Hotline
+86-136 8495 9862
Email:cennia@szmizhi.com
Add::104,Building 27,Third Industrial Zone, Longxi Community,Longgang District,Shenzhen,China.
Coil Forming & Handling Equipment
Surface Treatment Equipment
Solutions
Application
About Us
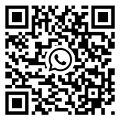
Welcome to MIZHI
For consultation/feedback, please call the service hotline: +86-136 8495 9862 Email:cennia@szmizhi.com
In the modern manufacturing landscape, where high - volume production is the norm across various industries, the demand for efficient and reliable surface treatment equipment has never been greater. The continuous - flow tumble belt shot blasting machine stands out as a revolutionary solution tailored to meet the exacting requirements of high - volume production environments. This type of machine combines innovative design concepts with advanced technologies to ensure that workpieces are processed quickly, thoroughly, and consistently, making it an indispensable asset for manufacturers aiming to enhance productivity and maintain high - quality standards.
Design and Structure of Continuous - Flow Tumble Belt Shot Blasting Machines
Tumble Belt Mechanism
The core of the continuous - flow tumble belt shot blasting machine is its unique tumble belt mechanism. The tumble belt is typically constructed from high - strength, wear - resistant materials such as heavy - duty rubber or specialized polymers reinforced with steel cables. This robust construction allows the belt to withstand the rigors of continuous operation and the impact of shot media during the blasting process. The belt is designed in a way that it forms a continuous loop, moving workpieces through the blasting chamber in a seamless and controlled manner.
The surface of the tumble belt often features a series of ridges, pockets, or other patterns. These elements serve to hold the workpieces in place and ensure that they are tumbled and rotated as they move along the belt. This tumbling action is crucial as it exposes all surfaces of the workpieces to the shot media, ensuring comprehensive and uniform surface treatment. For example, small metal components like bolts, nuts, and castings can be placed on the belt, and as the belt moves, the components are tumbled, allowing the shot to reach even the most intricate and hard - to - reach areas.
Blasting Chamber
The blasting chamber of a continuous - flow tumble belt shot blasting machine is a sealed enclosure designed to contain the shot media and prevent it from escaping during the blasting process. It is usually constructed from thick, durable steel plates to withstand the impact of the high - velocity shot. The interior of the chamber is often lined with wear - resistant materials such as manganese steel or rubber liners to protect the chamber walls from erosion caused by the shot media.
Inside the blasting chamber, multiple blasting wheels are strategically positioned. These wheels are responsible for accelerating the shot media to high speeds and propelling it towards the workpieces. The number and arrangement of the blasting wheels depend on the size and capacity of the machine as well as the specific requirements of the workpieces being processed. For high - volume production, machines may have four, six, or even more blasting wheels, ensuring that a large number of workpieces can be treated simultaneously and that the surface treatment is consistent across all of them.
Shot Recycling and Separation System
An efficient shot recycling and separation system is an integral part of the continuous - flow tumble belt shot blasting machine. As the shot media impacts the workpieces, it becomes contaminated with dirt, debris, and worn - out particles. To ensure the effectiveness of the blasting process and to reduce the consumption of shot media, a sophisticated recycling system is employed.
The used shot media, along with the contaminants, falls to the bottom of the blasting chamber and is collected. It then passes through a series of conveyors, air washers, and cyclones. The air washers use a stream of air to separate the lighter contaminants, such as dust and small debris, from the heavier shot media. The cyclones further refine the separation process by using centrifugal force to separate the shot from any remaining contaminants. Finally, magnetic separators are used to remove any ferrous contaminants from the shot, ensuring that only clean and reusable shot media is returned to the blasting process. This continuous recycling of shot media not only reduces operating costs but also minimizes the environmental impact by reducing the amount of waste generated.
Operational Principles and Advantages for High - Volume Production
Continuous - Flow Operation
The most significant advantage of the continuous - flow tumble belt shot blasting machine for high - volume production is its ability to operate continuously. Unlike batch - type shot blasting machines, which require the blasting chamber to be loaded, processed, and unloaded in separate cycles, the continuous - flow machine allows workpieces to be fed onto the tumble belt at one end and removed at the other end without any interruptions. This seamless flow of workpieces enables a much higher throughput rate, making it ideal for mass production environments.
For example, in an automotive parts manufacturing plant, thousands of small metal components need to be surface - treated every day. With a continuous - flow tumble belt shot blasting machine, these components can be continuously fed onto the belt, processed through the blasting chamber, and discharged for further processing or packaging. This eliminates the downtime associated with batch - processing, significantly increasing the overall productivity of the manufacturing line.
Uniform Surface Treatment
Another key advantage is the ability to provide uniform surface treatment across a large number of workpieces. The tumbling action of the belt combined with the consistent distribution of shot media from the multiple blasting wheels ensures that each workpiece receives the same amount of blasting, resulting in a consistent surface finish. This is particularly important in industries where product quality and appearance are critical, such as the aerospace and consumer goods industries.
In the aerospace industry, components need to have a precise surface finish to meet strict quality and safety standards. The continuous - flow tumble belt shot blasting machine can ensure that all components, whether they are small fasteners or large structural parts, are treated uniformly, reducing the risk of defects and improving the overall reliability of the final product.
Cost - Efficiency
Continuous - flow tumble belt shot blasting machines offer significant cost - efficiency benefits for high - volume production. The continuous operation reduces labor costs as fewer workers are required to load and unload the blasting chamber. Additionally, the efficient shot recycling and separation system reduces the consumption of shot media, further lowering operational costs.
Moreover, the high - throughput rate of these machines means that more workpieces can be processed in a shorter period, increasing the return on investment. For manufacturers with large - scale production requirements, the ability to produce more products in less time while maintaining quality can lead to substantial cost savings and improved profitability.
Applications in Different Industries
Automotive Industry
In the automotive industry, the continuous - flow tumble belt shot blasting machine is widely used for the surface treatment of various components. Engine parts, such as cylinder heads, crankshafts, and connecting rods, need to be cleaned and descaled before assembly. The machine can effectively remove rust, casting sand, and other contaminants from these parts, ensuring a proper fit and function.
Wheel rims, which are exposed to harsh environmental conditions during use, also require surface treatment to improve their durability and appearance. The tumble belt shot blasting machine can prepare the surface of the wheel rims for painting or other finishing processes, enhancing their corrosion resistance and aesthetic appeal. With the high - volume production requirements of the automotive industry, the continuous - flow operation of these machines allows manufacturers to keep up with the demand while maintaining strict quality control.
Metal Casting Industry
The metal casting industry benefits greatly from the use of continuous - flow tumble belt shot blasting machines. Castings often have rough surfaces, flash, and sand residues that need to be removed. The tumbling action of the belt is particularly effective in reaching the complex geometries and internal passages of castings, ensuring thorough cleaning.
For example, in a foundry that produces large - scale industrial castings, the continuous - flow machine can process a large number of castings in a short time. This not only speeds up the production process but also improves the quality of the castings by providing a consistent surface finish, which is essential for subsequent machining and assembly operations.
Hardware and Fastener Industry
In the hardware and fastener industry, where small components are produced in large quantities, the continuous - flow tumble belt shot blasting machine is an essential piece of equipment. Bolts, screws, nuts, and washers need to be cleaned, deburred, and prepared for coating or plating. The machine can handle these small components with ease, ensuring that they are uniformly treated and ready for the next stage of production.
The high - volume production capabilities of the machine allow hardware manufacturers to meet the demands of the market efficiently. Whether it's for construction, furniture, or general industrial applications, the consistent surface treatment provided by the continuous - flow tumble belt shot blasting machine helps to improve the performance and appearance of the final products.
Challenges and Future Developments
Challenges
Despite their many advantages, continuous - flow tumble belt shot blasting machines also face some challenges. One of the main challenges is the maintenance of the machine. The tumble belt, blasting wheels, and other components are subject to wear and tear due to the continuous operation and the impact of the shot media. Regular maintenance, including replacement of worn - out parts, is required to ensure the optimal performance of the machine. This maintenance can be time - consuming and costly, especially for large - scale machines used in high - volume production.
Another challenge is the adjustment of the machine for different types of workpieces. While the machine is designed to handle a wide range of components, some workpieces may require specific blasting parameters, such as shot velocity, shot flow rate, and belt speed. Adjusting these parameters accurately to achieve the best surface treatment results for different workpieces can be a complex task and may require skilled operators.
Future Developments
Looking ahead, the continuous - flow tumble belt shot blasting machine is likely to see further technological advancements. One area of development is the integration of more advanced automation and control systems. Smart sensors and artificial intelligence algorithms can be used to monitor the machine's operation in real - time, adjust the blasting parameters automatically based on the characteristics of the workpieces, and predict maintenance needs. This will not only improve the efficiency and accuracy of the machine but also reduce the reliance on skilled operators.
Another potential development is the use of new materials and designs for the machine components. For example, the development of more wear - resistant materials for the tumble belt and blasting wheels can extend their lifespan and reduce maintenance costs. Additionally, innovative designs that improve the efficiency of the shot recycling and separation system can further enhance the machine's performance and reduce its environmental impact.
In conclusion, the continuous - flow tumble belt shot blasting machine is a vital piece of equipment for high - volume production. Its unique design, operational principles, and wide range of applications make it an essential tool for manufacturers across various industries. While it faces some challenges, ongoing technological advancements are likely to further enhance its performance and capabilities, ensuring that it remains at the forefront of surface treatment technology for high - volume production in the future.