Hotline
+86-136 8495 9862
Email:cennia@szmizhi.com
Add::104,Building 27,Third Industrial Zone, Longxi Community,Longgang District,Shenzhen,China.
Coil Forming & Handling Equipment
Surface Treatment Equipment
Solutions
Application
About Us
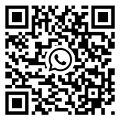
Welcome to MIZHI
For consultation/feedback, please call the service hotline: +86-136 8495 9862 Email:cennia@szmizhi.com
I. Introduction
Decoiling machines with cut - to - length functionality are essential equipment in various industries, especially in those dealing with metal sheets, coils of wire, or other flexible materials. These machines play a crucial role in streamlining the production process by efficiently unwinding the coil and cutting the material to the desired length. The combination of decoiling and cutting operations in one machine offers significant advantages in terms of productivity, accuracy, and quality control.
II. Working Principle of the Decoiling Machine Cut to Length
1.Decoiling Process
The decoiling process is the initial step in the operation of the machine. The coil of material, whether it's a metal sheet coil or a wire coil, is loaded onto the decoiling mandrel of the machine. The mandrel is usually designed to hold the coil securely in place during the unwinding process. It may have features such as expandable cores or clamping mechanisms to prevent the coil from slipping or rotating freely. As the machine starts, the mandrel rotates, and the material begins to unwind. The rotation speed of the mandrel can be adjusted according to the requirements of the production process. For example, for thicker or more rigid materials, a slower decoiling speed may be used to avoid any damage to the material or the machine.
2.Material Feeding and Alignment
After the material starts to unwind from the coil, it is fed into the machine for further processing. During this stage, proper alignment of the material is crucial. The machine has guiding rollers and alignment systems to ensure that the material moves in a straight line. These rollers are often adjustable to accommodate different widths of the material. The alignment systems use sensors or mechanical devices to detect any deviation of the material from its intended path. If the material is not properly aligned, it can lead to inaccurate cutting lengths or other processing issues. For instance, in the case of metal sheet processing, misaligned sheets can cause problems during subsequent operations such as stamping or bending.
3.Cut - to - length Operation
The cut - to - length operation is the core function of this machine. There are different methods for cutting the material to the desired length. One common method is using a shearing mechanism. In this case, the machine has a set of blades that are precisely positioned and timed to cut the material. The cutting action can be achieved through mechanical means, such as a hydraulic or pneumatic system that actuates the blades. Another cutting method is using a laser - cutting system. Laser - cutting offers high precision and can be used for a wide variety of materials. The laser beam is focused on the material, melting or vaporizing it to create a clean cut. The length at which the material is cut is determined by a measuring system within the machine. This system can be based on encoder wheels that measure the distance the material has traveled or other advanced measuring technologies. The desired length is usually set by the operator through a control panel.
4.Control and Monitoring Systems
The decoiling machine cut to length is equipped with advanced control and monitoring systems. The control system manages the operation of the entire machine, including the decoiling speed, material feeding speed, and the cutting process. It ensures that all these processes are coordinated smoothly. The monitoring system, on the other hand, keeps track of various parameters during the operation. It can monitor the tension of the material as it unwinds, the position of the material during alignment, and the accuracy of the cutting length. If any deviations or issues are detected, the system can alert the operator or make automatic adjustments. For example, if the tension in the material becomes too high or too low, the machine can adjust the decoiling speed or the tensioning rollers to correct the situation.
III. Key Components of the Decoiling Machine Cut to Length
1.Decoiling Mandrel
The decoiling mandrel is the central component for holding and unwinding the coil. It is usually made of high - strength materials to withstand the weight and torque of the coil. The design of the mandrel may vary depending on the type of coil. For large - diameter coils, the mandrel may have a larger diameter and stronger structure. It may also have features like a conical shape at the ends to facilitate easy loading and unloading of the coil. Some mandrels are equipped with motorized drives to provide the necessary rotational force for unwinding. Additionally, there are safety mechanisms associated with the mandrel to prevent accidents during coil loading and unloading.
2.Guiding and Alignment Rollers
These rollers are crucial for ensuring the smooth movement and proper alignment of the material. They are usually made of materials with low friction coefficients to minimize any resistance to the material's movement. The guiding rollers are positioned along the path of the material to direct it towards the cutting area. The alignment rollers are designed to correct any lateral displacement of the material. They may have adjustable positions to handle different widths of materials. Some advanced machines have self - adjusting alignment rollers that can automatically correct small deviations in the material's path.
3.Cutting Mechanism
As mentioned earlier, the cutting mechanism can be either a shearing system or a laser - cutting system. In a shearing system, the blades are carefully designed and manufactured to ensure clean and accurate cuts. The blades may be made of high - quality tool steel and have a specific cutting edge geometry. The shearing mechanism may include a power source such as a hydraulic cylinder that provides the necessary force for cutting. In a laser - cutting system, the laser generator is a key component. It produces a high - intensity laser beam that is focused onto the material through optical lenses. The laser - cutting system also has a cooling system to maintain the proper operating temperature of the laser generator.
4.Measuring and Control System
The measuring system is responsible for determining the length of the material to be cut. It usually consists of encoder wheels or linear measurement sensors. Encoder wheels are often used in simpler machines and work by counting the rotations of the wheel as the material passes over it. Linear measurement sensors, on the other hand, provide more accurate and direct measurement of the material's length. The control system includes a programmable logic controller (PLC) or other advanced control units. The PLC is programmed to manage the operation of the decoiling, feeding, and cutting processes based on the input from the operator and the data from the measuring system.
IV. Advantages of the Decoiling Machine Cut to Length
1.Increased Productivity
One of the main advantages of this machine is the significant increase in productivity. By combining the decoiling and cut - to - length operations in one unit, the need for manual handling and intermediate processing steps is reduced. The machine can continuously process the coil material, cutting it to the required lengths at a relatively high speed. This is especially beneficial in high - volume production environments where large quantities of materials need to be processed quickly. For example, in the manufacturing of metal parts for the automotive industry, the ability to quickly and accurately cut metal sheets to length can greatly accelerate the production process.
2.Accuracy in Cutting Length
The decoiling machine cut to length is designed to provide high - accuracy cutting. The measuring systems and advanced control mechanisms ensure that the material is cut to the desired length within very tight tolerances. This accuracy is crucial in many industries where the dimensions of the cut material directly affect the quality of the final product. For instance, in the production of electrical panels, precise cutting of wire lengths is essential for proper assembly and functioning of the panels.
3.Versatility in Material Handling
These machines are highly versatile in handling different types of materials. They can process various metals such as steel, aluminum, and copper, as well as non - metal materials like plastic sheets or wire. The ability to adjust the decoiling speed, cutting parameters, and alignment systems allows the machine to adapt to different material properties and thicknesses. This versatility makes it a valuable asset in a wide range of manufacturing applications.
4.Improved Quality Control
The integrated control and monitoring systems in the decoiling machine cut to length contribute to better quality control. The machine can detect and correct issues such as material misalignment or variations in tension during the process. By ensuring that the material is cut accurately and that the decoiling process is smooth, the quality of the cut material is improved. This leads to fewer defective products in the subsequent manufacturing steps and reduces waste.
V. Challenges and Solutions in the Operation of the Decoiling Machine Cut to Length
1.Material Tension Control
One of the challenges in operating the machine is maintaining proper tension in the material during the decoiling and cutting process. If the tension is too high, it can cause the material to stretch or even break. On the other hand, if the tension is too low, the material may not feed properly or may result in inaccurate cutting. To address this issue, the machine is equipped with tension - control rollers. These rollers can be adjusted to apply the appropriate amount of tension. Additionally, tension sensors are used to monitor the tension in real - time, and the control system can make adjustments based on the sensor data.
2.Cutting Blade Wear and Maintenance
In the case of shearing - based cutting mechanisms, the cutting blades are subject to wear over time. Worn - out blades can lead to rough cuts, burrs on the cut material, or inaccurate cutting lengths. Regular inspection and maintenance of the blades are necessary. The blades should be sharpened or replaced when they show signs of wear. Using high - quality cutting blades and providing proper lubrication during the cutting process can also extend the lifespan of the blades.
3.Alignment and Feeding Issues with Different Materials
Different materials have different physical properties, which can cause alignment and feeding problems. For example, thin and flexible materials may be more prone to wrinkling or misalignment. To overcome these issues, the guiding and alignment rollers can be adjusted to be more gentle and provide better support for such materials. The machine may also have additional features like anti - wrinkle rollers or special feeding mechanisms designed for specific types of materials.
4.Laser - cutting System Calibration and Safety
In laser - cutting - based decoiling machines, calibration of the laser system is crucial for accurate cutting. The laser beam needs to be properly focused and aligned. Regular calibration procedures should be carried out to ensure the quality of the cuts. Additionally, laser - cutting systems present safety hazards due to the high - intensity laser beam. The machine should be equipped with proper safety features such as enclosures, interlocks, and laser - shielding glasses to protect the operators from potential harm.
VI. Conclusion
The decoiling machine cut to length is a vital piece of equipment in modern manufacturing. Its unique working principle, key components, and numerous advantages make it an efficient and reliable solution for processing coil materials. Despite the challenges in its operation, proper management and the use of appropriate solutions can ensure that the machine performs optimally, contributing to increased productivity, improved quality, and greater versatility in the manufacturing process. As technology continues to advance, further improvements in these machines are expected to enhance their capabilities and meet the evolving demands of various industries.