Hotline
+86-136 8495 9862
Email:cennia@szmizhi.com
Add::104,Building 27,Third Industrial Zone, Longxi Community,Longgang District,Shenzhen,China.
Coil Forming & Handling Equipment
Surface Treatment Equipment
Solutions
Application
About Us
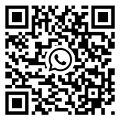
Welcome to MIZHI
For consultation/feedback, please call the service hotline: +86-136 8495 9862 Email:cennia@szmizhi.com
I. Introduction
Cut - to - length machines play a vital role in various industries, from metal processing to textile and paper manufacturing. Manufacturers of these machines are at the heart of providing the technology and equipment that enable precise cutting of materials to specific lengths. This article delves into the world of cut - to - length machine manufacturers, exploring their significance, the range of machines they produce, and the factors that set them apart in a competitive market.
II. Types of Cut - to - Length Machines Offered by Manufacturers
A. Metal - cutting Machines
1. Shear - type Cut - to - Length Machines
Many manufacturers specialize in shear - type cut - to - length machines for metals. These machines are designed to handle different thicknesses of metal sheets or coils. For example, some manufacturers produce hydraulic guillotine shears that can cut thick steel plates with high precision. The hydraulic system in these machines provides the necessary force to make clean, straight cuts. These are often used in heavy - duty applications such as in the construction of large - scale infrastructure or in the manufacturing of heavy machinery.
2. Plasma - cutting Machines
Plasma cut - to - length machines are also a significant part of the product range for many manufacturers. Plasma cutting is ideal for cutting metals with high speed and efficiency, especially for thicker materials. Manufacturers design plasma cut - to - length machines with advanced plasma torch technology. These torches can generate a high - temperature plasma arc that melts and blows away the metal, creating a cut. The machines are often equipped with features to control the plasma arc, such as adjustable gas flow and power settings, allowing for precise cutting of different types of metals.
3. Laser - cutting Machines
Laser cut - to - length machines are becoming increasingly popular among manufacturers. These machines use a highly focused laser beam to cut through metals. Laser cutting offers extremely high precision, making it suitable for intricate designs and fine - detailed work. Manufacturers are constantly innovating in laser cut - to - length machine technology. They are developing more powerful lasers with better beam quality, which can cut through thicker metals while maintaining the precision. Additionally, they are integrating advanced control systems that can optimize the cutting path and speed based on the design of the part being cut.
B. Non - metal - cutting Machines
1. Textile Cut - to - length Machines
In the textile industry, manufacturers produce cut - to - length machines specifically designed for fabrics. These machines need to be gentle on the fabric to prevent damage while still achieving accurate cuts. They often use sharp rotary blades or ultrasonic cutting technology. Rotary blade cut - to - length textile machines are suitable for cutting straight lengths of fabric. The blades are carefully designed to ensure a clean cut without fraying the edges. Ultrasonic cut - to - length machines, on the other hand, use high - frequency vibrations to cut the fabric. This method is particularly useful for cutting synthetic fabrics and for creating complex shapes without the need for additional finishing processes.
2. Paper Cut - to - length Machines
Paper cut - to - length machines are essential in the paper and packaging industries. Manufacturers produce a variety of these machines, from small table - top models for office use to large - scale industrial machines. Industrial paper cut - to - length machines can handle large rolls of paper and cut them into precise lengths for use in packaging, printing, or other applications. These machines typically use a combination of cutting mechanisms, such as rotary knives or guillotine - style blades. They are also equipped with accurate measurement systems to ensure the correct length of the cut paper.
III. Factors that Influence the Success of Cut - to - Length Machine Manufacturers
A. Technological Innovation
1. Research and Development
Successful manufacturers invest heavily in research and development. They are constantly looking for ways to improve the cutting performance of their machines. For example, in metal - cutting machines, they research new ways to increase the cutting speed while maintaining or improving the quality of the cut. This may involve developing new blade materials, optimizing the cutting algorithms in laser or plasma cutting, or improving the hydraulic or mechanical systems in shear - type machines. In non - metal - cutting machines, such as those for textiles and paper, they explore new cutting technologies that are more efficient and produce better - quality cuts.
2. Adaptation to New Materials
As new materials are introduced in various industries, manufacturers need to adapt their machines. For instance, with the development of new high - strength alloys in the metal industry, cut - to - length machine manufacturers must ensure that their machines can handle these materials effectively. In the textile industry, the emergence of new synthetic and composite fabrics requires manufacturers to develop cut - to - length machines that can cut these materials without causing damage or distortion.
B. Quality Control
1. Manufacturing Processes
Manufacturers with a reputation for high - quality cut - to - length machines have strict manufacturing processes. They start with high - quality raw materials for the construction of the machines. For example, in metal - cutting machines, they use high - grade steel for the frames and precision - engineered components for the cutting mechanisms. In the assembly process, they follow strict procedures to ensure that all parts are properly fitted and calibrated. This includes using advanced metrology tools to measure and adjust the components during assembly.
2. Testing and Certification
Before a cut - to - length machine leaves the factory, it must undergo rigorous testing. Manufacturers test the machines for accuracy in cutting length, the quality of the cut (such as smoothness of the cut edges in metal - cutting machines or absence of fraying in textile - cutting machines), and the reliability of the machine over extended periods of operation. Many manufacturers also seek certifications from relevant industry standards organizations. These certifications not only validate the quality of their machines but also give customers confidence in their products.
C. Customer Service
1. Technical Support
Providing excellent technical support is crucial for cut - to - length machine manufacturers. Customers may face issues with machine installation, operation, or maintenance. Manufacturers need to have a team of experienced technicians who can provide timely support. This may include on - site assistance for large - scale industrial machines or remote support via phone or internet for smaller machines. Technical support also involves providing training to customers' employees on how to operate and maintain the machines properly.
2. Customization Options
Many customers have specific requirements for their cut - to - length machines. Successful manufacturers offer customization options. For example, in the metal - cutting industry, a customer may need a machine that can handle a very wide range of metal thicknesses or a machine with a specific cutting speed for their production line. In the textile industry, a customer may require a cut - to - length machine with a particular cutting width or a machine that can be integrated into an existing production system. Manufacturers that can offer customized solutions are more likely to attract and retain customers.
IV. Market Trends and Their Impact on Cut - to - Length Machine Manufacturers
A. Industry 4.0 and Automation
1. Integration of Smart Technologies
The trend towards Industry 4.0 is having a significant impact on cut - to - length machine manufacturers. Manufacturers are increasingly integrating smart technologies into their machines. This includes adding sensors to monitor various parameters such as cutting speed, blade wear, and material thickness in real - time. These sensors are connected to a central control system, which can analyze the data and make adjustments to optimize the cutting process. For example, if the sensor detects that the blade is starting to wear, the system can alert the operator or automatically adjust the cutting parameters to maintain the quality of the cut.
2. Automation of Production Processes
Automation is also a major trend. Cut - to - length machine manufacturers are developing machines that can be fully automated, from loading the material to unloading the cut pieces. This reduces the need for human intervention, increases production efficiency, and improves the consistency of the cut products. For example, in a metal - cutting factory, an automated cut - to - length machine can be integrated with a robotic handling system to move the cut metal pieces to the next stage of production.
B. Sustainability and Environmental Concerns
1. Energy - efficient Machines
With growing environmental concerns, manufacturers are focusing on producing energy - efficient cut - to - length machines. In metal - cutting machines, for example, they are developing more efficient laser and plasma cutting systems that consume less power while still maintaining high - performance cutting. In non - metal - cutting machines, such as those for textiles and paper, manufacturers are looking at ways to reduce the energy consumption of motors and other components.
2. Use of Recyclable Materials
Manufacturers are also considering the use of recyclable materials in the construction of their machines. This not only helps in reducing the environmental impact but also aligns with the sustainability goals of their customers. For example, using recyclable plastics and metals in the casing and some non - critical components of the cut - to - length machines.
V. Global Competition among Cut - to - Length Machine Manufacturers
A. Key Players in Different Regions
1. Europe
In Europe, there are several well - known cut - to - length machine manufacturers. These manufacturers are often known for their high - quality engineering and precision - made machines. For example, German manufacturers are renowned for their metal - cutting machines, which are often used in high - end manufacturing sectors such as automotive and aerospace. They are characterized by their advanced technology, strict quality control, and excellent customer service. Italian manufacturers, on the other hand, may have a strong presence in the textile cut - to - length machine market, offering machines with innovative design and high - quality finishes.
2. Asia
Asia is a major hub for cut - to - length machine manufacturing. Chinese manufacturers have a large share of the market, especially in the production of cost - effective cut - to - length machines for a wide range of industries. They are able to offer a variety of machines at competitive prices due to their large - scale production capabilities and relatively lower labor costs. Japanese manufacturers are known for their technological innovation, particularly in the field of laser - cutting machines. Their machines are often at the forefront of technological advancements, with high precision and reliability.
3. North America
In North America, manufacturers focus on meeting the specific needs of the local industries. For example, in the United States, manufacturers may produce cut - to - length machines that are tailored to the requirements of the construction and manufacturing sectors in the country. They often emphasize on quality, safety, and compliance with local regulations. Canadian manufacturers may also have a niche in certain types of cut - to - length machines, especially those related to the forestry and paper industries.
B. Strategies for Competing in the Global Market
1. Product Differentiation
Manufacturers are using product differentiation as a key strategy to compete in the global market. This includes offering unique features in their machines, such as advanced cutting algorithms, innovative blade designs, or exclusive software for machine control. For example, a manufacturer may develop a cut - to - length machine with a patented cutting technology that offers superior cut quality compared to competitors' machines.
2. Cost - leadership
Cost - leadership is another important strategy. Manufacturers in regions with lower production costs, such as Asia, may aim to offer cut - to - length machines at the lowest possible price while still maintaining an acceptable level of quality. This requires efficient production processes, bulk purchasing of raw materials, and cost - effective marketing strategies. In contrast, manufacturers in high - cost regions may focus on adding value through superior quality and service to justify their higher prices.
In conclusion, cut - to - length machine manufacturers are operating in a dynamic and competitive environment. They need to continuously innovate, ensure high - quality products, provide excellent customer service, and adapt to market trends in order to succeed in the global market. Whether it is through technological advancements, quality control, or strategic marketing, these manufacturers play a crucial role in providing the tools necessary for precise material cutting in a wide range of industries.