Hotline
+86-136 8495 9862
Email:cennia@szmizhi.com
Add::104,Building 27,Third Industrial Zone, Longxi Community,Longgang District,Shenzhen,China.
Coil Forming & Handling Equipment
Surface Treatment Equipment
Solutions
Application
About Us
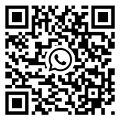
Welcome to MIZHI
For consultation/feedback, please call the service hotline: +86-136 8495 9862 Email:cennia@szmizhi.com
A concrete floor bead blaster is a powerful and specialized tool that has revolutionized the process of surface preparation and cleaning for concrete floors. This innovative equipment utilizes the force of small abrasive beads propelled at high velocities to achieve remarkable results in a variety of applications.
I. Working Principle
At the heart of a concrete floor bead blaster lies a mechanism that accelerates the abrasive beads. Typically, compressed air or a mechanical wheel system is employed to hurl the beads towards the concrete surface. As the beads impact the floor, they create a combination of abrasive action and kinetic energy transfer. This action effectively chips away at dirt, grime, old coatings, paint, and surface imperfections such as bumps and ridges. The beads' small size and hardness allow them to reach into pores and crevices, providing a thorough cleaning and roughening effect.
II. Components and Features
1. Blasting Unit: The blasting unit is the core component where the magic happens. It houses the abrasive bead reservoir and the mechanism for propelling the beads. In an air-powered bead blaster, a high-pressure air compressor is connected to the unit, which pressurizes the air and forces it through a nozzle along with the beads. In a wheel-based system, a rapidly rotating wheel imparts the necessary force to the beads, sending them flying towards the floor.
2. Abrasive Hopper: The abrasive hopper is designed to hold a sufficient quantity of beads to ensure continuous operation. It is often equipped with a feeding mechanism that regulates the flow of beads into the blasting unit, allowing for precise control over the amount of abrasives used. Some advanced models have a self-leveling hopper that ensures a consistent bead supply, regardless of the position of the blaster.
3. Dust Collection System: Given the nature of the bead blasting process, which generates a significant amount of dust and debris, a reliable dust collection system is essential. This typically includes a vacuum or suction device that captures the airborne particles as they are created. The collected dust is then filtered and stored in a collection bin, preventing it from spreading throughout the work area. A good dust collection system not only keeps the workplace clean but also improves air quality and protects the health of the operators.
4. Nozzle and Hose Assembly: The nozzle is the business end of the bead blaster, where the beads are ejected towards the concrete floor. It is designed to control the spread and direction of the abrasive stream, allowing for accurate targeting of specific areas. The hose connects the blasting unit to the nozzle and must be durable enough to withstand the high-pressure flow of beads and air. Some nozzles are adjustable, enabling the operator to change the blast pattern and intensity to suit different surface conditions.
5. Control Panel: Modern concrete floor bead blasters come equipped with a control panel that offers a range of functions. Operators can adjust the blasting pressure, the speed of the bead feed, and the frequency of the dust collection system. Some advanced models even have programmable settings, allowing for the creation of custom blasting profiles for different types of concrete surfaces or specific cleaning tasks.
III. Advantages
1. Efficient Cleaning and Surface Preparation: Bead blasting is a highly efficient method of removing contaminants from concrete floors. It can quickly strip away layers of dirt, paint, and other coatings that would be time-consuming and labor-intensive to remove by hand or with other traditional methods. The result is a clean and roughened surface that provides excellent adhesion for new coatings, such as epoxy, polyurethane, or concrete sealers.
2. Versatility: These bead blasters can be used on a wide variety of concrete surfaces, including industrial floors, garage floors, warehouse floors, and even outdoor pavements. They are suitable for both new construction projects and the renovation of existing floors. Whether the goal is to remove old, worn-out coatings or to prepare a new floor for its first finish, the bead blaster can handle the task.
3. Precision and Control: The ability to adjust the blasting parameters, such as pressure and bead flow, gives operators precise control over the surface treatment process. This precision allows for the removal of surface imperfections without causing excessive damage to the underlying concrete. It also enables the creation of a consistent surface profile, which is crucial for achieving a uniform and durable finish.
4. Environmentally Friendly: Compared to some other surface preparation methods, such as chemical stripping or sandblasting, bead blasting is relatively environmentally friendly. The use of small, recyclable beads and the efficient dust collection system reduce the amount of waste and airborne pollutants generated during the process. Additionally, the absence of harsh chemicals means that there is no risk of chemical runoff contaminating the surrounding environment.
5. Cost-Effective: While the initial investment in a concrete floor bead blaster may be significant, the long-term cost savings are substantial. The efficiency of the process reduces the need for extensive labor and the consumption of large quantities of cleaning materials. Moreover, the improved adhesion of coatings applied to a bead-blasted surface can extend the lifespan of the floor finish, reducing the frequency of costly recoating operations.
IV. Applications
1. Industrial and Commercial Facilities: In factories, warehouses, and manufacturing plants, concrete floor bead blasters are used to prepare floors for heavy-duty use. They remove old coatings and contaminants, creating a clean and slip-resistant surface that can withstand the wear and tear of forklift traffic, machinery vibrations, and chemical spills. This not only improves workplace safety but also enhances the durability and performance of the floor.
2. Garage and Residential Floors: For homeowners and garage owners, bead blasting is an effective way to transform dull and dirty concrete floors. It can remove oil stains, tire marks, and other unsightly blemishes, preparing the floor for a decorative coating or a simple clear sealant. The result is a clean, attractive, and easy-to-maintain floor surface.
3. Retail and Showroom Floors: In retail spaces and showrooms, the appearance of the floor is crucial. Bead blasting can be used to create a smooth and polished finish on concrete floors, enhancing the overall aesthetic appeal of the space. It can also remove any surface imperfections that could detract from the display of merchandise or the impression of the showroom.
4. Bridge and Infrastructure Projects: Concrete bridge decks and other infrastructure elements often require periodic maintenance and surface preparation. Bead blasters can be used to clean and roughen the surface, improving the bond between the concrete and subsequent repair materials or coatings. This helps to extend the lifespan of the structure and ensure its continued safety and functionality.
V. Operation and Maintenance
1. Operation: Before operating a concrete floor bead blaster, it is essential to ensure that the work area is properly ventilated and that all safety precautions are in place. Operators should wear appropriate personal protective equipment, including safety glasses, gloves, and a respirator. The bead blaster should be set up according to the manufacturer's instructions, with the correct type and size of abrasive beads loaded into the hopper. The operator then adjusts the control panel settings to the desired blasting parameters and begins the process, moving the blaster in a systematic manner to ensure even coverage of the floor surface.
2. Maintenance: Regular maintenance is crucial to keep the bead blaster in optimal working condition. This includes cleaning or replacing the filters in the dust collection system, checking the hoses and nozzles for wear and tear, and inspecting the blasting unit for any signs of damage or malfunction. The abrasive beads should also be replenished as needed, and the hopper and other components should be cleaned to prevent clogging and ensure proper bead flow.
In conclusion, a concrete floor bead blaster is a valuable tool for anyone involved in the surface preparation and cleaning of concrete floors. Its efficiency, versatility, and environmental friendliness make it a preferred choice in a wide range of applications, from industrial facilities to residential garages. By understanding its working principle, components, advantages, and applications, users can make the most of this powerful equipment to achieve outstanding results in concrete floor maintenance and improvement.