Hotline
+86-136 8495 9862
Email:cennia@szmizhi.com
Add::104,Building 27,Third Industrial Zone, Longxi Community,Longgang District,Shenzhen,China.
Coil Forming & Handling Equipment
Surface Treatment Equipment
Solutions
Application
About Us
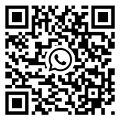
Welcome to MIZHI
For consultation/feedback, please call the service hotline: +86-136 8495 9862 Email:cennia@szmizhi.com
I. Introduction
The coil slitting machine line is a crucial component in the metal processing industry. Coils of various metals, such as steel, aluminum, and copper, are processed through these lines to be slit into narrower widths, which are then used in a wide range of applications. This process is essential for meeting the specific requirements of different industries, including construction, automotive, and electrical manufacturing.
II. Components of a Coil Slitting Machine Line
A. Uncoiling Unit
1. Mandrel and Expansion Mechanism
The uncoiling unit is the starting point of the coil slitting machine line. It consists of a mandrel on which the coil is placed. The mandrel has an expansion mechanism that secures the coil in place. This mechanism is crucial as it must be able to handle coils of different inner diameters. For example, in a steel coil slitting line, the mandrel may need to expand to fit coils with inner diameters ranging from 500mm to 600mm. The expansion is usually achieved through hydraulic or mechanical means. A hydraulic expansion system offers more precise control, allowing for a snug fit of the coil on the mandrel, which is important to prevent the coil from slipping during the uncoiling process.
2. Brake System
To control the speed of the uncoiling process, a brake system is incorporated. This system is necessary to ensure that the coil does not uncoil too quickly, which could lead to issues such as material wrinkling or improper feeding into the slitting section. The brake can be adjusted based on the characteristics of the coil, such as its thickness, width, and material type. For instance, a thicker and wider steel coil may require a more powerful brake to control its uncoiling speed compared to a thinner and narrower aluminum coil.
B. Slitting Section
1. Slitting Blades
The slitting section is the heart of the coil slitting machine line. It contains the slitting blades that are responsible for cutting the coil into narrower widths. These blades are typically made of high - quality tool steel or carbide. The choice of blade material depends on the type of metal being slit. For slitting hard metals like high - strength steel, carbide blades are often preferred due to their superior hardness and wear resistance. The blades are mounted on shafts, and the number of blades can vary depending on the desired number of slits. For example, a coil slitting line may have 3 - 10 slitting blades, depending on the width requirements of the final products.
2. Blade Gap Adjustment
Precise adjustment of the blade gap is crucial for achieving accurate slitting. The gap between the blades needs to be set according to the thickness of the coil. If the gap is too wide, the slitting quality will be poor, with rough edges and potential burrs. On the other hand, if the gap is too narrow, the blades may rub against each other, causing premature wear. Modern coil slitting machine lines often have automated blade gap adjustment systems, which can be calibrated based on the input of the coil thickness.
3. Drive System for Blades
The blades are driven by a motor - based drive system. This system provides the necessary rotational force to the blades, ensuring a smooth and continuous slitting operation. The drive system needs to be powerful enough to handle different types of coils. For example, when slitting thick - gauge steel coils, a high - torque drive system is required. The speed of the blade rotation can also be adjusted, depending on the slitting speed requirements and the characteristics of the coil.
C. Edge Trimming Unit
1. Trimming Blades
The edge trimming unit is responsible for removing any irregular or damaged edges from the slit coils. It uses trimming blades that are similar in nature to the slitting blades but are specifically designed for edge trimming. These blades are often adjustable in terms of their cutting depth, allowing for precise removal of the edges. For example, in an aluminum coil slitting line, the trimming blades can be set to remove only a few millimeters of the edge to clean up any surface imperfections.
2. Alignment and Positioning
To ensure accurate edge trimming, the alignment and positioning of the trimming blades are critical. The unit has mechanisms to precisely position the blades relative to the edges of the slit coils. This is achieved through sensors and servo - motor - based control systems. The sensors detect the position of the coil edges, and the servo - motors adjust the position of the trimming blades accordingly.
D. Recoiling Unit
1. Mandrel and Tension Control
The recoiling unit is where the slit and edge - trimmed coils are rewound into new coils. The mandrel in the recoiling unit is similar to that in the uncoiling unit but may have different tension control mechanisms. Tension control is essential during the recoiling process to ensure that the new coils are wound tightly and evenly. For example, in a copper coil slitting line, if the tension is too low, the coil may be loose and prone to unravelling during handling. If the tension is too high, it could cause the coil to deform or the material to stretch.
2. Wrapping and Packaging
Some recoiling units also include features for wrapping and packaging the new coils. This can involve using plastic or paper wrapping materials to protect the coils from damage during storage and transportation. The wrapping can be automated, with the machine line having mechanisms to apply the wrapping material evenly around the coil.
III. Working Principles of a Coil Slitting Machine Line
A. Material Feed
The coil is first placed on the uncoiling unit's mandrel, and the uncoiling process begins. The material is fed through a series of rollers that guide it towards the slitting section. These rollers are carefully spaced and aligned to ensure a smooth feed of the coil. The feed speed is controlled by the brake system in the uncoiling unit and the drive system in the slitting section.
B. Slitting Operation
As the coil enters the slitting section, the slitting blades start to cut the coil into the desired widths. The blades rotate at a high speed, and the coil is continuously fed through them. The cutting force exerted by the blades is determined by factors such as the blade sharpness, the speed of rotation, and the thickness of the coil. The slitting process generates heat, which is dissipated through cooling systems in some advanced coil slitting machine lines.
C. Edge Trimming
After the slitting, the coil passes through the edge trimming unit. The trimming blades are activated to remove the edges as per the set parameters. The trimmed edges are collected and disposed of separately. The edge trimming process helps to improve the quality of the slit coils, making them suitable for applications where precise edge quality is required.
D. Recoiling
The slit and edge - trimmed coils then enter the recoiling unit. Here, they are rewound onto new mandrels. The tension control system ensures that the recoiling is done with the appropriate amount of tension. Once the recoiling is complete, the new coils are either wrapped for protection or sent directly for further processing or storage.
IV. Applications of Coil Slitting Machine Lines
A. Construction Industry
1. Roofing and Siding
In the construction industry, coil slitting machine lines are used to produce narrow - width metal sheets for roofing and siding. For example, steel coils are slit into widths suitable for roofing tiles or siding panels. The slitted steel sheets can be further processed, such as being coated with protective layers or given a decorative finish, before being installed on buildings. This allows for more efficient use of materials and customization of the roofing and siding products.
2. Structural Components
Coil slitting is also used to produce structural components. Narrow - width steel or aluminum coils can be slit and then formed into beams, purlins, or girts. These components are used in the construction of buildings, bridges, and other structures. The ability to slit coils into specific widths ensures that the structural components can be fabricated to the exact dimensions required for a particular project.
B. Automotive Industry
1. Body Panels
In the automotive industry, coil slitting machine lines are used to produce metal sheets for body panels. For example, aluminum coils are slit into widths suitable for car doors, hoods, or fenders. The slitted sheets can be stamped and formed into the desired shapes with high precision. This is important as it helps in reducing the weight of the vehicle while maintaining its structural integrity.
2. Interior Components
Coil slitting is also used for producing interior automotive components. Narrow - width metal sheets can be used for making dashboard parts, seat frames, or trim pieces. The ability to slit coils into different widths allows for more flexibility in designing and manufacturing these components.
C. Electrical Manufacturing
1. Transformer Coils
In electrical manufacturing, coil slitting machine lines are used to produce narrow - width metal strips for transformer coils. Copper or aluminum coils are slit into the appropriate widths for winding around the transformer cores. The accurate slitting of these materials is crucial for the proper functioning of the transformers, as it affects the electrical resistance and magnetic properties of the coils.
2. Electrical Enclosures
Metal sheets slit from coils are also used for making electrical enclosures. These enclosures protect electrical components from environmental factors such as dust, moisture, and electromagnetic interference. The slitting process allows for the production of enclosures with the exact dimensions required for different electrical devices.
V. Factors Affecting the Performance of a Coil Slitting Machine Line
A. Coil Characteristics
1. Thickness
The thickness of the coil has a significant impact on the performance of the coil slitting machine line. Thicker coils require more powerful drive systems for the slitting blades and more precise tension control during recoiling. For example, a 5 - mm - thick steel coil will demand a higher torque drive for the blades compared to a 1 - mm - thick coil.
2. Width
The width of the coil also affects the slitting process. A wider coil may require more slitting blades or a different blade arrangement to achieve the desired slit widths. Additionally, wider coils may need more powerful uncoiling and recoiling systems to handle the increased mass.
3. Material Type
The type of metal in the coil, such as steel, aluminum, or copper, influences the choice of slitting blades, the cutting speed, and the overall performance of the machine line. For instance, copper is a relatively soft metal compared to steel, so the slitting blades for copper coils may need to be sharper and more precisely adjusted to prevent deformation of the slit edges.
B. Machine - related Factors
1. Blade Quality
The quality of the slitting and trimming blades is crucial for the performance of the coil slitting machine line. High - quality blades made of appropriate materials (e.g., carbide for hard metals) will result in better slitting and edge trimming quality. Dull or damaged blades will lead to rough cuts, burrs, and increased wear on other machine components.
2. Machine Calibration
Proper calibration of the entire coil slitting machine line is essential. This includes calibrating the uncoiling and recoiling systems for correct tension control, the slitting section for accurate blade gap adjustment and blade rotation speed, and the edge trimming unit for precise edge removal. Incorrect calibration can result in poor - quality products and reduced machine efficiency.
VI. Advantages of Using a Coil Slitting Machine Line
A. Material Utilization
Coil slitting machine lines allow for efficient material utilization. By slitting large - width coils into narrower widths, manufacturers can produce a variety of products from a single coil, reducing waste. For example, in a steel manufacturing plant, a large - width coil can be slit into different widths for roofing, siding, and structural components, minimizing the amount of scrap material.
B. Product Customization
These machine lines enable product customization. Manufacturers can slit coils into specific widths according to the requirements of different customers or applications. This is particularly important in industries such as automotive and construction, where customized products are in high demand. For instance, in the automotive industry, different car models may require body panels of different widths, which can be easily achieved through coil slitting.
C. Cost - effectiveness
Using a coil slitting machine line can be cost - effective. It reduces the need to purchase pre - slit materials, which are often more expensive. Additionally, by minimizing waste, it also reduces the overall cost of raw materials. For example, a company that produces electrical enclosures can save costs by slitting its own copper or steel coils instead of buying pre - slit sheets.
VII. Challenges and Future Developments
A. Challenges
1. Blade Wear
One of the main challenges in coil slitting machine lines is blade wear. The slitting and trimming blades are subject to significant wear during the cutting process, especially when slitting hard metals. Regular blade replacement is required, which can be costly and time - consuming.
2. Maintenance and Downtime
The complex nature of coil slitting machine lines means that they require regular maintenance. Components such as the uncoiling and recoiling systems, slitting blades, and edge trimming units need to be maintained to ensure optimal performance. Downtime for maintenance can be a significant issue, especially in high - volume production environments.
B. Future Developments
1. Automation and Industry 4.0 Integration
The future of coil slitting machine lines is likely to see increased automation and integration with Industry 4.0 concepts. Machines will be more connected, allowing for remote monitoring and control. Automated blade replacement systems and predictive maintenance based on real - time data analysis will be developed. For example, sensors can be installed to monitor blade wear, and when the wear reaches a critical level, the system can automatically order a replacement blade and schedule a maintenance break.
2. Improved Slitting Technologies
There will be continuous improvement in slitting technologies. New blade materials and designs will be developed to reduce blade wear and improve slitting quality. For example, advanced coatings on slitting blades may be introduced to increase their hardness and wear resistance. Additionally, new slitting methods that are more energy - efficient and produce less waste may emerge.
In conclusion, the coil slitting machine line is a vital part of the metal processing industry. It offers numerous advantages in terms of material utilization, product customization, and cost - effectiveness. However, it also faces challenges such as blade wear and maintenance requirements. With future developments in automation and slitting technologies, these machine lines are expected to become more efficient and reliable, further enhancing their importance in various industries.