Hotline
+86-136 8495 9862
Email:cennia@szmizhi.com
Add::104,Building 27,Third Industrial Zone, Longxi Community,Longgang District,Shenzhen,China.
Coil Forming & Handling Equipment
Surface Treatment Equipment
Solutions
Application
About Us
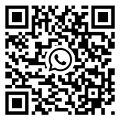
Welcome to MIZHI
For consultation/feedback, please call the service hotline: +86-136 8495 9862 Email:cennia@szmizhi.com
1. Introduction
In the complex and diverse world of industrial manufacturing and metalworking, surface treatment is a fundamental process that significantly impacts the quality, durability, and aesthetics of products. Drum blast machines have emerged as a crucial tool in this domain, offering an efficient and effective way to clean, deburr, descale, and finish a wide variety of components. These machines are widely used across multiple industries, from automotive and aerospace to foundries and general metal fabrication. This in - depth analysis will cover every aspect of drum blast machines, including their components, working principles, applications, advantages, challenges, and future trends.
2. Components of Drum Blast Machines
2.1 The Drum
The drum is the central and most distinctive component of a drum blast machine. It is typically a large, cylindrical container made of robust materials such as heavy - gauge steel. The interior of the drum may be lined with abrasion - resistant materials like rubber or polyurethane to protect the drum itself from the constant impact of the abrasive media and the components being processed. The drum is designed to rotate, either horizontally or at a slight incline, depending on the machine's design. The rotation speed can be adjusted, usually within a certain range, to optimize the blasting process. For example, in a small - scale job shop that processes small metal parts, a drum with a diameter of 1 - 2 meters might be sufficient. Larger industrial - grade drum blast machines used in automotive or aerospace manufacturing can have drums with diameters of up to 5 meters or more.
2.2 Abrasive Feeding System
The abrasive feeding system is responsible for supplying the abrasive media into the drum. There are different types of abrasive feeding mechanisms. One common type is the gravity - fed system, where the abrasive is stored in a hopper above the drum. A valve or a metering device controls the flow of the abrasive, allowing a precise amount to enter the drum. Another type is the pneumatic feeding system, which uses compressed air to propel the abrasive into the drum. This method is often used when a more consistent and high - volume supply of abrasive is required. The choice of abrasive media is also crucial. Common abrasives include steel shot, aluminum oxide, glass beads, and ceramic media. Each type of abrasive has its own characteristics, such as hardness, shape, and size, which determine its suitability for different applications. For example, steel shot is often used for heavy - duty cleaning and deburring, while glass beads are preferred for a more delicate surface finish.
2.3 Blasting Nozzles
Blasting nozzles are the devices through which the abrasive media is directed onto the components inside the drum. These nozzles are strategically positioned around the drum to ensure that the abrasive coverage is as uniform as possible. Nozzles are typically made of wear - resistant materials like tungsten carbide or high - chromium alloys to withstand the high - velocity impact of the abrasive particles. The design of the nozzles can vary, with some having a conical shape to focus the abrasive stream, while others may have a more diffused pattern for broader coverage. In a large - scale automotive parts manufacturing plant, the drum blast machine may have multiple nozzles arranged in a circular pattern around the drum to ensure that all the components, such as engine parts or chassis components, are evenly blasted.
2.4 Dust Collection System
During the blasting process, a significant amount of dust is generated. This dust consists of abrasive particles, debris from the components being processed, and in some cases, fine metal particles. The dust collection system is essential for maintaining a clean and safe working environment. It usually consists of a series of ducts, filters, and a powerful fan. The fan creates a suction force that draws the dust - laden air from the drum into the ducts. The filters then trap the dust particles, allowing clean air to be released back into the atmosphere. There are different types of filters used, such as cartridge filters and bag filters. Cartridge filters are known for their high - efficiency dust - removal capabilities and are often used in industrial settings where strict environmental regulations need to be met.
2.5 Drive System
The drive system is responsible for rotating the drum. It typically includes an electric motor, a gearbox, and a set of pulleys or chains. The electric motor provides the power, which is then transmitted through the gearbox to reduce the speed and increase the torque. The pulleys or chains connect the gearbox to the drum, ensuring smooth and consistent rotation. The drive system may also have variable - speed controls, allowing the operator to adjust the rotation speed of the drum according to the requirements of the blasting process. For example, when processing delicate components, a slower rotation speed may be required to prevent damage, while for heavy - duty cleaning of large - scale components, a higher speed can be used to increase the efficiency of the blasting process.
2.6 Control Panel
The control panel is the interface through which the operator interacts with the drum blast machine. It allows the operator to set various parameters such as the rotation speed of the drum, the flow rate of the abrasive, and the blasting time. In modern drum blast machines, the control panel may be a digital interface with touch - screen capabilities. This makes it easier for the operator to input and adjust the parameters. The control panel also provides information about the machine's status, such as the remaining amount of abrasive in the hopper, the temperature of the dust collection system, and any error messages. In an industrial setting, the control panel can be integrated into a larger plant - wide control system, allowing for remote monitoring and control of the drum blast machine.
3. Working Principle
The operation of a drum blast machine is based on the principle of abrasive impact.
1. Loading the Components: First, the components to be processed are loaded into the drum. This can be done manually for small - scale operations or using automated loading systems in large - scale industrial plants. The components are placed inside the drum in a way that ensures they are evenly distributed.
2. Abrasive Feeding: Once the components are loaded, the abrasive feeding system is activated. The abrasive media, which could be steel shot, glass beads, or other materials, is introduced into the drum. The flow rate of the abrasive is carefully controlled to ensure that there is an adequate amount of abrasive for effective blasting without over - saturating the drum.
3. Drum Rotation: The drive system then starts rotating the drum. As the drum rotates, the components inside the drum tumble and move around. The blasting nozzles, which are positioned around the drum, direct a high - velocity stream of abrasive particles onto the components. The impact of the abrasive particles on the components' surfaces removes contaminants such as rust, scale, paint, and burrs. The rotation of the drum ensures that all sides of the components are exposed to the abrasive stream, providing a uniform treatment.
4. Dust Collection: Simultaneously, the dust collection system is in operation. The fan in the dust collection system creates a negative pressure inside the drum, drawing in the dust - laden air. The dust, which includes abrasive particles, debris from the components, and fine metal particles, is then filtered out by the dust collection system, keeping the working environment clean and safe.
5. Unloading the Components: After the specified blasting time, the drum is stopped, and the components are unloaded. The components are now clean, deburred, and have a surface finish that is suitable for further processing, such as painting, plating, or assembly.
4. Applications
4.1 Automotive Industry
In the automotive industry, drum blast machines are used for a variety of applications. Engine components, such as cylinder heads, engine blocks, and crankshafts, often have complex shapes and need to be thoroughly cleaned and deburred. Drum blast machines can effectively remove casting sand, rust, and machining burrs from these components. The uniform surface finish provided by drum blasting also improves the adhesion of coatings, such as paint and anti - corrosion coatings. In the production of automotive body parts, drum blast machines are used to clean and prepare the surfaces before painting. This helps in achieving a smooth and durable paint finish, enhancing the aesthetics and corrosion resistance of the vehicle.
4.2 Aerospace Industry
The aerospace industry has strict quality and safety requirements. Drum blast machines play a crucial role in the surface treatment of aerospace components. Turbine blades, which are subjected to extreme temperatures and mechanical stresses, need to have a precise surface finish. Drum blasting can remove any surface imperfections, such as oxidation layers and machining marks, improving the aerodynamic performance and fatigue resistance of the blades. In the manufacturing of aircraft structural components, drum blast machines are used to clean and prepare the surfaces for bonding and painting. The high - quality surface treatment provided by drum blasting ensures the integrity and reliability of the aircraft.
4.3 Foundries
Foundries are one of the primary users of drum blast machines. After the casting process, the castings often have a rough surface, casting sand adhered to them, and other defects. Drum blast machines are used to clean the castings, removing the sand and any surface impurities. This not only improves the appearance of the castings but also prepares them for further machining and finishing operations. In the production of complex castings, such as engine blocks and large - scale industrial components, drum blast machines can effectively reach all the internal and external surfaces, ensuring a thorough cleaning and surface treatment.
4.4 General Metal Fabrication
In general metal fabrication shops, drum blast machines are used for a wide range of applications. They can be used to clean and finish metal sheets, pipes, and fabricated parts. For example, before painting or powder - coating metal furniture, drum blast machines can be used to remove any rust, grease, or other contaminants from the metal surfaces. This ensures a better adhesion of the coating and a more durable finish. In the production of industrial machinery parts, drum blast machines can be used to deburr and smooth the surfaces, improving the functionality and performance of the parts.
5. Advantages
5.1 High - Efficiency and Uniform Treatment
Drum blast machines offer high - efficiency surface treatment. The continuous rotation of the drum and the uniform distribution of the abrasive ensure that all components are treated evenly. This is in contrast to some manual or less - automated surface - treatment methods, which may result in inconsistent treatment. In a large - scale manufacturing plant, a drum blast machine can process a large number of components in a single batch, reducing the overall production time. For example, in an automotive parts manufacturing facility, a drum blast machine can process hundreds of small components, such as bolts and nuts, in one cycle, significantly increasing the productivity.
5.2 Versatility
These machines are highly versatile and can handle a wide variety of components in terms of size, shape, and material. Whether it's small, intricate metal parts or large - scale industrial components made of steel, aluminum, or other alloys, drum blast machines can be adjusted to provide the appropriate surface treatment. The choice of abrasive media also adds to the versatility. Different abrasives can be used depending on the specific requirements of the component, such as a more aggressive abrasive for heavy - duty cleaning or a finer abrasive for a smooth surface finish.
5.3 Cost - Effectiveness in the Long Run
Although the initial investment in a drum blast machine can be significant, it is cost - effective in the long run. The high - efficiency of the machine reduces the labor cost associated with manual surface - treatment methods. The ability to process a large number of components in one batch also reduces the per - unit processing cost. Additionally, the long - lasting components of the drum blast machine, such as the wear - resistant nozzles and the durable drum lining, reduce the maintenance and replacement costs over time.
5.4 Improved Product Quality
The surface treatment provided by drum blast machines improves the quality of the components. The removal of contaminants, burrs, and surface imperfections enhances the mechanical properties, such as fatigue resistance and corrosion resistance, of the components. The smooth and uniform surface finish also improves the aesthetics of the products, making them more appealing to customers. In industries where product quality is crucial, such as aerospace and automotive, drum blast machines play a vital role in ensuring the production of high - quality components.
6. Challenges
6.1 High Initial Investment
The purchase and installation of a drum blast machine can be a substantial capital investment. The cost of the machine itself, including the drum, abrasive feeding system, dust collection system, and drive system, can range from tens of thousands to hundreds of thousands of dollars, depending on the size and capabilities of the machine. In addition, there are costs associated with infrastructure development, such as a suitable workspace with proper ventilation, electrical systems to power the machine, and safety measures. Small and medium - sized enterprises may find it difficult to afford such high - cost equipment, which can limit their growth and competitiveness in the market.
6.2 Maintenance Requirements
Drum blast machines require regular maintenance to ensure their optimal performance. The abrasive media can cause wear and tear on the components of the machine, such as the blasting nozzles, the drum lining, and the abrasive feeding system. The nozzles need to be replaced periodically as they become worn out due to the constant impact of the abrasive particles. The drum lining may also need to be repaired or replaced if it gets damaged. The dust collection system also requires regular maintenance, including filter cleaning and replacement. Maintenance can be time - consuming and costly, and any downtime due to maintenance can affect the production schedule.
6.3 Environmental Concerns
The dust generated during the blasting process can be an environmental concern. If not properly collected and managed, the dust can contain abrasive particles, heavy metals, and other contaminants that can be harmful to the environment and human health. The disposal of used abrasive media also needs to be done in an environmentally responsible manner. Some abrasive media, such as steel shot, can be recycled, but others may require special disposal methods. Meeting environmental regulations regarding dust emissions and waste disposal can be a challenge for manufacturers using drum blast machines.
6.4 Operator Training
Operating a drum blast machine effectively requires proper training. The operator needs to understand how to set the correct parameters, such as the rotation speed of the drum, the flow rate of the abrasive, and the blasting time. Incorrect settings can lead to under - treatment or over - treatment of the components, resulting in poor product quality. The operator also needs to be aware of safety procedures, such as wearing appropriate personal protective equipment and following proper loading and unloading procedures. Lack of proper training can lead to accidents and reduced productivity.
7. Future Trends
7.1 Integration of Automation and Smart Technologies
The future of drum blast machines lies in the integration of automation and smart technologies. Automated loading and unloading systems can be integrated with the drum blast machine, reducing the need for manual labor and improving the efficiency of the process. Smart sensors can be installed on the machine to monitor various parameters, such as the wear of the nozzles, the amount of abrasive in the hopper, and the temperature of the dust collection system. This data can be analyzed using artificial intelligence and machine - learning algorithms to predict maintenance needs, optimize the blasting process, and improve overall efficiency.
7.2 Development of Environmentally Friendly Abrasives and Processes
As environmental concerns become more prominent, there will be a growing focus on developing environmentally friendly abrasives and processes. New types of biodegradable or recyclable abrasives may be developed, reducing the environmental impact of the blasting process. The dust collection and waste - management systems of drum blast machines will also be improved to meet stricter environmental regulations. For example, more efficient dust - collection technologies may be developed to reduce the amount of dust emissions, and better recycling methods for used abrasive media may be implemented.
7.3 Customization for Specialized Applications
In response to the increasing demand for specialized products in various industries, drum blast machines will likely become more customizable. Manufacturers will be able to tailor the machines to meet the specific requirements of different applications, such as processing components with unique shapes or materials. This may involve the development of specialized blasting nozzles, drum designs, and abrasive - feeding systems. For example, in the medical device manufacturing industry, where components need to be treated with extreme precision and cleanliness, customized drum blast machines can be developed to meet these stringent requirements.
In conclusion, drum blast machines are an essential and powerful tool in the industrial surface - treatment landscape. Their components, working principle, wide - ranging applications, numerous advantages, and the challenges they face all contribute to their significance in modern manufacturing. With the advent of new technologies and the evolving demands of various industries, drum blast machines are set to undergo further advancements, continuing to play a pivotal role in the production of high - quality components.