Hotline
+86-136 8495 9862
Email:cennia@szmizhi.com
Add::104,Building 27,Third Industrial Zone, Longxi Community,Longgang District,Shenzhen,China.
Coil Forming & Handling Equipment
Surface Treatment Equipment
Solutions
Application
About Us
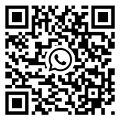
Welcome to MIZHI
For consultation/feedback, please call the service hotline: +86-136 8495 9862 Email:cennia@szmizhi.com
1. Introduction
In the vast realm of metal processing industries, the coil cut to length machine stands as a cornerstone piece of equipment. Its primary function is to transform large - scale metal coils into precisely sized flat sheets, which are then used as raw materials in a plethora of downstream manufacturing processes. This transformation is not only about size reduction but also about meeting the exact dimensional requirements demanded by various industries, from automotive manufacturing to construction and beyond. The coil cut to length machine has evolved significantly over the years, integrating advanced technologies to enhance precision, efficiency, and versatility.
2. Components of a Coil Cut to Length Machine
2.1 Uncoiler
The uncoiler is the starting point of the coil - processing journey. It serves as the holder for the metal coil, which can vary in size, weight, and material composition. There are different types of uncoilers available in the market. One common type is the hydraulic expandable mandrel uncoiler. This design allows for easy loading and unloading of coils with different inner diameters. The hydraulic system enables the mandrel to expand and firmly grip the inner core of the coil, ensuring a stable and controlled unwinding process. Electrically - driven uncoilers are also prevalent, offering precise speed control. They are often equipped with tension - control mechanisms to prevent the metal strip from getting slack or over - tightened during unwinding. A well - functioning uncoiler is crucial as any irregularity in the unwinding process can lead to downstream problems such as misalignment in the leveling and cutting operations.
2.2 Leveler
After the metal strip is unwound from the coil, it typically has some inherent curvature and unevenness due to the coiling process. The leveler is tasked with straightening the strip. It consists of multiple rolls arranged in a specific pattern. The number of rolls can range from 7 to 21 or more, depending on the thickness and material properties of the metal. For example, for thin - gauge aluminum strips, a 9 - roll leveler might be sufficient, while thick - gauge steel strips may require a 21 - roll leveler. The rolls apply a combination of bending and stretching forces to the metal strip. As the strip passes through the leveler, the rolls gradually correct the shape, eliminating any waves, curls, or bowing. Some advanced levelers are equipped with adjustable roll - gap mechanisms, allowing operators to fine - tune the leveling process according to the specific requirements of the metal strip.
2.3 Measuring and Feeding System
Accurate measurement and feeding of the metal strip are essential for achieving the desired cut lengths. The measuring system usually employs encoder - based technology. Encoders are devices that translate the linear movement of the metal strip into electrical signals, which can be precisely measured and counted. This information is then fed into the machine's control system, which calculates the length of the strip as it moves. The feeding system, on the other hand, is responsible for moving the metal strip forward at a consistent speed. It can be a set of powered rolls or a servo - driven system. Servo - driven feeding systems offer higher precision and faster response times, enabling the machine to quickly adjust the feeding speed based on the programmed cut lengths.
2.4 Cutting Unit
The cutting unit is the most critical component of the coil cut to length machine as it is where the actual cutting of the metal strip into individual sheets takes place. There are two main cutting methods: mechanical shearing and laser cutting.
- Mechanical Shearing: This is the more traditional and widely used method. It involves the use of sharp blades to shear the metal strip. The blades are typically made of high - quality tool steel and are designed to withstand the high forces generated during the cutting process. Mechanical shearing can be further classified into different types, such as guillotine shearing and rotary shearing. Guillotine shearing is suitable for straight - line cuts and is often used for thicker metal sheets. The cutting action is similar to that of a large pair of scissors, with one stationary blade and one moving blade. Rotary shearing, on the other hand, uses rotating blades and is more suitable for high - speed cutting of thinner metal strips.
- Laser Cutting: Laser - cutting technology has gained popularity in recent years, especially for applications that require high - precision cuts and intricate shapes. In a laser - cutting - equipped coil cut to length machine, a high - energy laser beam is focused on the metal strip. The laser beam heats the metal to its melting or vaporization point, effectively cutting through the material. Laser cutting offers several advantages over mechanical shearing, such as extremely narrow kerf widths (the width of the cut), minimal heat - affected zones, and the ability to cut complex shapes without the need for expensive tooling. However, it also has some drawbacks, including higher equipment costs and lower cutting speeds for thick - gauge materials.
2.5 Stacker
Once the metal sheets are cut to the desired lengths, they need to be neatly stacked for further processing or storage. The stacker is responsible for this task. It can be a simple manual - assisted stacker or a fully automated robotic stacker. Automated stackers are equipped with sensors and actuators that can detect the position of the cut sheets and stack them in a precise and organized manner. Some stackers are designed to handle different sheet sizes and weights, and they can adjust the stacking height and pattern accordingly. The proper functioning of the stacker is important as it ensures that the cut sheets are not damaged during the stacking process and are ready for easy transportation and handling.
3. Working Principle
The operation of a coil cut to length machine is a highly coordinated and sequential process.
1. Unwinding Phase: The metal coil is first loaded onto the uncoiler. The uncoiler's mandrel is expanded to grip the inner core of the coil securely. The control system then starts the unwinding process, gradually releasing the metal strip from the coil. The tension of the strip is carefully monitored and adjusted to ensure a smooth unwinding operation.
2. Leveling Phase: As the unwound metal strip enters the leveler, the rolls begin to work on straightening it. The strip passes through the series of rolls, which apply the necessary bending and stretching forces. The operator can adjust the roll - gap settings based on the thickness and material of the strip to achieve the best leveling results.
3. Measuring and Feeding Phase: While the strip is being leveled, it also passes through the measuring and feeding system. The encoder in the measuring system continuously measures the length of the strip as it moves forward. The feeding system, based on the programmed cut lengths, moves the strip at a consistent speed towards the cutting unit.
4. Cutting Phase: When the measured length of the strip reaches the programmed value, the cutting unit is activated. In the case of mechanical shearing, the blades close rapidly to cut the strip. For laser cutting, the laser beam is fired, melting and vaporizing the metal to create the cut.
5. Stacking Phase: After cutting, the individual metal sheets are conveyed to the stacker. The stacker arranges the sheets in a stack, either in a simple layer - by - layer pattern or in a more complex pattern depending on the requirements.
4. Applications
4.1 Automotive Industry
In the automotive manufacturing sector, the coil cut to length machine plays a vital role. The body panels of cars, such as the hood, roof, doors, and fenders, are made from precisely cut metal sheets. These sheets need to be of the exact size and shape to ensure a perfect fit during the assembly process. The high - precision cuts provided by the coil cut to length machine contribute to the overall structural integrity and aesthetic appeal of the vehicle. For example, the door panels need to be cut with such accuracy that they can be easily welded to the body frame and have proper alignment with the door hinges and locks. Additionally, the use of advanced coil cut to length machines allows automotive manufacturers to produce a large volume of parts in a short period, meeting the high - demand requirements of the industry.
4.2 Construction Industry
The construction industry is another major consumer of metal sheets produced by coil cut to length machines. Metal sheets are used for roofing, siding, and structural components. In roofing applications, the metal sheets need to be cut to specific lengths to fit the dimensions of the building's roof. The coil cut to length machine can produce these sheets with the required precision, reducing waste and ensuring a proper fit. For siding, the sheets may need to be cut with specific profiles or patterns to enhance the building's appearance. In structural components, such as steel beams and columns made from sheet - formed sections, the accurate cutting of the metal sheets is crucial for the overall strength and stability of the structure.
4.3 Appliance Manufacturing
Home appliances like refrigerators, washing machines, and stoves rely on metal sheets for their outer casings and internal components. The coil cut to length machine is used to produce these sheets with the exact dimensions needed. For example, the outer cabinet of a refrigerator requires metal sheets that are cut to fit around the insulation, doors, and shelves. The precise cutting ensures a seamless and aesthetically pleasing finish. In the case of washing machines, the metal sheets for the drum and the outer body need to be cut accurately to ensure proper functioning and durability.
4.4 Packaging Industry
In the packaging industry, metal sheets are used to produce cans, containers, and closures. The coil cut to length machine is used to cut the metal sheets into the appropriate sizes for further forming processes. For example, the sheets for making beverage cans need to be cut with high precision to ensure that they can be easily formed into the cylindrical shape and have proper seams and closures. The accurate cutting also helps in reducing material waste and improving the overall production efficiency of the packaging industry.
5. Advantages
5.1 High Precision
One of the most significant advantages of the coil cut to length machine is its ability to achieve high - precision cuts. The advanced control systems, measuring devices, and cutting technologies enable the machine to cut metal sheets with very tight tolerances. In industries where a perfect fit of components is crucial, such as aerospace and electronics, this precision is essential. For example, in the production of electronic enclosures, the metal sheets need to be cut with an accuracy of within a few millimeters to ensure proper fitting of the internal components. The high - precision cuts also contribute to the overall quality and reliability of the end - products.
5.2 High Efficiency
Coil cut to length machines are designed for continuous operation. They can process metal coils at a relatively high speed, reducing the production time per unit of metal sheet. The automated nature of the process, from unwinding to stacking, minimizes the need for manual intervention. This not only increases productivity but also reduces labor costs. For example, in a large - scale automotive manufacturing plant, a high - speed coil cut to length machine can produce hundreds of body panels per hour, meeting the high - volume production requirements of the assembly line.
5.3 Material Savings
By cutting the metal sheets to the exact required lengths, the coil cut to length machine helps in reducing material waste. In traditional manual cutting methods, there is often a significant amount of excess material due to inaccurate measurements and cutting. With the precise cutting capabilities of the coil cut to length machine, manufacturers can optimize the use of metal coils, resulting in cost savings. This is especially important considering the high cost of metal materials, and it also contributes to a more sustainable manufacturing process.
5.4 Versatility
These machines are highly versatile and can handle a wide range of metal materials, including steel, aluminum, copper, and various alloys. They can also process metal strips of different thicknesses and widths. Additionally, with the option of different cutting methods (mechanical shearing and laser cutting), the coil cut to length machine can be adapted to different application requirements. For example, it can be used to produce both large - scale structural components from thick - gauge steel and small - scale precision parts from thin - gauge aluminum.
6. Challenges
6.1 High Initial Investment
The purchase and installation of a coil cut to length machine can be a substantial capital investment. The cost of the machine itself can range from tens of thousands to several million dollars, depending on its size, capabilities, and the cutting technology it incorporates. In addition to the machine cost, there are also expenses associated with infrastructure development, such as a suitable workshop space with proper ventilation (especially for laser - cutting machines), electrical systems to power the equipment, and safety measures. Small and medium - sized enterprises may find it difficult to afford such high - cost equipment, which can limit their growth and competitiveness in the market.
6.2 Maintenance and Calibration
To ensure the continued high - precision operation of the coil cut to length machine, regular maintenance and calibration are essential. The cutting blades in mechanical shearing units need to be sharpened or replaced regularly to maintain their cutting performance. The rolls in the leveler and the feeding system also require periodic inspection and maintenance to ensure smooth operation. In the case of laser - cutting machines, the laser source, optics, and cooling systems need to be carefully maintained. Calibration of the measuring and control systems is also crucial to ensure accurate length measurements and cutting operations. Any deviation in calibration can lead to inaccurate cuts and reduced product quality.
6.3 Skilled Labor Requirement
Operating and maintaining a coil cut to length machine requires a certain level of technical expertise. Workers need to be trained in setting up the machine, programming the cut lengths, adjusting the tension and roll - gap settings, and troubleshooting any issues that may arise during operation. The shortage of skilled labor in some regions can pose a challenge to the efficient use of these machines. Employers may need to invest in training programs or hire experienced technicians, which can add to the overall operational costs.
6.4 Technological Obsolescence
The field of metal - processing technology is constantly evolving. New and more advanced coil cut to length machines are being developed regularly, incorporating the latest control systems, cutting technologies, and material - handling capabilities. Older machines may become technologically obsolete, requiring manufacturers to upgrade or replace them to remain competitive. This not only involves significant financial investment but also disrupts the production process during the transition period.
7. Future Trends
7.1 Integration of Industry 4.0 Technologies
The future of coil cut to length machines lies in the integration of Industry 4.0 technologies, such as the Internet of Things (IoT), artificial intelligence (AI), and machine learning (ML). IoT sensors can be installed on the machine to monitor various parameters, such as temperature, vibration, and cutting forces, in real - time. This data can be transmitted to a central control system, where AI and ML algorithms can analyze it to predict equipment failures, optimize cutting parameters, and improve overall efficiency. For example, AI can adjust the cutting speed and power based on the real - time condition of the metal strip and the cutting tool, reducing the risk of tool wear and improving the quality of the cuts.
7.2 Development of Hybrid Cutting Technologies
There is a growing trend towards the development of hybrid cutting technologies that combine the advantages of different cutting methods. For example, a combination of mechanical shearing and laser - assisted cutting may be developed. In this hybrid system, the mechanical shearing can be used for the initial rough cutting, and the laser - assisted cutting can be used for fine - tuning the edges and achieving higher precision. This approach can potentially improve the cutting speed, quality, and cost - effectiveness of the coil cut to length machine.
7.3 Adaptation to New Materials
As new types of metal alloys and composite materials are being developed, coil cut to length machines will need to be adapted to handle these materials. This may require the development of new cutting tools, leveler designs, and control algorithms. For example, advanced composite materials with high - strength - to - weight ratios are being increasingly used in the aerospace and automotive industries. Coil cut to length machines will need to be able to process these materials with the same level of precision and efficiency as traditional metals.
In conclusion, the coil cut to length machine is an indispensable piece of equipment in the metal - processing industry. Its components, working principle, wide - ranging applications, numerous advantages, and the challenges it faces all contribute to its significance in modern manufacturing. With the advent of new technologies and the evolving demands of various industries, the coil cut to length machine is set to undergo further advancements, playing an even more crucial role in the future of metal manufacturing.