Hotline
+86-136 8495 9862
Email:cennia@szmizhi.com
Add::104,Building 27,Third Industrial Zone, Longxi Community,Longgang District,Shenzhen,China.
Coil Forming & Handling Equipment
Surface Treatment Equipment
Solutions
Application
About Us
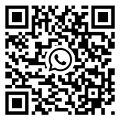
Welcome to MIZHI
For consultation/feedback, please call the service hotline: +86-136 8495 9862 Email:cennia@szmizhi.com
I. Introduction
When it comes to surface preparation equipment, Blastrac shot blasters are among the top choices in the market. These machines are renowned for their efficiency, reliability, and ability to transform various surfaces for a wide range of applications. If you are considering purchasing a Blastrac shot blaster, it is essential to understand the different aspects of these machines, including their features, available models, potential applications, and what to look for during the buying process.
II. Overview of Blastrac Shot Blasters
1.
Brand Reputation
Blastrac has established itself as a leading brand in the shot blasting industry. With years of experience and continuous innovation, they have built a reputation for producing high - quality equipment. Their shot blasters are used in numerous industries around the world, from construction and renovation to industrial manufacturing and more. The brand is known for its commitment to providing reliable and durable machines that can withstand the rigors of heavy - use applications.
2.
Working Principle
The Blastrac shot blaster operates based on the fundamental principle of shot blasting. It propels small abrasive particles, or shot, at high velocity towards a surface. This kinetic energy of the shot dislodges contaminants such as rust, paint, grease, and old coatings from the surface. At the same time, it can also modify the surface texture by removing a controlled amount of material. This prepares the surface for subsequent processes like painting, coating, or applying a new finish. The shot is typically made from materials like steel, but there are also options for other types of abrasives depending on the specific requirements of the job.
3.
Benefits of Shot Blasting with Blastrac
Shot blasting with a Blastrac machine offers several significant benefits. Firstly, it provides a more efficient alternative to traditional surface preparation methods such as manual sanding or chemical stripping. It can cover large areas in a relatively short time, reducing labor costs and project duration. Secondly, the process results in a high - quality surface finish. The controlled nature of the shot blasting ensures a uniform removal of material, leaving the surface with the right texture for better adhesion of coatings. Additionally, Blastrac shot blasters often come with features that make them environmentally friendly, such as dust collection systems that reduce air pollution and abrasive recycling capabilities that minimize waste.
III. Different Models of Blastrac Shot Blasters
1.
Hand - held Models
Hand - held Blastrac shot blasters are designed for small - scale and detailed surface preparation tasks. They are lightweight and easy to maneuver, making them ideal for working in confined spaces or on small areas. These models are often used for jobs like removing paint from small metal parts, preparing edges of larger surfaces, or working on intricate details in restoration projects. Despite their size, they still offer adjustable blasting parameters, allowing the operator to control the intensity of the shot blasting according to the surface requirements. They usually have a simple yet effective dust collection mechanism to keep the working area clean.
2.
Walk - behind Models
Walk - behind Blastrac shot blasters are more powerful and suitable for larger surface areas. These self - propelled machines are commonly used in industrial settings, construction sites, or for preparing floors in commercial buildings. They can cover significant distances while maintaining a consistent blasting action. Walk - behind models typically have a larger abrasive hopper, enabling longer operation without the need for frequent refilling. They also come with more advanced control panels that allow the operator to adjust settings such as the speed of the machine, the flow rate of the abrasive, and the velocity of the shot. The dust collection systems in these models are more robust to handle the increased dust generated during larger - scale operations.
3.
Ride - on Models
Ride - on Blastrac shot blasters are designed for very large - scale surface preparation projects. These heavy - duty machines are equipped with a seat for the operator and are capable of covering vast areas quickly. They are often used for preparing airport runways, large industrial complexes, or extensive parking lots. The ride - on design provides comfort during long - duration operations and allows for better control over the machine's movement. These models have a high - capacity abrasive delivery system and a highly efficient dust collection and filtration unit to handle the massive amount of material generated during the blasting process. They also feature advanced control systems with programmable options for precise operation and consistent surface preparation.
4.
Specialty Models
In addition to the standard models, Blastrac also offers specialty shot blasters. These are designed for specific applications or industries. For example, there may be models with extra - wide blasting heads for quickly covering large, flat surfaces. Some specialty models are built to operate in hazardous environments, such as those with explosion - proof features for use in areas with flammable gases. There are also models with specialized abrasive delivery systems for handling unique abrasives or for achieving very high - precision surface preparation in industries like electronics or medical device manufacturing.
IV. Key Features to Consider
1.
Abrasive Delivery and Recycling System
The abrasive delivery system is a crucial feature of a Blastrac shot blaster. It should be able to provide a consistent flow of abrasive to the blasting head. Look for models with adjustable flow rate controls, as this allows you to customize the intensity of the shot blasting based on the surface condition. The abrasive recycling system is also important. It not only reduces the cost of consumables but also minimizes waste. A good recycling system should be able to effectively separate the used abrasive from the debris and clean it for reuse. Check for the quality of the separation mechanism and the durability of the components involved in the recycling process.
2.
Dust Collection and Filtration
An efficient dust collection and filtration system is essential for maintaining a clean and healthy working environment. The system should be able to capture a large percentage of the dust and debris generated during the shot blasting process. Look for features such as powerful fans, high - quality filters (such as cartridge filters or bag filters), and a well - designed ducting system. The ability to easily clean or replace the filters is also an important consideration. Some models may have additional features like dust - suppression technology or the option to connect to an external dust collection unit for even better performance.
3.
Blasting Head and Nozzle Design
The design of the blasting head and nozzle directly affects the quality of the shot blasting. The blasting head should be able to distribute the abrasive shot evenly across the surface. Look for models with adjustable nozzles, which can change the angle and spread of the shot. This is particularly useful for reaching difficult - to - access areas or for achieving different surface textures. The nozzle material should be durable, as it is subjected to continuous abrasion. Some advanced nozzles may have features like ceramic inserts or other wear - resistant coatings to increase their lifespan.
4.
Control Panel and Automation
The control panel is the interface through which you will operate the Blastrac shot blaster. Look for an intuitive and user - friendly control panel that allows you to easily adjust parameters such as the speed of the machine (if applicable), the velocity of the abrasive shot, and the flow rate of the abrasive. Some models may offer more advanced automation features, such as programmable settings for different surface preparation profiles. This can be extremely useful for achieving consistent results, especially in repetitive jobs. Automation can also include features like automatic start - stop functions based on sensor inputs, which can improve the efficiency and safety of the operation.
5.
Drive System (for Mobile Models)
For walk - behind and ride - on models, the drive system is an important consideration. The drive system should provide smooth and stable movement across the surface. Look for features such as powerful motors, reliable transmission systems, and good traction. In the case of ride - on models, the comfort of the operator's seat and the ergonomics of the control layout are also relevant factors. A well - designed drive system ensures that the shot blaster can move efficiently over the surface, maintaining a consistent blasting pattern.
V. Applications of Blastrac Shot Blasters
1.
Industrial Flooring
In industrial settings, Blastrac shot blasters are widely used for preparing floors. Whether it's a concrete floor in a manufacturing plant, a warehouse, or a food processing facility, proper surface preparation is crucial. The shot blaster can remove old coatings, grease, oil, and other contaminants from the floor surface. It also levels the floor, creating a smooth and even substrate for the application of new coatings, such as epoxy or polyurethane. This improves the durability and performance of the flooring system, reducing the risk of delamination or wear.
2.
Concrete Restoration and Renovation
For concrete restoration projects, Blastrac shot blasters are invaluable. They can remove damaged or deteriorated concrete layers, exposing fresh and sound concrete. This allows for the repair of cracks, spalling, or other forms of concrete damage. The shot blaster can also be used to prepare the surface for the application of decorative concrete overlays, stains, or sealants. By creating a clean and textured surface, it enhances the adhesion of these decorative materials, resulting in a more attractive and long - lasting finish.
3.
Metal Surface Preparation
In metalworking industries, Blastrac shot blasters are used to prepare metal surfaces. This includes removing rust, paint, and scale from metal parts. The shot blasting process cleans the metal surface thoroughly, providing an ideal base for subsequent processes such as painting, plating, or welding. It improves the quality of the bond between the metal and the coating or the welded joint, enhancing the overall durability and performance of the metal structure.
4.
Shipbuilding and Marine Applications
In the shipbuilding and marine industries, Blastrac shot blasters are used for preparing the surfaces of ships, barges, and offshore structures. The equipment can remove old paint, marine growth, and corrosion from the hulls and decks. This not only improves the appearance of the vessel but also prevents further corrosion by providing a clean surface for the application of anti - corrosive coatings. The ability to work in marine environments, including dealing with saltwater - related issues, makes the Blastrac shot blaster an essential tool in this industry.
5.
Bridge and Infrastructure Maintenance
Bridges and other infrastructure elements require regular maintenance, and Blastrac shot blasters play a significant role in this process. They can be used to remove old paint and corrosion from bridge girders, decks, and support structures. The surface preparation achieved by the shot blaster ensures the effectiveness of new protective coatings, extending the lifespan of the infrastructure. In addition, the shot blaster can be used to prepare surfaces for repairs, such as filling cracks or replacing damaged sections of concrete or metal.
VI. Buying Considerations
1.
Project Requirements
Before purchasing a Blastrac shot blaster, carefully consider your project requirements. Determine the size and nature of the surfaces you will be working on. If you are mainly dealing with small - scale or detailed jobs, a hand - held model might be sufficient. For larger areas, such as industrial floors or construction sites, a walk - behind or ride - on model would be more appropriate. Also, consider the types of surfaces you will be preparing (e.g., concrete, metal, or a combination) and the level of contamination or damage. This will help you choose the right model with the appropriate power and features for your specific needs.
2.
Budget
Set a budget for your purchase. Blastrac shot blasters come in a range of prices, depending on the model and its features. While it's tempting to go for the cheapest option, keep in mind that investing in a higher - quality machine with better features may save you money in the long run. Consider the cost not only of the initial purchase but also of consumables (such as abrasives), maintenance, and potential repairs. A more expensive model with an efficient abrasive recycling system and durable components may have a lower overall cost of ownership over time.
3.
After - sales Support
Check the availability of after - sales support. This includes things like technical assistance, spare parts availability, and warranty options. A reliable manufacturer or dealer should be able to provide you with prompt technical support in case you encounter any issues with your shot blaster. Easy access to spare parts is also crucial, as it minimizes downtime in the event of a component failure. Look for manufacturers with a good reputation for customer service and a wide network of service centers or authorized dealers.
4.
Training and Operator Requirements
Consider the training and operator requirements for the Blastrac shot blaster. Some models may be more complex to operate than others, especially those with advanced automation features. Ensure that your operators will be able to use the machine safely and effectively. Look for training options provided by the manufacturer or dealer, such as on - site training or online tutorials. Additionally, consider any safety regulations or certifications that may be required for operating the shot blaster in your area.
5.
Comparative Analysis with Competitors
It's a good idea to conduct a comparative analysis with other shot blaster brands on the market. Look at the features, performance, and price of similar models from different manufacturers. This will help you determine if the Blastrac shot blaster offers the best value for your money. Consider factors such as the quality of construction, the reputation of the brand, and customer reviews. While Blastrac has a strong reputation, it's still important to make an informed decision based on a comprehensive comparison.
VII. Maintenance and Care
1.
Regular Cleaning
Regular cleaning of the Blastrac shot blaster is essential for its proper operation. After each use, clean the abrasive hopper to remove any debris or clumped - up abrasives. The blasting head and nozzles should be inspected and cleaned to ensure they are free from blockages. The dust collection and filtration system should be emptied and the filters cleaned or replaced as needed. This helps to maintain the efficiency of the machine and prevent damage to the components.
2.
Abrasive Inspection and Replacement
Periodically check the quality of the abrasive. Over time, the abrasive may become worn, rounded, or contaminated. Worn - out abrasive can lead to poor surface preparation results. If the abrasive is in poor condition, replace it. Also, make sure the abrasive delivery system is working properly, and there are no issues with the flow of the abrasive.
3.
Component Inspection
Regularly inspect the various components of the shot blaster, including the motors, drive systems (if applicable), bearings, and other moving parts. Look for signs of wear, such as excessive vibration, unusual noises, or visible damage. Lubricate the moving parts as per the manufacturer's instructions to ensure smooth operation. Any damaged components should be replaced promptly to avoid further problems.
4.
Calibration and Testing
Periodically calibrate the Blastrac shot blaster to ensure that it is operating at the correct settings. This includes checking and adjusting the abrasive flow rate, the velocity of the shot, and other relevant parameters. Test the machine on a sample surface to verify that the shot blasting is performing as expected. Calibration and testing should be carried out by trained personnel using the appropriate tools.
Purchasing a Blastrac shot blaster for sale can be a significant investment, but it can also bring great rewards in terms of efficient and high - quality surface preparation. By understanding the different models, features, applications, buying considerations, and maintenance requirements, you can make an informed decision that meets your specific needs. Whether you are in the construction, industrial, marine, or any other relevant industry, a well - chosen Blastrac shot blaster can be a valuable asset for your surface preparation tasks.