Hotline
+86-136 8495 9862
Email:cennia@szmizhi.com
Add::104,Building 27,Third Industrial Zone, Longxi Community,Longgang District,Shenzhen,China.
Coil Forming & Handling Equipment
Surface Treatment Equipment
Solutions
Application
About Us
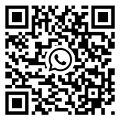
Welcome to MIZHI
For consultation/feedback, please call the service hotline: +86-136 8495 9862 Email:cennia@szmizhi.com
Continuous - Run Roller Conveyor Shot Blasting Machine for High - Volume Manufacturing
1. Introduction
In the fast - paced world of high - volume manufacturing, industries such as automotive, construction, and metalworking constantly strive to meet the ever - increasing demand for products while maintaining high quality standards. One crucial aspect of the manufacturing process is surface treatment, and the continuous - run roller conveyor shot blasting machine has emerged as a game - changer in this regard. This advanced machinery is designed to efficiently and effectively clean, strengthen, and prepare the surfaces of a wide range of products in a continuous and high - volume manner.
2. Working Principle
2.1 Roller Conveyor System
The continuous - run roller conveyor forms the backbone of this shot blasting machine. It consists of a series of parallel rollers that are powered to rotate continuously. The rollers are spaced closely enough to support the workpieces being processed, whether they are large metal sheets, structural components, or small - to - medium - sized parts. The conveyor is designed to move the workpieces through the shot blasting chamber at a consistent and adjustable speed.
Workpieces are loaded onto the conveyor at the infeed end. Specialized fixtures or supports can be used to ensure that the workpieces are properly positioned and stable during transit. As the conveyor moves, the workpieces are smoothly transported through the various stages of the shot blasting process. The speed of the conveyor can be adjusted based on factors such as the type of workpiece, the desired intensity of surface treatment, and the overall production volume requirements. For example, for delicate workpieces that require a more gentle treatment, a slower conveyor speed may be chosen, while for more robust components, a faster speed can be utilized to increase throughput.
2.2 Shot Blasting Unit
The shot blasting unit is where the actual surface treatment takes place. This unit typically consists of multiple centrifugal wheels or high - pressure nozzles, or a combination of both.
Centrifugal wheels are a common feature in continuous - run roller conveyor shot blasting machines. These wheels are equipped with vanes that accelerate abrasive media, such as small metal or ceramic shots, to high velocities. The shots are fed into the center of the wheel and are then flung outwards at speeds often exceeding 80 meters per second. Multiple centrifugal wheels are strategically positioned around the roller conveyor within the shot blasting chamber. This arrangement allows for comprehensive coverage of the workpiece surfaces as they move along the conveyor. The orientation and angle of the wheels can be adjusted to target specific areas of the workpiece, ensuring that all surfaces, including complex geometries and hard - to - reach areas, are effectively treated.
In some cases, high - pressure nozzles may be used instead of or in addition to centrifugal wheels. These nozzles are capable of delivering a highly focused stream of abrasive media at high pressures. They are particularly useful for treating workpieces with irregular shapes or for providing a more targeted surface treatment in specific areas. The pressure and flow rate of the abrasive media through the nozzles can be precisely controlled to achieve the desired level of surface impact.
2.3 Abrasive Media Recycling and Separation
Efficient use of abrasive media is essential in high - volume manufacturing to keep production costs down. The continuous - run roller conveyor shot blasting machine is equipped with a sophisticated abrasive media recycling and separation system.
After the abrasive media impacts the workpiece and falls to the bottom of the shot blasting chamber, it is collected through a series of chutes and conveyor belts. The used media is then passed through a separation process. This process typically involves a combination of mechanical sieving to remove large debris and magnetic separation (if the abrasive media is ferromagnetic) to extract any metal particles that may have been worn off the workpieces or the machine components during the blasting process. The clean and reusable abrasive media is then recycled back into the shot blasting unit, ready for the next cycle of treatment. This closed - loop system not only reduces the cost of constantly purchasing new abrasive media but also minimizes environmental waste, making it an environmentally friendly and cost - effective solution.
3. Advantages in High - Volume Manufacturing
3.1 Unparalleled Production Throughput
1. Continuous Operation: The continuous - run nature of the roller conveyor allows for a non - stop production process. Unlike batch - type shot blasting machines that require time for loading, unloading, and setting up each batch, this machine can continuously feed workpieces into the shot blasting chamber and output treated products. In a high - volume automotive manufacturing plant, for example, where thousands of parts need to be surface - treated daily, the continuous - run roller conveyor shot blasting machine can handle the large volume efficiently, significantly increasing the overall production output.
2. High - Speed Processing: The ability to adjust the speed of the roller conveyor and the high - velocity shot projection from the centrifugal wheels or nozzles enables rapid surface treatment. Manufacturers can optimize the conveyor speed and shot blasting parameters to achieve the desired surface finish in the shortest possible time. This high - speed processing is crucial for meeting tight production schedules and high - volume demand in industries such as construction, where large quantities of steel components need to be prepared for assembly.
3.2 Consistent and High - Quality Surface Treatment
1. Uniform Coverage: The strategic arrangement of the shot - blasting units around the roller conveyor ensures that all workpieces receive a uniform surface treatment. As the workpieces move continuously along the conveyor, they are exposed to a consistent stream of abrasive media from multiple angles. This results in a uniform surface finish across all products, regardless of their size or shape. In the metalworking industry, where consistent surface quality is essential for painting, coating, or further processing, the continuous - run roller conveyor shot blasting machine provides the reliability needed to meet strict quality standards.
2. Precise Control: The machine offers a high degree of control over the surface treatment process. Operators can adjust parameters such as the conveyor speed, the intensity of shot projection (by changing the speed of centrifugal wheels or the pressure of nozzles), and the type and size of abrasive media. This precise control allows for customization of the surface treatment to meet the specific requirements of different workpieces. For example, for parts that require a more aggressive surface cleaning, a higher shot projection intensity can be set, while for delicate components, a gentler treatment can be achieved by adjusting the relevant parameters.
3.3 Cost - Efficiency
1. Reduced Labor Costs: The automated nature of the continuous - run roller conveyor shot blasting machine significantly reduces the need for manual labor. In traditional surface treatment methods, workers may need to manually load, unload, and treat each workpiece, which is time - consuming and labor - intensive. With this machine, the only human intervention required is periodic monitoring and maintenance. This not only cuts down on labor costs but also reduces the variability in the quality of surface treatment that may be associated with manual work, leading to more consistent product quality.
2. Efficient Abrasive Usage: The abrasive media recycling and separation system in the machine ensures that the abrasive media is used efficiently. In high - volume manufacturing, the cost of abrasive media can be a significant expense. By recycling and reusing the shots, manufacturers can save a substantial amount of money over time. Additionally, the reduced need to dispose of used abrasive media also reduces environmental costs associated with waste management.
4. Applications in Various Industries
4.1 Automotive Industry
1. Engine Components: In the automotive industry, engine components such as cylinder heads, crankshafts, and connecting rods require a high - quality surface treatment. The continuous - run roller conveyor shot blasting machine can effectively remove rust, scale, and casting residues from these components. The shot - peening effect of the blasting process also strengthens the surface, improving the fatigue resistance of the parts. This is crucial for ensuring the long - term reliability and performance of engines, which are subject to high stress and vibration during operation.
2. Body Panels and Chassis Parts: Body panels and chassis parts need to have a clean and smooth surface for proper painting and corrosion protection. The machine can clean and prepare the surfaces of these parts, removing any contaminants that could affect the adhesion of paint or coatings. The uniform surface finish achieved by the machine also enhances the aesthetic appeal of the vehicle body.
4.2 Construction Industry
1. Steel Structural Components: The construction industry relies heavily on steel structural components such as beams, columns, and trusses. These components need to be surface - treated to prevent corrosion and improve their structural integrity. The continuous - run roller conveyor shot blasting machine can handle large - sized steel components, cleaning and roughening the surface to enhance the adhesion of protective coatings. In large - scale construction projects, where thousands of tons of steel components are used, the high - volume processing capability of this machine is invaluable.
2. Fencing and Railings: Fencing and railing products made of metal also benefit from the surface treatment provided by this machine. The shot blasting process can clean and strengthen the surface of these products, making them more durable and resistant to environmental factors. The uniform finish also gives them an attractive appearance.
4.3 Metalworking Industry
1. Sheet Metal Fabrication: In sheet metal fabrication, the continuous - run roller conveyor shot blasting machine can be used to clean and prepare the surface of metal sheets before further processing such as stamping, bending, or welding. The machine can remove any oxide layers or contaminants on the sheet metal, improving the quality of the subsequent manufacturing processes. It also ensures that the surface of the finished product is smooth and free from defects.
2. Forged and Cast Parts: Forged and cast parts often have rough surfaces and may contain impurities. The shot blasting machine can effectively clean and refine the surface of these parts, improving their dimensional accuracy and surface finish. This is important for ensuring proper fit and function in assemblies.
5. Operation and Maintenance
5.1 Operation
1. Initial Setup: Before starting the high - volume production process, the machine needs to be properly set up. This involves adjusting the speed of the roller conveyor to match the production requirements. The operator also needs to select the appropriate abrasive media and set the intensity of the shot blasting by adjusting the speed of the centrifugal wheels or the pressure of the nozzles. Safety checks must be carried out to ensure that all protective guards are in place and the machine is in proper working condition.
2. Loading and Unloading: Workpieces are loaded onto the roller conveyor at the infeed end. The operator needs to ensure that the workpieces are properly positioned on the conveyor to ensure even treatment. At the outfeed end, the treated workpieces are unloaded and either sent for further processing (such as painting or assembly) or packaged for shipment.
3. Monitoring: During the operation, the operator should continuously monitor the machine. This includes checking the performance of the shot - blasting units, ensuring that the roller conveyor is moving smoothly, and observing the quality of the treated workpieces. If any issues are detected, such as uneven surface treatment, abnormal noise from the machine, or problems with the abrasive media recycling system, the machine should be stopped immediately for troubleshooting.
5.2 Maintenance
1. Regular Inspection: Regular inspection of the machine is crucial to ensure its long - term reliable operation. Components such as the roller conveyor, centrifugal wheels, nozzles (if applicable), and abrasive media recycling system should be inspected for wear and tear. The rollers on the conveyor may need to be replaced periodically if they show signs of damage or excessive wear. The vanes on the centrifugal wheels, which are subject to high - velocity impacts from the abrasive media, should be checked for erosion and replaced when necessary. The abrasive media recycling system should be inspected to ensure that there are no blockages in the chutes or conveyors.
2. Lubrication: Proper lubrication of moving parts is essential. The bearings on the roller conveyor and the motors driving the shot - blasting units need to be lubricated regularly to reduce friction and prevent premature failure. This helps to maintain the smooth operation of the machine and reduces the risk of breakdowns during high - volume production.
3. Abrasive Media Management: The quality of the abrasive media also needs to be managed. Over time, the abrasive shots may become worn or contaminated. The operator should periodically check the quality of the recycled abrasive and add new abrasive as needed to maintain the effectiveness of the shot blasting process. The size and type of abrasive media may also need to be adjusted depending on the changing requirements of the workpiece production.
6. Conclusion
The continuous - run roller conveyor shot blasting machine has become an indispensable tool in high - volume manufacturing. Its ability to provide high - throughput, consistent quality surface treatment, and cost - efficiency makes it a preferred choice for industries that need to process large quantities of workpieces. By understanding its working principle, operation, and maintenance requirements, manufacturers can optimize their production processes and meet the increasing demand for high - quality products in a competitive market. As technology continues to evolve, it is expected that further improvements will be made to this machine, further enhancing its performance and capabilities in high - volume manufacturing applications.