Hotline
+86-136 8495 9862
Email:cennia@szmizhi.com
Add::104,Building 27,Third Industrial Zone, Longxi Community,Longgang District,Shenzhen,China.
Coil Forming & Handling Equipment
Surface Treatment Equipment
Solutions
Application
About Us
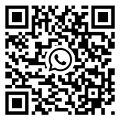
Welcome to MIZHI
For consultation/feedback, please call the service hotline: +86-136 8495 9862 Email:cennia@szmizhi.com
In the world of metal fabrication and manufacturing, coil slitting equipment plays a crucial role in transforming large coils of metal into narrower strips with precision and efficiency. This advanced machinery is designed to handle a wide range of metal materials, including steel, aluminum, copper, and stainless steel, and is used in various industries such as automotive, construction, appliance manufacturing, and more.
The coil slitting process begins with the unwinding of a large coil of metal. The coil is then fed through a series of rollers and guides to ensure smooth and stable movement. As the coil passes through the slitting section, it is cut into narrower strips by a set of circular knives or blades. The width of the strips can be adjusted by changing the spacing between the blades or by using different sets of blades.
One of the key features of coil slitting equipment is its precision. The machinery is designed to cut the metal coils with extremely tight tolerances, ensuring that the resulting strips are of consistent width and thickness. This precision is achieved through the use of advanced cutting technology, such as high-speed circular knives or blades, and precise control systems that monitor and adjust the cutting process in real-time.
Another important aspect of coil slitting equipment is its efficiency. The machinery is capable of processing large coils of metal quickly and efficiently, reducing production time and increasing output. This efficiency is achieved through the use of automated feeding and cutting systems, as well as advanced control systems that optimize the cutting process and minimize downtime.
In addition to precision and efficiency, coil slitting equipment also offers a high level of versatility. The machinery can be configured to handle different types of metal materials, thicknesses, and widths, making it suitable for a wide range of applications. Additionally, some coil slitting equipment can be equipped with additional features such as edge trimming, perforating, and embossing, further expanding its capabilities.
The design and construction of coil slitting equipment are also critical factors to consider. The machinery must be robust and reliable, able to withstand the rigors of continuous operation in a demanding industrial environment. It should be made from high-quality materials and components to ensure long service life and minimal maintenance requirements.
Safety is also a top priority when it comes to coil slitting equipment. The machinery should be equipped with comprehensive safety features such as guards, emergency stop buttons, and safety interlocks to protect operators from potential hazards. Additionally, proper training and safety procedures should be in place to ensure the safe operation of the equipment.
When choosing coil slitting equipment, it is important to consider the specific needs of your business. This includes factors such as the types and thicknesses of metal materials you will be processing, the required strip widths and lengths, and your production volume. You should also consider the reputation and experience of the manufacturer, as well as the quality of their after-sales support.
In conclusion, coil slitting equipment is an essential tool for metal fabrication and manufacturing. Its precision, efficiency, versatility, and safety features make it a valuable asset for businesses in various industries. By choosing the right coil slitting equipment and working with a reputable manufacturer, you can improve your production processes, increase output, and enhance the quality of your products.
Used Steel Slitters for Sale
I. Introduction
Used steel slitters present an attractive option for businesses in the steel processing industry, especially those looking to expand their production capabilities or replace existing equipment at a more affordable cost. These machines have a significant role in transforming large steel coils into narrower strips, which are then used in various applications such as construction, automotive manufacturing, and metal fabrication. However, purchasing a used steel slitter requires careful consideration of multiple factors to ensure that the machine meets the specific requirements of the buyer.
II. Types of Used Steel Slitters Available
1. Roll - slitting Steel Slitters
Roll - slitting steel slitters are among the most common types found in the used market. These machines use circular knives mounted on shafts to cut the steel coil. The knives rotate as the steel passes through, and the number and position of the knives can be adjusted to achieve different slit widths. When considering a used roll - slitting steel slitter, it's crucial to examine the condition of the knives. Signs of wear, such as nicks, dull edges, or uneven wear patterns, can affect the quality of the cuts. The shafts holding the knives should also be inspected for straightness and proper alignment. If the shafts are bent or misaligned, it can lead to vibrations during operation, resulting in poor - quality slitting and potential damage to the machine. Additionally, the rollers used for guiding and feeding the steel coil need to be in good condition. They should rotate smoothly and have a consistent surface to ensure the steel moves evenly through the slitting process.
2. Shear - slitting Steel Slitters
Shear - slitting steel slitters utilize a shearing action with straight blades to cut the steel. These machines are often preferred for thicker steel coils or when a more precise cut is required. When evaluating a used shear - slitting steel slitter, the quality and sharpness of the blades are of utmost importance. Blades that are dull or damaged will not be able to make clean cuts and may cause burrs or deformations in the slit steel strips. The hydraulic or mechanical system that powers the shearing action also needs to be thoroughly checked. Any leaks in the hydraulic system or problems with the mechanical actuators can lead to inconsistent cutting force and poor performance. The alignment of the blades and the backup anvils is another critical factor. Proper alignment ensures that the shearing force is evenly distributed, resulting in accurate cuts.
3. Laser - slitting Steel Slitters
Although less common in the used steel slitter market, laser - slitting machines offer high - precision cutting. These machines use a high - power laser beam to melt or vaporize the steel along the desired cutting path. When considering a used laser - slitting steel slitter, the condition of the laser source is a primary concern. The laser's power output may have decreased over time, affecting the cutting speed and quality. The focusing optics need to be inspected for any scratches, dirt, or damage that could cause the laser beam to be misaligned or diffused. The control system for the laser, including the software and associated electronics, must also be evaluated. An outdated or malfunctioning control system can lead to errors in setting the cutting parameters and ultimately result in sub - standard cuts.
III. Factors Affecting the Price of Used Steel Slitters
1. Age and Usage History
The age of the steel slitter is an obvious factor influencing its price. Older machines are generally less expensive, but their usage history within that age range is equally important. A machine that has been used intensively for many years will likely show more signs of wear and tear compared to one that has seen less use. For example, a 10 - year - old steel slitter that was in operation for 8 hours a day, 5 days a week, will have more wear on its components than a similar - aged machine that was only used for 4 hours a day, 3 days a week. The type of steel processed during its usage history also matters. If the machine was used to slit thick and high - strength steel coils, the components may have endured more stress, reducing the machine's value. Information about previous maintenance records can provide valuable insights into the machine's condition and potential lifespan.
2. Condition of Key Components
Cutting Tools: As mentioned earlier, the condition of the cutting tools significantly impacts the price. In roll - slitting machines, the cost of replacing circular knives can be substantial, so if the existing knives are in poor condition, the price of the used slitter should reflect this. Similarly, in shear - slitting machines, the cost of new blades and any necessary adjustments to the blade - holding system need to be considered. In laser - slitting machines, the expense of repairing or replacing the laser source or optics can be high, affecting the overall value of the used equipment.
Mechanical Structure: The frame, rollers, shafts, and other mechanical parts of the steel slitter must be inspected for any signs of damage. Cracks in the frame, bent rollers, or misaligned shafts can reduce the machine's functionality and safety. A machine with a damaged mechanical structure may require extensive repairs or even replacement of parts, which should be factored into the price. The condition of the bearings and other moving parts also affects the machine's smooth operation. Worn - out bearings can cause vibrations and additional wear on other components.
Control System: The control system of a used steel slitter can range from simple mechanical controls to advanced computer - based systems. An outdated or malfunctioning control system can limit the machine's usability. If the control system is not able to accurately control the slitting process, such as setting the correct cutting speed, slit width, or tension control, the machine's value will be lower. Upgrading or repairing the control system can be costly, so the current state of the control system is an important consideration when pricing the used slitter.
3. Brand and Reputation
The brand of the steel slitter plays a significant role in determining its price in the used market. Well - known and reputable brands are often associated with better - quality components, more reliable performance, and better - supported after - sales service. Even in the used condition, machines from established brands may command a higher price. For example, a used steel slitter from a leading international brand may have been built with higher - quality materials and more precise manufacturing tolerances compared to a machine from an unknown or less - reputable brand. Buyers may be willing to pay more for a used slitter from a trusted brand because they have more confidence in its durability and performance, even with some wear and tear.
IV. Inspection and Evaluation of Used Steel Slitters
1. Mechanical Inspection
Overall Structure: A detailed inspection of the machine's structure should start with checking for any visible signs of damage to the frame. Welds should be examined for cracks, and the overall integrity of the structure should be verified. The machine should be level and stable, and any signs of deformation or misalignment should be noted. The connection points between different components, such as the attachment of rollers to the frame or the mounting of the cutting unit, should be inspected for tightness and proper alignment.
Rollers and Guides: The rollers used for guiding and feeding the steel coil are crucial for the slitting process. Their surfaces should be inspected for wear, scratches, or pitting. Any irregularities on the roller surfaces can affect the smooth movement of the steel and lead to poor - quality cuts. The rollers should rotate freely without any binding or excessive friction. The guides that direct the steel towards the cutting area should be in good condition and properly aligned. Misaligned guides can cause the steel to deviate from its intended path, resulting in inaccurate slitting.
Cutting Mechanism: For roll - slitting machines, the circular knives need to be carefully examined. The sharpness of the knives, as well as any signs of wear or damage on the cutting edges, should be evaluated. The clearance between the knives and the backup rollers should be within the manufacturer's specified range. In shear - slitting machines, the straight blades should be inspected for sharpness, straightness, and any signs of chipping or cracking. The alignment of the blades with the anvils and the condition of the blade - actuating mechanism, whether hydraulic or mechanical, are critical. In laser - slitting machines, the laser - generating unit, focusing optics, and beam - delivery system should be thoroughly inspected as described earlier.
2. Electrical and Control System Inspection
Electrical Components: The electrical components of the used steel slitter, including motors, sensors, and wiring, should be checked for proper functioning. Motors should be tested for their speed, torque, and any abnormal noises during operation. The power supply connections should be secure, and the electrical insulation should be in good condition to prevent any electrical hazards. Sensors, such as those for measuring steel coil tension, position, or speed, should be calibrated and verified for accuracy. Any faulty sensors can lead to incorrect operation of the machine.
Control System: The control system should be evaluated for its functionality and ease of use. The control panel should be inspected for any damaged buttons, switches, or displays. The software or programming of the control system should be examined to ensure that it can be understood and modified if necessary. The ability of the control system to communicate with different components of the machine, such as the motors and sensors, should be tested. If the control system is unable to provide accurate control over the slitting process, it may need to be repaired or upgraded, which can add to the cost of the used machine.
3. Performance Testing
Coil Loading and Unwinding: The ability of the used steel slitter to handle and unwind a steel coil should be tested. The coil should be loaded onto the machine smoothly, and the unwinding process should be stable. The tension control during unwinding should be monitored to ensure that the steel is fed at a consistent tension. Any issues with coil loading or unwinding, such as difficulty in starting or stopping the coil, or inconsistent tension, can indicate problems with the machine's mechanical or control systems.
Slitting Operation: A performance test of the slitting operation should be conducted using a sample steel coil. The quality of the cuts should be inspected for straight edges, consistent widths, and minimal burrs. The cutting speed and accuracy should be within the acceptable range for the type of machine. The machine should be able to maintain stable operation during the slitting process without excessive vibrations or other signs of malfunction. If possible, different thicknesses of steel coils should be tested to evaluate the machine's versatility.
V. Advantages and Disadvantages of Buying Used Steel Slitters
1. Advantages
Cost - savings: The most significant advantage of purchasing a used steel slitter is the potential for cost - savings. Used machines are typically much less expensive than new ones, making them an attractive option for small and medium - sized businesses with limited capital. This allows these businesses to acquire the necessary equipment to enter or expand their steel slitting operations without incurring a large financial burden. For example, a new high - end steel slitter may cost several hundred thousand dollars, while a used but still functional one of a similar type could be available for a fraction of that price, depending on its age, condition, and other factors.
Immediate Availability: Used steel slitters are usually available for immediate purchase and delivery. This can be a crucial advantage for businesses that need to quickly increase their production capacity or replace a malfunctioning machine. Unlike new equipment, which may have a lead - time for manufacturing and delivery, a used slitter can be put into operation relatively quickly, minimizing downtime and allowing for a faster return to production.
Suitable for Specific Applications: There may be used steel slitters available that are particularly well - suited for certain types of steel processing applications. For example, a machine that was previously used in a construction - related steel processing facility may be optimized for slitting thick steel coils used in building materials. This can provide better performance for businesses with similar requirements compared to a general - purpose new machine that may need additional customization.
2. Disadvantages
Wear and Tear: The main drawback of used steel slitters is the potential for wear and tear on the components. Cutting tools, rollers, mechanical parts, and electrical systems may have already undergone significant use, which can lead to more frequent breakdowns and maintenance requirements. The cost of repairing or replacing these worn - out components should be carefully considered when evaluating the purchase of a used slitter. For instance, if the circular knives on a roll - slitting machine need to be replaced soon after purchase, it can add a significant amount to the overall cost of the machine.
Lack of Warranty and Support: Unlike new machines, used steel slitters usually come with limited or no warranty. This means that if any problems arise with the machine after purchase, the buyer may have to bear the full cost of repairs. Additionally, getting technical support for older or less - common models can be challenging. Manufacturers may no longer provide support for these machines, and finding replacement parts can be difficult and expensive. This lack of warranty and support can be a significant risk for the buyer.
Outdated Technology: Used steel slitters may be based on older technology, which could limit their performance and efficiency. They may not have the latest features such as advanced control systems, improved cutting techniques, or energy - efficient components. This could result in lower productivity and higher operating costs in the long run compared to newer machines. For example, an older used steel slitter may not be able to adjust cutting parameters as precisely as a new machine, leading to less accurate cuts and more material waste.
VI. Conclusion
Used steel slitters for sale can be a viable option for businesses in the steel processing industry, but they require careful evaluation. The type of slitter, its age, condition of components, brand, and performance all need to be thoroughly inspected before making a purchase decision. While the cost - savings and immediate availability of used machines can be attractive, the potential risks associated with wear and tear, lack of warranty and support, and outdated technology must be weighed carefully. By conducting a comprehensive assessment, buyers can make an informed decision and potentially acquire a used steel slitter that meets their production needs and provides value for money.