such as oil filters, air filters, and fuel filters. The shot - blasted surface of the wire mesh improves its filtration efficiency by providing a better surface for trapping contaminants. It also enhances the durability of the filters, which is crucial in the demanding automotive environment.
Exhaust Systems: Some components in automotive exhaust systems, such as catalytic converter substrates, may use wire mesh. The shot - blasting process strengthens the wire mesh, allowing it to withstand the high temperatures and vibrations associated with exhaust systems.
Filtration and Sieving Industry
Industrial Filtration: In industries such as chemical, pharmaceutical, and food and beverage, wire mesh filters are used to separate solids from liquids or gases. The shot - blasted surface of the wire mesh ensures that the filter has a clean and efficient filtration surface, reducing the risk of clogging and improving the overall filtration performance.
Sieving Applications: For sieving powders and granular materials, wire mesh sieves with shot - blasted surfaces offer better durability and accuracy in particle separation. The clean and smooth surface of the sieves, achieved through shot blasting, allows for more efficient flow of materials through the mesh.
Conclusion
The automatic wire mesh shot blasting machine has become an indispensable tool in the mass production of wire mesh products. Its ability to enhance product quality, increase production efficiency, and offer cost - effectiveness makes it a preferred choice for manufacturers across various industries. By understanding its working principle, operation, and maintenance requirements, and leveraging its applications in different sectors, manufacturers can optimize their production processes and meet the growing demand for high - quality wire mesh products in the global market. As technology continues to advance, it is expected that further improvements will be made to the automatic wire mesh shot blasting machine, further enhancing its performance and capabilities in mass production.