Hotline
+86-136 8495 9862
Email:cennia@szmizhi.com
Add::104,Building 27,Third Industrial Zone, Longxi Community,Longgang District,Shenzhen,China.
Coil Forming & Handling Equipment
Surface Treatment Equipment
Solutions
Application
About Us
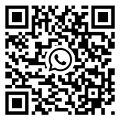
Welcome to MIZHI
For consultation/feedback, please call the service hotline: +86-136 8495 9862 Email:cennia@szmizhi.com
I. Introduction
Cut to length equipment is a vital category of machinery in numerous industrial sectors. It is designed to transform raw materials, which are often in the form of continuous rolls, bars, or sheets, into pieces of specific lengths. This process is crucial as it provides the necessary components for subsequent manufacturing processes, ensuring that the dimensions of the cut materials meet the strict requirements of the end products. The development of cut to length equipment has been driven by the need for precision, efficiency, and reliability in modern manufacturing.
II. Types of Cut to Length Equipment
1.
Roll - fed Cut to Length Machines
Roll - fed cut to length machines are commonly used for processing sheet materials such as metal sheets, plastic films, and paper. These machines are designed to handle materials that are supplied in roll form. The roll of material is mounted on an unwind stand at the beginning of the machine. As the machine operates, the material is unwound and fed through a series of rollers. The rollers play a crucial role in guiding the material and maintaining its tension. One of the key features of these machines is the cutting mechanism. Depending on the application, different cutting methods can be employed. For example, a shearing mechanism is often used for cutting metal sheets. The shearing blades are carefully aligned and actuated to make clean cuts. In the case of plastic films, a hot - wire cutting system may be used. The hot wire melts the plastic as it passes through, creating a smooth edge. These machines are widely used in industries such as automotive manufacturing for cutting body panels, and in the packaging industry for cutting plastic films for bags and pouches.
2.
Bar and Tube Cut to Length Machines
Bar and tube cut to length machines are specialized for cutting cylindrical materials like metal bars, tubes, and rods. These machines can handle different diameters and lengths of materials. One common type is the saw - based cut to length machine. Circular saws are frequently used for cutting smaller - diameter bars and tubes. The circular saw blade rotates at high speed, and the bar or tube is fed into the cutting zone. The feed rate and the speed of the saw blade are carefully controlled to ensure a clean cut. For larger - diameter and thicker - walled tubes, band saws are often employed. Band saws have a continuous blade that wraps around two or more wheels. The material is held in place, and the band saw blade cuts through it. Another type of cutting mechanism for bars and tubes is the cold - sawing method. Cold - saws use a circular blade with teeth that cut the material without generating excessive heat, which is beneficial for maintaining the material's properties. These machines are essential in industries such as construction, where metal bars and tubes are cut to length for structural applications, and in the manufacturing of mechanical components.
3.
Wire Cut to Length Machines
Wire cut to length machines are designed specifically for cutting wire materials. They can handle different wire gauges and materials, including copper, aluminum, and steel wires. One type of wire cut to length machine is the flying - shear machine. In a flying - shear wire cut to length machine, the cutting blades move with the wire during the cutting process. This allows for high - speed cutting of continuous wire without stopping the wire's flow. The speed of the cutting blades is synchronized with the speed of the wire to ensure accurate cut lengths. Another type is the rotary - blade wire cut to length machine. In this machine, a rotary blade rotates at high speed and cuts the wire as it passes through a cutting zone. These machines are widely used in the electrical and electronics industries for cutting wire to the required lengths for wiring harnesses and circuit connections.
III. Working Principle of Cut to Length Equipment
1.
Material Loading and Unwinding (for Roll - fed Machines)
In roll - fed cut to length equipment, the first step is loading the roll of material onto the unwind stand. The unwind stand is designed to hold the roll securely and allow it to rotate freely during the unwinding process. There are usually mechanisms to adjust the tension of the roll to prevent it from unwinding too quickly or too slowly. Once the roll is properly positioned, the material is gradually unwound and fed into the machine. Sensors are often used to monitor the position and tension of the material during this process. If the tension becomes too high or too low, the machine can make adjustments to maintain the optimal condition.
2.
Feeding and Alignment
After unwinding, the material is fed through the machine. In all types of cut to length equipment, proper feeding and alignment are essential. For sheet - based roll - fed machines, there are multiple rollers that guide the material along a specific path. These rollers can be adjusted to accommodate different widths of the sheet. In bar and tube cut to length machines, there are usually guiding mechanisms that hold the material in place and ensure that it is fed straight into the cutting zone. In wire cut to length machines, similar guiding and feeding systems are used to keep the wire in the correct position. The alignment of the material is crucial as any misalignment can lead to inaccurate cut lengths or poor - quality cuts.
3.
Length Measurement and Control
Accurate length measurement is a fundamental part of cut to length equipment. There are various methods for measuring the length of the material. In some machines, encoder wheels are used. Encoder wheels are attached to the rollers or other moving parts that are in contact with the material. As the material moves, the encoder wheels rotate, and the rotation is measured to calculate the distance traveled by the material. Another common method is the use of linear measurement sensors. These sensors can be based on optical, magnetic, or other principles. The measured length data is sent to the control system of the machine. The control system compares the actual length with the preset length value. When the desired length is reached, the control system triggers the cutting operation.
4.
Cutting Process
The cutting process varies depending on the type of cut to length equipment and the material being processed. In shearing - based sheet cutting machines, the cutting blades are actuated by hydraulic, pneumatic, or mechanical means. The blades move towards each other with a specific force to cut through the sheet. In saw - based bar and tube cutting machines, the saw blade rotates at high speed, and the material is fed into the blade at a controlled rate. The cutting action generates heat, and in some cases, cooling systems are used to manage the temperature. In wire cut to length machines, the flying - shear or rotary - blade mechanisms cut the wire with high precision. The cutting speed and the synchronization with the material's movement are carefully controlled to ensure accurate cut lengths.
5.
Post - cutting Handling and Quality Control
After the cutting operation, there are usually post - cutting handling steps. In some cases, the cut pieces are stacked or conveyed to another location for further processing. Quality control is also an important aspect. Sensors may be used to check the length accuracy of the cut pieces. If the length is outside the specified tolerance range, the machine can be adjusted or the piece may be marked for rejection. Additionally, visual inspection systems can be employed to check for any surface defects or burrs on the cut material.
IV. Key Components of Cut to Length Equipment
1.
Unwind Stand and Tension Control System (for Roll - fed Machines)
The unwind stand is the starting point for roll - fed cut to length equipment. It is usually made of a sturdy structure to support the weight of the roll. The stand may have expandable shafts or other mechanisms to hold the roll firmly. The tension control system is crucial for maintaining the proper tension of the material during unwinding. It consists of tension rollers, sensors, and control mechanisms. The tension rollers apply pressure to the material to control its tension. The sensors measure the tension, and the control mechanisms adjust the position of the rollers or the speed of the unwind to keep the tension within the desired range.
2.
Feeding and Guiding Rollers or Mechanisms
Feeding and guiding rollers are essential components in all types of cut to length equipment. In roll - fed machines, these rollers are designed to handle sheet materials. They are usually made of materials with low friction coefficients to ensure smooth movement of the material. The rollers may have different surface finishes or coatings depending on the material being processed. In bar and tube cut to length machines, the guiding mechanisms can include V - blocks, clamps, or other fixtures that hold the material in place and direct it towards the cutting zone. In wire cut to length machines, small - diameter rollers or guides are used to keep the wire in the correct path.
3.
Length Measurement Sensors and Control System
Length measurement sensors are key components for accurate cut to length operations. Encoder wheels are simple and cost - effective sensors that are widely used. They are usually mounted on the feeding rollers or other moving parts. High - resolution encoder wheels can provide relatively accurate length measurements. Linear measurement sensors, such as laser - based or magnetic - based sensors, offer higher precision. The control system of the machine, often based on a programmable logic controller (PLC), receives the length data from the sensors. The PLC is programmed to control the entire operation of the machine, including the feeding speed, the cutting process, and any post - cutting handling based on the measured length and the preset parameters.
4.
Cutting Unit
The cutting unit is the core component that determines the quality of the cut. In shearing - based machines, the cutting unit consists of the upper and lower blades, blade holders, and the actuating mechanism. The blades are usually made of high - quality tool steel and are carefully sharpened and aligned. In saw - based machines, the cutting unit includes the saw blade, the motor that drives the saw blade, and the blade - guiding system. The saw blade's quality, such as its teeth geometry and material, affects the cutting performance. In wire cut to length machines, the cutting unit can be a flying - shear mechanism with its moving blades and drive system or a rotary - blade setup with the rotating blade and associated components.
V. Advantages of Cut to Length Equipment
1.
Precision and Accuracy
Cut to length equipment is designed to provide high - precision cuts. The combination of accurate length measurement sensors and advanced control systems ensures that the cut lengths are within very tight tolerances. This precision is crucial in many manufacturing processes. For example, in the production of electronic components, precise wire lengths are required for proper circuit connections. In the automotive industry, accurate cutting of metal sheets for body panels ensures a proper fit during assembly. The ability to consistently produce cut materials with the desired lengths improves the overall quality of the final products.
2.
Increased Productivity
These machines significantly increase productivity compared to manual cutting methods. The automated operation allows for continuous cutting without the need for frequent stops and starts. For example, in roll - fed cut to length machines for plastic films, the machine can process a large roll of material in a relatively short time. The high - speed cutting capabilities of some equipment, such as flying - shear wire cut to length machines, enable rapid processing of materials. Additionally, the reduction in manual labor not only speeds up the process but also reduces the risk of human errors during cutting.
3.
Versatility in Material Handling
Cut to length equipment can handle a wide variety of materials. Roll - fed machines can process different types of sheets, including metals, plastics, and papers. Bar and tube cut to length machines can handle various metals and alloys with different diameters and lengths. Wire cut to length machines can work with different wire gauges and materials. This versatility makes them suitable for diverse manufacturing applications across multiple industries. The ability to adjust the machine's parameters, such as cutting speed, tension control, and cutting force, allows for the processing of different materials with optimal results.
4.
Improved Quality Control
The integrated quality control mechanisms in cut to length equipment ensure that the cut material meets the required quality standards. The length measurement sensors and other inspection systems detect any deviations from the specified length or any surface defects. If an issue is detected, the machine can be adjusted immediately, or the defective piece can be removed from the production line. This continuous monitoring and control of quality reduce the number of rejects and improve the overall reliability of the manufacturing process.
VI. Challenges and Solutions in the Operation of Cut to Length Equipment
1.
Material Variability
One of the main challenges is dealing with the variability of materials. Different materials have different physical properties, such as hardness, elasticity, and melting points. For example, cutting a soft plastic sheet requires a different approach than cutting a hard metal sheet. To address this, the equipment may have adjustable cutting parameters. The operator can select the appropriate cutting speed, force, or other settings based on the material being processed. Additionally, using specialized cutting tools or blades for different material types can improve the cutting quality. In some cases, pre - processing of the material may be necessary to make it more suitable for cutting.
2.
Wear and Maintenance of Cutting Tools
In cut to length equipment, the cutting tools are subject to wear over time. In shearing - based machines, the blades may become dull, leading to poor cut quality. In saw - based machines, the saw blade's teeth can wear down. Regular inspection of the cutting tools is essential. The tools should be sharpened or replaced when they show signs of wear. Using high - quality cutting tools and providing proper lubrication during the cutting process can extend the lifespan of the tools. Additionally, some machines may have built - in tool - changing mechanisms to facilitate easy replacement of worn - out tools.
3.
Length Measurement Accuracy and Calibration
The accuracy of length measurement is crucial for the performance of the equipment. However, factors such as sensor drift, mechanical vibrations, or changes in environmental conditions can affect the measurement accuracy. Regular calibration of the length measurement sensors is required. This can involve using standard calibration tools and procedures to ensure that the sensors are providing accurate readings. Additionally, the machine's mechanical components, such as the feeding rollers and guides, should be inspected and maintained to prevent any issues that could affect the length measurement, such as misalignment or uneven rotation.
4.
Automation and Integration with Production Lines
Integrating cut to length equipment with other production processes can be challenging. The equipment needs to be synchronized with the upstream and downstream operations in the production line. For example, if the cut material is to be used in an assembly process, the speed and timing of the cut to length equipment need to be coordinated with the assembly process. To achieve this, advanced control systems and communication protocols may be used. The equipment can be equipped with interfaces that allow it to communicate with other machines in the production line, enabling seamless integration.
VII. Conclusion
Cut to length equipment is an essential part of modern manufacturing, enabling the transformation of raw materials into precisely cut pieces for further processing. Its various types, working principles, key components, advantages, and the challenges associated with its operation all contribute to the complex landscape of industrial production. With continuous technological advancements, these machines are expected to become even more efficient, accurate, and versatile, further enhancing the productivity and quality of manufacturing processes. As industries continue to evolve and demand higher - quality products in shorter production times, the role of cut to length equipment will remain crucial.