Hotline
+86-136 8495 9862
Email:cennia@szmizhi.com
Add::104,Building 27,Third Industrial Zone, Longxi Community,Longgang District,Shenzhen,China.
Coil Forming & Handling Equipment
Surface Treatment Equipment
Solutions
Application
About Us
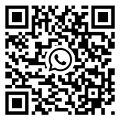
Welcome to MIZHI
For consultation/feedback, please call the service hotline: +86-136 8495 9862 Email:cennia@szmizhi.com
1. Introduction
In the intricate web of modern manufacturing and metal - processing industries, the coil slitting machine stands as a cornerstone of efficient material transformation. This specialized equipment is designed to take large - width metal coils and slice them into narrower strips, tailored to the specific requirements of various downstream applications. From the automotive sector, where precision - cut metal components are essential for vehicle safety and performance, to the construction industry, which demands accurately sized metal sheets for roofing, siding, and structural elements, the coil slitting machine plays a pivotal role. Its ability to convert raw coil materials into precisely sized products not only streamlines production processes but also significantly contributes to cost - effectiveness and quality control across multiple industries.
2. Working Principle and Components
2.1 Decoiling Unit
The operation of a coil slitting machine commences with the decoiling unit. This crucial component is responsible for carefully unwinding the large - diameter metal coil. It consists of a sturdy, expandable mandrel that firmly grips the inner diameter of the coil. Motors, often with variable - speed capabilities, are connected to the mandrel. These motors enable smooth and controlled unwinding of the coil, ensuring a consistent feed of the metal strip into the subsequent processing stages. For instance, in the processing of thin - gauge aluminum coils for the packaging industry, the decoiling unit must unwind the coil at a precise speed to prevent stretching or wrinkling of the delicate material. Advanced tension control systems are integrated into the decoiling unit. These systems monitor and adjust the tension in the metal strip as it is unwound. Maintaining optimal tension is essential; too much tension can cause the strip to stretch or break, while too little tension can result in sagging or uneven feeding, which may lead to defects in the slit strips.
2.2 Leveling and Straightening Section
After decoiling, the metal strip typically has some curvature or irregularities due to the coiling process. The leveling and straightening section of the coil slitting machine is designed to eliminate these imperfections. This section is composed of a series of precision - ground rolls. The rolls are arranged in a specific pattern, and as the metal strip passes through them, they apply a controlled amount of pressure. The number of rolls, their diameter, and the pressure they exert can be adjusted according to the thickness and type of the metal being processed. For example, when dealing with thick - gauge steel coils for the construction of heavy - machinery frames, the leveling section may have more rolls and apply higher pressure to effectively straighten the stiff metal. The straightening process not only makes the strip flat but also ensures that it has a consistent cross - sectional shape, which is fundamental for accurate slitting.
2.3 Slitting Section
The slitting section is the heart of the coil slitting machine. Here, the actual cutting of the metal strip into narrower strips takes place. High - precision circular slitting knives are the key components in this section. These knives are made from high - quality tool steel, often heat - treated to achieve exceptional hardness and wear resistance. The knives are mounted on precisely machined arbors. The distance between the knives can be adjusted to achieve the desired strip widths. In modern coil slitting machines, computer - controlled systems are used to manage the knife - setting process. Operators can input the required strip widths into the control panel, and the system automatically adjusts the positions of the knives with great accuracy. This allows for the production of slit strips with very tight width tolerances, often within ±0.1mm or even less in high - end machines. The slitting section also features a cutting mechanism that can operate at high speeds, enabling efficient processing of large volumes of metal. The cutting speed can be adjusted based on the thickness and type of the metal, ensuring optimal cutting performance and quality.
2.4 Scrap Rewinding and Strip Winding Units
As the metal strip is slit, the scrap material (the narrow strips that are not part of the final product) needs to be removed efficiently. The scrap rewinding unit in the coil slitting machine is designed to handle this task. It quickly and neatly winds up the scrap into a coil, which can be easily disposed of or recycled. On the other hand, the strip winding units are responsible for winding the slit strips into individual coils. These units are equipped with advanced tension control systems to ensure that the coils are wound tightly and evenly. The tension control is crucial; if the tension is too high, the strip may be stretched or damaged, and if it is too low, the coils may be loose and prone to tangling. The strip winding units can precisely adjust the tension according to the characteristics of the metal strip, ensuring high - quality coil winding.
3. Applications across Diverse Industries
3.1 Automotive Industry
In the automotive industry, coil slitting machines are indispensable. Metal strips produced by these machines are used for manufacturing a wide range of components. For car body panels, such as doors, hoods, and fenders, the coil slitting machine provides the precisely cut metal strips required for stamping operations. The accurate widths and straight edges of the slit strips ensure that the stamped panels fit together perfectly during the assembly process. This not only improves the aesthetics of the vehicle but also enhances its structural integrity and safety. In the production of engine parts, such as cylinder heads and engine blocks, the coil slitting machine cuts metal strips for the manufacturing of gaskets and other small components. The high - precision slitting ensures that these components have the correct dimensions, which is crucial for the proper functioning of the engine.
3.2 Construction Industry
The construction industry is another major consumer of products processed by coil slitting machines. Metal sheets are used extensively for roofing, siding, and structural components. For roofing applications, the coil slitting machine can cut metal coils into strips of the exact width required for different roofing systems. This ensures a proper fit and reduces the need for on - site cutting and adjustments. In the case of siding, the precise slitting allows for the production of uniform - sized metal strips that can be easily installed to create a smooth and aesthetically pleasing exterior. For structural components, such as steel beams and columns, the coil slitting machine can cut metal strips that are further processed into channels, angles, and other profiles. The accuracy of the slitting process contributes to the overall strength and stability of the construction structures.
3.3 Electrical and Electronics Industry
In the electrical and electronics industry, coil slitting machines play a vital role in the production of components such as electrical enclosures, circuit boards, and connectors. For electrical enclosures, the coil slitting machine cuts metal strips to the required widths for forming the enclosures. The precise slitting ensures that the enclosures have a tight - fitting and secure design, protecting the electrical components inside. In the production of circuit boards, the coil slitting machine cuts metal strips for the manufacturing of conductive traces and other components. The high - precision slitting is essential for ensuring the proper electrical conductivity and functionality of the circuit boards. For connectors, the coil slitting machine cuts metal strips into narrow widths that are used to make the contact points. The accuracy of the slitting process ensures that the connectors have a reliable and consistent connection.
4. Advantages of Coil Slitting Machines
4.1 High Precision
One of the most significant advantages of coil slitting machines is their high precision. The advanced control systems, high - quality components, and precise machining of these machines enable them to achieve extremely tight tolerances. This precision is crucial for industries where even the slightest deviation in the width of the slit strips can lead to significant problems. For example, in the aerospace industry, where metal components need to meet strict quality and safety standards, the high - precision slitting of coil slitting machines ensures that the slit metal strips used for manufacturing aircraft parts have the exact dimensions required. The high - precision slitting also reduces the need for secondary processing, such as trimming or re - sizing, which saves time and cost.
4.2 High - Speed Processing
Coil slitting machines are designed for high - speed processing, allowing for efficient production of large volumes of slit metal strips. The powerful motors, advanced drive systems, and optimized cutting mechanisms enable the machines to operate at high speeds without sacrificing quality. This is especially important for industries with high - volume production requirements, such as the automotive and construction industries. For example, in a large - scale automotive manufacturing plant, the coil slitting machine can quickly process metal coils into the required slit strips, keeping up with the production pace of the assembly lines. The high - speed processing also reduces the overall production time, enabling companies to bring their products to market faster.
4.3 Material Utilization and Waste Reduction
By precisely cutting the metal coils into the required strip widths, coil slitting machines optimize material utilization. In traditional cutting methods, there is often a significant amount of waste due to inaccurate cuts. Coil slitting machines minimize this waste, as the accurate slitting ensures that the metal is used as efficiently as possible. This not only reduces the cost of raw materials but also has a positive environmental impact by reducing the amount of waste that needs to be disposed of. For example, in a metal - processing factory that processes large volumes of steel coils, the use of a coil slitting machine can lead to substantial savings in raw material costs over time.
4.4 Versatility
Coil slitting machines are highly versatile, capable of handling a wide range of metal types, thicknesses, and widths. Whether it's processing thin - gauge aluminum for the packaging industry, thick - gauge steel for the heavy - machinery industry, or copper for the electrical industry, the coil slitting machine can adjust its parameters to achieve optimal slitting results. The adjustable knife - setting mechanism and the flexible control systems allow for easy adaptation to different production requirements. This versatility makes the coil slitting machine suitable for a diverse range of industries and applications, providing a single - solution for various metal - slitting needs.
5. Challenges and Solutions in Coil Slitting Machine Operation
5.1 Wear and Tear of Cutting Tools
The circular slitting knives in coil slitting machines are subject to significant wear and tear during operation. The continuous cutting of hard metals can cause the knife edges to become dull over time. Dull knives can lead to poor - quality cuts, increased cutting forces, and reduced productivity. To address this issue, manufacturers often use high - quality, wear - resistant tool steels for the knives. Regular maintenance, including sharpening or replacing the knives at appropriate intervals, is also crucial. Some advanced coil slitting machines are equipped with automatic tool - monitoring systems that can detect the wear of the knives and alert the operator when replacement is necessary.
5.2 Material Variability
Metal coils can vary in their properties from batch to batch, such as hardness, thickness, and surface finish. These variations can pose challenges to the slitting process. For example, if the metal is harder than expected, it may require more cutting force, which can affect the accuracy of the cut and the lifespan of the cutting tools. To overcome this, modern coil slitting machines are often equipped with sensors that can detect the properties of the incoming metal coil. Based on the data collected by these sensors, the machine can automatically adjust the cutting parameters, such as cutting speed, force, and power, to ensure a consistent and high - quality cut.
5.3 Operator Training and Skill Requirements
Operating a coil slitting machine requires a certain level of technical skills and knowledge. The operator needs to be familiar with the machine's control systems, knife - setting procedures, and safety protocols. Inadequate operator training can lead to errors in the slitting process, such as incorrect strip widths or damaged coils. To address this, manufacturers provide comprehensive operator training programs. These programs cover everything from basic machine operation to advanced troubleshooting and maintenance. Some companies also offer online training resources and continuous support to ensure that operators are up - to - date with the latest techniques and best practices.
6. Future Trends in Coil Slitting Machine Technology
6.1智能化和自动化
The future of coil slitting machines lies in increased智能化 and自动化. Advanced artificial intelligence (AI) and machine learning (ML) algorithms will be integrated into these machines. AI - powered sensors will be able to detect and analyze the quality of the metal coil and the slitting process in real - time. For example, they can identify surface defects, thickness variations, or irregularities in the coil and automatically adjust the slitting parameters to compensate for these issues. Automated material handling systems will also become more prevalent, reducing the need for manual labor and increasing productivity. Robotic arms may be used for tasks such as coil loading, unloading, and scrap removal, further streamlining the production process.
6.2 Sustainable and Environmentally Friendly Features
As environmental concerns continue to grow, coil slitting machines will incorporate more sustainable and environmentally friendly features. This may include the use of energy - efficient motors and drives to reduce power consumption. Recycling systems for scrap materials will be more advanced, ensuring that a higher percentage of the scrap metal is recycled. The use of lubricants and coolants in the slitting process will also be optimized to minimize environmental impact. For example, some machines may use water - based lubricants or closed - loop coolant systems that recycle and purify the coolant.
6.3 Integration with Industry 4.0
Coil slitting machines will be an integral part of the Industry 4.0 ecosystem. They will be connected to the Internet of Things (IoT), allowing for remote monitoring and control. Manufacturers will be able to access real - time data on the machine's performance, such as production rates, energy consumption, and tool wear, from anywhere in the world. This data can be used for predictive maintenance, quality control, and production optimization. Coil slitting machines will also be integrated with other manufacturing equipment, such as stamping presses, welding robots, and automated storage and retrieval systems, to create fully automated and intelligent manufacturing lines.
In conclusion, the coil slitting machine is a vital piece of equipment in the modern manufacturing landscape. Its precision, high - speed processing, and versatility make it essential for industries across the board. While there are challenges associated with its operation, ongoing technological advancements and innovative solutions are continuously improving its performance and capabilities. As we look to the future, the coil slitting machine will play an even more significant role in driving efficiency, quality, and sustainability in the metal - processing and manufacturing industries.