Hotline
+86-136 8495 9862
Email:cennia@szmizhi.com
Add::104,Building 27,Third Industrial Zone, Longxi Community,Longgang District,Shenzhen,China.
Coil Forming & Handling Equipment
Surface Treatment Equipment
Solutions
Application
About Us
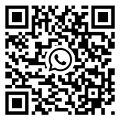
Welcome to MIZHI
For consultation/feedback, please call the service hotline: +86-136 8495 9862 Email:cennia@szmizhi.com
In the metal processing industry, a cut to length production line is an essential piece of equipment for cutting metal coils or sheets into specific lengths. This type of production line is designed to handle a wide range of materials, including steel, aluminum, copper, and other metals. In this article, we will explore the different components of a cut to length production line, its working principle, applications, and benefits.
I. Introduction to Cut to Length Production Line
A cut to length production line is a continuous processing system that consists of several components working together to cut metal coils or sheets into specific lengths. The main components of a cut to length production line include a decoiler, a straightener, a shear, and a stacker. These components are designed to handle different stages of the production process, from unwinding the metal coil to cutting it into the desired length and stacking the finished products.
II. Components of a Cut to Length Production Line
1. Decoiler
The decoiler is the first component of a cut to length production line. It is used to unwind the metal coil and feed it into the straightener. Decoilers can be either manual or automatic, depending on the production requirements. Manual decoilers are suitable for small-scale production, while automatic decoilers are designed for high-volume production.
2. Straightener
The straightener is used to flatten the metal sheet or coil before it is cut. This is important to ensure that the cut edges are straight and smooth. Straighteners can be either roller type or tension type, depending on the material being processed. Roller type straighteners are suitable for thin materials, while tension type straighteners are designed for thicker materials.
3. Shear
The shear is the main cutting component of a cut to length production line. It is used to cut the metal sheet or coil into the desired length. Shears can be either mechanical or hydraulic, depending on the cutting force required. Mechanical shears are suitable for thin materials, while hydraulic shears are designed for thicker materials.
4. Stacker
The stacker is used to stack the cut metal sheets or coils for easy handling and transportation. Stackers can be either manual or automatic, depending on the production requirements. Manual stackers are suitable for small-scale production, while automatic stackers are designed for high-volume production.
III. Working Principle of a Cut to Length Production Line
The working principle of a cut to length production line is relatively simple. The metal coil is unwound by the decoiler and fed into the straightener. The straightener flattens the metal sheet or coil and then feeds it into the shear. The shear cuts the metal sheet or coil into the desired length, and the cut pieces are then stacked by the stacker. The entire process is automated and can be controlled by a computerized control system.
IV. Applications of a Cut to Length Production Line
A cut to length production line is widely used in the metal processing industry for a variety of applications. Some of the common applications include:
1. Automotive Industry
In the automotive industry, cut to length production lines are used to cut metal sheets and coils for body panels, chassis parts, and other components. The high precision and efficiency of these production lines ensure that the parts are cut to the exact specifications required for assembly.
2. Construction Industry
In the construction industry, cut to length production lines are used to cut metal sheets and coils for roofing, siding, and other building materials. The ability to cut large coils into specific lengths makes these production lines ideal for large-scale construction projects.
3. Appliance Industry
In the appliance industry, cut to length production lines are used to cut metal sheets and coils for refrigerator panels, washing machine drums, and other components. The high precision and consistency of these production lines ensure that the parts are cut to the exact dimensions required for assembly.
4. Other Industries
Cut to length production lines are also used in other industries such as aerospace, shipbuilding, and furniture manufacturing. The versatility and efficiency of these production lines make them suitable for a wide range of applications.
V. Benefits of a Cut to Length Production Line
1. High Precision
Cut to length production lines are designed to cut metal sheets and coils with high precision. The use of advanced cutting technology and computerized control systems ensures that the parts are cut to the exact specifications required for assembly. This reduces waste and improves the quality of the finished products.
2. High Efficiency
These production lines are highly automated and can process large volumes of metal sheets and coils in a short period of time. This reduces labor costs and increases productivity, making them ideal for high-volume production.
3. Versatility
Cut to length production lines can handle a wide range of materials and thicknesses, making them suitable for a variety of applications. They can be easily adjusted to cut different lengths and widths, providing flexibility in production.
4. Cost-Effective
The high precision and efficiency of cut to length production lines reduce waste and labor costs, making them a cost-effective solution for metal processing. Additionally, the ability to process large coils into specific lengths reduces material handling and storage costs.
VI. Maintenance and Troubleshooting of a Cut to Length Production Line
To ensure the smooth operation of a cut to length production line, regular maintenance is essential. Some of the common maintenance tasks include:
1. Lubrication
Regular lubrication of the moving parts of the production line is necessary to reduce friction and wear. This includes lubricating the decoiler, straightener, shear, and stacker.
2. Inspection
Regular inspection of the production line is necessary to detect any signs of wear or damage. This includes inspecting the cutting blades, rollers, and conveyor belts for signs of wear or damage.
3. Cleaning
Regular cleaning of the production line is necessary to remove dust, debris, and metal shavings. This includes cleaning the decoiler, straightener, shear, and stacker.
In case of any problems or malfunctions, troubleshooting is necessary to identify the root cause of the problem and take appropriate measures to resolve it. Some of the common troubleshooting steps include:
1. Check the Power Supply
Check the power supply to ensure that the production line is receiving the correct voltage and current.
2. Check the Control System
Check the control system to ensure that it is functioning properly. This includes checking the sensors, switches, and relays for any signs of damage or malfunction.
3. Check the Mechanical Components
Check the mechanical components of the production line to ensure that they are functioning properly. This includes checking the cutting blades, rollers, and conveyor belts for any signs of wear or damage.
VII. Future Trends in Cut to Length Production Lines
The cut to length production line industry is constantly evolving, and several future trends are expected to shape the industry. Some of the common future trends include:
1. Automation and Robotics
The use of automation and robotics in cut to length production lines is expected to increase in the future. This will improve productivity, reduce labor costs, and increase the precision and quality of the finished products.
2. Digitalization and Connectivity
The integration of digital technology and connectivity in cut to length production lines is expected to increase in the future. This will enable real-time monitoring and control of the production process, improve efficiency, and reduce downtime.
3. Sustainability
The demand for sustainable manufacturing practices is expected to increase in the future. Cut to length production lines are expected to become more energy-efficient and environmentally friendly, with features such as waste reduction, energy recovery, and low-emission cutting technology.
4. Customization and Flexibility
The demand for customized and flexible production solutions is expected to increase in the future. Cut to length production lines are expected to become more adaptable to different materials, thicknesses, and lengths, providing greater flexibility in production.
a cut to length production line is an essential piece of equipment for the metal processing industry. With its high precision, efficiency, versatility, and cost-effectiveness, it is widely used in a variety of applications. Regular maintenance and troubleshooting are necessary to ensure the smooth operation of the production line, and future trends such as automation, digitalization, sustainability, and customization are expected to shape the industry in the coming years.