Hotline
+86-136 8495 9862
Email:cennia@szmizhi.com
Add::104,Building 27,Third Industrial Zone, Longxi Community,Longgang District,Shenzhen,China.
Coil Forming & Handling Equipment
Surface Treatment Equipment
Solutions
Application
About Us
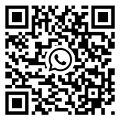
Welcome to MIZHI
For consultation/feedback, please call the service hotline: +86-136 8495 9862 Email:cennia@szmizhi.com
Introduction:
In the world of metal processing and manufacturing, cut-to-length machine manufacturers play a crucial role. These companies are responsible for designing, producing, and supplying the machinery that enables businesses to efficiently cut sheet metal and other materials to specific lengths. With the increasing demand for precision and productivity in various industries, the importance of reliable cut-to-length machine manufacturers cannot be overstated.
The cut-to-length machine is a specialized piece of equipment that is used to cut large coils of sheet metal or other materials into smaller, more manageable lengths. These machines are essential in industries such as automotive, aerospace, construction, and appliance manufacturing, where precise cuts and consistent quality are required.
Design and Innovation:
Cut-to-length machine manufacturers are constantly striving to improve their products through design innovation. They invest in research and development to create machines that are more efficient, accurate, and user-friendly. Some of the key design features that distinguish top manufacturers include:
1. Advanced Controls: Modern cut-to-length machines are equipped with sophisticated control systems that allow operators to set precise cutting lengths, speeds, and other parameters. These controls may include touchscreen interfaces, programmable logic controllers (PLCs), and computer numerical control (CNC) technology.
2. High-Speed Cutting: To meet the demands of high-volume production, manufacturers are developing cut-to-length machines that can cut materials at extremely fast speeds. This requires advanced cutting mechanisms and powerful motors to ensure smooth and accurate cuts.
3. Versatility: Many manufacturers offer cut-to-length machines that can handle a wide range of materials, including different thicknesses and types of sheet metal, as well as other materials such as plastics and composites. This versatility allows businesses to use a single machine for multiple applications, reducing equipment costs and increasing productivity.
4. Precision Engineering: Accuracy is crucial in cut-to-length operations, and manufacturers employ precision engineering techniques to ensure that their machines deliver consistent and reliable cuts. This may include using high-quality cutting tools, precision rollers, and accurate measuring systems.
5. Safety Features: Cut-to-length machines can be dangerous if not operated properly, so manufacturers incorporate a variety of safety features into their designs. These may include safety guards, emergency stop buttons, and interlocks to prevent accidents and protect operators.
Manufacturing Process:
The manufacturing process of cut-to-length machines is a complex and highly specialized endeavor. It typically involves several stages, including:
1. Design and Engineering: The first step is to design the machine based on customer requirements and industry standards. This involves creating detailed drawings and specifications using computer-aided design (CAD) software. Engineers then analyze the design to ensure that it is structurally sound and capable of performing the required cutting tasks.
2. Component Selection: Once the design is finalized, manufacturers source high-quality components from trusted suppliers. These components may include motors, gears, cutting tools, control systems, and structural materials. The selection of quality components is crucial for ensuring the reliability and performance of the final product.
3. Fabrication and Assembly: The selected components are then fabricated and assembled into the cut-to-length machine. This may involve welding, machining, and assembling various parts to create a complete machine. Skilled technicians and engineers work carefully to ensure that each component is installed correctly and that the machine is properly aligned and calibrated.
4. Testing and Quality Control: Before a cut-to-length machine is shipped to a customer, it undergoes extensive testing and quality control procedures. This may include functional testing to ensure that all components are working properly, as well as precision testing to verify the accuracy of the cutting process. Manufacturers also conduct inspections to ensure that the machine meets all safety and quality standards.
5. Packaging and Shipping: Once the machine passes all tests and inspections, it is carefully packaged to protect it during shipping. Manufacturers may use crates, pallets, or other packaging materials to ensure that the machine arrives at its destination in good condition. Shipping arrangements are then made to deliver the machine to the customer's location.
Customer Service and Support:
In addition to manufacturing high-quality cut-to-length machines, top manufacturers also provide excellent customer service and support. This includes:
1. Installation and Training: Manufacturers often offer installation services to ensure that the machine is set up correctly and operates smoothly. They may also provide training to operators to ensure that they are familiar with the machine's features and functions.
2. Maintenance and Repair: To keep cut-to-length machines in optimal condition, manufacturers offer maintenance and repair services. This may include routine inspections, preventive maintenance, and emergency repair services to minimize downtime and ensure continuous production.
3. Spare Parts Supply: Manufacturers maintain an inventory of spare parts to ensure that customers can quickly obtain replacement parts when needed. This helps to minimize downtime and keep the machine running smoothly.
4. Technical Support: Customers can rely on manufacturers for technical support and advice. This may include troubleshooting problems, providing software updates, and answering questions about machine operation and maintenance.
Applications and Industries:
Cut-to-length machines are used in a wide range of industries and applications. Some of the common industries that rely on these machines include:
1. Automotive: In the automotive industry, cut-to-length machines are used to cut sheet metal for body panels, chassis components, and other parts. The precision and efficiency of these machines are essential for meeting the strict quality standards of the automotive industry.
2. Aerospace: The aerospace industry requires high-precision cuts for aircraft components and structures. Cut-to-length machines are used to cut materials such as aluminum, titanium, and composites to exact lengths and tolerances.
3. Construction: In the construction industry, cut-to-length machines are used to cut sheet metal for roofing, siding, and other applications. These machines can handle large coils of material and cut them into precise lengths, saving time and labor.
4. Appliance Manufacturing: Appliance manufacturers use cut-to-length machines to cut sheet metal for the outer casings and internal components of appliances such as refrigerators, washing machines, and ovens. The accuracy and consistency of these machines are important for ensuring the quality and appearance of the final product.
5. Metal Fabrication: General metal fabrication shops use cut-to-length machines for a variety of applications, including cutting sheet metal for custom projects, fabricating structural components, and producing metal parts for machinery and equipment.
Conclusion:
Cut-to-length machine manufacturers play a vital role in the metal processing and manufacturing industries. Their innovative designs, high-quality manufacturing processes, and excellent customer service ensure that businesses have access to reliable and efficient machinery for cutting sheet metal and other materials to specific lengths. As the demand for precision and productivity continues to grow, these manufacturers will continue to evolve and improve their products to meet the needs of their customers.
Sheet Metal Cut to Length Machine: Precision Engineering for Metal Fabrication
In the world of metal fabrication, the sheet metal cut to length machine is an essential tool that offers precision, efficiency, and versatility. This advanced piece of equipment is designed to cut sheet metal into specific lengths with accuracy and consistency, meeting the demands of various industries.
The sheet metal cut to length machine operates on a simple yet effective principle. It uses a series of rollers and cutting tools to feed and cut the sheet metal to the desired length. The machine is capable of handling a wide range of sheet metal thicknesses and widths, making it suitable for various applications.
One of the key advantages of the sheet metal cut to length machine is its precision. The machine is equipped with advanced measuring and cutting systems that ensure accurate cuts every time. This precision is crucial for applications where exact dimensions are required, such as in the production of automotive parts, electronics enclosures, and architectural panels.
The machine's cutting tools are typically made of high-quality materials that are designed to withstand the rigors of cutting sheet metal. These tools can be adjusted to different cutting angles and depths, allowing for a wide range of cutting options. Additionally, the machine's rollers are designed to provide a smooth and stable feed of the sheet metal, ensuring consistent cutting results.
Efficiency is another important aspect of the sheet metal cut to length machine. The machine is capable of processing large quantities of sheet metal in a short amount of time, reducing production time and increasing productivity. This is achieved through the use of automated feeding and cutting systems that can operate continuously without the need for manual intervention.
The sheet metal cut to length machine is also highly versatile. It can be used to cut a variety of sheet metal materials, including steel, aluminum, copper, and stainless steel. Additionally, the machine can be configured to cut different lengths and widths, making it suitable for a wide range of applications.
In addition to its cutting capabilities, some sheet metal cut to length machines also offer additional features such as punching, notching, and bending. These features allow for the production of more complex sheet metal parts without the need for additional processing steps.
The operation of the sheet metal cut to length machine is relatively simple and user-friendly. The machine is typically controlled by a computerized control system that allows the operator to set the desired cutting length and other parameters. The operator then loads the sheet metal onto the machine's feeding system, and the machine automatically feeds and cuts the sheet metal to the specified length.
Maintenance of the sheet metal cut to length machine is also relatively easy. The machine's components are designed for durability and reliability, and regular maintenance can help ensure its long-term performance. This includes cleaning the machine, checking and replacing worn parts, and lubricating the moving components.
The sheet metal cut to length machine has had a significant impact on the metal fabrication industry. It has enabled manufacturers to produce sheet metal parts with greater accuracy and efficiency, reducing waste and increasing productivity. Additionally, the machine's versatility has allowed for the production of a wider range of sheet metal products, meeting the diverse needs of different industries.
Looking to the future, the sheet metal cut to length machine is likely to continue evolving and improving. As technology advances, we can expect to see even more advanced features and capabilities being added to these machines. For example, there may be developments in automation and robotics, allowing for fully automated production lines. Additionally, there may be improvements in cutting technology, resulting in even more precise and efficient cuts.
In conclusion, the sheet metal cut to length machine is a valuable tool for metal fabricators. Its precision, efficiency, and versatility make it an essential piece of equipment for producing sheet metal parts for a wide range of applications. As the demand for high-quality sheet metal products continues to grow, the sheet metal cut to length machine is sure to play an important role in the metal fabrication industry for years to come.