Hotline
+86-136 8495 9862
Email:cennia@szmizhi.com
Add::104,Building 27,Third Industrial Zone, Longxi Community,Longgang District,Shenzhen,China.
Coil Forming & Handling Equipment
Surface Treatment Equipment
Solutions
Application
About Us
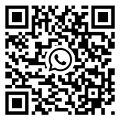
Welcome to MIZHI
For consultation/feedback, please call the service hotline: +86-136 8495 9862 Email:cennia@szmizhi.com
I. Introduction
Coil slitting lines play a crucial role in various industries by converting wide coils of materials, such as metal (steel, aluminum, etc.), plastic, or paper, into narrower coils or strips. The manufacturers of coil slitting lines are key players in providing the necessary equipment for this important process. These manufacturers are responsible for designing, engineering, and producing high - quality coil slitting lines that meet the diverse needs of different industries.
II. Key Manufacturers in the Global Market
1. Bradbury Group
- Bradbury Group is a well - known manufacturer in the coil slitting line industry. With a long - standing reputation, they offer a wide range of coil slitting solutions. Their machines are known for their precision and reliability. Bradbury Group invests heavily in research and development to continuously improve their products. For example, they have developed advanced slitting technology that can handle different thicknesses of materials with high accuracy. Their coil slitting lines are often equipped with state - of - the - art control systems. These control systems, typically based on Programmable Logic Controllers (PLCs), allow for precise control of the slitting process, including the speed of the uncoiling, slitting, and recoiling operations. The Bradbury Group also provides excellent customer service. They offer installation support, training for operators, and after - sales maintenance services. This comprehensive approach ensures that their customers can operate the coil slitting lines efficiently and with minimal downtime.
2. FIMI - Italy
- FIMI is an Italian manufacturer that has made a name for itself in the coil slitting line market. Their machines are renowned for their high - quality construction and innovative design. FIMI focuses on customization to meet the specific requirements of different customers. They understand that each industry and even each individual customer may have unique needs when it comes to coil slitting. For instance, in the automotive industry, the precision requirements for slitting metal coils used in car body parts are extremely high. FIMI can customize their coil slitting lines to achieve the necessary accuracy levels. Their machines also incorporate advanced safety features. In a coil slitting line, there are many moving parts and potentially dangerous operations, such as the slitting blades. FIMI's safety features include guards around the slitting area, emergency stop buttons, and safety interlocks. This not only protects the operators but also ensures the long - term reliability of the equipment by preventing accidental damage.
3. Red Bud Industries - USA
- Red Bud Industries is a leading American manufacturer of coil slitting lines. They have a strong presence in the North American market and are also expanding globally. One of the key strengths of Red Bud Industries is their ability to produce high - throughput coil slitting lines. These lines are designed to handle large volumes of coils efficiently. They use high - quality components in their machines, such as heavy - duty motors for the uncoiling and recoiling processes. This ensures that the machines can operate continuously for long periods without overheating or experiencing mechanical failures. Red Bud Industries also offers energy - efficient solutions. In today's environment - conscious manufacturing world, reducing energy consumption is crucial. Their coil slitting lines are engineered to minimize energy usage while maintaining high - performance levels. For example, they may use variable - speed drives to optimize the power consumption of the motors based on the actual load of the operation.
III. Design and Engineering Aspects of Coil Slitting Lines by Manufacturers
1. Uncoiling Section
- In the design of the uncoiling section, manufacturers focus on several key factors. The ability to handle different coil sizes and weights is essential. A well - designed uncoiling section should be adjustable to accommodate coils with varying diameters and widths. Manufacturers use mandrels of different sizes or adjustable cradles to hold the coils. For example, for large - diameter and heavy - weight coils, a robust mandrel with a high load - bearing capacity is required. The uncoiling section also needs proper braking mechanisms. These brakes are crucial for controlling the unwinding speed of the coil. If the braking is too weak, the coil may unwind too quickly, leading to material slack and potential damage. On the other hand, if the braking is too strong, it can cause excessive tension on the material, which may result in stretching or tearing. Manufacturers often use servo - controlled brakes or pneumatic brakes to achieve precise speed control.
2. Slitting Section
- The slitting section is the heart of the coil slitting line. Manufacturers use different types of slitting methods, such as rotary slitting or shear slitting, depending on the material properties. Rotary slitting is often preferred for thinner materials as it offers a clean cut with less burr. In rotary slitting, the blades are mounted on rotating shafts. The manufacturers need to ensure the precise alignment of these blades to achieve accurate slitting. They use high - quality bearings and precision - machined shafts for this purpose. Shear slitting, on the other hand, is more suitable for thicker materials. It involves a shearing action between two blades. Manufacturers design the shear slitting mechanism to provide sufficient cutting force. This requires the use of strong and durable blades made of high - grade steel. In addition to the slitting blades, the slitting section also includes guide rollers. These guide rollers are used to keep the material in the correct position during slitting. They are carefully designed to minimize friction and ensure smooth material movement.
3. Recoiling Section
- The recoiling section is responsible for winding the slit coils or strips back into a roll. Manufacturers need to design this section to produce high - quality, tightly wound rolls. One important aspect is the tension control during recoiling. If the tension is not consistent, the resulting roll may be loose or have uneven winding. To achieve proper tension control, manufacturers use load - cell - based feedback systems. These systems measure the tension in real - time and adjust the speed of the recoiling motor accordingly. The recoiling mandrel also needs to be designed to ensure that the roll is wound evenly. Some manufacturers use expanding mandrels that can adapt to different widths of the slit material. Additionally, the recoiling section may include features such as edge - guiding devices to keep the material centered during recoiling, which is crucial for producing neat and uniform rolls.
IV. Quality Control and Standards in Coil Slitting Line Manufacturing
1. Material Selection
- High - quality coil slitting lines start with the selection of appropriate materials for their construction. Manufacturers carefully choose materials for each component of the line. For example, in the slitting blades, they use high - grade steel alloys that have excellent hardness and wear resistance. This ensures that the blades can maintain their sharpness over a long period of use. For the structural components of the line, such as the frames and supports, they use strong and durable metals like steel or aluminum alloys. These materials are not only selected for their mechanical properties but also for their resistance to corrosion, especially in industrial environments where the coil slitting lines may be exposed to moisture or chemicals.
2. Manufacturing Processes
- Manufacturers follow strict manufacturing processes to ensure the quality of the coil slitting lines. Precision machining is a key part of these processes. Components such as the shafts, bearings, and blade holders need to be machined to very high tolerances. For example, the shafts that hold the slitting blades must be machined with a high degree of straightness and roundness to ensure proper blade rotation. Welding processes are also carefully controlled. In the construction of the line's frames and supports, welding is used to join different parts. Manufacturers ensure that the welds are of high quality, free from defects such as porosity or cracks. This is achieved through the use of skilled welders and advanced welding techniques, such as robotic welding in some cases. Assembly processes are also crucial. Each component is carefully assembled, and proper alignment and fit are ensured. For example, the alignment between the uncoiling, slitting, and recoiling sections is critical for the overall performance of the coil slitting line.
3. Quality Testing
- Quality testing is an integral part of the manufacturing process for coil slitting lines. Manufacturers conduct various tests at different stages of production. Before assembly, individual components are tested for their mechanical properties. For example, the slitting blades are tested for their hardness and sharpness. The motors used in the uncoiling and recoiling processes are tested for their power output and efficiency. During the assembly process, functional tests are carried out. The entire coil slitting line is run with test materials to check for proper operation of all components. This includes testing the speed control of the uncoiling and recoiling, the accuracy of the slitting process, and the tension control in the line. After the line is fully assembled, final quality tests are performed. These may include load - testing the line with maximum - capacity coils to ensure that it can handle the expected workload without any problems.
V. Customer Support and After - Sales Service by Coil Slitting Line Manufacturers
1. Installation and Commissioning
- Coil slitting line manufacturers provide installation and commissioning services to their customers. This involves sending a team of technicians to the customer's site to install the equipment. During installation, the technicians ensure that all components are properly assembled and connected. They also perform initial setup of the control systems, such as programming the Programmable Logic Controllers (PLCs) with the appropriate parameters for the customer's specific requirements. Commissioning is a crucial step where the technicians test the fully installed line with real - production materials. They make any necessary adjustments to ensure that the line operates at its optimal performance. This may include fine - tuning the tension control, slitting accuracy, or the speed of the various operations.
2. Operator Training
- Manufacturers also offer operator training as part of their customer support. Trained operators are essential for the efficient and safe operation of the coil slitting line. The training programs typically cover both theoretical and practical aspects. Theoretically, operators are taught about the principles of coil slitting, the function of each component in the line, and the importance of various parameters such as tension control and slitting accuracy. Practically, they are trained on how to operate the control panel, start and stop the line, adjust the settings for different materials and production requirements, and perform basic maintenance tasks such as cleaning and lubrication. Some manufacturers may also offer advanced training for operators to handle more complex operations or troubleshooting.
3. Maintenance and Spare Parts
- After - sales maintenance is a key aspect of customer support provided by coil slitting line manufacturers. They offer maintenance contracts that can include regular inspections, preventive maintenance, and emergency repairs. Regular inspections involve checking all components of the line for wear and tear, proper alignment, and functionality. Preventive maintenance may include tasks such as replacing worn - out parts before they cause a breakdown, lubricating moving parts, and calibrating sensors. In case of emergency repairs, manufacturers have a team of service technicians who can be quickly dispatched to the customer's site. Additionally, manufacturers ensure the availability of spare parts. They maintain a stock of commonly used spare parts and can also manufacture custom - made parts if required. This ensures that the customer's coil slitting line can be quickly repaired in case of a component failure, minimizing downtime.
VI. Technological Innovations in Coil Slitting Line Manufacturing
1. Automation and Robotics
- Many coil slitting line manufacturers are incorporating automation and robotics into their products. Automation can range from simple automatic feeding and unloading systems to fully automated control of the entire slitting process. For example, some manufacturers are using robotic arms to load and unload coils, which not only increases efficiency but also improves safety by reducing the need for human operators to handle heavy coils. In the slitting process itself, automation can be used to adjust the slitting parameters based on real - time data from sensors. This allows for more precise slitting and can adapt to changes in the material properties or production requirements.
2. Advanced Control Systems
- Advanced control systems are another area of innovation. Manufacturers are using more sophisticated Programmable Logic Controllers (PLCs) and Human - Machine Interfaces (HMIs). These advanced PLCs can handle more complex algorithms for controlling the various operations in the coil slitting line. The HMIs are becoming more user - friendly, with touch - screen interfaces and real - time data visualization. Operators can easily monitor and control all aspects of the line, such as the speed of each section, the tension in the material, and the status of various components. Some control systems also incorporate artificial intelligence and machine learning algorithms. These can be used to predict potential problems in the line, such as component failures or deviations in slitting accuracy, based on historical data and real - time sensor readings.
3. Energy - efficient Designs
- With the increasing focus on energy conservation, coil slitting line manufacturers are developing energy - efficient designs. This includes using energy - efficient motors, such as variable - speed motors that can adjust their power consumption according to the actual load. Some manufacturers are also exploring alternative energy sources for powering parts of the line. For example, using solar - powered sensors or auxiliary systems. Additionally, the overall design of the line is being optimized to reduce energy losses. This can involve improving the insulation of electrical components, reducing friction in the moving parts, and optimizing the layout of the line to minimize the distance that the material has to travel, which in turn reduces the energy required for material transport.
VII. Market Trends and Future Outlook for Coil Slitting Line Manufacturers
1. Increasing Demand from Emerging Economies
- The demand for coil slitting lines is growing in emerging economies. Countries such as China, India, and Brazil are experiencing rapid industrial growth, especially in sectors like automotive, construction, and electronics. These industries require a large amount of slit coils for their manufacturing processes. For example, in the automotive industry in China, the production of cars has been increasing steadily, and with it, the demand for coil slitting lines to process metal sheets for car body parts, engine components, and interior trim. Coil slitting line manufacturers are looking to expand their market share in these emerging economies by establishing local manufacturing facilities, partnerships, or distribution networks.
2. Focus on Sustainability
- Sustainability is becoming an important trend in the coil slitting line manufacturing industry. Manufacturers are increasingly focused on reducing the environmental impact of their products. This includes using more sustainable materials in the construction of the lines, reducing energy consumption as mentioned earlier, and also minimizing waste during the manufacturing process. For example, some manufacturers are exploring ways to recycle or reuse the scrap materials generated during the slitting process. Additionally, they are developing more environmentally friendly manufacturing processes, such as using water - based lubricants instead of oil - based ones.
3. Customization and Flexibility
- Customers are demanding more customized and flexible coil slitting lines. As industries become more diverse and specialized, they require equipment that can be tailored to their specific needs. For example, a small - scale electronics manufacturer may need a coil slitting line that can handle very thin and precise slitting of conductive foils for battery production. Coil slitting line manufacturers are responding to this trend by offering more customization options. They are developing modular designs that can be easily configured to meet different requirements. This also allows for easier upgrades and modifications in the future as the customer's needs change.
In conclusion, coil slitting line manufacturers play a vital role in providing the necessary equipment for industries that rely on coil slitting processes. They are constantly evolving in terms of design, quality control, customer support, and technological innovation to meet the changing needs of the market. As the global economy and industrial sectors continue to develop, the future outlook for coil slitting line manufacturers is likely to be shaped by trends such as increasing demand from emerging economies, sustainability, and customization.