Hotline
+86-136 8495 9862
Email:cennia@szmizhi.com
Add::104,Building 27,Third Industrial Zone, Longxi Community,Longgang District,Shenzhen,China.
Coil Forming & Handling Equipment
Surface Treatment Equipment
Solutions
Application
About Us
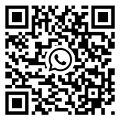
Welcome to MIZHI
For consultation/feedback, please call the service hotline: +86-136 8495 9862 Email:cennia@szmizhi.com
Blast Pro Shot Blaster Comprehensive Exploration of an Industrial Powerhouse
1. Introduction
In the vast landscape of industrial surface preparation, the Blast Pro Shot Blaster has emerged as a highly efficient and reliable solution. Surface preparation is a fundamental step in numerous industries, including manufacturing, construction, automotive, and aerospace. It involves removing contaminants, rust, paint, and other unwanted materials from surfaces to create a clean and suitable substrate for subsequent processes such as painting, coating, or bonding. The Blast Pro Shot Blaster, with its advanced technology and robust construction, has become a preferred choice for professionals seeking to achieve high quality surface finishes.
2. Working Principle of the Blast Pro Shot Blaster
2.1. Shot Acceleration Mechanism
At the heart of the Blast Pro Shot Blaster's operation is the shot acceleration mechanism. This mechanism is designed to propel abrasive shots at high velocities towards the target surface. The most common method used in these shot blasters is the centrifugal force based acceleration. A high speed impeller, driven by a powerful motor, is at the core of this process. The impeller has carefully designed vanes that catch the abrasive shots. As the impeller rotates at speeds typically ranging from 10,000 to 30,000 revolutions per minute, the shots are flung outwards due to centrifugal force. This force accelerates the shots to velocities that can reach up to 150 200 meters per second.
For example, in a Blast Pro Shot Blaster model designed for heavy duty industrial applications, the impeller is made of high strength alloy steel to withstand the intense forces generated during operation. The vanes are shaped in a way that maximizes the transfer of energy from the impeller to the shots, ensuring efficient acceleration. The motor powering the impeller is often a high torque electric motor, which can provide the necessary rotational force to achieve the desired shot velocities.
2.2. Shot Recycling and Separation System
Another crucial aspect of the Blast Pro Shot Blaster's working principle is the shot recycling and separation system. After the shots impact the target surface and remove the contaminants, they need to be recovered and reused. The shot blaster is equipped with a collection system that captures the spent shots, along with the removed debris.
This collection system typically consists of a conveyor belt or a series of ducts that lead the shots and debris to a separation unit. The separation unit uses a combination of methods to separate the reusable shots from the debris. One common method is the use of a cyclone separator. In a cyclone separator, the mixture of shots and debris is forced to spin in a circular motion. The centrifugal force causes the heavier shots to be thrown towards the walls of the cyclone and then fall into a collection bin, while the lighter debris is carried away by the air flow and exhausted.
In addition to the cyclone separator, some Blast Pro Shot Blasters may also use magnetic separation. This is particularly useful when dealing with metal shots, as the magnetic field can attract and separate the shots from non magnetic debris. The recycled shots are then fed back into the shot acceleration mechanism, ready to be reused in the blasting process. This shot recycling and separation system not only reduces the cost of abrasive media but also helps to minimize waste and environmental impact.
2.3. Control and Monitoring Systems
Modern Blast Pro Shot Blasters are equipped with advanced control and monitoring systems. These systems allow operators to precisely control the blasting process and ensure consistent results. The control system typically includes a user interface, which can be a simple control panel with buttons and dials or a more advanced touch screen interface.
Through this interface, operators can adjust parameters such as the shot flow rate, the speed of the impeller, and the blasting time. For example, if the target surface has a thick layer of paint or rust that needs to be removed, the operator can increase the shot flow rate and the impeller speed to increase the blasting intensity. On the other hand, for a more delicate surface that requires a gentler treatment, the operator can reduce these parameters.
The monitoring system, on the other hand, uses sensors to continuously monitor various aspects of the blasting process. Sensors can measure the shot flow rate, the temperature of the impeller, and the pressure in the blasting chamber. If any of these parameters deviate from the set values, the monitoring system can alert the operator and, in some cases, automatically adjust the operation of the shot blaster to prevent damage to the equipment or ensure the quality of the surface preparation.
3. Components of the Blast Pro Shot Blaster
3.1. Impeller Assembly
The impeller assembly is the most critical component of the Blast Pro Shot Blaster, as it is responsible for accelerating the shots. The impeller itself is usually made of high quality alloy steel, which is heat treated to enhance its strength and wear resistance. The vanes of the impeller are carefully designed to ensure efficient shot acceleration. They are often shaped in a way that provides a smooth transition for the shots as they are picked up and flung outwards.
The impeller is mounted on a shaft, which is connected to the motor. The shaft is supported by high quality bearings that can withstand the high speed rotation and the heavy loads generated during the shot acceleration process. In some advanced Blast Pro Shot Blaster models, the impeller assembly may also include a cooling system. This is because the high speed rotation of the impeller can generate a significant amount of heat, and if not properly cooled, it can affect the performance and lifespan of the impeller.
3.2. Shot Storage and Feeding System
The shot storage and feeding system is responsible for storing the abrasive shots and delivering them to the impeller at a controlled rate. The shot storage container, often referred to as the shot hopper, is designed to hold a sufficient quantity of shots to ensure continuous operation. The hopper is usually made of a durable material, such as steel, to withstand the abrasive nature of the shots.
The shot feeding mechanism is designed to regulate the flow of shots from the hopper to the impeller. There are different types of shot feeding mechanisms, with the most common being the gravity fed and the mechanical fed systems. In a gravity fed system, the shots flow down from the hopper to the impeller due to gravity. This type of system is simple and cost effective but may not be suitable for applications where a highly precise shot flow rate is required.
In a mechanical fed system, a device such as a screw conveyor or a vibrating feeder is used to control the shot flow rate. These mechanical devices can be adjusted to deliver a consistent and precise amount of shots to the impeller, making them ideal for applications where accuracy is crucial. The shot feeding system may also include sensors to monitor the level of shots in the hopper. When the shot level gets low, an alarm can be triggered to alert the operator to refill the hopper.
3.3. Blasting Chamber
The blasting chamber is where the actual surface preparation takes place. It is designed to contain the abrasive shots and the debris generated during the blasting process. The blasting chamber is typically made of a thick, wear resistant material, such as hardened steel or rubber lined steel. The inner walls of the chamber are often lined with replaceable wear plates to further protect the chamber from the abrasive action of the shots.
The blasting chamber has an opening through which the target surface is inserted. This opening can be designed in different ways, depending on the type of application. For example, in a shot blaster used for small scale parts, the opening may be a small door or a hatch. In a large scale industrial shot blaster, the opening may be a conveyor belt sized entrance that allows for continuous feeding of the parts to be blasted.
The blasting chamber also has an exhaust system to remove the dust and debris generated during the blasting process. The exhaust system is connected to the dust collection system, which will be discussed in the next section. The design of the blasting chamber is crucial for ensuring efficient and safe operation of the shot blaster.
3.4. Dust Collection System
The dust collection system is an essential component of the Blast Pro Shot Blaster, as it helps to maintain a clean and safe working environment. During the blasting process, a significant amount of dust is generated, which consists of the removed contaminants, such as rust, paint particles, and abrasive shot fines. This dust can be a health hazard if not properly contained and can also cause damage to the equipment.
The dust collection system typically includes a dust collector unit, which can be of different types, such as cyclonic dust collectors, bag filter dust collectors, or cartridge type dust collectors. Cyclonic dust collectors use centrifugal force to separate the dust particles from the air. The dust laden air is forced to spin in a cyclone, and the heavier dust particles are thrown towards the walls of the cyclone and then fall into a collection bin.
Bag filter dust collectors, on the other hand, use fabric bags to trap the dust particles. The dust laden air passes through the bags, and the dust is collected on the surface of the bags. Periodically, the bags are cleaned, either by shaking or by using a reverse air pulse, to remove the accumulated dust. Cartridge type dust collectors work in a similar way to bag filter dust collectors but use cylindrical cartridges instead of bags. The dust collection system is connected to the blasting chamber and the exhaust system, ensuring that the dust generated during the blasting process is effectively removed.
4. Applications of the Blast Pro Shot Blaster
4.1. Automotive Industry
In the automotive industry, the Blast Pro Shot Blaster is widely used for surface preparation of various components. Before painting or coating automotive parts, it is essential to remove any rust, paint, or contaminants from the surface to ensure proper adhesion of the coating. The shot blaster can be used to clean the surfaces of car body panels, engine blocks, and wheels.
For example, in the restoration of classic cars, the Blast Pro Shot Blaster can be used to remove layers of old paint and rust from the body panels, revealing the original metal surface. The high velocity shots can effectively remove even the most stubborn contaminants, leaving the surface clean and ready for further processing. In the production of new cars, the shot blaster can be used to prepare the surfaces of engine components, such as cylinder heads and crankshafts, for better adhesion of protective coatings.
4.2. Construction Industry
The construction industry also benefits greatly from the use of the Blast Pro Shot Blaster. In the restoration of old buildings, the shot blaster can be used to remove layers of paint, dirt, and grime from brick, stone, and concrete surfaces. This helps to restore the original appearance of the building and also prepares the surface for repainting or other finishing treatments.
For example, in the restoration of historical buildings, the Blast Pro Shot Blaster can be used to carefully remove the old paint and coatings without damaging the underlying structure. The shot blaster can also be used to clean the surfaces of steel structures, such as bridges and buildings, to prevent corrosion. By removing rust and other contaminants, the shot blaster helps to extend the lifespan of these structures.
4.3. Aerospace Industry
In the aerospace industry, surface preparation is of utmost importance to ensure the safety and performance of aircraft components. The Blast Pro Shot Blaster is used to clean and prepare the surfaces of aircraft parts, such as landing gear, engine components, and wing structures.
The high precision and consistent surface finish achieved by the shot blaster are crucial in the aerospace industry. For example, in the preparation of engine components, the shot blaster can be used to remove any oxidation or contaminants from the surface, ensuring proper fit and function of the parts. The shot blaster can also be used to create a surface texture that enhances the adhesion of coatings, which are often used to protect the components from the harsh operating conditions in the aerospace environment.
4.4. Manufacturing Industry
In the manufacturing industry, the Blast Pro Shot Blaster is used in a wide range of applications. It can be used to clean and prepare the surfaces of metal parts before assembly, to remove burrs and sharp edges, and to improve the surface finish of products.
For example, in the production of machinery parts, the shot blaster can be used to clean the surfaces of gears, shafts, and bearings. The high velocity shots can remove any machining marks or burrs, resulting in a smoother surface finish. This not only improves the appearance of the parts but also enhances their performance and lifespan. In the production of consumer products, such as appliances and furniture, the shot blaster can be used to prepare the metal surfaces for painting or coating, ensuring a durable and attractive finish.
5. Advantages of the Blast Pro Shot Blaster over Traditional Methods
5.1. Higher Efficiency
The Blast Pro Shot Blaster offers significantly higher efficiency compared to traditional surface preparation methods. The high velocity shots can quickly and effectively remove contaminants from the surface, reducing the time required for surface preparation. For example, compared to manual sanding or scraping, the shot blaster can cover a much larger surface area in a shorter period.
In a large scale industrial application, such as the surface preparation of a steel structure, a team of workers using traditional methods may take days to complete the job. However, with a Blast Pro Shot Blaster, the same job can be completed in a matter of hours. The continuous operation of the shot blaster, along with its high speed shot acceleration mechanism, allows for a more efficient and productive surface preparation process.
5.2. Better Surface Finish
The Blast Pro Shot Blaster can achieve a better surface finish compared to many traditional methods. The high velocity shots impact the surface in a uniform manner, creating a consistent surface texture. This is particularly important in applications where a smooth and even surface finish is required, such as in the automotive and aerospace industries.
For example, when preparing a surface for painting, the uniform surface finish achieved by the shot blaster ensures better adhesion of the paint. The shot blaster can also be used to create a specific surface texture, such as a slightly roughened surface, which can enhance the adhesion of coatings. In contrast, traditional methods such as hand sanding may result in an uneven surface finish, which can lead to problems such as paint peeling or poor coating adhesion.
5.3. Cost Effectiveness
In the long run, the Blast Pro Shot Blaster can be more cost effective than traditional surface preparation methods. Although the initial investment in a shot blaster may be higher compared to some basic hand held tools, the increased efficiency and reduced labor requirements can result in significant cost savings over time.
For example, by reducing the time required for surface preparation, the shot blaster can increase the productivity of a manufacturing or construction project. This can lead to faster project completion and potentially higher profits. Additionally, the shot recycling and separation system in the shot blaster reduces the cost of abrasive media, as the shots can be reused multiple times. The lower maintenance requirements of the shot blaster, compared to some complex traditional surface preparation equipment, also contribute to its cost effectiveness.
5.4. Environmentally Friendly
The Blast Pro Shot Blaster is relatively more environmentally friendly compared to some traditional surface preparation methods. For example, traditional chemical based surface cleaning methods may involve the use of harsh chemicals that can be harmful to the environment. In contrast, the shot blaster uses abrasive media, which is a non chemical alternative.
The dust collection system in the shot blaster helps to minimize the release of dust and debris into the air, reducing the environmental impact of the surface preparation process. The shot recycling and separation system also helps to reduce waste, as the reusable shots are not discarded. In addition, the use of a shot blaster can reduce the need for large amounts of water, which is often required in some traditional surface cleaning methods, such as pressure washing.
6. Maintenance and Safety Considerations for the Blast Pro Shot Blaster
6.1. Maintenance
Regular maintenance is essential to keep the Blast Pro Shot Blaster in optimal working condition. The impeller assembly, being the most critical component, requires regular inspection. The impeller vanes should be checked for signs of wear and damage. If the vanes are worn or chipped, they can affect the shot acceleration and the overall performance of the shot blaster. In such cases, the vanes may need to be repaired or replaced.
The bearings supporting the impeller shaft should also be regularly lubricated to ensure smooth rotation. The shot storage and feeding system should be inspected for any blockages or malfunctions. The hopper should be cleaned periodically to remove any accumulated debris. The dust collection system requires regular maintenance as well. The filters in the dust collector should be cleaned or replaced as needed to ensure efficient dust removal.
The control and monitoring systems should be checked regularly to ensure that they are functioning properly. Calibration of the sensors may be required from time to time to ensure accurate measurement of parameters such as shot flow rate and impeller speed. Regular maintenance not only helps to extend the lifespan of the shot blaster but also ensures consistent and high quality performance.
6.2. Safety
Safety is a top priority when operating the Blast Pro Shot Blaster. The high velocity shots can be extremely dangerous if not properly contained. Operators should always wear appropriate personal protective equipment, including safety goggles, protective clothing, and respiratory protection. The blasting chamber should be properly sealed to prevent the escape of shots and dust.
The electrical components of the shot blaster should be properly grounded to prevent electrical accidents. The shot blaster should be installed in a well ventilated area to prevent the build up of dust and fumes. The control panel should be clearly labeled, and operators should be trained on how to operate the shot blaster safely. Emergency stop buttons should be easily accessible, and operators should be familiar with the emergency procedures. Regular safety inspections should be conducted to ensure that all safety features are in working order.
7. Future Trends in Shot Blasting Technology with a Focus on the Blast Pro Shot Blaster
7.1. Automation and Robotics Integration
The future of shot blasting technology, including the Blast Pro Shot Blaster, is likely to see increased integration of automation and robotics. Automated shot blasters can be programmed to perform specific surface preparation tasks with a high degree of precision and consistency. Robotics can be used to move the shot blaster around the work area, allowing for the treatment of complex shaped surfaces.
For example, in the automotive industry, robots can be used to guide the Blast Pro Shot Blaster to clean and prepare the surfaces of car body panels. The robot can follow a pre programmed path, ensuring that all areas of the panel are evenly blasted. This not only increases the efficiency of the surface preparation process but also reduces the risk of human error. Automated systems can also be equipped with sensors to monitor the surface condition in real time and adjust the blasting parameters accordingly, further enhancing the quality of the surface preparation work.