Hotline
+86-136 8495 9862
Email:cennia@szmizhi.com
Add::104,Building 27,Third Industrial Zone, Longxi Community,Longgang District,Shenzhen,China.
Coil Forming & Handling Equipment
Surface Treatment Equipment
Solutions
Application
About Us
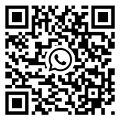
Welcome to MIZHI
For consultation/feedback, please call the service hotline: +86-136 8495 9862 Email:cennia@szmizhi.com
Bead blasting machines employ small, spherical media—such as glass beads, ceramic beads, or steel beads—to refine surface textures and achieve uniform finishes. This technique is widely used in manufacturing, metalworking, and decorative industries for tasks like deburring, surface smoothing, and creating matte or satin finishes. The spherical shape of the media ensures a consistent, non-directional blast pattern, minimizing the risk of scratches while effectively removing imperfections.
Glass bead blasting, the most common type, uses crushed or rounded glass particles. Crushed glass beads are more aggressive, suitable for removing light rust and paint, while rounded beads produce a smoother, brighter finish. This makes them ideal for preparing surfaces for painting or plating, as the slight etching improves adhesion. For example, in the aerospace industry, bead blasting is used to clean and finish turbine blades, enhancing their aerodynamic efficiency and reducing corrosion risks.
Ceramic beads offer higher hardness and durability than glass, making them suitable for heavy-duty applications on stainless steel, titanium, and other tough materials. They are often used in the medical device industry to create smooth, sterile surfaces on surgical instruments. Steel bead blasting, utilizing small steel shot, is highly aggressive and effective for descaling and prepping cast iron or steel components for coating. However, steel media can introduce contaminants like iron particles, necessitating thorough cleaning in sensitive applications.
Bead blasting machines are available in various configurations, including cabinet systems for small parts and automated conveyor systems for large-scale production. Key advantages include precise control over surface roughness (measured in Ra values), minimal material removal, and the ability to process complex geometries. However, proper maintenance is critical to prevent media contamination and ensure consistent results. For instance, worn-out beads can break down into angular fragments, altering the blasting effect.
In summary, bead blasting combines efficiency with finesse, making it an indispensable tool in industries requiring both functional and aesthetic surface treatments. Its adaptability to different media and applications ensures continued relevance in modern manufacturing and craftsmanship.