Hotline
+86-136 8495 9862
Email:cennia@szmizhi.com
Add::104,Building 27,Third Industrial Zone, Longxi Community,Longgang District,Shenzhen,China.
Coil Forming & Handling Equipment
Surface Treatment Equipment
Solutions
Application
About Us
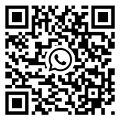
Welcome to MIZHI
For consultation/feedback, please call the service hotline: +86-136 8495 9862 Email:cennia@szmizhi.com
Blast Wheel: The blast wheel is often regarded as the "heart" of the shot blasting system. It is a centrifugal device with an internal impeller and blades. When the blast wheel rotates at high speeds, typically around 3600 rpm, it imparts a tremendous amount of kinetic energy to the steel shot, propelling it towards the workpiece at speeds ranging from 250 to 300 ft. per second. The design and condition of the blast wheel significantly impact the performance and efficiency of the shot blasting process. A well-maintained and properly designed blast wheel can ensure a consistent and powerful shot stream, resulting in effective surface treatment.
Blast Cabinet: Serving as the "body" of the system, the blast cabinet is fabricated from durable materials such as manganese steel and AR plate. Its primary functions are to support the blast wheels and contain the steel shot within a confined area. This containment is crucial for safety reasons and also to facilitate the recovery of the shot for reuse. The cabinet must be able to withstand the continuous wear and tear caused by the high-velocity impact of the shot, especially in heavy-duty industrial applications where the system may operate 24 hours a day, three shifts a week.
Abrasive Recovering System: As the "circulatory system" of the shot blasting machine, this component is responsible for collecting and recycling the used shot. After the shot strikes the workpiece, it falls to the bottom of the machine and is recovered via a screw conveyor and bucket elevator system. The recovered shot is then transported through an "air-wash" separation system, which removes any small broken-down contaminants and excessive dust. This ensures that the recycled shot is clean and in good condition for reuse, reducing waste and lowering the overall cost of the process.
Work Handling System: The work handling system can be considered the "legs and arms" of the shot blasting machine. It is responsible for presenting the workpiece to be cleaned in the most efficient manner. There are various types of work handling systems, including tumble barrels for small parts, rotating tables for flat or cylindrical workpieces, spinner hanger fixtures for irregularly shaped objects, and overhead monorail, roll conveyor, or continuous mesh belt systems for larger or continuous production lines. The choice of work handling system depends on the size, shape, and quantity of the workpieces to be processed.
Dust Collector & Airwash Separator: These components act as the "lungs" of the shot blasting system. The dust collector provides the necessary ventilation to remove dust generated during the blasting process from the blast cabinet. It also creates an air stream across the "air-wash" separator, which cleans the small fines and foreign contaminants from the shot before it is reused. A reliable dust collection and air-wash separation system is essential for maintaining a clean working environment, protecting the health of operators, and ensuring the long-term reliability and efficiency of the shot blasting machine.
Electrical Controls: The electrical system, including push button controls and programmable logic controllers (PLCs), serves as the "brains" of the shot blasting machine. It controls the random start/stop operation of the machine and its associated components, such as the blast wheel, conveyor systems, and dust collector. Advanced electrical control systems can also be integrated with PLC automation and robotic interfacing, allowing for more precise control, improved productivity, and the ability to handle complex production schedules. These automation systems usually require factory pre-programming and customization based on the specific requirements of the customer.
Working Principle
The shot blasting system operates based on the principle of using centrifugal force to project abrasive shot onto the surface of a workpiece. The shot is loaded into the blast wheel, which rotates at high speed. As the wheel spins, the shot is forced to the outer edge of the wheel due to centrifugal acceleration. When the shot reaches the edge of the wheel, it is released and projected towards the workpiece with high velocity. The impact of the shot on the surface creates a combination of abrasive and peening effects.
Applications
Automotive Industry: In the automotive manufacturing process, shot blasting is used to clean and prepare surfaces before painting or coating. It removes rust, scale, and other contaminants from car bodies, chassis, and engine components, ensuring excellent adhesion of the paint or coating and enhancing the durability and corrosion resistance of the finished product. Additionally, shot peening can be applied to critical components such as gears, shafts, and springs to improve their fatigue strength and resistance to wear.
Aerospace Industry: The aerospace sector demands the highest level of surface quality and integrity. Shot blasting is used to clean and prepare turbine blades, engine components, and structural parts, removing surface defects, oxides, and heat treatment scales. Shot peening is also widely employed to induce compressive residual stresses in these components, increasing their resistance to fatigue, stress corrosion cracking, and improving their overall reliability and lifespan.
Metalworking and Machining: Shot blasting is an essential step in metalworking and machining operations. It helps to remove burrs, sharp edges, and surface irregularities from machined parts, improving their dimensional accuracy and surface finish. Moreover, it can be used to descale and clean metal sheets, bars, and forgings, preparing them for further processing such as welding, forming, or heat treatment.
Construction and Infrastructure: In the construction industry, shot blasting is used to prepare concrete surfaces for coatings, overlays, or adhesives. It can remove laitance, dirt, and other surface contaminants from concrete floors, pavements, and bridge decks, creating a clean and rough surface that promotes better adhesion of the subsequent treatment. Shot blasting can also be used to clean and roughen the surfaces of steel structures, such as bridges and buildings, before applying protective coatings.
Foundry and Casting: In foundries, shot blasting is used to clean castings by removing sand, scale, and other residues from the surface. This not only improves the appearance of the casting but also enhances its mechanical properties by reducing surface defects and improving the surface finish. Shot blasting can also be used for shot peening of castings to increase their strength and durability.
Advantages
Efficient Surface Cleaning: Shot blasting is a highly efficient method of removing surface contaminants, rust, scale, and old coatings compared to manual or chemical cleaning methods. It can cover large surface areas quickly, reducing labor costs and increasing productivity, especially for large-scale production or surface treatment projects.
Improved Surface Quality: The impact of the shot on the surface creates a uniform and controlled roughness, which enhances the adhesion of coatings, paints, and adhesives. This results in a longer-lasting and more durable finish, reducing the risk of coating failure due to poor adhesion.
Enhanced Material Properties: Shot peening, a form of shot blasting, can induce compressive residual stresses in metal components, improving their fatigue strength, wear resistance, and resistance to stress corrosion cracking. This can significantly extend the lifespan of critical components in high-stress applications.
Versatility: Shot blasting systems can be used to treat a wide variety of materials, including steel, aluminum, cast iron, titanium, and concrete. They can also handle different shapes and sizes of workpieces, making them suitable for diverse industrial applications.
Environmentally Friendly: Shot blasting is a dry and mechanical process that does not involve the use of harmful chemicals, reducing environmental pollution and potential health hazards associated with chemical cleaning agents. Additionally, the recyclability of the shot media further minimizes waste generation.
Considerations for Operation and Maintenance
Proper Setup and Calibration: To achieve optimal results, it is essential to set up and calibrate the shot blasting system correctly. This includes adjusting the blast pattern, ensuring the correct alignment of the blast wheels, and setting the appropriate shot velocity and feed rate based on the workpiece material, shape, and surface requirements.
Regular Maintenance: Routine maintenance is crucial to keep the shot blasting system in good working condition. This includes inspecting and replacing worn parts of the blast wheel, cleaning and maintaining the abrasive recovering system, checking the dust collector and air-wash separator for proper operation, and lubricating moving components. Regular maintenance not only ensures the efficiency and performance of the system but also extends its lifespan and reduces the risk of breakdowns.
Safety Precautions: The operation of a shot blasting system involves certain risks due to the high-velocity projection of abrasive shot. Operators must wear appropriate personal protective equipment, such as safety glasses, ear protection, gloves, and protective clothing, to prevent injuries from flying debris and noise. The work area should be properly enclosed and ventilated to control dust emissions and ensure a safe working environment.
Abrasive Selection: The choice of abrasive shot material depends on the specific application, workpiece material, and desired surface finish. Different types of shot, such as steel shot, stainless steel shot, aluminum oxide, or glass beads, offer varying levels of hardness, density, and abrasiveness. Selecting the right abrasive is essential for achieving the desired surface treatment results while minimizing damage to the workpiece.
Conclusion
In summary, a shot blasting system is a powerful and versatile surface treatment solution that offers numerous benefits in terms of efficiency, surface quality improvement, material property enhancement, and environmental friendliness. Its wide range of applications across various industries makes it an essential tool for modern manufacturing and construction processes. However, proper operation, maintenance, and safety precautions are necessary to ensure the optimal performance and longevity of the system, as well as the safety of the operators. With continuous advancements in technology, shot blasting systems are likely to become even more efficient, precise, and environmentally sustainable in the future, further expanding their applications and contributing to the improvement of product quality and performance in different industries.