Hotline
+86-136 8495 9862
Email:cennia@szmizhi.com
Add::104,Building 27,Third Industrial Zone, Longxi Community,Longgang District,Shenzhen,China.
Coil Forming & Handling Equipment
Surface Treatment Equipment
Solutions
Application
About Us
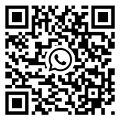
Welcome to MIZHI
For consultation/feedback, please call the service hotline: +86-136 8495 9862 Email:cennia@szmizhi.com
Introduction
In the world of metal processing and manufacturing, the cut to length coil line plays a crucial role. It is a highly specialized piece of equipment that has revolutionized the way metal coils are transformed into precisely sized metal sheets. This article delves deep into the various aspects of cut to length coil lines, including their components, working principles, applications, advantages, and the challenges associated with them.
Components of a Cut to Length Coil Line
1. Uncoiler: This is the starting point of the coil line. The uncoiler is responsible for holding the metal coil and gradually unwinding it. There are different types of uncoilers, such as the fixed - type and the expandable - mandrel type. The expandable - mandrel uncoiler can adapt to different inner diameters of the coils, providing more flexibility in handling various coil sizes. It is equipped with motors and control systems to ensure a smooth and controlled unwinding process.
2. Leveler: Once the metal strip is unwound, it often has some curvature and unevenness due to the coiling process. The leveler is designed to flatten the strip. It consists of multiple rolls that apply controlled pressure to the metal strip, gradually straightening it. The number of rolls and their arrangement can vary depending on the thickness and material of the metal strip. For example, for thicker steel strips, a more robust leveler with a larger number of rolls may be required.
3. Cutting Unit: This is the heart of the cut to length coil line. The cutting unit is responsible for shearing the straightened metal strip into the desired lengths. There are two main types of cutting methods: mechanical shearing and laser cutting. Mechanical shearing uses sharp blades to cut the metal, which is a cost - effective and high - speed method for most common metal materials. Laser cutting, on the other hand, uses a high - energy laser beam to melt and vaporize the metal, providing extremely precise cuts, especially for thinner and more delicate materials or when high - precision edges are required.
4. Stacker: After the metal strips are cut to the desired lengths, they need to be neatly stacked for further processing or storage. The stacker is designed to receive the cut sheets and stack them in an organized manner. It can be automated to adjust the stacking height and ensure that the sheets are stacked evenly, preventing damage to the cut metal sheets.
Working Principle
The operation of a cut to length coil line is a sequential and highly coordinated process. First, the metal coil is loaded onto the uncoiler. The control system of the uncoiler is then activated, and it starts to unwind the coil at a controlled speed. As the metal strip comes out of the uncoiler, it enters the leveler. The leveler's rolls work in tandem to gradually flatten the strip, eliminating any waviness or curvature.
Once the strip is leveled, it moves forward to the cutting unit. The cutting unit is programmed with the desired length of the cut sheets. When the strip reaches the cutting position, the cutting mechanism is activated. In the case of mechanical shearing, the blades close rapidly to cut the strip. For laser cutting, the laser beam is focused on the strip, melting and vaporizing the metal along the cutting line.
After cutting, the individual sheets are conveyed to the stacker. The stacker positions the sheets one by one, creating a neat stack. Throughout the entire process, sensors and control systems are used to monitor and adjust the speed, tension, and position of the metal strip to ensure accurate and efficient operation.
Applications
1. Automotive Industry: In the automotive manufacturing process, cut to length coil lines are used to produce various metal components. For example, the body panels of cars, such as the hood, doors, and fenders, are made from metal sheets that are cut to precise lengths and shapes using these coil lines. The high - precision cuts ensure a perfect fit during the assembly process, improving the overall quality and appearance of the vehicle.
2. Construction Industry: Metal sheets are widely used in the construction industry for roofing, siding, and structural components. Cut to length coil lines are used to produce the required lengths of metal sheets according to the construction plans. The ability to produce large quantities of accurately sized sheets helps in streamlining the construction process and reducing waste.
3. Appliance Manufacturing: Home appliances like refrigerators, washing machines, and ovens require metal sheets for their outer casings and internal components. Cut to length coil lines are used to manufacture these sheets with the exact dimensions needed, ensuring a seamless manufacturing process and a consistent product quality.
Advantages
1. High Precision: Cut to length coil lines can achieve extremely high precision in cutting the metal sheets. The advanced control systems and cutting technologies ensure that the length and width tolerances of the cut sheets are within very narrow limits. This precision is crucial for industries where a perfect fit of components is essential, such as the automotive and aerospace industries.
2. High Efficiency: These coil lines are designed for continuous operation. They can process metal coils at a relatively high speed, reducing the production time per unit of metal sheet. The automated nature of the process, from uncoiling to stacking, also minimizes the need for manual intervention, further increasing productivity.
3. Material Savings: By cutting the metal sheets to the exact required lengths, cut to length coil lines help in reducing material waste. This is especially important considering the high cost of metal materials, and it also contributes to a more sustainable manufacturing process.
Challenges
1. Initial Investment: The purchase and installation of a cut to length coil line can be a significant capital investment. The cost includes not only the equipment itself but also the associated infrastructure, such as a suitable workshop space, electrical systems, and ventilation for laser - cutting - equipped coil lines. Small and medium - sized enterprises may find it difficult to afford such high - cost equipment.
2. Maintenance and Calibration: To ensure the continued high - precision operation of the coil line, regular maintenance and calibration are required. The cutting blades need to be sharpened or replaced regularly in mechanical shearing units, and the laser - cutting systems need to be maintained to ensure the quality of the laser beam. Any deviation in the calibration can lead to inaccurate cuts and reduced product quality.
3. Skilled Labor Requirement: Operating and maintaining a cut to length coil line requires a certain level of technical expertise. Workers need to be trained in setting up the equipment, programming the cutting lengths, and troubleshooting any issues that may arise during operation. The shortage of skilled labor in some regions can pose a challenge to the efficient use of these coil lines.
Future Developments
1. Integration of Smart Technologies: In the future, cut to length coil lines are likely to be integrated with more smart technologies, such as the Internet of Things (IoT) and artificial intelligence (AI). IoT sensors can be used to monitor the performance of the equipment in real - time, sending data to a central control system. AI algorithms can then analyze this data to predict maintenance needs, optimize cutting parameters, and improve overall efficiency.
2. Enhanced Material Compatibility: As new types of metal alloys and composite materials are developed, cut to length coil lines will need to be adapted to handle these materials. This may involve the development of new cutting technologies and leveler designs to ensure that these advanced materials can be processed with the same level of precision and efficiency as traditional metals.
In conclusion, the cut to length coil line is an essential piece of equipment in the metal - processing industry. Its components, working principles, wide range of applications, numerous advantages, and the challenges it faces all contribute to its significance in modern manufacturing. With future developments on the horizon, it is set to play an even more crucial role in the evolving landscape of metal manufacturing.