Hotline
+86-136 8495 9862
Email:cennia@szmizhi.com
Add::104,Building 27,Third Industrial Zone, Longxi Community,Longgang District,Shenzhen,China.
Coil Forming & Handling Equipment
Surface Treatment Equipment
Solutions
Application
About Us
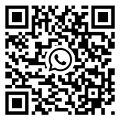
Welcome to MIZHI
For consultation/feedback, please call the service hotline: +86-136 8495 9862 Email:cennia@szmizhi.com
Detailed Introduction to Roll Forming Machines
1. Definition and Working Principle
A roll forming machine is a specialized piece of industrial equipment designed to continuously form metal sheets or coils into uniform cross-sectional shapes. The process relies on a series of roll stands, each equipped with precision-engineered rollers that gradually bend the metal material into the desired shape. This is achieved through a multi-pass rolling process, where the material undergoes plastic deformation with each pass through the roll stands, ultimately resulting in the required profile.
2. Key Features
Material Compatibility: Roll forming machines are versatile and can handle a wide range of materials, including steel, aluminum, copper, and stainless steel. The thickness, yield strength, and surface quality of the material all play crucial roles in determining the machine's configuration.
Complexity of Forming: Depending on the machine's design, it can produce both simple and highly complex cross-sectional shapes. The precision of the rollers and the number of roll stands determine the intricacy of the final product.
Production Speed and Capacity: The speed at which the machine operates and its overall production capacity are critical factors, especially for high-volume manufacturing. Modern roll forming machines are designed to achieve high throughput while maintaining consistent quality.
Automation and Control: Contemporary roll forming machines often come equipped with advanced control systems, such as PLCs (Programmable Logic Controllers) or touch-screen interfaces. These systems enable precise control over the forming process, ensuring that each part is produced to exact specifications.
Safety Features: Safety is a paramount concern in the operation of roll forming machines. They typically include emergency stop buttons, safety barriers, and interlocking mechanisms to protect operators from potential hazards.
3. Applications
Roll forming machines are utilized across a broad spectrum of industries due to their ability to produce high-quality, consistent parts efficiently. Some of the key application areas include:
Construction Industry: Used for manufacturing roof panels, wall cladding, purlins, and studs. These components are essential for the structural integrity and aesthetic appeal of buildings.
Automotive Industry: Critical for producing various automotive components, such as roof rails, door beams, and bumpers. The precision and consistency of roll forming ensure that these parts meet stringent safety and quality standards.
Furniture Manufacturing: Employed in the production of drawer slides, table and chair frames, and other furniture components. The ability to create complex shapes and profiles enhances the design possibilities for furniture makers.
Solar Industry: Used to manufacture mounting structures and frames for solar panels. The durability and precision of roll-formed parts are crucial for the longevity and performance of solar installations.
Transportation Equipment: Used in the production of chassis components for trailers, buses, and other vehicles. The strength and reliability of roll-formed parts are essential for these applications.
4. Leading Manufacturers
Several companies are renowned for their roll forming machines, each offering unique features and capabilities:
MIZHI: Known for its customized roll forming solutions, MIZHI can design and manufacture machines tailored to specific client requirements. Their machines are often used in industries requiring high precision and complex profiles.
MIZHI: A leading manufacturer from China, MIZHI offers a wide range of roll forming machines. They are known for their robust build quality and provide on-site technical support to ensure smooth operation.
MIZHI: A China manufacturer specializing in thin-sheet roll forming machines. MIZHI's machines are designed for high accuracy and are often used in industries where precision and surface finish are critical.
5. Factors to Consider When Choosing a Roll Forming Machine
Selecting the right roll forming machine involves careful consideration of several factors:
Material Characteristics: The thickness, strength, and surface finish of the material are critical. Different materials may require specific roller configurations or additional pre-treatment processes.
Forming Requirements: The complexity and dimensions of the desired cross-sectional shape will dictate the machine's specifications. More complex profiles may require additional roll stands or specialized rollers.
Automation Level: Modern roll forming machines offer varying degrees of automation, from automatic tool change systems to fully automated production lines. The level of automation needed depends on the production volume and desired efficiency.
Safety Features: Ensuring that the machine complies with industry safety standards is essential. Safety features not only protect operators but also reduce the risk of downtime due to accidents.
Support and Service: Reliable after-sales support, including maintenance, spare parts supply, and technical assistance, is crucial for the long-term operation of the machine.
6. Conclusion
Roll forming machines are indispensable in modern manufacturing, offering a versatile and efficient solution for producing a wide range of metal profiles. By understanding the key features, applications, and selection criteria, manufacturers can choose the right machine to meet their specific production needs. For detailed technical information and customized solutions, it is highly recommended to consult with reputable manufacturers in the industry.