Hotline
+86-136 8495 9862
Email:cennia@szmizhi.com
Add::104,Building 27,Third Industrial Zone, Longxi Community,Longgang District,Shenzhen,China.
Coil Forming & Handling Equipment
Surface Treatment Equipment
Solutions
Application
About Us
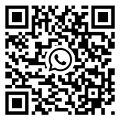
Welcome to MIZHI
For consultation/feedback, please call the service hotline: +86-136 8495 9862 Email:cennia@szmizhi.com
Introduction:
In the realm of industrial manufacturing, cut to length line manufacturers play a crucial role in providing efficient and accurate solutions for processing metal coils. These manufacturers design and produce specialized machinery that can cut metal sheets to specific lengths, widths, and thicknesses, meeting the diverse needs of various industries. In this extensive article, we will delve deep into the world of cut to length line manufacturers, exploring their significance, capabilities, product offerings, and the factors to consider when choosing a manufacturer.
I. The Importance of Cut to Length Lines
Cut to length lines are essential in the metal processing industry as they enable the conversion of large metal coils into precisely sized sheets. This process is crucial for a wide range of applications, including automotive manufacturing, construction, appliance production, and more. By using cut to length lines, manufacturers can ensure consistent quality, reduce waste, and increase productivity.
II. Key Features and Capabilities of Cut to Length Lines
1. Coil Handling
Cut to length lines are designed to handle large metal coils with ease. They typically feature coil cars or decoilers that can safely load and unload coils of different sizes and weights. Some advanced models may also include coil centering devices and tension control systems to ensure smooth and accurate feeding of the coil.
2. Straightening
Before the metal sheet is cut, it often needs to be straightened to remove any curvature or distortion. Cut to length lines usually incorporate straightening units that use a series of rollers to flatten the sheet and ensure a uniform thickness throughout.
3. Cutting Mechanisms
The cutting mechanism is the heart of a cut to length line. There are several types of cutting methods available, including guillotine shearing, rotary shearing, and laser cutting. Guillotine shearing is the most common method and offers high cutting accuracy and speed. Rotary shearing is suitable for thinner materials and can provide a continuous cutting process. Laser cutting is a more advanced option that offers extremely precise cuts and can handle a wide range of materials.
4. Length and Width Measurement
Accurate length and width measurement is essential for ensuring the correct sizing of the cut sheets. Cut to length lines are equipped with measuring devices such as encoders and laser sensors to precisely determine the dimensions of the sheet. Some systems may also include automated length adjustment and width control features to allow for quick and easy changes in sizing.
5. Stacking and Packaging
After the sheets are cut, they need to be stacked and packaged for transportation and storage. Cut to length lines often include stacking devices and packaging systems that can handle different sheet sizes and weights. Some advanced models may even have robotic stacking and packaging capabilities for increased efficiency.
III. Types of Cut to Length Lines
1. Manual Cut to Length Lines
Manual cut to length lines are the simplest and most affordable option. They require operator intervention for loading and unloading coils, straightening, cutting, and stacking. These lines are suitable for small-scale operations or for processing materials that do not require high precision or productivity.
2. Semi-Automatic Cut to Length Lines
Semi-automatic cut to length lines offer a higher level of automation than manual lines. They typically include features such as automatic coil loading, straightening, and cutting, but may still require some operator assistance for stacking and packaging. These lines are ideal for medium-sized operations that need a balance between productivity and cost.
3. Fully Automatic Cut to Length Lines
Fully automatic cut to length lines are the most advanced and productive option. They are designed to operate with minimal operator intervention, handling all aspects of the cutting process from coil loading to stacking and packaging. These lines are suitable for large-scale industrial operations that require high precision, speed, and efficiency.
IV. Product Offerings of Cut to Length Line Manufacturers
1. Standard Models
Most cut to length line manufacturers offer a range of standard models that are designed to meet the general needs of the market. These models come in different sizes and configurations, with varying cutting capacities, coil handling capabilities, and automation levels. Standard models are often a cost-effective solution for businesses that do not have unique or specialized requirements.
2. Customized Solutions
In addition to standard models, many manufacturers also offer customized cut to length lines. These solutions are designed to meet the specific needs of individual customers, taking into account factors such as the type of material being processed, the required cutting accuracy, production volume, and available space. Customized lines can be tailored to fit unique production processes and can include specialized features such as special cutting methods, additional automation components, or integrated quality control systems.
3. After-Sales Support and Services
Cut to length line manufacturers also provide after-sales support and services to ensure the smooth operation and longevity of their machinery. This may include installation and commissioning services, operator training, technical support, spare parts supply, and maintenance contracts. A reliable manufacturer will offer comprehensive after-sales support to help customers maximize the performance and lifespan of their cut to length lines.
V. Factors to Consider When Choosing a Cut to Length Line Manufacturer
1. Reputation and Experience
When choosing a cut to length line manufacturer, it is important to consider their reputation and experience in the industry. Look for manufacturers with a proven track record of providing high-quality machinery and excellent customer service. Read reviews and testimonials from other customers, and research the manufacturer's history and track record of innovation and reliability.
2. Product Quality and Performance
The quality and performance of the cut to length line are crucial factors to consider. Look for manufacturers that use high-quality materials and components in their machinery, and ensure that the line is designed to meet your specific cutting requirements. Consider factors such as cutting accuracy, speed, productivity, and ease of operation. Request product samples or demonstrations if possible to evaluate the quality and performance of the machine.
3. Customization Options
If you have unique or specialized cutting requirements, look for a manufacturer that offers customization options. A manufacturer that can tailor their machinery to your specific needs will be able to provide a more efficient and effective solution for your business. Consider factors such as the ability to customize cutting lengths, widths, and thicknesses, as well as the availability of special cutting methods or automation features.
4. After-Sales Support
After-sales support is an important consideration when choosing a cut to length line manufacturer. Look for a manufacturer that offers comprehensive after-sales support, including installation, training, technical support, and spare parts supply. A reliable manufacturer will be committed to ensuring the smooth operation and longevity of their machinery, and will be available to assist you whenever needed.
5. Price and Cost of Ownership
While price is an important factor, it should not be the only consideration. Consider the overall cost of ownership of the cut to length line, including factors such as initial purchase price, installation costs, maintenance expenses, and energy consumption. Look for a manufacturer that offers a balance between quality and price, and consider the long-term value and return on investment of the machinery.
VI. The Future of Cut to Length Line Manufacturing
As the industrial manufacturing industry continues to evolve, cut to length line manufacturers are constantly innovating and improving their products to meet the changing needs of their customers. Some of the trends that are likely to shape the future of cut to length line manufacturing include:
1. Increased Automation and Intelligence
With the advent of Industry 4.0, cut to length lines are becoming more automated and intelligent. Manufacturers are incorporating advanced technologies such as artificial intelligence, machine learning, and the Internet of Things (IoT) to improve the performance and efficiency of their machinery. These technologies can enable real-time monitoring and optimization of the cutting process, predictive maintenance, and remote control and diagnostics.
2. Sustainable Manufacturing
As environmental concerns become more prominent, cut to length line manufacturers are focusing on developing sustainable manufacturing solutions. This may include the use of energy-efficient motors, recycled materials, and waste reduction strategies. Manufacturers are also exploring alternative cutting methods that are less harmful to the environment, such as waterjet cutting or plasma cutting.
3. Customization and Flexibility
Customers are increasingly demanding customized and flexible manufacturing solutions. Cut to length line manufacturers are responding to this trend by offering more customization options and modular designs that can be easily adapted to different production requirements. This allows businesses to quickly and easily reconfigure their cutting lines to meet changing market demands.
4. Integration with Other Manufacturing Processes
Cut to length lines are often part of a larger manufacturing process. In the future, manufacturers are likely to focus on integrating their machinery with other manufacturing processes, such as stamping, welding, and painting. This can improve productivity, reduce waste, and enhance the overall quality of the final product.
Cut to length line manufacturers play a vital role in the metal processing industry by providing efficient and accurate solutions for cutting metal coils. When choosing a manufacturer, it is important to consider factors such as reputation, product quality, customization options, after-sales support, and price. By selecting a reliable and innovative manufacturer, businesses can ensure the success of their metal processing operations and stay competitive in the market. As the industry continues to evolve, cut to length line manufacturers will continue to innovate and improve their products to meet the changing needs of their customers.