Hotline
+86-136 8495 9862
Email:cennia@szmizhi.com
Add::104,Building 27,Third Industrial Zone, Longxi Community,Longgang District,Shenzhen,China.
Coil Forming & Handling Equipment
Surface Treatment Equipment
Solutions
Application
About Us
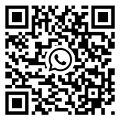
Welcome to MIZHI
For consultation/feedback, please call the service hotline: +86-136 8495 9862 Email:cennia@szmizhi.com
I. Introduction
In the world of metal processing and manufacturing, a cut to length line is an essential piece of equipment. It offers precision cutting of metal coils into specific lengths, enabling efficient production and meeting the diverse needs of various industries. Whether you are in the automotive, construction, or appliance sector, a cut to length line can significantly enhance your production capabilities. In this article, we will explore the features, benefits, and considerations when purchasing a cut to length line for sale.
II. Features of a Cut to Length Line
A. Coil Uncoiling System
1. Description and Function
The coil uncoiling system is the first stage of a cut to length line. It is responsible for unwinding the metal coil and feeding it into the line for cutting. This system typically consists of an uncoiler, which holds the coil and allows it to rotate freely, and a tension control device to ensure smooth feeding of the material.
2. Advantages
Accommodates various coil sizes: Cut to length lines can handle different coil widths and thicknesses, providing flexibility for different production requirements.
Precise tension control: The tension control device ensures that the material is fed at a consistent tension, preventing wrinkles, buckling, or other defects during cutting.
Efficient coil handling: Some uncoilers are equipped with features such as automatic coil loading and unloading, reducing labor and increasing productivity.
B. Straightening System
1. Description and Function
After the coil is unwound, the material passes through a straightening system. This system consists of a series of rollers that flatten and align the metal sheet, removing any curvature or distortion from the coil. The straightening process is crucial for ensuring accurate cutting and minimizing waste.
2. Advantages
High precision straightening: Advanced straightening systems can achieve extremely accurate flatness and alignment, ensuring that the cut pieces meet strict quality standards.
Adjustable settings: The straightening rollers can be adjusted to accommodate different material thicknesses and qualities, providing flexibility in processing various types of metal.
Improved cutting quality: A properly straightened sheet allows for cleaner cuts and reduces the risk of burrs or jagged edges.
C. Cutting System
1. Description and Function
The cutting system is the heart of a cut to length line. It consists of a cutting mechanism, such as a shear or a laser cutter, that precisely cuts the metal sheet into the desired lengths. The cutting system is controlled by a computerized control system that ensures accurate positioning and repeatability.
2. Advantages
Precise cutting: Cut to length lines can achieve extremely accurate cuts, with tolerances as low as a few millimeters. This precision is essential for applications where tight dimensional accuracy is required.
Versatile cutting options: Depending on the type of cut to length line, different cutting mechanisms can be used, such as mechanical shears, hydraulic shears, or laser cutters. Each cutting method has its own advantages and is suitable for different materials and thicknesses.
High cutting speed: Modern cut to length lines can operate at high speeds, significantly increasing production output.
D. Stacking and Packaging System
1. Description and Function
Once the metal sheets are cut, they are stacked and packaged for transportation or storage. The stacking and packaging system typically consists of a conveyor belt that transports the cut pieces to a stacking area, where they are organized and bundled. Some systems may also include automatic packaging machines for added efficiency.
2. Advantages
Organized stacking: The stacking system ensures that the cut pieces are neatly arranged, making it easier to handle and transport.
Protection during transportation: Packaging the cut pieces helps protect them from damage during shipping and storage.
Increased productivity: Automatic stacking and packaging systems can reduce labor and increase the overall efficiency of the production process.
III. Benefits of a Cut to Length Line
A. Increased Efficiency
1. Streamlined production process: A cut to length line automates the cutting process, reducing the need for manual labor and increasing production speed. This leads to higher productivity and shorter lead times.
2. Reduced material waste: The precise cutting capabilities of a cut to length line minimize material waste by ensuring that each piece is cut to the exact length required. This can result in significant cost savings over time.
3. Consistent quality: The computerized control system of a cut to length line ensures accurate cutting and repeatability, resulting in consistent quality of the cut pieces. This is crucial for industries that require high-quality metal products.
B. Versatility
1. Accommodates different materials: Cut to length lines can process a wide range of metal materials, including steel, aluminum, copper, and stainless steel. This versatility allows manufacturers to meet the diverse needs of different industries.
2. Customizable cutting lengths: The control system of a cut to length line can be programmed to cut metal sheets into specific lengths, allowing for customization and flexibility in production. This is useful for applications where different lengths are required for different products.
3. Integration with other processes: Cut to length lines can be integrated with other metal processing equipment, such as slitting lines or press brakes, to create a complete production line. This integration can further enhance efficiency and productivity.
C. Cost Savings
1. Reduced labor costs: By automating the cutting process, a cut to length line reduces the need for manual labor, resulting in lower labor costs. Additionally, the increased productivity of the line can lead to higher output with fewer workers.
2. Lower material waste: As mentioned earlier, the precise cutting capabilities of a cut to length line minimize material waste, reducing material costs.
3. Improved inventory management: With the ability to cut metal sheets into specific lengths on demand, manufacturers can reduce inventory levels and carry only the materials they need for immediate production. This can free up capital and reduce storage costs.
IV. Considerations When Buying a Cut to Length Line
A. Production Requirements
1. Coil sizes and thicknesses: Determine the maximum and minimum coil widths and thicknesses that your production will require. This will help you choose a cut to length line that can handle your specific material specifications.
2. Cutting lengths and tolerances: Consider the range of cutting lengths you need and the required tolerances. Make sure the cut to length line you choose can meet your precision requirements.
3. Production volume: Estimate your production volume to determine the capacity and speed of the cut to length line you need. A higher production volume may require a more advanced and high-capacity line.
B. Quality and Reliability
1. Manufacturer reputation: Research the reputation of different cut to length line manufacturers. Look for companies with a proven track record of quality and reliability in the industry.
2. Build quality: Inspect the build quality of the cut to length line, including the materials used, welding quality, and overall construction. A well-built line will last longer and require less maintenance.
3. After-sales support: Consider the availability of after-sales support, such as technical assistance, spare parts availability, and maintenance services. A reliable manufacturer will provide good after-sales support to ensure the smooth operation of your line.
C. Cost and Budget
1. Initial investment: Determine your budget for purchasing a cut to length line. Consider the cost of the line itself, as well as any additional equipment or accessories you may need, such as uncoilers, straightening systems, or packaging machines.
2. Operating costs: Consider the operating costs of the cut to length line, including electricity consumption, maintenance costs, and consumables such as cutting blades. These costs can add up over time and should be factored into your budget.
3. Return on investment: Evaluate the potential return on investment of a cut to length line. Consider the increased productivity, reduced material waste, and cost savings that the line can bring to your business. Make sure the investment is justified based on your production needs and long-term goals.
A cut to length line for sale can be a valuable investment for your metal processing business. It offers precision cutting, increased efficiency, versatility, and cost savings. When considering purchasing a cut to length line, carefully evaluate your production requirements, quality and reliability needs, and budget. Choose a reputable manufacturer and ensure that the line is capable of meeting your specific needs. With the right cut to length line, you can enhance your production capabilities and stay competitive in the metal processing industry.