Hotline
+86-136 8495 9862
Email:cennia@szmizhi.com
Add::104,Building 27,Third Industrial Zone, Longxi Community,Longgang District,Shenzhen,China.
Coil Forming & Handling Equipment
Surface Treatment Equipment
Solutions
Application
About Us
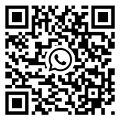
Welcome to MIZHI
For consultation/feedback, please call the service hotline: +86-136 8495 9862 Email:cennia@szmizhi.com
I. Introduction
The cut - to - length and slitting machine is a highly versatile and important piece of equipment in various industries. It combines two essential functions: cutting a continuous material to a specific length (cut - to - length) and slitting a wide roll of material into narrower strips (slitting). This machine has revolutionized the processing of materials such as metal, plastic, and paper, enabling manufacturers to obtain materials in the precise dimensions required for their end - products.
II. Working Principles of Cut - to - length and Slitting Machines
1. Slitting Process
- The slitting operation in the machine is designed to divide a wide roll of material into narrower widths. There are different slitting methods employed. Rotary slitting is a common technique where circular blades are used. These blades are mounted on shafts and rotate at high speeds. The rotary slitting mechanism is suitable for slitting thin to medium - thickness materials like plastic films or thin metal sheets. For thicker materials, shear slitting may be preferred. Shear slitting involves two blades that move relative to each other in a shearing motion to cut through the material. The slitting process requires precise control of the blade alignment. Any misalignment can lead to uneven slitting widths or rough edges on the slit material. To ensure accurate slitting, modern machines may use laser - guided alignment systems or high - precision mechanical alignment devices.
- The slitting section also needs to manage the tension of the material during the slitting process. If the tension is too high, the material may stretch or break, while too low tension can cause wrinkling or misalignment. Tension control devices, such as load cells and tension rollers, are used to maintain the optimal tension. Additionally, the slitting unit may have guide rollers that help to guide the material smoothly through the slitting blades, minimizing friction and ensuring a straight - line slitting operation.
2. Cut - to - length Process
- The cut - to - length process in the machine is responsible for cutting the material, whether it is the original wide roll or the slit strips, into specific lengths. There are several mechanisms for achieving this. One method is the use of a flying shear. A flying shear moves synchronously with the moving material and cuts it at the desired length while the material is in motion. This is advantageous for high - speed production lines as it does not require the material to stop for cutting. Another mechanism is the use of a stationary cutter with a material - stopping and - starting system. In this case, the material is fed to a fixed cutting position, stopped briefly, cut to the required length, and then restarted. This method may be more suitable for materials that are difficult to cut while in motion or for applications where very high - precision cuts are required.
- The accuracy of the cut - to - length operation depends on several factors. The speed of the material feed needs to be accurately controlled. If the feed speed is inconsistent, it will be difficult to achieve precise cut lengths. The cutting device itself, whether it is a flying shear or a stationary cutter, must be sharp and properly aligned. Dull blades or misaligned cutting edges can lead to inaccurate cuts. The control system of the machine also plays a crucial role. A Programmable Logic Controller (PLC) - based control system can measure the length of the material accurately and trigger the cutting operation at the right moment.
III. Components of Cut - to - length and Slitting Machines
1. Uncoiling System
- The uncoiling system is the starting point of the machine's operation. It is designed to hold and unwind the large roll of material. The uncoiling system typically consists of a mandrel on which the roll is mounted. The mandrel must be strong enough to support the weight of the roll, which can vary depending on the material and the size of the roll. There are braking mechanisms associated with the uncoiling system. These brakes are used to control the unwinding speed of the roll. If the brakes are not properly calibrated, the roll may unwind too quickly or too slowly, causing problems such as material slack or excessive tension. Tension control devices in the uncoiling system ensure that the material is under the correct tension as it starts its journey through the machine.
2. Slitting Unit
- As mentioned earlier, the slitting unit contains the slitting blades and associated components. The blades are made of high - quality materials, such as carbide - tipped steel for metal slitting or hardened steel for plastic slitting. The blade holders are designed to hold the blades firmly and allow for easy adjustment and replacement. In addition to the blades, the slitting unit has a drive mechanism to rotate the blades in the case of rotary slitting or to operate the shearing motion in shear slitting. The unit also includes alignment systems, tension control elements, and guide rollers as described previously.
3. Cut - to - length Unit
- The cut - to - length unit is where the actual cutting to specific lengths occurs. For a flying shear - based cut - to - length unit, it includes the flying shear mechanism with its blades, drive system to move the shear synchronously with the material, and a control system to determine the cutting points. In the case of a stationary cutter - based unit, it has the stationary cutter, a material - handling system to stop and start the material, and a precision - measurement system to ensure accurate cut lengths.
4. Recoiling System (if applicable)
- After the material has been slit and cut to length, in some cases, it needs to be rewound into rolls. The recoiling system is responsible for this. The recoiling system has a mandrel on which the processed material is wound. Similar to the uncoiling mandrel, it needs to be strong and well - designed. Tension control during recoiling is crucial to ensure that the resulting roll is wound evenly and tightly. Edge - guiding devices may be used to keep the material centered during recoiling, preventing uneven winding.
IV. Control Systems in Cut - to - length and Slitting Machines
1. Programmable Logic Controllers (PLCs)
- PLCs are at the heart of the control systems in cut - to - length and slitting machines. They are used to manage multiple aspects of the machine's operation. In the slitting process, PLCs can control the speed of the slitting blades, the tension of the material, and the alignment of the blades. For example, they can adjust the blade speed based on the thickness of the material being slit. In the cut - to - length process, PLCs can accurately measure the length of the material using sensors and trigger the cutting operation at the exact desired length. They can also control the speed of the material feed to ensure consistent cut lengths. Additionally, PLCs are responsible for safety - related functions, such as emergency stop procedures and interlocking between different components to prevent accidental operation.
2. Human - Machine Interfaces (HMIs)
- HMIs provide an interface between the operators and the cut - to - length and slitting machine. Through the HMI, operators can set various parameters for the machine. For example, they can specify the slitting widths, the cut - to - length values, the production speed, and the number of pieces to be produced. The HMI also displays real - time information about the status of the machine, such as the current position of the material, the status of each component (e.g., if a blade needs replacement), and the overall production progress. Modern HMIs are often touch - screen based, making it easy for operators to interact with the machine and monitor its performance.
3. Sensor - based Feedback Control
- Sensor - based feedback control is essential for the accurate operation of the machine. There are various types of sensors used. Photoelectric sensors are used to detect the presence and position of the material. This is useful for ensuring that the material is properly aligned during both the slitting and cut - to - length processes. Load cells are used to measure the tension in the material. The data from these sensors is fed back to the control system (usually the PLC). Based on this feedback, the control system can make real - time adjustments. For example, if a load cell detects that the tension is too high, the PLC can adjust the speed of the uncoiling or recoiling (if applicable) to reduce the tension.
V. Applications of Cut - to - length and Slitting Machines in Different Industries
1. Packaging Industry
- In the packaging industry, these machines are widely used. For example, in the production of cardboard boxes, large rolls of corrugated cardboard are slit into the appropriate widths for box - making using the slitting function. Then, the cut - to - length function is used to cut the cardboard into the required lengths for the sides of the boxes. For plastic films used for wrapping products, the slitting machine can produce the desired widths of the film, and the cut - to - length operation cuts the film to the appropriate length for wrapping individual items or groups of items. This ensures that the packaging materials are in the exact dimensions needed, reducing waste and improving the overall efficiency of the packaging process.
2. Automotive Industry
- The automotive industry also benefits greatly from cut - to - length and slitting machines. In the production of car body parts, metal sheets are often slit into narrower strips for specific components and then cut to length for proper assembly. For example, the steel used for door frames or roof rails may be processed using these machines. Additionally, in the manufacturing of interior components such as seat covers or dashboard parts, plastic or fabric materials may be slit and cut to length to fit the specific design requirements of different vehicle models.
3. Construction Industry
- In the construction industry, cut - to - length and slitting machines are used for a variety of materials. For metal roofing and siding materials, the slitting function is used to produce the correct widths of the sheets, and the cut - to - length function ensures that the sheets are cut to the appropriate lengths for installation on buildings. For plywood or other building materials, these machines can be used to slit and cut to length for formwork or other construction applications. This helps to ensure that the building materials are precisely sized, which is crucial for the structural integrity and aesthetics of the building.
VI. Advantages of Cut - to - length and Slitting Machines
1. Precision and Accuracy
- One of the main advantages of these machines is their ability to provide high precision and accuracy in both slitting and cut - to - length operations. The combination of advanced control systems, high - quality blades, and precise measurement devices allows for the production of materials with very accurate dimensions. In industries where the fit and function of the end - product depend on the accuracy of the material dimensions, such as the electronics or aerospace industries, this precision is crucial. For example, in the production of printed circuit boards or aircraft components, even a small deviation in the slitting width or cut - to - length can have a significant impact on the performance of the final product.
2. Versatility
- Cut - to - length and slitting machines are highly versatile. They can handle a wide range of materials, including different types of metals, plastics, and papers. This versatility allows manufacturers in various industries to use the same machine for different materials and applications. For example, a machine can be used to slit and cut aluminum sheets for the automotive industry in the morning and then be used to process plastic films for the packaging industry in the afternoon.
3. Productivity and Efficiency
- These machines can significantly increase productivity and efficiency in material processing. The high - speed operation of the slitting and cut - to - length processes, combined with the ability to continuously process large rolls of material, reduces the production time per unit of product. Additionally, the accurate slitting and cut - to - length operations reduce material waste, as the materials are produced in the exact dimensions required. This not only saves on material costs but also improves the overall efficiency of the manufacturing process.
VII. Challenges and Solutions in Cut - to - length and Slitting Machine Operation
1. Blade Wear and Replacement
- Blade wear is a significant challenge in the operation of these machines. The slitting and cut - to - length blades are subject to wear due to the continuous cutting of materials. Dull blades can lead to poor - quality slitting and inaccurate cut lengths. To address this, high - quality blades made of durable materials should be used. For example, carbide - tipped blades are often preferred for metal slitting. Regular blade inspection and replacement are also necessary. Some machines are equipped with blade - monitoring systems that can detect when a blade needs to be replaced based on factors such as blade wear or vibration.
2. Material Handling and Tension Control
- Maintaining proper material handling and tension control throughout the slitting and cut - to - length processes can be difficult. Different materials have different properties, such as thickness, elasticity, and rigidity, which can affect the tension requirements. Incorrect tension can cause problems such as material stretching, wrinkling, or misalignment. To overcome this, advanced tension control systems, such as those based on load cells and PID controllers, are used. These systems can measure the tension in real - time and make adjustments to the speed of the uncoiling, slitting, or recoiling (if applicable) processes to maintain the correct tension. Additionally, proper material - handling components, such as guide rollers with low - friction coatings, are used to ensure smooth movement of the material.
3. Alignment and Straightness of Material
- Ensuring the alignment and straightness of the material during both slitting and cut - to - length operations is crucial for accurate results. If the material is not properly aligned or straight, it can lead to uneven slitting widths or inaccurate cut lengths. To address this, alignment and guiding devices are used. These include guide rollers with adjustable positions and laser - guided alignment systems in some advanced machines. The guide rollers help to keep the material in the correct position, while the laser - guided systems provide a more precise alignment, especially for high - precision applications.
VIII. Future Trends in Cut - to - length and Slitting Machines
1. Automation and Robotics
- The future of cut - to - length and slitting machines will see increased automation and the integration of robotics. Robotic arms can be used for tasks such as loading and unloading rolls of material, which can improve safety and efficiency. Automation can also be extended to the slitting and cut - to - length processes themselves. For example, the machine can automatically adjust the slitting and cut - to - length parameters based on real - time data from sensors. This will further increase the precision and productivity of the machines.
2. Integration with Industry 4.0
- These machines will be increasingly integrated with Industry 4.0 concepts. They will be connected to the factory's overall network, allowing for real - time data sharing. Operators will be able to remotely monitor and control the machines, and predictive maintenance will become more common. Sensors on the machines will be able to detect potential problems before they cause a breakdown, and the necessary maintenance can be scheduled in advance. This integration will also enable better production planning and resource allocation within the factory.
3. Advanced Materials and Technologies
- As new materials are developed in various industries, cut - to - length and slitting machines will need to adapt. For example, the development of high - strength and lightweight materials in the automotive and aerospace industries will require new slitting and cut - to - length technologies. Laser - slitting technology may become more prevalent as it offers high - precision slitting for a wide range of materials. Additionally, new blade materials and designs may be developed to improve the efficiency and quality of the slitting and cut - to - length operations.
In conclusion, cut - to - length and slitting machines are essential tools in modern manufacturing. Their ability to accurately slit and cut materials to the required lengths and widths has a significant impact on the productivity, quality, and cost - effectiveness of end - products in multiple industries. As technology continues to evolve, these machines will continue to improve and adapt to meet the ever - changing needs of the manufacturing world.